Brazil is one of the largest producers and consumers of clay construction materials. According to the Secretariat of Geology, Mining, and Mineral Processing (MME, 2022), ~170 million tons of clay are used annually in the structural red ceramic industry in Brazil. Natural clays are essential in the red ceramic industry (Jemaï et al., Reference Jemaï, Karoui-Yaakoub, Sdiri, Salah, Azouzi and Duplay2015). In particular, sealing and structural blocks made of red clays are the most widely used and versatile products in Brazil's construction industry (Zaccaron et al., Reference Zaccaron, Nandi and Bernardin2021). This is ascribed to the favourable characteristics of clays, including their availability, mechanical, physical and thermal durability, unique acoustic properties and weathering resistance (Deboucha & Hashim, Reference Deboucha and Hashim2011; Shakir & Mohammed, Reference Shakir and Mohammed2013; Ukwatta et al., Reference Ukwatta, Mohajerani, Setunge and Eshtiaghi2015; Kazmi et al., Reference Kazmi, Abbas, Saleem, Munir and Khitab2016; Muñoz et al., Reference Muñoz, Morales, Letelier and Mendívil2016).
Due to their plasticity, clay-based materials are suitable for extrusion moulding; however, the more plastic the material, the greater the water content necessary to achieve the workable plasticity, which may lead to the emergence of drying cracks and hence reductions in mechanical strength (Andrade et al., Reference Andrade, Al-Qureshi and Hotza2011).
For ceramic purposes, clay deposits have a wide geographical distribution throughout Brazil. This can be attributed to the extensive sedimentary covering of the Brazilian geological substrate, which includes Phanerozoic basins and Cenozoic deposits that form significant residual weathering covers through their geomorphological evolution. In a geological context, two main types of deposits are distinguished: quaternary and sedimentary basin clays (Schaefer et al., Reference Schaefer, Fabris and Ker2008; Cabral Junior et al., Reference Cabral Junior, Tanno, Sintoni, Motta and Coelho2012).
Quaternary clays are associated with deposits that fill valley bottoms and coastal plains, forming lenticular deposits with thicknesses in the range of metres that occupy hectares. Sedimentary basin clays comprise shales, argillites, siltstones, rhythmites and pelites, which are called ‘taguas’ generically. These rocks contain clay minerals of the illite group predominantly, which are rich in potassium, an alkali metal that decreases their sintering temperature. In addition, tagua rocks contain large amounts of ferruginous materials, which facilitate the sintering process and provide reddish firing colours (Cabral Júnior et al., Reference Júnior M., Motta, Almeida, Tanno, Luz and Lins2008).
To optimize the processing of red ceramics, it is necessary to know the chemical and mineralogical characteristics of the composition used to manufacture the product, amongst other factors. Plasticity is a key property (Vasconcellos et al., Reference Vasconcellos, Sousa, Moura, Silva, Gomes and Barbosa2019). Plasticity is related to the deformation of a body that is retained after stress relief when subjected to a certain external force (Aghayev & Küçükuysal, Reference Aghayev and Küçükuysal2018). It is affected by many of the physicochemical parameters of clays, especially their mineralogy, particle-size distribution and the presence of soluble salts and organic matter. The plastic characteristics of clays and therefore their workability during the forming process constitute some of the main requirements for their use in the manufacture of red ceramics (Marsigli & Dondi, Reference Marsigli and Dondi1997).
Given its complexity, the plasticity of clays has been investigated empirically using various test methodologies. In the red ceramics sector, the most widespread methods used are those of Atterberg and Pfefferkorn (Marsigli & Dondi, Reference Marsigli and Dondi1997). Several studies have been carried out in recent years on the interpretation of the plastic behaviours of clays using the Atterberg and Pfefferkorn methods (Crozetta et al., Reference Crozetta, Nandi, Rosso, Zaccaron and Niero2016; Karakan & Demir, Reference Karakan and Demir2018, Reference Karakan and Demir2020; Karakan et al., Reference Karakan, Shimobe and Sezer2020; Karakan, Reference Karakan2022a, Reference Karakan2022b) and the indentation method.
Doménech et al. (Reference Doménech, Sánchez, Sanz, García and Ginés1994) evaluated the plasticity of ceramic compositions using the indentation method and determined that the liquid limit (LL) and the plastic limit (PL) can be obtained for consistencies (applied forces) of 1 and 46 N, respectively. A comparison between the indentation method and the Pfefferkorn method showed that the former is reliable and more accurate than the latter, in addition to it being more practical in its application (Modesto & Bernardin, Reference Modesto and Bernardin2008).
Red ceramic products mainly include roof tiles, structural blocks and bricks, which have high plasticity, requiring considerable amounts of water for their shaping through extrusion. In the subsequent drying process, water is removed from the moulded material using significant amounts of thermal energy (Inocente et al., Reference Inocente, Nandi, Rosso, de Oliveira and Zaccaron2017; Nield & Simmons, Reference Nield and Simmons2019; Nicolas et al., Reference Nicolas, Vlasova, Aguilar, Kakazey, Cano, Matus and Puig2020). Nevertheless, some clays have no appreciable plasticity and therefore do not require considerable amounts of water for extrusion.
The drying of ceramic materials has been studied extensively in the past (Toei, Reference Toei1985; Toei et al., Reference Toei, Okazaki and Tamon1994; Ben Mabrouk & Belghith, Reference Mabrouk S. and Belghith1995; Ketelaars et al., Reference Ketelaars, Pel, Coumans and Kerkhof1995; Zanden, Reference Zanden1996) in an attempt to optimize this process. These studies, however, were limited by their slow drying cycles (>10 h). Recent studies have focused on shorter drying times (<3 h), with an emphasis mainly on the nature of the raw materials used (Zaccaron et al., Reference Zaccaron, Nandi and Bernardin2021, Reference Zaccaron, Nandi, Dal Bó, Arcaro and Bernardin2022).
Fast drying (~60 min) is most often used for ceramic materials with low water contents (typically <8%). This means that the use of fast drying for red ceramics is not simple, as the highly plastic clays used in red ceramics have water contents that exceed 20% and can reach 25%. Thus, the removal of water at high heating rates may lead to the formation of drying cracks, which reduce the mechanical strength of the material or even render it unusable. Thus, the use of fast drying in the red ceramics sector requires the study of clays and compositions that allow for adequate extrusion whilst only requiring short drying times (<120 min) for the reduction of water without promoting the appearance of permanent defects in the dried sections.
Hence, the study of clay-based ceramic formulations for the manufacture of red ceramics using the fast-drying process should include careful analysis of the plasticity of the clay by means of its mineralogical composition and the nature and granulometric distribution of its particles. This approach may allow the elimination of water at greater evaporation rates without causing permanent defects in the material.
Although the physicochemical and mineralogical properties of the clays used in red ceramic formulations could facilitate the mixing process and minimize losses incurred during formation and thermal treatment (drying and firing), studies focused on the plastic behaviour of clays to determine those compositions suitable for extrusion, especially for fast-drying processes, remain scarce. This study aims to analyse the plasticity behaviour of various clays used in the fast-drying production of red ceramics.
Materials and methods
Three clays, namely yellow clay (AM), grey clay (AC) and green clay (AV), were collected from a quarry located 5 km from the city of Itu, state of São Paulo, Brazil, at an altitude of ~583 m; the latitudes and longitudes of their sources are shown in Fig. 1.

Fig. 1. Schematic map of the locations of the leading Brazilian sedimentary basins and collection points of the raw materials used in the study.
The AM samples were collected from a hill slope occurring over a wide geographical area, being obtained from thick and homogeneous deposits in easy-to-access topographical locations outside of flood areas. The AC samples were obtained from a horizontal formation at a depth of >30 m, requiring excavation. The samples were homogeneous, obtained from thick deposits gathered by mining. Finally, the AV sample was collected from horizontal layers, requiring excavation. However, the layers are thin and close to the surface, thereby facilitating extraction.
Approximately 150 kg of each raw sample were collected from five different sites in the corresponding quarry locations. Through a quartering process (Tan, Reference Tan2005), each sample was homogenized and reduced to 80 kg for the laboratory tests. The remaining material was stored in plastic bags.
The samples were dried in a laboratory oven (Deleo, Brazil) at 45 ± 5°C until reaching a constant weight. Once dehydrated, the AM clay was homogenized in a HNTB 100 homogenizer (Natreb, Brazil) and subsequently disaggregated in an LN-15 laboratory roller mill (Natreb, Brazil), while the AC and AV clays were ground for 5 min in a CT-058 hammer mill (Servitech, Brazil) with a 3-mm sieve opening (minimum opening used in an industrial mill).
For the characterization, the clays were ground in a porcelain mortar and passed through a 200-mesh sieve (American Standard Test Sieve Series (ASTM), 74-μm aperture). The chemical analysis of the samples was conducted using X-ray fluorescence (XRF) spectrometry (Bruker S2 Ranger, Germany). The loss on ignition (LOI) of the samples was determined after calcination at 1000°C for 3 h. The mineralogical analysis was conducted using X-ray diffraction (XRD; Bruker D8 Phaser, Germany) with Cu-Kα1 radiation (λ = 1.5406 Å) at 30 kV and 30 mA and at a scanning range of 2–72°2θ and a scanning rate of 2° min–1. Semiquantitative phase quantification was conducted using the rational analysis method. The clay fraction (<2 μm) was determined by employing the NBR 7181 technical standard (ABNT, 2016). Thermogravimetric (TG) analysis was performed in a simultaneous analyser (Netzsch 409 Jupiter F3, Germany) at a heating rate of 10°C min–1 from room temperature to 1000°C in synthetic air. The particle-size distribution was determined using laser diffraction (CILAS 1064, France) in the range of 0.04–500 μm for 60 s using sodium salt (PL/G, Lamberti, Brazil) as the dispersant. The residues (i.e. non-silty/clayey material) retained on the 325-mesh sieve (44-μm aperture) after wet sieving were collected and sieved in an electromagnetic shaker (BerTel, Brazil) for 5 min using a set of sieve apertures of 590, 420, 297, 210, 149, 105 and 74 μm.
Clay minerals are negatively charged because of the permanent charges generated by the isomorphic substitutions in the octahedral and tetrahedral sheets and the formation of negative charges at their edges (Ammann et al., Reference Ammann, Bergaya and Lagaly2005). The cation-exchange capacity (CEC) is the ability of the clay to retain cations to balance this negative charge. In this study, CEC was determined using methylene blue adsorption (AFNOR, 1998). The amount of methylene blue adsorbed by the clay sample indicates the ability of the clay to adsorb cations from a solution, thereby predicting the reactivity of the clay based on the CEC.
To determine the specific surface area and open pore volume distribution, the clay samples were analysed in powder form, outgassed in a vacuum at 300°C for ~3 h and analysed in a Nova 1200e apparatus (Quantachrome, UK) using liquid nitrogen as the adsorbate. The results were determined using the Brunauer–Emmett–Teller (BET) and Barrett–Joyner–Halenda (BJH) mathematical approaches (Brunauer et al., Reference Brunauer, Emmett and Teller1938).
The compositions of the studied clays were determined using the mixture design of experiments (DoE). Formulations of various contents of the studied clays were investigated (Fig. 2). According to the vertices of the diagram in Fig. 2 and the two-way (side) and three-way (centroid) interactions, 10 mixtures were defined, including pure clays (100%), to optimize the mixture design. The mixture design provides an effective mathematical model to predict the properties of the original components and their combinations at specific proportions.

Fig. 2. Triaxial diagram of the developed compositions.
The LL, PL and plasticity index (PI) of the samples were obtained using the indentation method at consistencies (applied forces) of 1 and 46 N for LL and PL, respectively, using a cone penetrometer (Natreb, Brazil).
Analysis of variance (ANOVA) was used to obtain a regression equation for the relationship between the PI experimental data and the content of the used clays in the investigated formulations. The ANOVA was performed using the software Statistica v.10 (Statsoft, USA) at a significance level of 95% (p = 0.05).
Finally, for the preparation of the Winkler diagram, granulometric analysis of the formulations was carried out by sieving and sedimentation; the latter is appropriate for determining the particle-size distribution of clay-based ceramic compositions based on Stokes’ Law (Stokes, Reference Stokes1852) and in accordance with Brazilian standard NBR 7181 (ABNT, 2016). A total of 1 kg of each formulation was dried in an oven at 110 ± 5°C (Solab SL-100, Brazil) and ground to determine the hygroscopic humidity. In this procedure, the samples were sieved to determine particle sizes of between 0.075 and 76 mm. The sieving process was divided into coarse sieving, which refers to the particles retained on the 2.0-mm sieve (10 mesh), and fine sieving, which refers to the particles that passed through the 2.0-mm sieve. The equivalent diameters of the fine fraction of the sample were calculated. Assuming approximately spherical particles, Stokes’ Law was applied to relate the sedimentation velocity and particle diameter (NBR 7181; ABNT, 2016). The particle-shedding velocity was obtained indirectly by measuring the suspension density after stirring to achieve homogenization. A densimeter was used to measure the density at regular time intervals. The densimeter reading was correlated with the particle drop height. From these results, a Winkler diagram was employed to help determine which of the studied formulations were suitable for the manufacture of red ceramics.
Results and discussion
Chemistry and mineralogy
Table 1 presents the results of the chemical analysis of the clay samples conducted using XRF spectrometry.
Table 1. Chemical composition of the clay samples obtained using XRF spectroscopy.

The clays are composed mostly of SiO2. Clays with SiO2 contents >70 wt.% are not preferred in ceramics because of their undesirable reactions with other oxides that generate undesirable phases at low firing temperatures (Monsif et al., Reference Monsif, Zerouale, Idrissi Kandri, Mozzon, Sgarbossa and Zorzi2019). The AM clay had the greatest silica content (>66 wt.%), followed by the AC clay (62 wt.%) and the AV clay (59 wt.%), which are similar values to those obtained for commonly used raw materials in red ceramic manufacturing (Nandi et al., Reference Nandi, Zaccaron, Fernandes, Dagostin and Bernardin2014; Inocente et al., Reference Inocente, Nandi, Rosso, de Oliveira and Zaccaron2017). The raw materials exhibited Fe2O3 contents >5 wt.%, which provide a reddish colour after firing, making them suitable for the manufacture of red ceramics (Dondi et al., Reference Dondi, Raimondo and Zanelli2014; Pardo et al., Reference Pardo, Jordan and Montero2018; Harrati et al., Reference Harrati, Manni, Hassani, Sdiri, Kalakhi and Bouari2020). The total content of fluxing agents (Na2O and K2O) was >5 wt.% in the AC clay, whereas the contents in the AV and AM clays are >4 and >2 wt.%, respectively. The presence of potassium is attributed mainly to muscovite mica and orthoclase, which occur in the AV clay. These oxides favour the formation of melt during sintering, thereby reducing the porosity and increasing the mechanical strength of the products (Dondi et al., Reference Dondi, Ercolani, Melandri, Mingazzini and Marsigli1999; Cavalcante et al., Reference Cavalcante, Dondi, Ercolani, Guarini, Melandri, Raimondo and Rocha e Almendra2004; Zanelli et al., Reference Zanelli, Raimondo, Guarini and Dondi2011; Conserva et al., Reference Conserva, Melchiades, Nastri, Boschi, Dondi and Guarini2017).
The LOI is attributed to the dehydroxylation reactions of silicates, the combustion of organic matter and the decomposition of carbonates (Eliche-Quesada et al., Reference Eliche-Quesada, Sandalio-Pérez, Martínez-Martínez, Pérez-Villarejo and Sánchez-Soto2018). The LOI values in the studied clays varied between 4.8 and 6.5 wt.%, which are typical values for red ceramics. High LOI values can increase porosity in the ceramic material after sintering (Achik et al., Reference Achik, Benmoussa, Oulmekki, Ijjaali and Moudden2021).
The AM and AC clays are rich in quartz (36 and 33 wt.%, respectively), whereas the AV clay has a small quartz content (4 wt.%; Fig. 3 & Table 2). Kaolinite was detected in the AM clay (34 wt.%) and trace montmorillonite was observed in the AV clay. The main minerals that comprise the raw materials are quartz and muscovite mica. Quartz is essential in the drying process because it can act as an auxiliary in the extrusion process, as a deplasticizer that facilitates the extrusion process and as a capillary former that facilitates the fast-drying process (Crozetta et al., Reference Crozetta, Nandi, Rosso, Zaccaron and Niero2016).

Fig. 3. XRD traces of the investigated clay samples.
Table 2. Mineralogical composition of the raw materials obtained using XRD analysis.

A = albite; C = calcite; CH = chlorite; K = kaolinite; M = muscovite; MT = montmorillonite; O = orthoclase; Q = quartz.
The thermal analysis curves of the samples show some similarities (Fig. 4). The TG analysis shows the mass losses at temperatures <100°C, corresponding to water evaporation (Nieto et al., Reference Nieto, Abad and Azañón2008). The AV clay exhibits a greater mass loss (~5.5 wt.%), which indicates the significant impact of this temperature range on this clay, affecting the fast-drying process negatively.

Fig. 4. TG analysis of the investigated clay samples.
The AM and AC clays have smaller mass losses at <100°C (~2 and ~1 wt.%, respectively), which are more suitable for the fast-drying process. In addition, for the AC clay, a greater mass loss (~5 wt.%) was observed in the 300–500°C temperature range.
Particle-size analysis
The particle size of the raw material is essential for optimizing ceramic manufacturing processes, as a suitable particle size eliminates the production of certain defects. This property is fundamental for clays because the mineralogical composition could influence the physical parameters of the raw material. In some cases, the particle size could affect the mechanical strength, permeability and density of the material. Finer particles can promote the packing of particles, thereby increasing the density and mechanical resistance of the material. In addition, such tightly packed particles could reduce water flow from the interior to the surface, thereby inhibiting drying and increasing the duration of the drying cycle significantly. Thus, the particle-size distribution is very relevant to the plasticity of compositions for application in red ceramics (|Monteiro & Vieira, Reference Monteiro and Vieira2004). Figure 5 shows the cumulative particle-size distributions and results curve based on the particle-size distributions of the clay samples.
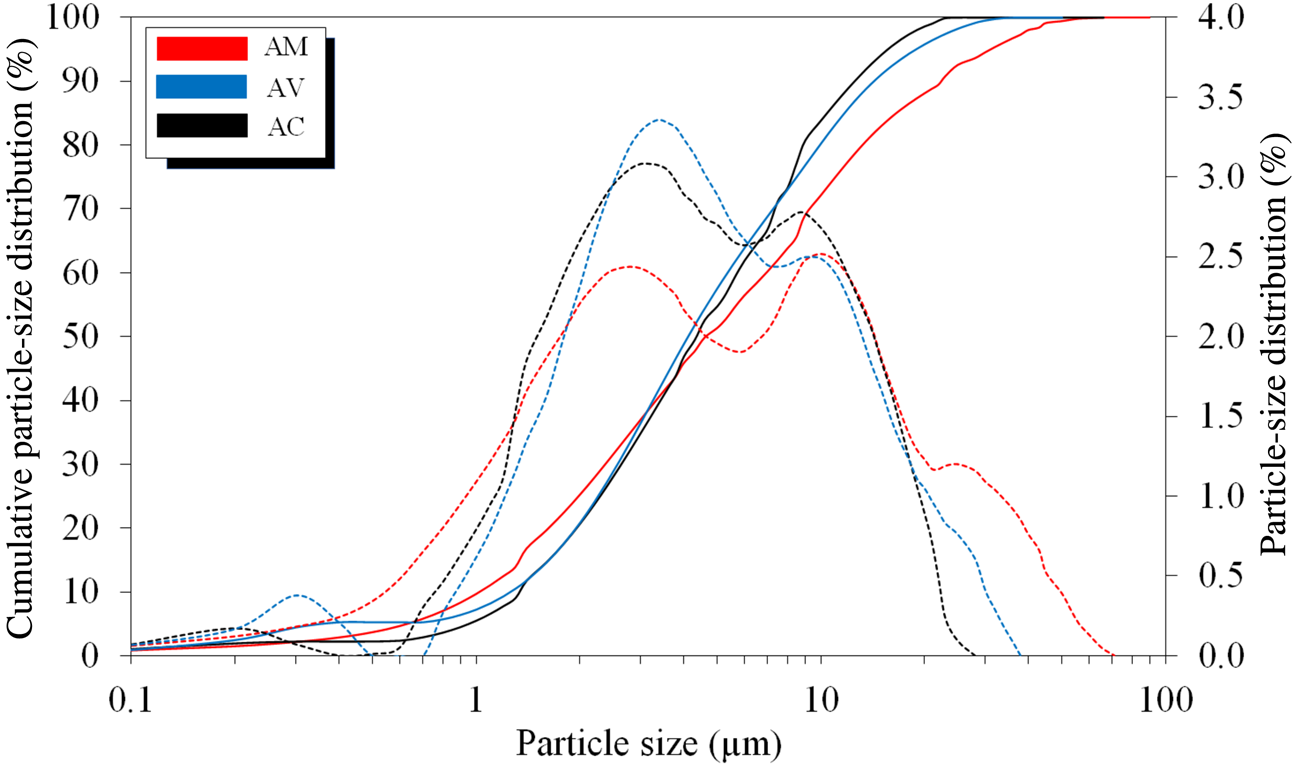
Fig. 5. Cumulative value distribution and particle-size distribution of the raw materials: solid lines = cumulative value distributions; dashed lines = particle-size distributions.
The AC and AV clays have trimodal distributions, with their first peaks of ~10% of particles having sizes <1 μm. The AM clay exhibits a bimodal behaviour.
As these clay particles are not spherical, the same treatment as that used for spherical particles with lower density values was used to determine the packing density. The results for the particle-size distributions of the raw materials with accumulated fractions of 10, 50 and 90 wt.%, the average particle diameters (D m) and their size fractions and the amounts of residue (coarse material) retained on the ASTM 325-mesh sieve (44 μm) are shown in Table 3.
Table 3. Size distribution (μm), average particle diameter (μm), contents of various sizes (wt.%) and contents of coarser particles (>44 μm; wt.%) of the raw materials.

The AM clay has a coarser particle-size distribution, with an average particle size >9 μm, whereas the AC and AV clays have similar particle-size distributions. However, the AM clay contains the largest proportion of the <2 μm size fraction; this is also true of the 20–44 μm size fraction. The coarser particles retained on the 325-mesh sieve (>44 μm) can be disaggregated using dispersion equipment.
The coarser particles in the clay (i.e. non-clay materials and sand) facilitate various stages of the production process; thus, they are important to ensuring the quality of the red ceramics by promoting the fast-drying process (Oliveira, Reference Oliveira2011). Common impurities in clays, such as quartz, reduce shrinkage because they are non-plastic materials (i.e. they have minimal interactions with moisture and consequently do not cause shrinkage; Crozetta et al., Reference Crozetta, Nandi, Rosso, Zaccaron and Niero2016). In the AC clay, 57.7 wt.% of particles were >44 μm, which would facilitate the drying process by assisting in the formation of capillaries and promoting water flow. However, excessive amounts of particles of this size could decrease the mechanical strength of such products (Nicolas et al., Reference Nicolas, Vlasova, Aguilar, Kakazey, Cano, Matus and Puig2020). Thus, the AV clay was the most plastic due to its small coarse-particle content (7.5 wt.%). The AM clay contained more coarser particles than the AV clay but less than that of the AC clay, which is typical of sandy clays used in the production of red ceramics.
The AC and AV clays were ground in a laboratory hammer mill. However, their great hardness values inhibited fragmentation, rendering them unsuitable for use in traditional red ceramic preparation procedures. Crude residues should have a homogeneous particle-size distribution to facilitate the extrusion and drying stages.
According to the particle-size distribution of the raw waste (Table 4), the AM and AV clay samples were finer because the majority of their waste was finer than 100 mesh. The AC clay had a coarser particle size mainly composed of particles retained in the 50 mesh sieve (>60 wt.%). The coarser-particle contents for the AC and AV clays were influenced by the grinding process, which was standardized, as has been presented previously in this work.
Table 4. Retained particles obtained by sieving the raw materials.

CEC, specific surface area and pore volume
Figure 6 shows the CEC results obtained from the methylene blue adsorption test compared with the clay mineral contents (Table 1). The AV clay exhibited the greatest CEC due to the abundance of clay minerals in this clay (Tables 2, 3 & 5). A greater clay mineral content results in a greater CEC.

Fig. 6. Correlation between CEC and clay mineral content.
Table 5. Specific surface areas and pore volumes of the clay samples.

The AV, AM and AC clays consisted of 50.1, 49.5, and 28.2 wt.% clay materials, respectively (Table 2). A greater CEC value results in the adsorption of greater quantities of methylene blue molecules in a given clay mass (Arab et al., Reference Arab, Araújo and Pejon2015).
Although the AM and AV clays had comparable clay contents, the AV clay had a greater CEC, a smaller average particle diameter (Table 3) and the largest specific surface area (Table 5). These differences can be ascribed to the particle sizes of the clays (De Kimpe et al., Reference De Kimpe, Laverdiere and Martel1979; Petersen et al., Reference Petersen, Moldrup, Jacobsen and Rolston1996; De Jong, Reference De Jong1999). Thus, by correlating the CEC values and mass loss behaviours of the studied raw material samples (Fig. 4), the AV clay, which had the greatest CEC value, had the greatest water loss up to 100°C (~5.5 wt.%), followed by the AM clay (~2 wt.%) and the AC clay (~1 wt.%). In the red ceramic manufacturing process, the great water loss up to 100°C observed for the AV clay, or a material exhibiting similar behaviour, can increase the evaporation rate to too great an extent and lead to the generation of cracks during the fast-drying process; therefore, their content in the ceramic formulation must be moderate or even reduced to zero.
The results regarding the specific surface area of the clay samples are listed in Table 5. The specific surface area is dependent on several variables, such as the type and amount of clay minerals, the CEC and the particle size (De Kimpe et al., Reference De Kimpe, Laverdiere and Martel1979; Petersen et al., Reference Petersen, Moldrup, Jacobsen and Rolston1996; De Jong, Reference De Jong1999). The AV clay had the greatest specific surface area, followed by the AM and AC clays. As expected, increasing the clay fraction and decreasing the particle diameter (Tables 1 & 3) increased the specific surface area. A great specific surface area indicates the greater reactivity of the samples, including greater water adsorption on the surfaces of the clay particles (Grohmann, Reference Grohmann1972). Thus, by correlating the CEC with the difficulty of water elimination by drying, it can be understood that the AV clay in the formulations should be modified. Moreover, the cumulative volume of BJH desorption from the pores was greater for the AM clay (8.88 × 10−2 cm3 g–1) and AV clay samples (8.11 × 10−2 cm3 g–1) than that of the AC clay sample (5.36 × 10−2 cm3 g–1).
Plasticity of the formulations
The characterization results were used to prepare ten formulations from the studied clays. The experimental process and analysis were performed using the mixture design methodology. The formulations adopted in this study are presented in Fig. 7 and Table 6. The vertices and centroids of the restricted regions in Fig. 2 were analysed to determine the points for the experimental design with complex constraints.

Fig. 7. Force (N) applied for the indentation of the formulations as a function of the water content (wt.%).
Table 6. Clay ceramic formulations (mixtures; wt.%) using the selected raw materials according to the mixture design.

Plasticity is an essential property in the manufacture of red ceramics, indicating the workability of the raw material (Modesto & Bernardin, Reference Modesto and Bernardin2008; Moon, Reference Moon2016; Spagnoli & Feinendegen, Reference Spagnoli and Feinendegen2017; Baghdad et al., Reference Baghdad, Bouazi, Bouftouha, Hatert and Fagel2019). The plasticity results of the materials determined using the indentation technique are presented in Fig. 7. The LL, PL and PI of the samples were calculated from the equations obtained from the regression analysis and are presented in Table 7.
Table 7. Regression equation, PL, LL, PI and PI/LL ratio values and corresponding classification of each studied formulation according to Oliveira (Reference Oliveira2011) and Moreno-Maroto & Alonso-Azcárate (Reference Moreno-Maroto and Alonso-Azcárate2018).

aMathematical expressions were obtained using Excel™ software.
F = force; W = water content.
The water content used for formulation F3 to reach the PL and LL was significantly greater than those for the other formulations. As formulation F3 corresponds to 100 wt.% AV clay, the greater specific surface area and CEC indicate a greater amount of water to be needed in the forming process by extrusion. In contrast, the opposite behaviour was observed for formulation F2 (100 wt.% AC clay), which has the smallest specific surface area and CEC. Clays with greater plasticity have less resistance to deformation because plastic clays need greater water contents for moulding. Plasticity occurs because of the lubricating action of water between the lamellar particles of clays (Modesto & Bernardin, Reference Modesto and Bernardin2008). Clays with greater water contents could develop cracks during drying.
Oliveira (Reference Oliveira2011) purposed the following classification of clays according to their PI:
• 0 < PI < 1: non-plastic clays
• 1 < PI < 7: low-plasticity clays
• 7 < PI < 15: moderate-plasticity clays
• PI > 15: high-plasticity clays
However, Moreno-Maroto & Alonso-Azcárate (Reference Moreno-Maroto and Alonso-Azcárate2018) introduced a new parameter to evaluate the plasticity of clays: the PI/LL ratio. Clays with a PI/LL ratio ≤ 0.33 can be considered low-plasticity clays, those with a PI/LL ratio < 0.33 and >0.5 are moderate-plasticity clays and those with a PI/LL ratio >0.5 are high-plasticity clays.
The plasticity classifications of the formulations studied according to Oliveira (Reference Oliveira2011) and Moreno-Maroto & Alonso-Azcárate (Reference Moreno-Maroto and Alonso-Azcárate2018) are presented in Table 7. These classifications are very good indications of clay plasticity. There were some acceptable differences between classifications depending on the used criteria, demonstrating the complexity of defining a parameter that indicates the best clay to be used in a given process. According to the classification of Moreno-Maroto & Alonso-Azcárate (Reference Moreno-Maroto and Alonso-Azcárate2018), all investigated formulations in our work could be used in red ceramic manufacturing, except formulation F1 (high plasticity) and excluding formulations F2 and F3 as these were pure clays. Therefore, other criteria needed to be used in our work to determine the best potential formulations for fast-drying red ceramics.
The interaction with water and the workability of the formulation decreased as the plastic content with deformation resistance of the clay decreased. Most of these clays contained abundant minerals that adsorb small amounts of water on the particle surface, such as quartz. Thus, moisture variations, although small, resulted in significant variation in the force required for indentation/deformation.
The results obtained were validated by statistical analysis. Table 8 shows the PI results obtained through ANOVA and plotted as a response surface (Fig. 8). A reliability threshold of 95% was employed. For the analysis, a higher F-value indicates greater significance and a lower p-value suggests greater reliability.

Fig. 8. PI response surface for the formulations studied (F1–F10).
Table 8. ANOVA of the PI values of the investigated formulations.

The model that is statistically significant with 95% confidence (i.e. p < 0.05) is highlighted in bold.
df = degrees of freedom; MS = mean squares; SS = sum of squares.
The plasticity of clays is influenced in a complex way by their mineralogical and granulometric characteristics. This makes it difficult to predict the LL and PL values of a clay material based on its composition; at most, it is possible to identify general trends that can provide indications of the degree of workability (Marsigli & Dondi, Reference Marsigli and Dondi1997). The PI tended to increase as AM clay was incorporated into the mixtures, whereas the AV and AC clays were plasticity reducers.
Equation 1 shows the mathematical expression that best fits the PI and clay content experimental data for the raw materials and formulations investigated in this work:

where x is the AM clay content (wt.%), y is the AV clay content (wt.%) and z is the AC clay content (wt.%).
Figure 9 presents the classification of the extrusion of the studied formulations in a Holtz and Kovacs diagram (Fig. 9a) and according to their extrusion workability (Fig. 9b). Although the graphs in Fig. 9 have been developed for PL and LL values obtained using the Atterberg method, our experimental data, obtained using the indentation method, fit these graphs very well.

Fig. 9. Classification for the extrusion of the formulations: (a) on the Holtz and Kovacs diagram and (b) according to extrusion workability.
Figure 9a shows a Holtz and Kovacs diagram (i.e. PI as a function of the LL of the investigated formulations; Holtz & Kovacs, Reference Holtz and Kovacs1981). All of the prepared formulations are classified within the low- and moderate-plasticity fields, including the F1, F2 and F3 formulations, (pure AM, AC and AV clays, respectively). The F1 formulation (AM clay) exhibited the greatest PI value and behaved as an illite and montmorillonite clay, although these minerals were not present in its composition. This might be explained by the presence of muscovite mica that is similar to illite and the lack of low-plasticity minerals, such as albite and orthoclase, although significant amounts of quartz were present. The F3, F5 and F8 formulations are within the illite clay area of the diagram. Thus, they are considered formulations of greater plasticity than formulation F1. The low PI values of the F2, F4, F6 and F9 formulations are related to their greater feldspar (albite) content and AC clay contents of 100.0, 50.0, 50.0 and 66.6 wt.%, respectively.
Formulations F2, F4, F6 and F9 are in the region of low-plasticity clays. The PI/LL ratio values (Moreno-Maroto & Alonso-Azcárate, Reference Moreno-Maroto and Alonso-Azcárate2018) were: F2 = 0.37, F4 = 0.41, F6 = 0.38 and F9 = 0.42 (Table 7). Formulations F2 and F6 (lower PI/LL ratio values) are farther from the region comprising moderate-plasticity clays, while formulations F4 and F9 are closer to this region, as they have greater PI/LL ratios.
The plastic properties of the clay samples are indicated in the extrusion workability factor graph (Casagrande, Reference Casagrande1932; Casagrande, Reference Casagrande1948; Gippini, Reference Gippini1969) in Fig. 9b. This diagram shows two ranges of plasticity values: an optimal and an acceptable one for processing of the clayey material. This means that we would be able to achieve high extrusion quality during industrial processes with these clays (Marsigli & Dondi, Reference Marsigli and Dondi1997). This may serve as a basis for defining and optimizing the formulations that could be used for the fast-drying process. The PI value is essential to determining the applicability of such formulations. Formulations F7 and F10 exhibited good extrusion behaviour and formulation F3, which corresponds to the pure AV clay, had acceptable extrusion properties. However, working with only one clay is not recommended during production processes. Thus, the formulations should be corrected before defects can develop during the manufacturing process. In Fig. 9b, only formulations F5 and F8 are present within the optimal extrusion zone (Gippini, Reference Gippini1969), indicating that they would be easy to work with, thereby improving the extrusion process and enabling great productivity (Marsigli & Dondi, Reference Marsigli and Dondi1997).
Thus, when the PL and PI data obtained using the indentation method were used to evaluate the extrusion workability factor (Fig. 9b), similar results as discussed previously were observed. Formulations F3, F5, F7, F8 and F10 could be used in extrusion; however, the use of formulation F3 would not be recommended, as it consists only of one clay (AV clay). Therefore, the graphs in Fig. 9 could be helpful, within an acceptable margin of safety, when choosing formulations with the greatest possibility of being used successfully in extrusion.
Figure 10 shows the suitability of the prepared formulations for obtaining ceramic products based on the Winkler diagram, which is an essential tool for use when processing red ceramics (Winkler, Reference Winkler1954).

Fig. 10. Projection of the clay formulations on a Winkler diagram (Winkler, Reference Winkler1954). The fields are defined as follows: A = standard bricks; B = vertically perforated bricks; C = tiles and masonry bricks; D = hollow bricks.
Based on the particle-size distributions of the clays, the manufacture of specific types of products and mixing of raw materials can be achieved. Clay minerals and formulations located close to the apex in Fig. 10 for the <2 μm fraction have greater plasticity. Greater plasticity is advantageous because it increases the mechanical strength of the material and decreases wear on the stock preparation and production equipment. However, formulations with greater plasticity require more water, rendering the drying stage difficult and increasing the energy demand to remove the structural water from the clay minerals during the firing stage. According to these results, all of the prepared formulations are suitable for manufacturing masonry bricks and tiles (Strazzera et al., Reference Strazzera, Dondi and Marsigli1997; Semiz, Reference Semiz2017).
The technique of using DoE and ANOVA for the formulation of ceramic compositions from the studied clays was adequate for the analysis of plasticity behaviour during extrusion. Through the extrusion workability factor, it was possible to define the formulations that could be used for the fast-drying process, as only the formulations that presented optimal and acceptable extrusion conditions could be used. In this study, four formulations were selected (F5, F7, F8 and F10), which, according to the plasticity analysis and the Winkler diagram, are suitable for the manufacture of fast-drying red ceramics.
Summary and conclusions
This work assessed three clay raw materials from Itu, São Paulo, Brazil, for the manufacture of fast-drying red ceramics. The clays consisted principally of SiO2, Al2O3, Fe2O3, K2O and MgO and contained abundant muscovite mica, quartz, kaolinite and albite. All of the clay samples had Fe2O3 contents >5 wt.%, which provides the reddish colours of the ceramics. The Al2O3/SiO2 ratios indicated significant clay mineral contents. The formulations with AM and AC clay contents exhibited great plasticity. The AC clay was more suitable for the preparation of red ceramic formulations for fast drying. The greater content of coarser particles of this clay (57.74%) compared to its AM and AV clay counterparts (17.15% and 7.55%, respectively) increased the permeability of the material and facilitated drying. Among the 10 prepared formulations, formulation F5 (50.0 wt.% AM clay and 50.0 wt.% AV clay), formulation F7 (33.3 wt.% AM clay, 33.3 wt.% AC clay and 33.3 wt.% AV clay), formulation F8 (66.6 wt.% AM clay, 16.7 wt.% AC clay and 16.7 wt.% AV clay) and formulation F10 (16.7 wt.% AM clay, 16.7 wt.% AC clay and 66.6 wt.% AV clay) presented the most appropriate PL and PI values within the acceptable levels for extrusion. Through the extrusion workability factor, it was possible to determine the formulations that could be used in the fast-drying process, as only the formulations that presented optimal and acceptable extrusion conditions can be used for this purpose. Four formulations were selected (F5, F7, F8 and F10), which, according to the plasticity analysis and the Winkler diagram, are suitable for the manufacture of fast-drying red ceramics. Therefore, this study provided notable findings on the development of red ceramic formulations processed by extrusion for the manufacture of fast-drying red ceramics. Although every company that manufactures red ceramics uses clays with varying characteristics from those used in this study, the evaluation based on the chemical, mineralogical and granulometric composition and the methodology for determining the PI can be used as a guide for determining the composition necessary to allow formation by extrusion in the manufacture of fast-drying red ceramics.
Financial support
The authors thank the Coordination for Higher Education Improvement (CAPES/Brazil, processes no. 88887.502321/2020-00 and 88887.356961/2019-00) and the National Council for Scientific and Technological Development (CNPq/Brazil, processes no. 306992/2019-1, 307761/2019-3, 310328/2020-9 and 304054/2021-6) for the financial support of this work.
Supplementary material
To view supplementary material for this article, please visit https://doi.org/10.1180/clm.2023.9.