Nomenclature
- A
-
peak-to-peak amplitude of plunging motion
- b
-
span of half-wing
-
${C_L}$
-
lift coefficient
-
${C_M}$
-
root-bending moment coefficient
- c
-
chord length
- f
-
oscillation frequency
- H
-
height of mini-spoiler
- h
-
displacement of wing
- k
-
reduced frequency;
$\pi fc/{U_\infty }$
- Q*
-
normalised Q – criterion;
$Q{c^2}/U_\infty ^2\;$
- Re
-
Reynolds number
- sAR
-
semi aspect ratio
- T
-
period of plunging motion
- t
-
time
-
${U_\infty }$
-
freestream velocity
-
${V_{mag}}$
-
velocity magnitude
-
${V_{pl}}$
-
plunging velocity
- x
-
chordwise distance
- x s /c
-
normalised chordwise distance of spoiler
- y
-
cross-stream distance
- z
-
spanwise distance
- α
-
geometric angle-of-attack
-
${\alpha _{eff}}$
-
effective angle-of-attack
-
${\alpha _{gust,amp}}$
-
amplitude of gust angle
-
$\varLambda$
-
sweep angle
-
${\omega _z}$
-
spanwise vorticity
-
${\omega _x}$
-
streamwise vorticity
1.0 Introduction
The detrimental lift changes for aircraft encountering gusts, turbulence or during manoeuvres can be substantial. Traditionally, designing aircraft wings to withstand these extreme forces has required reinforcing and adding weight, which compromises fuel efficiency. Loads alleviation can be helpful in designing lighter wing structures, thus improving fuel efficiency. It has been suggested that incorporating technologies to mitigate gust and manoeuvre loads on commercial aircraft could lead to a 20% improvement in endurance, reduce operating cost by 7% and reduce fuel burn by 11% [Reference Haghighat, Liu and Martins1–Reference Xu and Kroo3]. Conventionally, this is achieved by using relatively large/heavy mechanical surfaces such as trailing-edge flaps. However, their significant mass results in low-frequency responses. This necessitated research on high-frequency actuators such as fluidic devices [Reference Al-Battal, Cleaver and Gursul4] and mini-spoilers [Reference Heathcote, Gursul and Cleaver5]. Various flow control actuators proposed for loads attenuation have been reviewed by Li and Qin [Reference Li and Qin6].
Regardless of the type of the actuators, flow physics of loads alleviation mainly depends on the chordwise location of the actuators. The main mechanisms are ‘separation control’ near the leading-edge and ‘circulation control’ near the trailing-edge. Figure 1 compares the lift reduction performance with either separation control near the leading edge or circulation control near the trailing edge at small angles of attack. Note that although mini-spoilers are illustrated in this figure, similar characteristics are also observed for fluidic actuators. For the circulation control near the trailing edge, mini-spoilers work similarly to a Gurney flap but are positioned on the suction side of the aerofoil rather than the pressure side. The potential flow calculations estimate a constant lift change (e.g. around
${\rm{\Delta }}{C_L} = - 0.2$
for the spoiler height of H/c = 0.04) as a function of angle-of-attack if the spoilers are treated as a flap with a 90-deg of flap angle [Reference Liu and Montefort7]. The slope of the lift coefficient of the aerofoil with the spoiler remains the same as
$2\pi .\;$
At low angles of attack, these spoilers induce a small region of separated flow characterised by counter-rotating vortices [Reference Liebeck8–Reference Date and Turnock11]. However, their effectiveness diminishes as the angle-of-attack or gust angle increases since they become immersed in a separated flow.
In contrast, when mini-spoilers are positioned near the leading edge, they produce separated shear layer and totally separated flow over the aerofoil as sketched in Fig. 1. The lift change is small at low angles of attack. At higher angles of attack, leading-edge mini-spoilers achieve a much greater reduction in lift compared to trailing-edge spoilers due to the separated flow over the aerofoil. If the separated flow with leading-edge mini-spoilers is modelled as the Kirchhoff-Rayleigh flow [Reference Kirchhoff12, Reference Rayleigh13], the free-streamline theory estimates the lift coefficient at small angles of attack as
${C_L} = 2\pi \alpha /4$
, representing a quarter of the lift coefficient anticipated under the thin-aerofoil theory for attached flows, equivalent to a lift reduction of
${\rm{\Delta }}{C_L} = - \frac{3}{4}\left( {2\pi \alpha } \right)$
. This significant reduction in the lift is consistent with the experimental measurements reported by Heathcote et al. [Reference Heathcote, Gursul and Cleaver5].
The separation control and circulation control sketched in Fig. 1 for stationary aerofoils are significantly modified in the case of oscillating aerofoils. Even for clean aerofoils (no actuation for loads attenuation), flow may separate near the leading edge, and the shear layer may roll up into discrete vortices [Reference McCroskey14]. In a simulation of aeroelastic bending deformation of wings as well as large-wavelength gusts, leading-edge vortices generally have increased the mean lift and maximum lift on clean plunging aerofoils [Reference Chiereghin, Cleaver and Gursul15]. This increase is correlated with the maximum effective angle-of-attack of the motion, which suggests that plunge velocity (also implying gust velocity) plays an important role. For plunging aerofoils, the mini-spoilers near the leading edge could delay or even prevent the roll-up into a leading-edge vortex (LEV), providing effective lift alleviation [Reference Bull, Chiereghin, Cleaver and Gursul16]. The spoiler increases the distance of the separated shear layer from the aerofoil surface and also modifies the velocity at the separation point, delaying the roll-up into a vortex. However, with increasing plunge velocity, leading-edge vortices develop, and the efficacy of the mini-spoilers diminishes.
More recently, Hadjipantelis et al. [Reference Hadjipantelis, Son, Wang and Gursul17] extended the previous work on the full-span spoilers on aerofoils to the part-span spoilers on finite wings. Both the three-dimensional and two-dimensional spoilers exhibit similar mechanisms of loads attenuation as well as decaying frequency responses with increasing frequency and amplitude of the oscillations. This happens as strong three-dimensionality of the leading-edge vortices develops on clean finite wings with increasing amplitude and frequency of the unsteady wing motion [Reference Yilmaz and Rockwell18–Reference Son, Gao, Gursul, Cantwell, Wang and Sherwin21]. Hadjipantelis et al. [Reference Hadjipantelis, Son, Wang and Gursul17] showed that the finite-span mini-spoilers are not able to modify the strong leading-edge vortices and therefore lose their effectiveness. Whereas the performance of leading-edge spoilers on plunging wings has been well-documented, the performance of trailing-edge spoilers on plunging wings has not been investigated so far. The first objective of this article is to present a direct comparison of the separation control and circulation control on plunging wings.
The second objective is to investigate the effect of wing sweep on plunging wings. For clean swept wings, delta-wing-like leading-edge vortices may remain attached, also displaying vortex breakdown at high-plunge velocities [Reference Gursul and Cleaver22]. It is known that the sweep angle exerts a profound influence on the bending moment as plunge frequency is increased [Reference Chiereghin, Bull, Cleaver and Gursul23]. This is because the movement of the leg of the LEV on the wing is modified. The axial velocity along the vortex filament may exhibit jet-like and wake-like profiles, accompanied by gradual vortex breakdown. Vigorous flow within the leading-edge vortices has been observed in the computational simulations [Reference Garmann and Visbal24]. In a related study of the interaction of a travelling incident vortex with swept wings, there has been evidence of significant flow developing along the axis of the LEV [Reference Qian, Wang and Gursul25]. Shedding of the leading-edge vortices may change from being parallel to the incident vortex to being parallel to the leading edge with increasing angle-of-attack. Full-span mini-spoilers on a swept wing prevents the formation of a coherent LEV along the wing-span [Reference Qian, Wang and Gursul26]. In this article, the performance of both the leading-edge and trailing-edge spoilers on swept wings is investigated and compared. In addition, various mini-spoiler configurations placed on both unswept and swept wings are examined experimentally in a water tunnel. The spoiler placements studied in this research are illustrated in Fig. 2. In addition to the unswept wing (
$\varLambda$
= 0°), a
$\varLambda$
= 30° and a
$\varLambda$
= 40° swept wing were tested (the wing with the highest sweep angle is not shown in this figure).
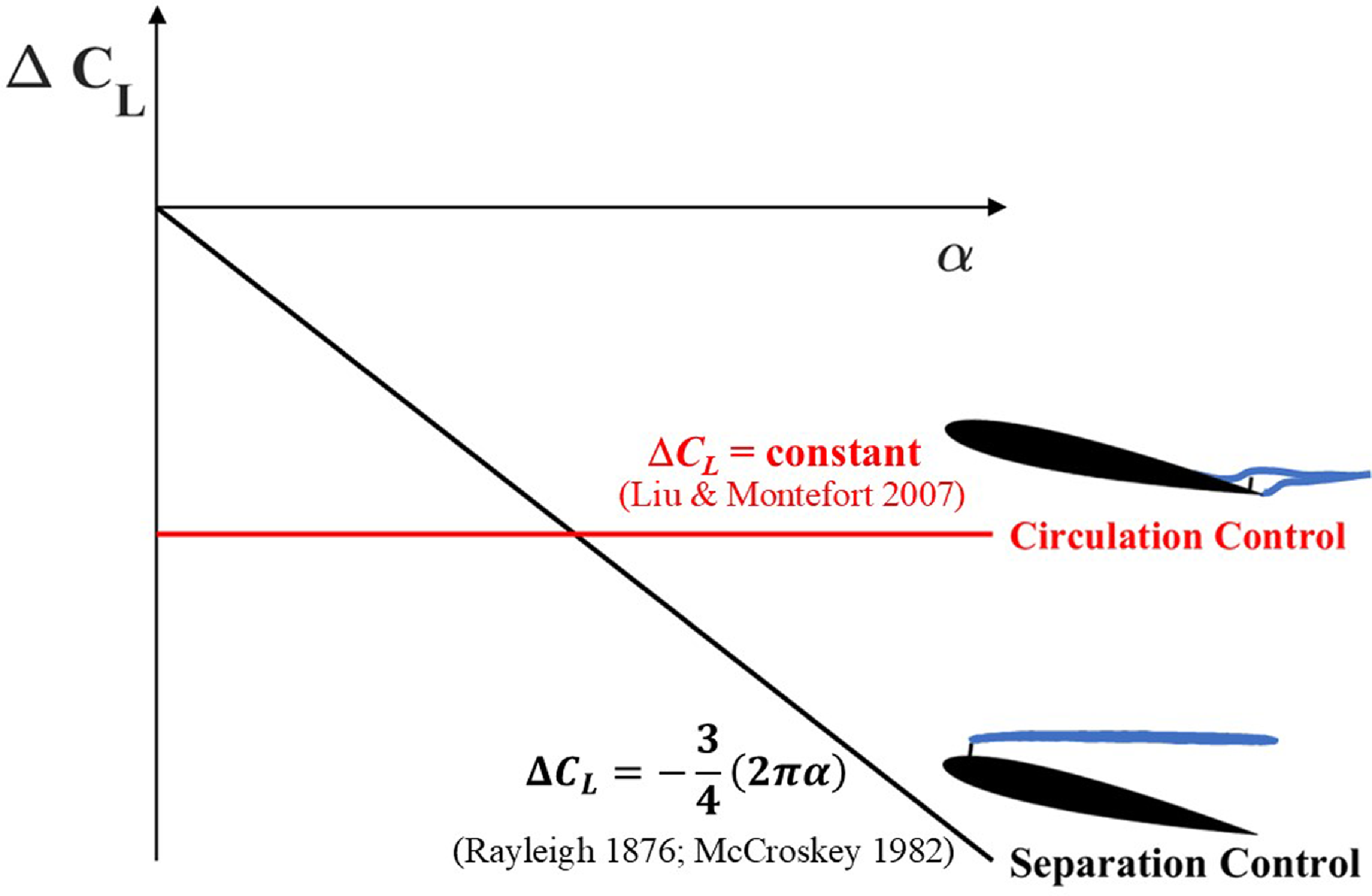
Figure 1. Effects of circulation control and separation control on change of lift coefficient for stationary wings.
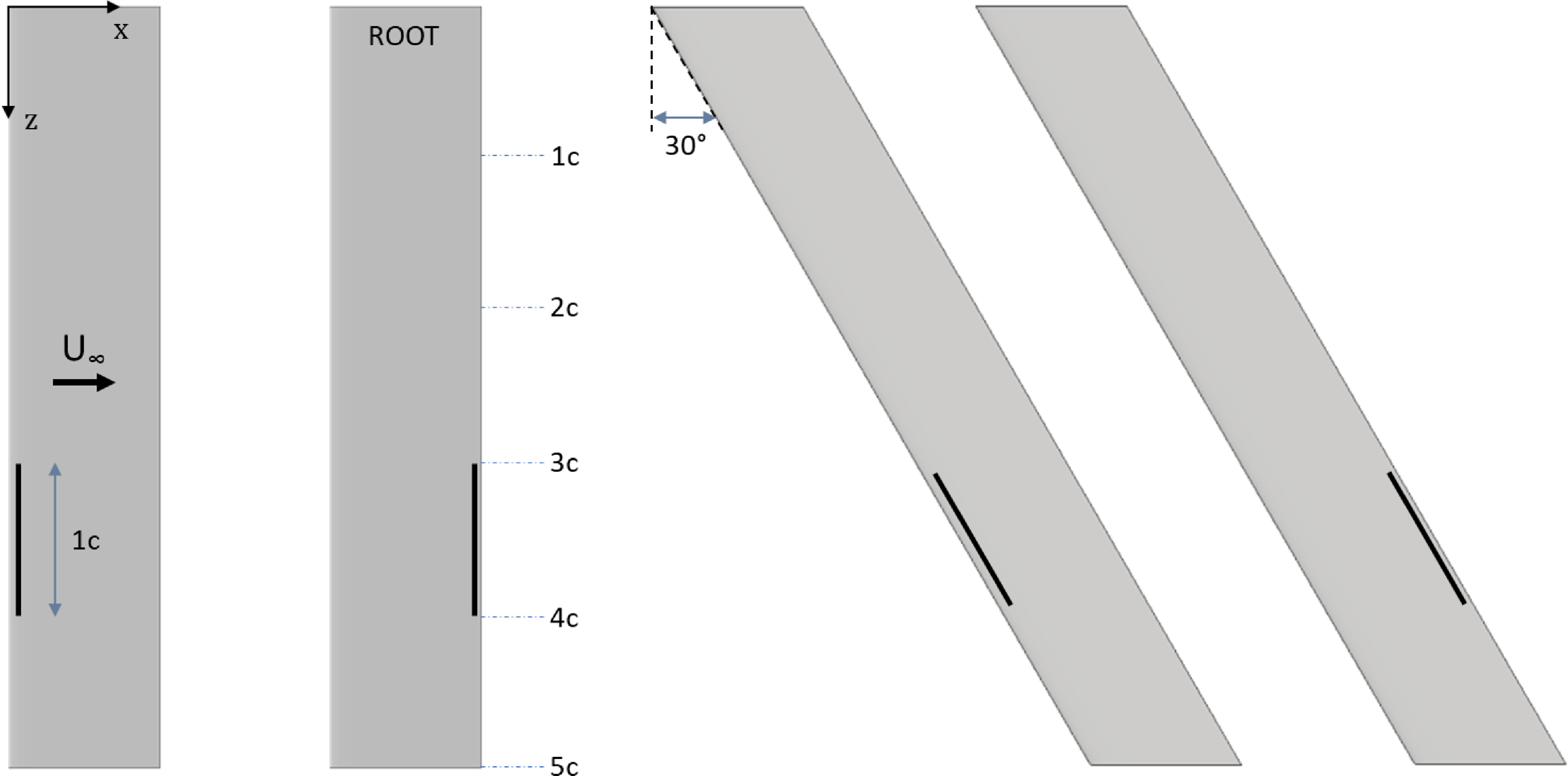
Figure 2. Wing and spoiler configurations tested in the water tunnel.
2.0 Experimental Methods
The experiments were conducted in a closed-loop free-surface water tunnel at the University of Bath, featuring a test section measuring 381 mm in width, 508 mm in depth and 1,530 mm in length, capable of achieving flow speeds up to 0.5 m/s. Turbulence intensity, measured using laser Doppler velocimetry (LDV), was maintained below 0.5%. A rectangular wing with a NACA 0012 profile was submerged in water and subjected to sinusoidal plunging motion perpendicular to the freestream (Fig. 3). The Reynolds number, based on the chord length, was kept constant at Re = 20,000. Sweep angles of
$\varLambda$
= 0°, 30° and 40° were tested, all with a semi-aspect ratio of sAR = 5. Mini-spoilers were added to the wings, positioned at the leading edge and trailing edge on the suction surface, as illustrated in Fig. 2. Detailed force, bending moment and flow measurements were conducted at pre-stall and near-stall angles of attack. Chiereghin et al. [Reference Chiereghin, Bull, Cleaver and Gursul23] reported the stall angles of attack at Re = 20,000 to be approximately
${\alpha _s} \approx 9^\circ $
for both
$\varLambda$
= 0° and
$\varLambda$
= 40° wings.
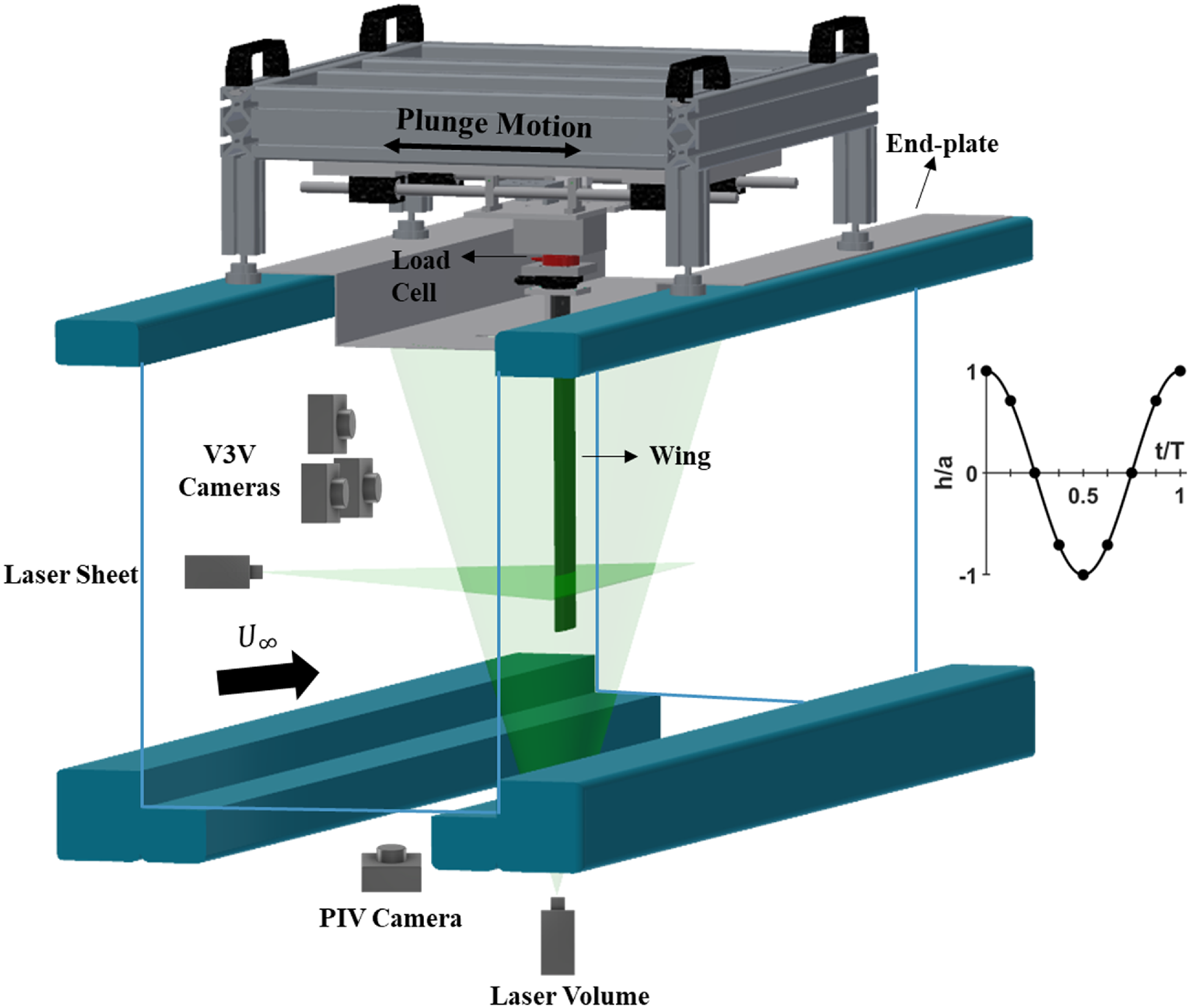
Figure 3. Experimental setup.
The wings, with a chord length of c = 62.7 mm, were manufactured from PA - 2200 polyamide material using selective laser sintering (SLS). They feature a polished, smooth surface and were painted matt black to minimise reflectivity during flow measurements. To enhance structural support and prevent bending, a 25 x 5 mm T800 carbon fiber-reinforced polymer (CFRP) spar was inserted into the wing for about 80% of the span. Two spoiler heights of H/c = 4% and H/c = 8% were tested. The spoilers were constructed from 3-ply zero-degree layout T800 CFRP with a thickness of 0.75 mm. As shown in Fig. 2, each spoiler, spanning one chord length (c), is positioned spanwise between 60% and 80% of the half wing’s span (b), which was previously determined to be optimal for stationary and plunging unswept wings due to the influence of the wingtip vortex [Reference Hadjipantelis, Son, Wang and Gursul17]. To facilitate a direct comparison of the effect of wing sweep on load alleviation performance, the mini-spoilers were kept at the same spanwise location for the swept wings in this study.
The wing was mounted on a manual rotation stage, allowing for precise adjustments of the geometric angle-of-attack with an accuracy of ±0.2°. This rotation stage was connected to a moving carriage via a sensor, which collected data on lift force and root-bending moment. To minimise friction, the carriage was supported by four air bearings, which absorbed bending and torque loads. The plunging motion was facilitated by a Zaber LSQ150B-T3 translation stage, controlled by an X-MCB1 controller. The controller generated a sinusoidal signal to orchestrate the plunging motion, following the function:
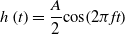
Throughout the study, the normalised peak-to-peak amplitude was kept constant at A/c = 0.5, and the system can achieve the motion up to an accuracy of 2%. The reduced frequency, k, of the plunging motion is defined as:

A range of 0 ≤k ≤ 1.1 was tested in this study, exceeding the certification requirements for a typical single-aisle airliner and going beyond the gust conditions typically encountered during cruise.
2.1 Force and moment measurements
The lift force and root-bending moment were recorded using an ATI Industrial Automation Mini40 six-axis force/torque sensor, positioned at the quarter-chord axis of the wings. The data acquisition was set at a rate 2,000 times the plunging frequency, and the phase-averaged values were derived from 50 cycles. For static measurements, data were collected at a frequency of 1,000 Hz over a duration of 40 seconds. To eliminate inertial effects, the product of the moving mass and the instantaneous acceleration was subtracted from the lift and moment data. The resulting signal was then filtered using two zero-phase Butterworth third-order band-stop filters to remove structural frequencies between 6-10 Hz and 20-60 Hz. Additionally, a zero-phase 200-point moving average filter was employed to minimise random noise.
The changes in the loads were calculated by subtracting the baseline case from the control case, and the changes in the lift and bending moment coefficients were calculated with the following equations:


where b is the span of the half-wing. The measurement uncertainties of the lift and bending moment coefficients depend on the mean angle-of-attack and the reduced frequency. However, the uncertainty of the percentage lift reduction is relatively independent of the mean angle-of-attack, sweep angle and reduced frequency in the range tested [Reference Hadjipantelis27]. It was estimated that the percentage change of the maximum lift and bending moment coefficients,
${\rm{\Delta }}{C_{L,max}}/{C_{L,max}}$
and
${\rm{\Delta }}{C_{M,max}}/{C_{M,max}}$
, between the wing with spoiler and the clean wing (baseline) had an uncertainty of 8% to 9%.
The validation of the force/moment system for the baseline wings of
$\varLambda$
= 0°, 30° and 40° was performed by comparing the lift coefficient across a range of angles of attack, as shown in Fig. 4(a). The measured lift coefficients of the unswept clean wing align well with those reported in literature [Reference Chiereghin, Bull, Cleaver and Gursul23] with the stall angle remaining the same (
${\alpha _s} \approx 9^\circ $
). For the swept wings, the measured lift coefficients at α = 5° and 9° were compared using the independence principle, which assumes that only the flow acting normal to the leading edge affects the aerodynamics [Reference Anderson28]. This principle is mathematically expressed as:
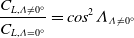
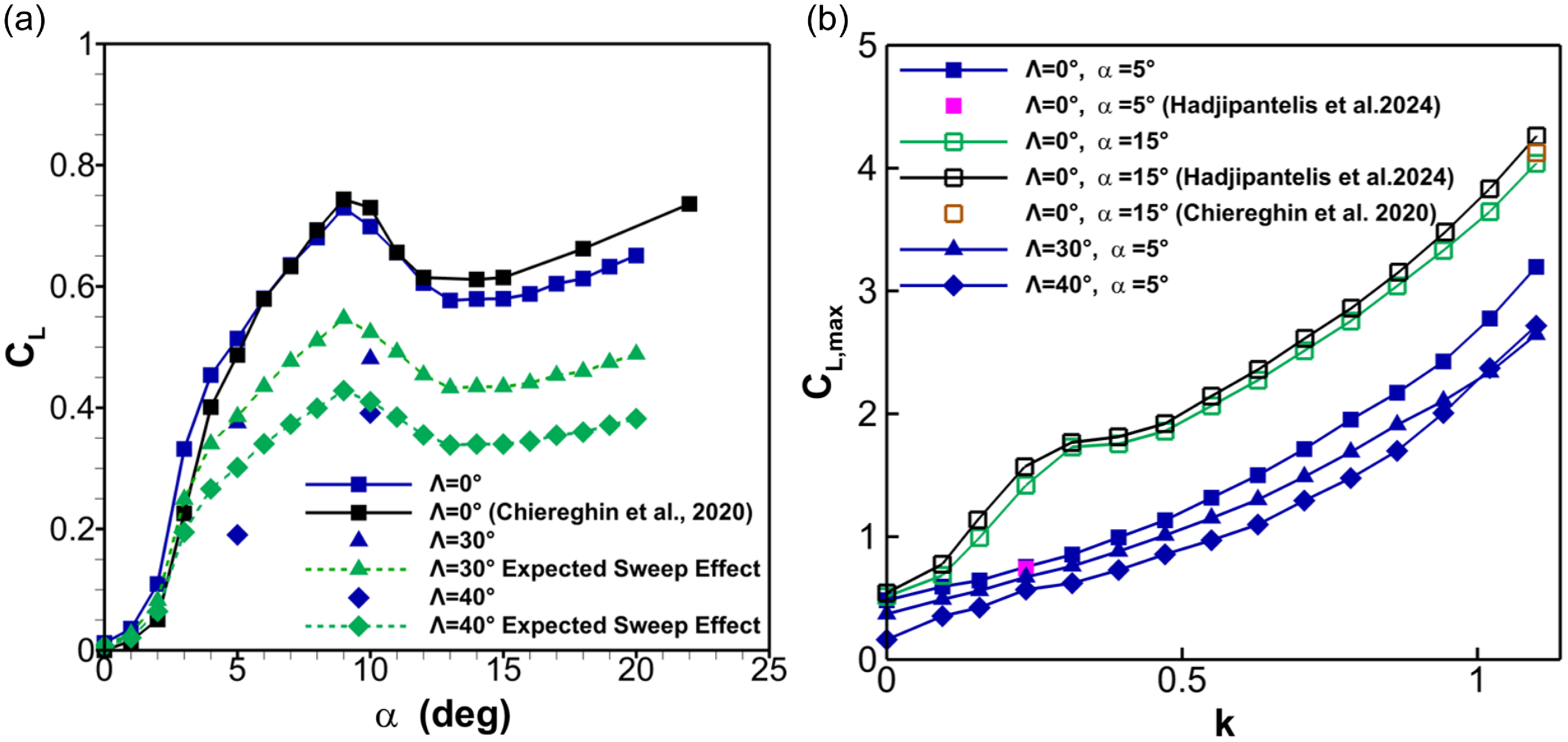
Figure 4. For clean wings, variation of (a) lift coefficient as a function of angle-of-attack for stationary wings; (b) maximum lift coefficient as a function of reduced frequency of the plunging motion;
$\varLambda$
= 0°, 30° and 40°.
Figure 4(a) shows a close consistency between the measured C
L
and the estimated sweep effect, especially for the
$\varLambda$
= 30° wing. However, for the
$\varLambda$
= 40° wing, there is some discrepancy between the estimated C
L
and the measured C
L
at α = 5°. Note that the independence principle is most accurate for wings with smaller sweep angles [Reference Anderson28]. The observed discrepancy for the larger sweep angle can be attributed to the increased prominence of three-dimensional and spanwise flow effects as reported previously at this Reynolds number [Reference Chiereghin, Bull, Cleaver and Gursul23, Reference Qian, Wang and Gursul25, Reference Qian, Wang and Gursul26].
The validation of the force measurements for the oscillating wings is shown in Fig. 4(b), with the maximum lift coefficients presented against the reduced frequency of the plunging motion. For the unswept wing, at angles of attack of 5° and 15°, the maximum lift coefficients were compared over a range of reduced frequencies or at discrete values published in previous studies [Reference Hadjipantelis, Son, Wang and Gursul17, Reference Chiereghin, Bull, Cleaver and Gursul23]. For the fixed angle-of-attack of α = 5°, Fig. 4(b) illustrates that increasing sweep angle results in a decrease in the maximum lift coefficient, possibly due to the independence principle. However, this difference between
$\varLambda$
= 30° and
$\varLambda$
= 40° diminishes at high reduced frequencies.
2.2 Volumetric velocimetry measurements
The volumetric three-dimensional velocimetry system utilised in this research was a TSI V3V™. It is based on defocusing digital particle image velocimetry and has been developed by Pereira et al. [Reference Pereira, Gharib, Dabiri and Modarress29] and Pereira and Gharib [Reference Pereira and Gharib30]. A particle tracking algorithm is used for two-frame three-dimensional particle tracking [Reference Pereira, Stuer, Graf and Gharib31]. The measurements were conducted on the wing’s suction surface. This setup features an EverGreen2 double-pulsed laser (ND: YAG 200 mJ, repetition rate 3.75 Hz) and three 4-megapixel (2,048 × 2,048) 12-bit CCD cameras, each equipped with Nikon AF Nikkor 50 mm f/1.8D lenses. As seen in Fig. 3, the laser beam was shaped into a cone and directed into the test section via a 45° mirror. A specific frame (TSI V3V-9000-CS) was used to mount the cameras, and a TSI model 610036 synchroniser was utilised. The water was seeded with 50
$\mu$
m PSP polyamide particles. Calibration involved focusing the cameras on a calibration plate with a grid of regularly spaced dots positioned at the centre of the test section. The plate was then incrementally moved through the volume section in 5 mm steps, capturing images at each position. Each measurement volume, with a field of view of 140 x 140 x 100 mm, had to be calibrated separately. For the unswept wing, two measurement volumes were used to capture the vortical structures for about 80% of the wingspan, while four volumes were used for the swept wing. Data for multiple volumes were collected separately and merged using reference points either on the unswept wing or on a plate secured from the same mount as the swept wing.
Images were acquired at four instants within a given period (T) with 0.25T increments. For each phase of the measurements, 100 images were captured. Image processing was performed using Insight V3V-4G with an interrogation volume of 8 x 8 x 8 mm with 50% overlap, resulting in a spatial resolution of 4 mm (6.4% of chord length). Processing steps included particle detection, triplet processing, particle tracking and velocity interpolation to generate a regular grid of velocity vectors using Gaussian weighting. The uncertainty was estimated to be less than 3% of the freestream velocity.
2.3 Particle image velocimetry (PIV) measurements
Two-dimensional particle image velocimetry (PIV) measurements were conducted on the wing’s suction surface using a TSI PIV system. This system features an 8-megapixel (3,320 × 2,496) Powerview Plus CCD camera equipped with a Nikon AF Nikkor 50 mm f/1.8D lens, providing a field of view measuring 313 x 235 mm. This system shares the same synchroniser and laser as the V3V system. The water was seeded with hollow glass spheres 8–12
$\mu$
m in diameter. Phase-locked PIV measurements were conducted at the same time instances as for the V3V system, with the same number of images taken. The images were acquired at the mid-span plane of the spoiler. A diagram of the PIV system setup is also shown in Fig. 3. In addition, in order to obtain a qualitative flow pattern near the wing surface and parallel to the chordline, the laser sheet was positioned at approximately 0.10c from the wing’s chordline to ensure flow capture while minimising laser sheet reflections.
Insight 4G software was used to process the images, utilising an interrogation window size of 20 x 20 or 32 x 32 pixels with 50% overlap, achieving a spatial resolution of 1.6-2.8% of the chord length. The measurement uncertainty was estimated to be less than 2% of the freestream velocity. While PIV measurements provide almost 2.5 times finer spatial resolution for the coarser interrogation window size and a wider field of view compared to volumetric velocimetry measurements, the V3V system provides comprehensive insight into vortical structures, spanwise flow and three-dimensional effects influenced by the wing’s finite geometry. Both methods were synergistically employed in this study to leverage their respective strengths and enhance the overall data interpretation.
3.0 Results
3.1 Unswept wings
Figure 5 shows the changes in the maximum lift and bending moment coefficients at pre-stall (α = 5°), stall (α = 9°) and post-stall (α = 15°) angles of attack for the unswept plunging wing with the leading-edge (LE) and trailing-edge (TE) spoilers. Note that the changes in the force/moment coefficients have been normalised by the maximum coefficients of the baseline wing at the corresponding reduced frequency and angle-of-attack. The dashed lines show reduced frequencies (k = 0.24 and 0.94) where flow measurements were performed. With the leading-edge spoiler (x s /c = 0.08), at the pre-stall and stall angles of attack, the maximum percent reduction in lift and moment occurs at k = 0, decreasing as the reduced frequency of the wing plunging motion increases, with minimal reduction observed at higher reduced frequencies. In line with previous studies, the cut-off frequency is defined as the point where the percent reduction in lift and moment either intersects zero or stabilises at higher frequencies [Reference Hadjipantelis, Son, Wang and Gursul17]. However, at the post-stall angle-of-attack, the spoiler shows peak effectiveness around a reduced frequency of k = 0.24, but its load alleviation performance declines at higher reduced frequencies, following similar trends seen at other angles of attack.
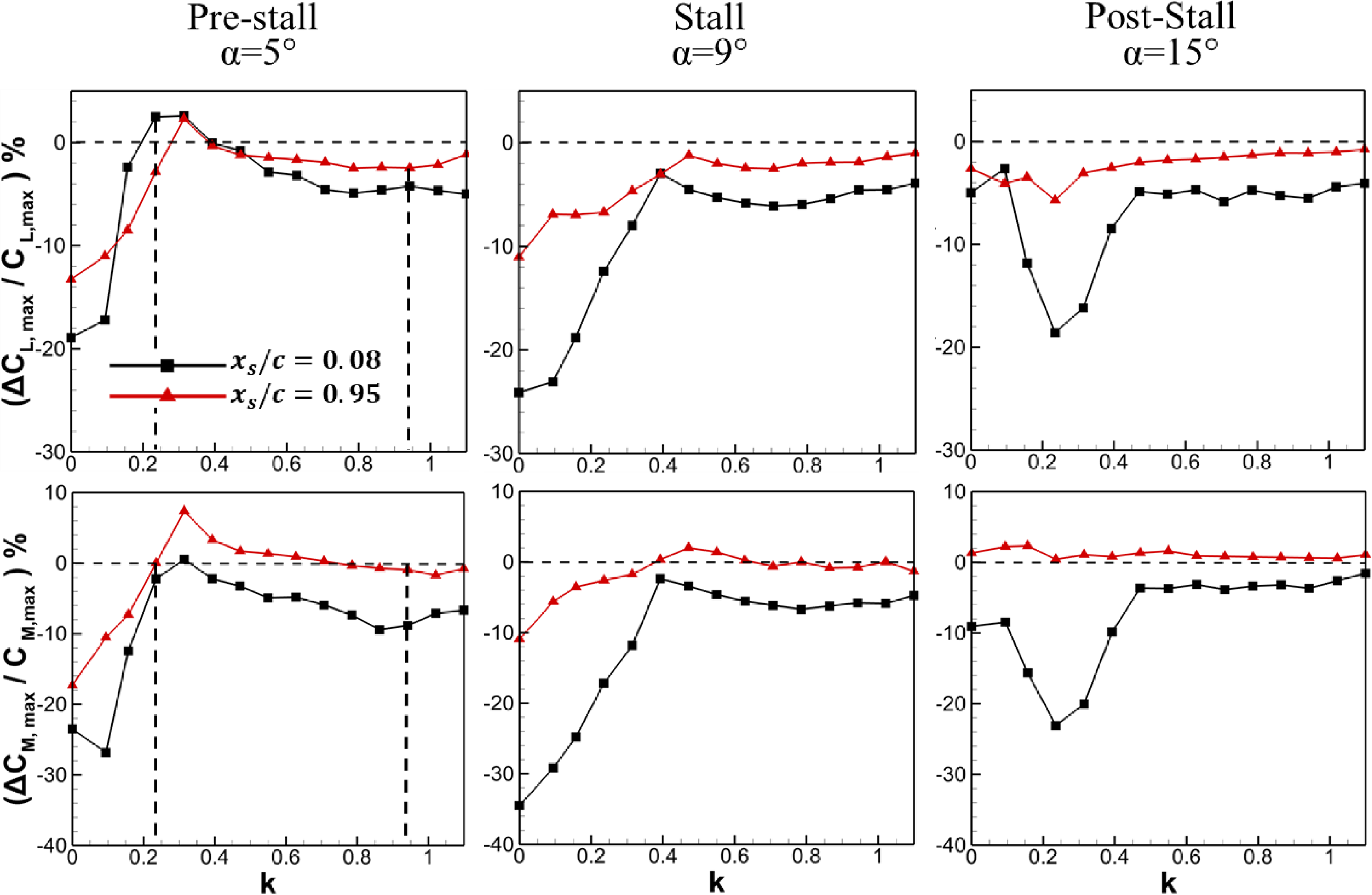
Figure 5. Percent lift and moment reduction for
$\varLambda$
= 0° plunging wing with leading-edge and trailing-edge spoilers. Dashed lines indicate frequencies of k = 0.24 and k = 0.94 for flow measurements, H/c = 4%.
The trailing-edge spoiler exhibits similar frequency response trend to the leading-edge spoiler at the pre-stall and the stall angles of attack, though its maximum percent reduction in lift and moment at k = 0 is significantly less than for the LE spoiler configuration. However, at the post-stall angle-of-attack, the trailing-edge spoiler fails to alleviate the loads. The similarity of the frequency responses between both spoiler placements shows that their cut-off frequencies are closely aligned. Although the magnitude of the lift reduction is larger for the trailing-edge spoiler at pre-stall angles of attack (see, for example, Fig. 1), the percent reduction (effectiveness) of the trailing-edge spoiler is smaller, with most obvious differences observed at k = 0. Note that for both LE and TE spoiler configurations, the trends between lift and bending moment are closely aligned.
The percentage changes in the maximum lift coefficient at the pre-stall angle-of-attack of α = 5° with both 4%c and 8%c spoiler heights are shown in Fig. 6. At lower plunging velocities, the taller spoiler (H/c = 8%) significantly outperforms the shorter one (H/c = 4%) in percent lift reductions, particularly when positioned near the leading edge. However, as the reduced frequency increases, the impact of spoiler height on load alleviation diminishes. For the TE spoiler, the cut-off frequency remains unchanged, but for the taller spoiler placed at x s /c = 0.08, the cut-off frequency is slightly delayed.
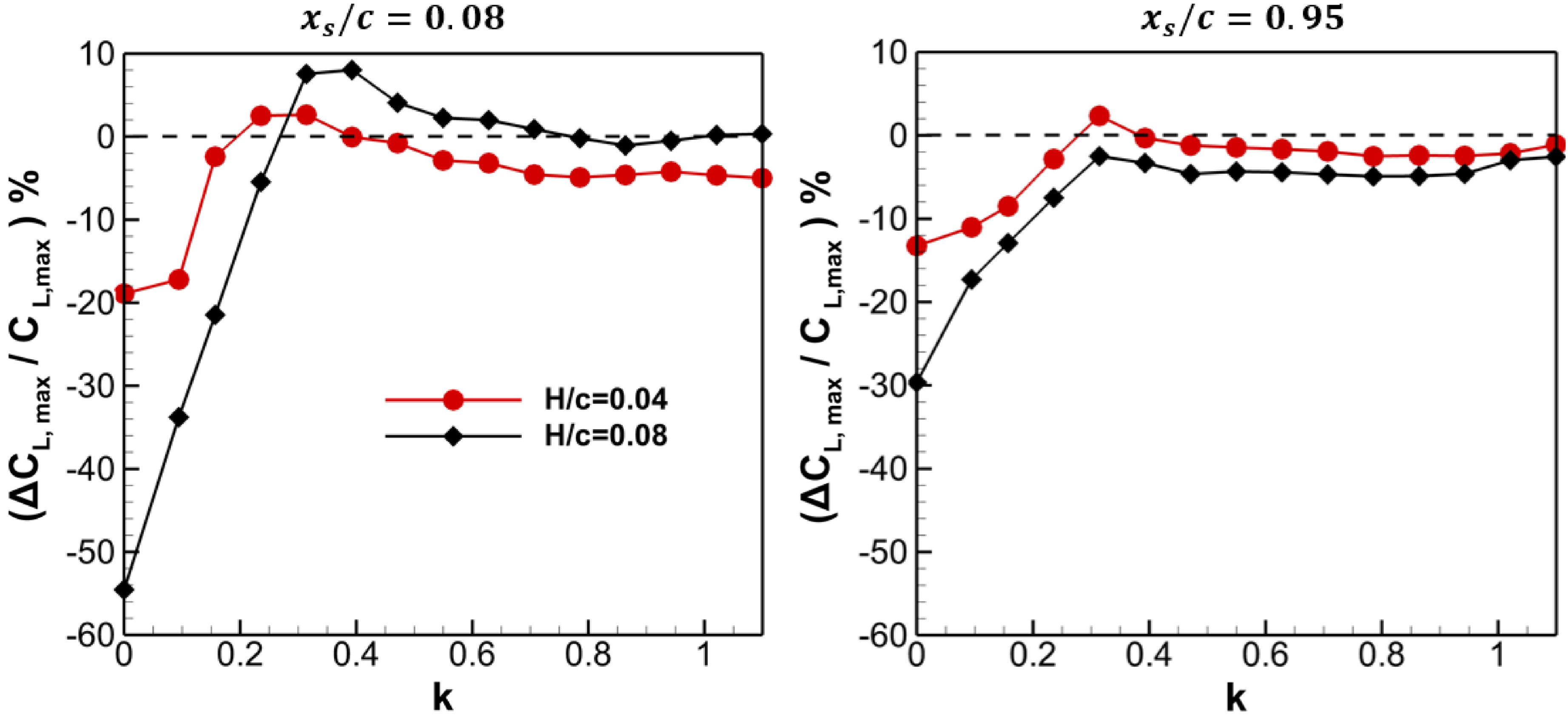
Figure 6. Percentage change in maximum lift coefficient as a function of reduced frequency, for leading-edge spoiler (left) and trailing-edge spoiler (right), H/c = 4% and 8%, α = 5°,
$\varLambda$
= 0°.
In order to show the effects of the leading-edge and trailing-edge spoilers on the flow fields of the stationary wing (k = 0), the magnitudes of the time-averaged velocity derived from the PIV measurements are plotted in Fig. 7 for α = 5°. For the baseline wing, the flow appears to be attached throughout the wing’s surface (within the resolution of the measurements). The leading-edge spoiler (positioned at x s /c = 0.08) induces flow separation from the leading edge that encompasses the whole of the wing’s upper surface. This yields the wing incapable of producing sufficient lift force and results in a significant decrease in the aerodynamic loads (see also Figs 5 and 6). In contrast, the trailing-edge spoiler (located at x s /c = 0.95) generates a small separation region and a small wake behind it. The slope of the streamlines downstream of the spoiler indicates that the spoiler deflects the flow upwards, reducing the effective camber and the circulation of the wing, therefore decreasing the lift. At k = 0, the leading-edge spoiler performs slightly better than the trailing-edge spoiler.
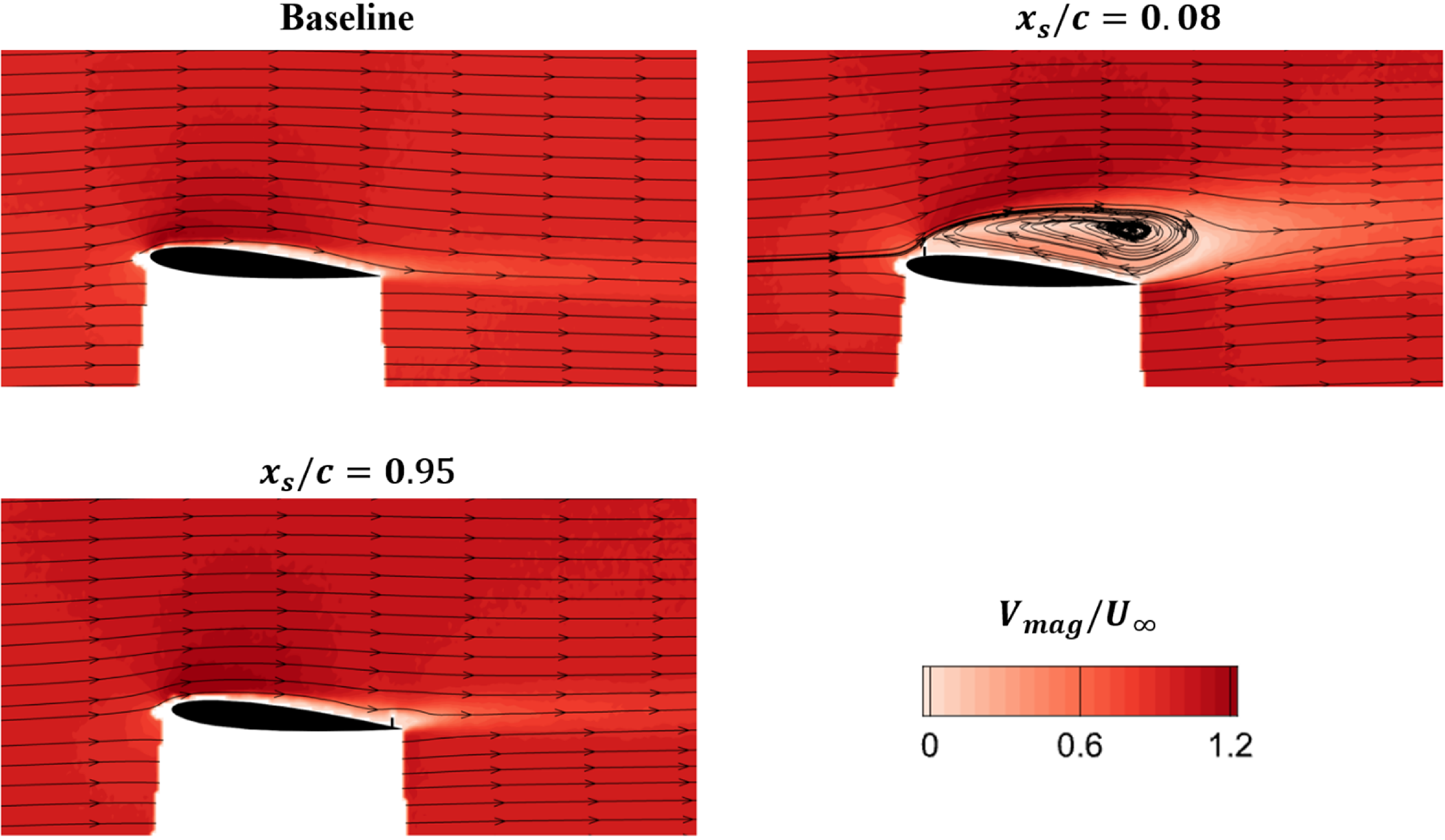
Figure 7. Contours of time-averaged velocity magnitude from PIV measurements for stationary wings with trailing-edge and leading-edge spoilers as well as for baseline wing, α = 5°,
$\varLambda$
= 0°, H/c = 4%.
Next, we examine the flow fields near the cut-off frequency (k = 0.24). Figure 8 presents the phase-averaged velocity magnitudes superimposed with streamline patterns derived from PIV measurements for the baseline wing and with the trailing-edge spoiler at α = 5°. This phase (t/T = 0.25) corresponds to the largest effective angle-of-attack since it is related to the plunging motion and velocity as:

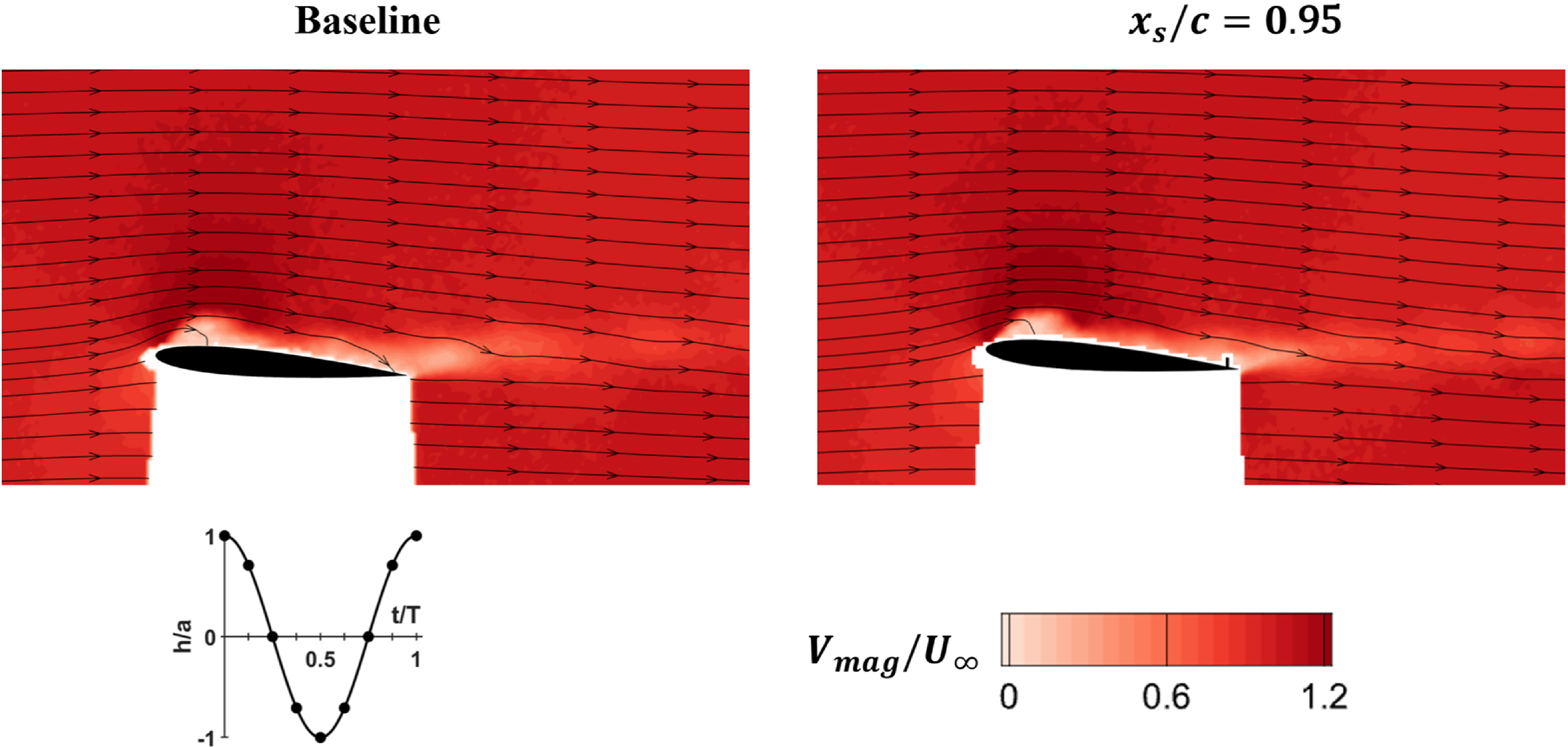
Figure 8. Phase-averaged velocity magnitude contours at t/T = 0.25 from PIV measurements for baseline wing and with trailing-edge spoiler at k = 0.24, α = 5°,
$\varLambda$
= 0°, H/c = 4%.
For the baseline wing, a mild flow separation is observed over the wing that starts near the leading edge due to the increased unsteadiness. Note that the flow field with the spoiler in Fig. 8 is similar to that of the baseline wing case. Hence, the main reason of the cut-off frequency for the trailing-edge spoiler is the leading-edge flow separation. At the cut-off frequency, the spoiler cannot deflect the potential flow (compare with the slope of the k = 0 case in Fig. 7) and the resulting reduction in aerodynamic loads is significantly diminished. The difference between the percent lift reduction of the two spoilers is within the experimental uncertainty in this case (see Fig. 5).
Figure 9 compares the three-dimensional flows over the baseline wing and the wing with the leading-edge spoiler at k = 0.24 for the same angle-of-attack. The phase-averaged vortical flow structures and the near-surface streamlines are plotted at four phases. For visualisation purposes, the three-dimensional vortical structures were identified using the Q–criterion technique, which is the second invariant of the velocity gradient tensor defined as
$Q = 0.5\left( {\parallel {\rm{\Omega }}{\parallel ^2} - \parallel S{\parallel ^2}} \right)$
[Reference Hunt, Wray and Moin32, Reference Jeong and Hussain33]. Here Ω and S are the vorticity and strain tensors, respectively, and
$\|.\|$
represents the Euclidean norm. The isosurfaces of nondimensionalised Q–criterion defined as
${Q^*} = \frac{{Q{c^2}}}{{U_\infty ^2}}$
= 0.25 were coloured by spanwise vorticity and presented in this paper. It has been reported previously that the phase-averaged lift and moment coefficients of both plunging clean wing and the wings with spoilers always become maximum near the maximum effective angle-of-attack (e.g. near t/T = 0.25) for the whole range of reduced frequency tested presently [Reference Hadjipantelis, Son, Wang and Gursul17]. Flow separation is observed over the spoiler at all phases in Fig. 9. The near-surface streamlines suggest a growing separation region during the downward plunging motion, with the recirculation region (‘bubble’) reaching the wing trailing edge at around t/T = 0.25. As a result, the mini-spoiler loses its effectiveness in reducing the maximum lift and moment at this reduced frequency (e.g. Figs 5 and 6). During the upward plunging, the separation region significantly decreases. At t/T = 0.75, which corresponds to the minimum effective angle-of-attack, there is an indication of the reattachment of the flow over the wing. At this point in the plunging cycle, the effective angle-of-attack is negative and therefore the suction (upper) surface becomes the pressure surface, and the presence of the spoiler may also alter the pressure distribution on the suction surface. The combination of these two effects result in a load reduction at t/T = 0.75 [Reference Hadjipantelis, Son, Wang and Gursul17]. Nevertheless, the maximum lift and bending moment observed at around t/T = 0.25 is what drives the spoiler design, as well as the focus of this paper. In summary, for both the leading-edge and trailing-edge spoilers, flow separation near the leading edge is at the origin of performance degradation and cut-off frequency in alleviating the maximum loads.
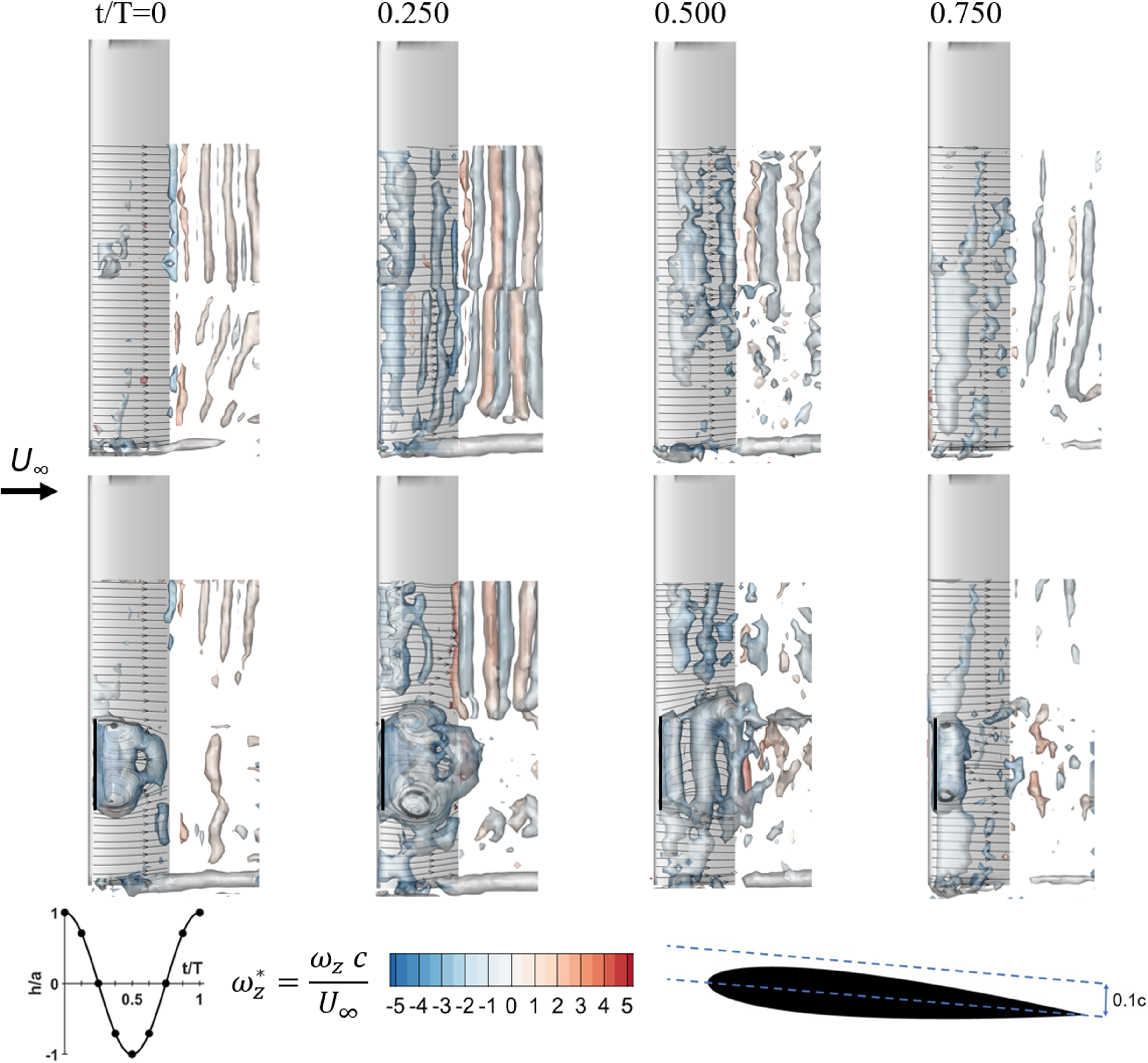
Figure 9. Top views of vortical structures with isosurfaces of Q
* = 0.25, coloured with spanwise vorticity, on the clean wing (top) and with the leading-edge spoilers (bottom) for the case of α = 5°, k = 0.24,
$\varLambda$
= 0°, H/c = 4%.
It has been deduced from Fig. 5 that regardless of the angle-of-attack and spoiler placement, load alleviation worsens at high reduced frequencies. Figure 10 compares the vortical structures of the baseline wing and the wing with the spoilers at both the leading and trailing edges over four phases at k = 0.94. The flow patterns appear nearly identical between the baseline wing and the configuration with the spoiler at x s /c = 0.95. The LEV begins forming as early as t/T = 0.25, fully develops, and reaches the mid-chord by t/T = 0.500. It then moves towards the trailing edge around t/T = 0.75, with the leg moving inboard. The similarities between the trailing-edge spoiler case and the clean wing indicate that the spoiler does not influence the formation of the LEV. With the LE spoiler at x s /c = 0.08, the spoiler triggers flow separation during the downward part of the plunging motion, creating a horseshoe vortex that detaches by t/T = 0.500. The horseshoe vortex is already downstream of the wing by t/T = 0.75. It appears that the horseshoe vortex has minimal influence on the LEV formation. Regardless of the chordwise location of the part-span mini-spoilers, by t/T = 0.75, all cases demonstrate comparable vortical flows, suggesting that the formation of a strong LEV is unavoidable. As the LEV could not be made less coherent or less strong compared to the baseline wing case, load attenuation is not feasible, at least for the parameters used in this study.
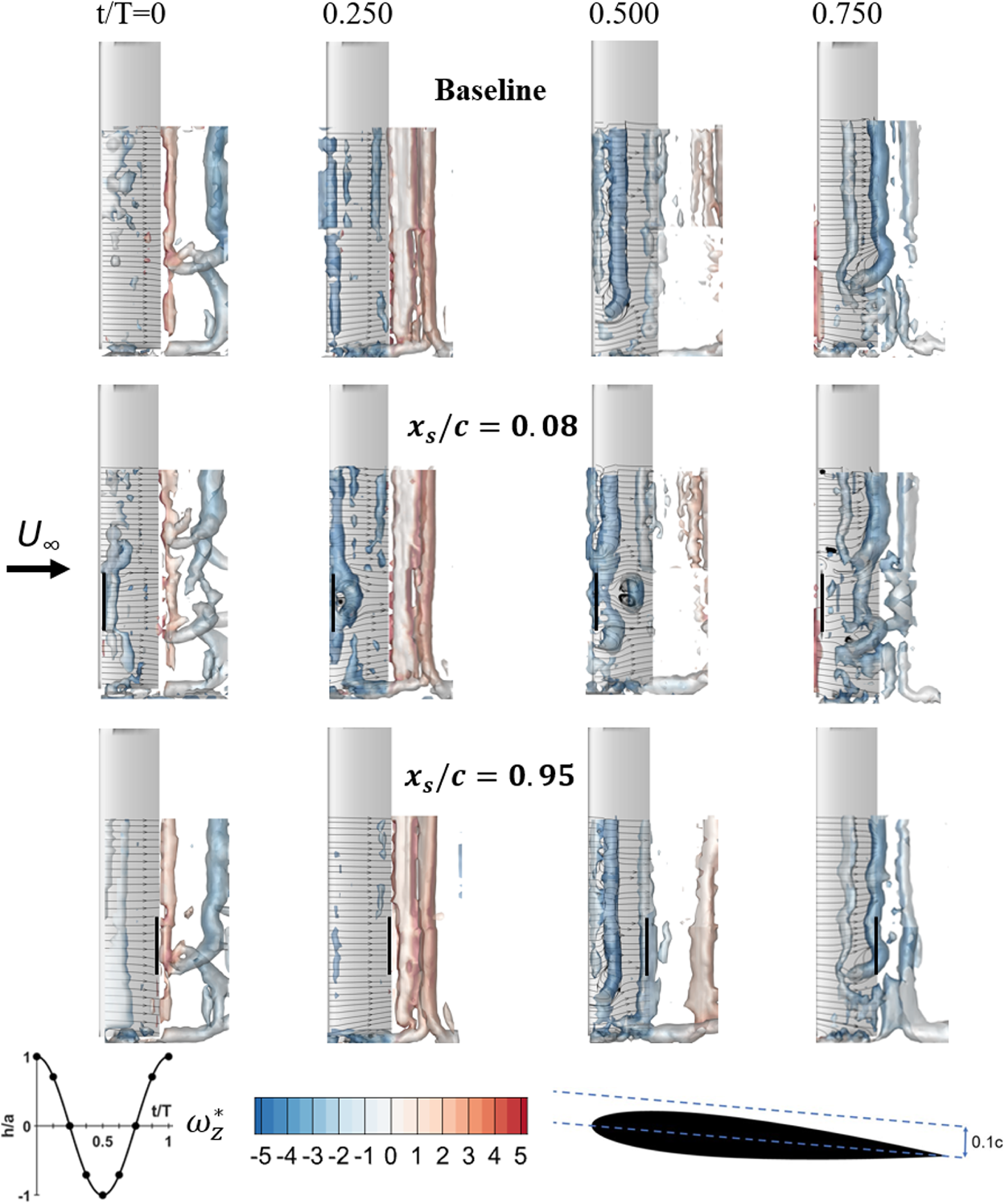
Figure 10. Top views of vortical structures with isosurfaces of Q
* = 0.25, coloured with spanwise vorticity, on the clean wing and with the trailing-edge and leading-edge spoilers for the case of α = 5°, k = 0.94,
$\varLambda$
= 0°, H/c = 4%.
So far, the frequency response of the separation control and circulation control for loads attenuation was considered as a function of the reduced frequency of the plunging motion (see, for example, Figs 5 and 6). If plunging motion is interpreted as a gust, in addition to the reduced frequency, the amplitude of the gust angle should be considered:

Here A is the peak-to-peak plunge amplitude. The percentage change in lift coefficients as a function of equivalent amplitude of gust angle at the pre-stall (α = 5°) and the stall (α = 9°) angles of attack are shown in Fig. 11. The effects of spoiler heights of H/c = 0.04 and 0.08 with the trailing-edge and leading-edge spoiler placements are included. There are similarities between Fig. 11 with Figs. 5 and 6. Once the gust amplitude reaches a certain value, loads attenuation is no longer possible. This critical value of the gust amplitude varies in a range of 5° to 11° for this wing at this Reynolds number. However, the present experiments cannot separate the effects of the gust reduced frequency (k) and the gust amplitude
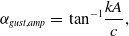
separately as both parameters depend on the frequency of the plunging motion.
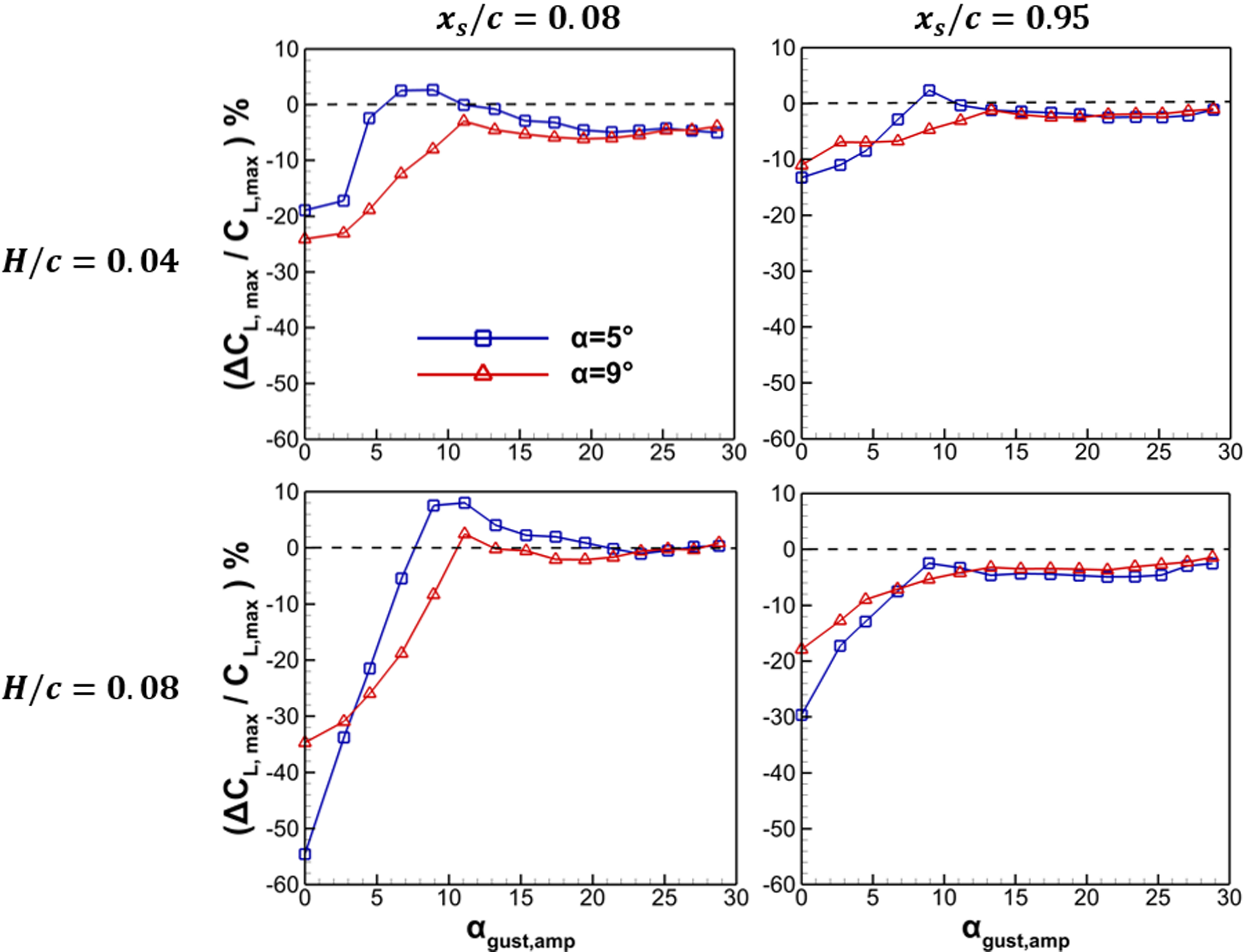
Figure 11. Percentage change in lift coefficient as a function of equivalent amplitude of gust angle of
$\varLambda$
= 0° plunging wing with 4%c (top) and 8%c (bottom) spoiler height with leading-edge (left) and trailing-edge (right) spoiler placement at α = 5° and 9°.
3.2 Swept wings
To analyse the impact of wing sweep angle on the load alleviation capabilities of mini-spoilers, percentage changes in maximum lift and bending moment coefficients for
$\varLambda$
= 0°, 30° and 40° wings with the leading-edge and the trailing-edge spoiler at α = 5° are presented in Fig. 12. The dashed lines represent the frequencies at which flow measurements were conducted to complement the force measurements. It can be observed that the
$\varLambda$
= 30° case, when contrasted with the unswept wing (
$\varLambda$
= 0°), clearly demonstrates that increasing the wing sweep angle diminishes the effectiveness of load alleviation capabilities for both the LE and TE spoiler placements. Nonetheless, for
$\varLambda$
= 30° wing, some degree of load alleviation is attainable for k = 0 and up to the cut-off reduced frequency. Both spoiler placements show similar performance, especially for the bending moment alleviation. Note that both the LE and TE spoiler placements were tested for
$\varLambda$
= 0° and 30° wings, while only the LE spoiler placement was tested for
$\varLambda$
= 40° wing. For the
$\varLambda$
= 40° case, the results indicate that load alleviation is not achievable for this sweep angle, and the variations in loads, even for k = 0, are minimal.
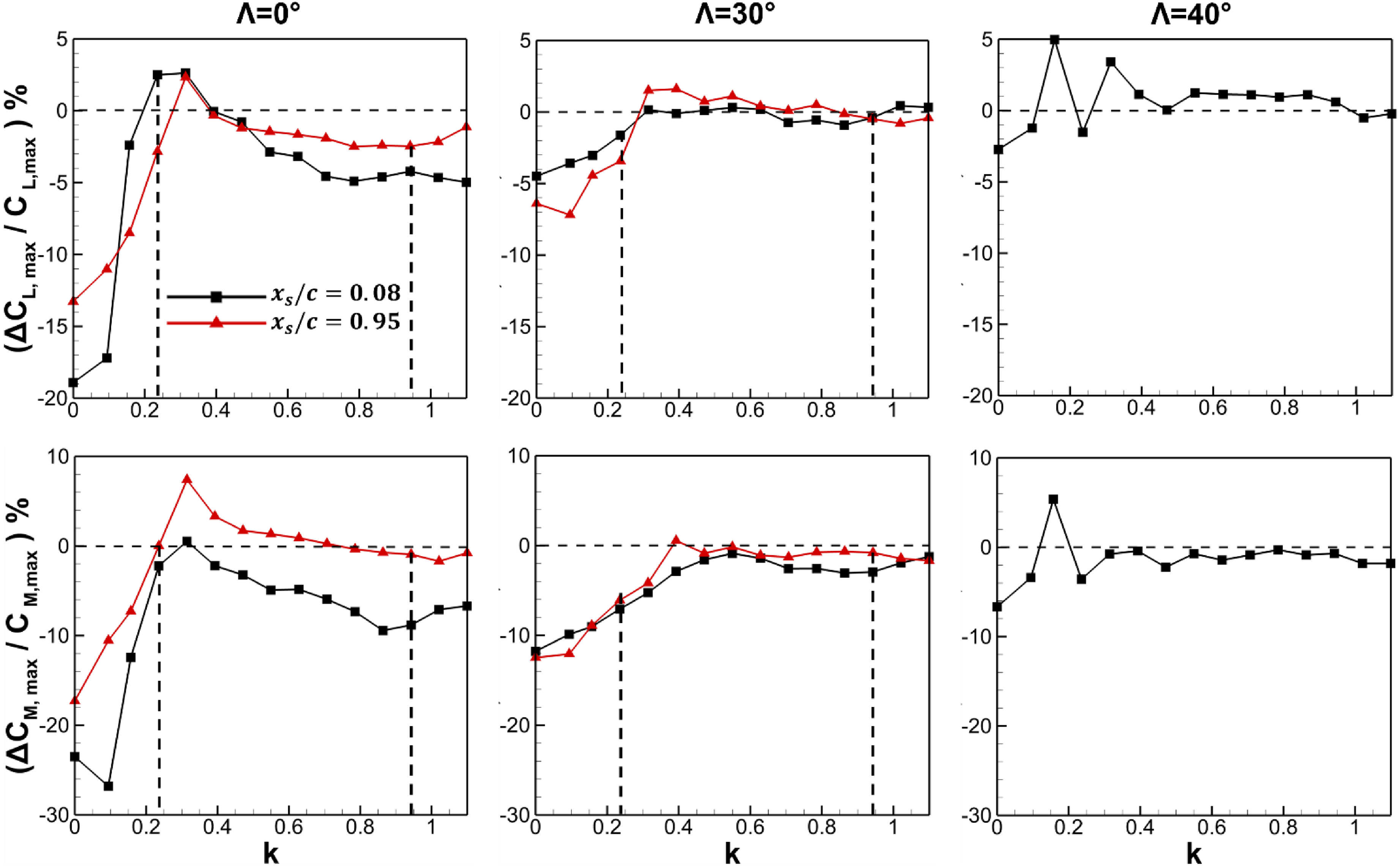
Figure 12. Percent reduction of maximum lift and bending moment coefficient for
$\varLambda$
= 0°, 30° and 40° wings with leading-edge and trailing-edge spoilers for α = 5°. Dashed lines indicate frequencies of k = 0.24 and k = 0.94. H/c = 4%.
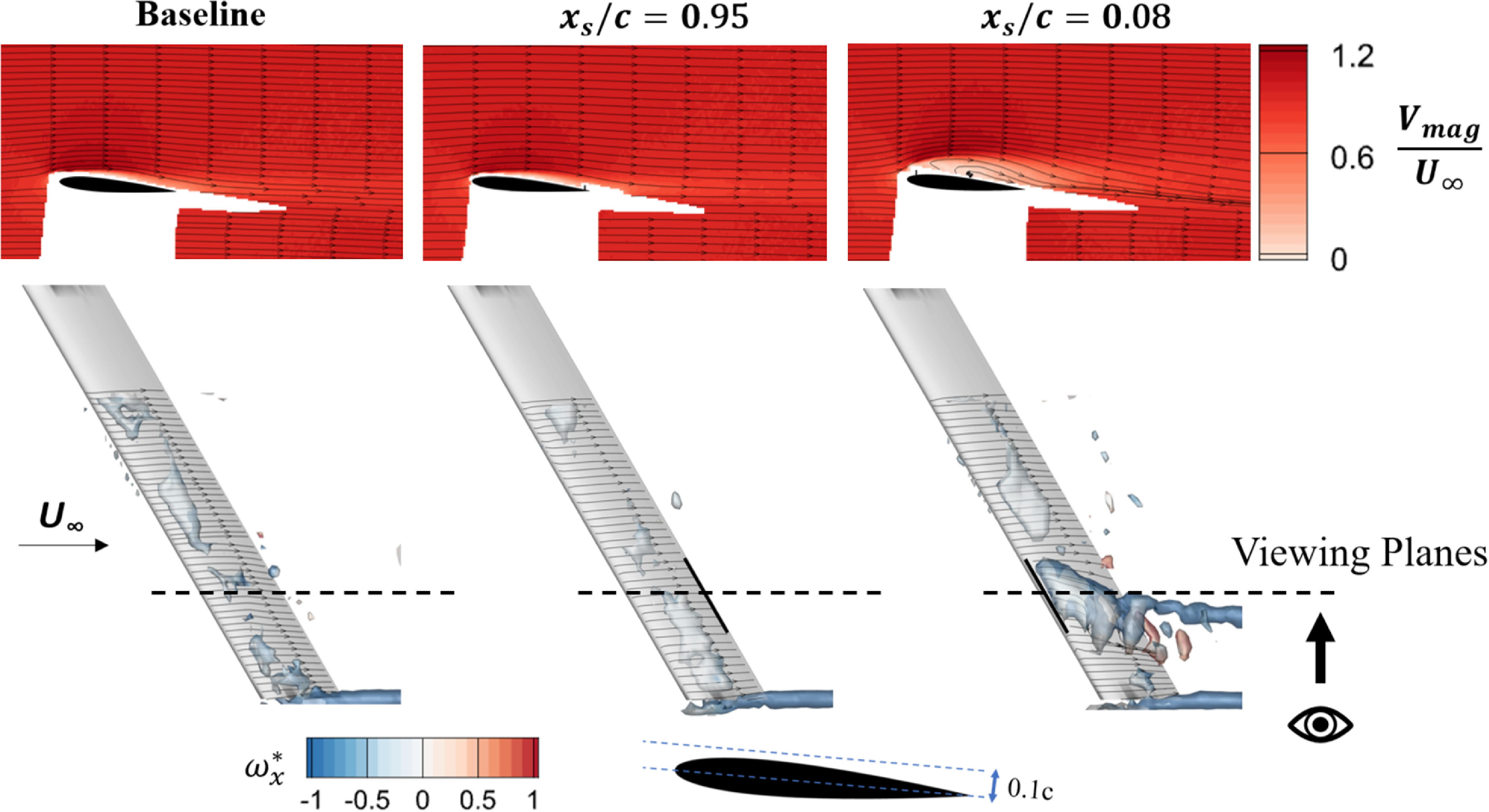
Figure 13. Time-averaged velocity magnitude contours from PIV measurements (top) and top views of vortical structures with isosurfaces of Q
*=0.25, coloured with streamwise vorticity, from volumetric measurements (bottom) on a clean wing and with the addition of leading-edge and trailing-edge spoilers for the case of α = 5°, k = 0,
$\varLambda$
= 30°, H/c = 4%.
Flow measurements using both the PIV (with better spatial resolution) in the mid-span plane of the spoiler and the three-dimensional volumetric measurements are presented in Fig. 13 for
$\varLambda$
= 30°, α = 5°, and k = 0. The magnitude of the time-averaged velocity from the PIV data in the mid-span plane of the spoiler is shown at the top, while the vortical structures coloured by streamwise vorticity together with near-surface streamlines are plotted at the bottom. For the clean wing case, both flow measurement techniques indicate that the flow remains attached over the wing upper surface. The flow patterns of the clean wing case are generally similar to those of the TE spoiler case. Nevertheless, a slight increase in the upward deflection of the streamlines in the wake is consistent with the small lift reduction (see Fig. 12). The inclined wake produced by the trailing-edge spoiler still generates some degree of circulation control. In contrast, the LE spoiler positioned at x
s
/c = 0.08 induces flow separation behind it, which also reduces the loads slightly (see Fig. 12). Spanwise flow induced by the wing sweep significantly modifies the wake of the spoiler. Momentum is carried from the inboard of the spoiler into the wake, which effectively decreases the extent of the separation region. A new streamwise vortex is observed. Figure 14 examines the streamwise vortex shed from the spoiler. The top views of vortical structures are shown on the left and the streamwise vorticity in the cross-sectional plane is plotted on the right. The streamwise vortex has the same direction of rotation as the tip vortex. It appears that this vortex was shed from the spoiler’s inboard tip, and it propagates outboard due to the spanwise flow and tends to reattach the flow behind the spoiler. During this process, a secondary vortex of opposite sign forms as the streamwise vortex interacts with the wing boundary layer. The reattachment may reduce the effective area of the spoiler, thereby diminishing its load alleviation performance.
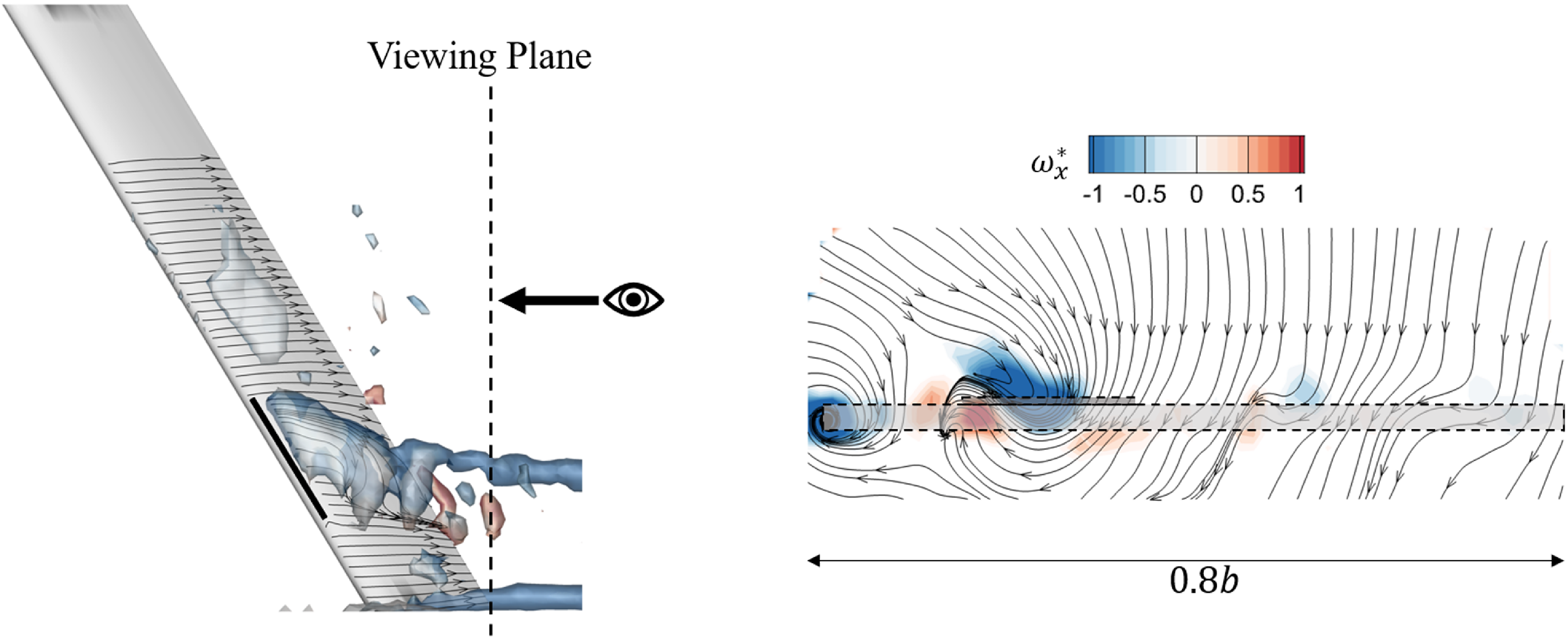
Figure 14. Top views of vortical structures with isosurfaces of Q
* = 0.25 on a wing with leading-edge spoiler (left) and streamwise vorticity in cross-sectional slice (right), for the case of α = 5°, k = 0,
$\varLambda$
= 30°, H/c = 4%.
Moving to k = 0.24, the phase-averaged vortical structures over the
$\varLambda$
= 30° wing at α = 5° are presented in Fig. 15. The isosurfaces of the vortical structures, coloured with streamwise vorticity, on both the baseline wing and the wing with LE and TE spoilers are shown. For the clean wing, as the effective angle-of-attack increases, weak vortical structures begin to form at the leading-edge (t/T = 0.25). With the trailing-edge spoiler added, these vortical structures are stronger and visible at t/T = 0.25 and 0.5. This may be caused by the adverse pressure gradient imposed by the trailing-edge spoiler. As the spoiler is immersed in the separated flow, the effectiveness is decreased (see Fig. 12). The LE spoiler induces flow separation from the beginning of the plunging motion (t/T = 0) and can be observed throughout the entire motion. Similar to the stationary wing case (k = 0) shown in Fig. 14, the leading-edge spoiler generates a streamwise vortex from its inboard tip, causing the flow to reattach behind the spoiler and thereby reducing its effectiveness in load alleviation.
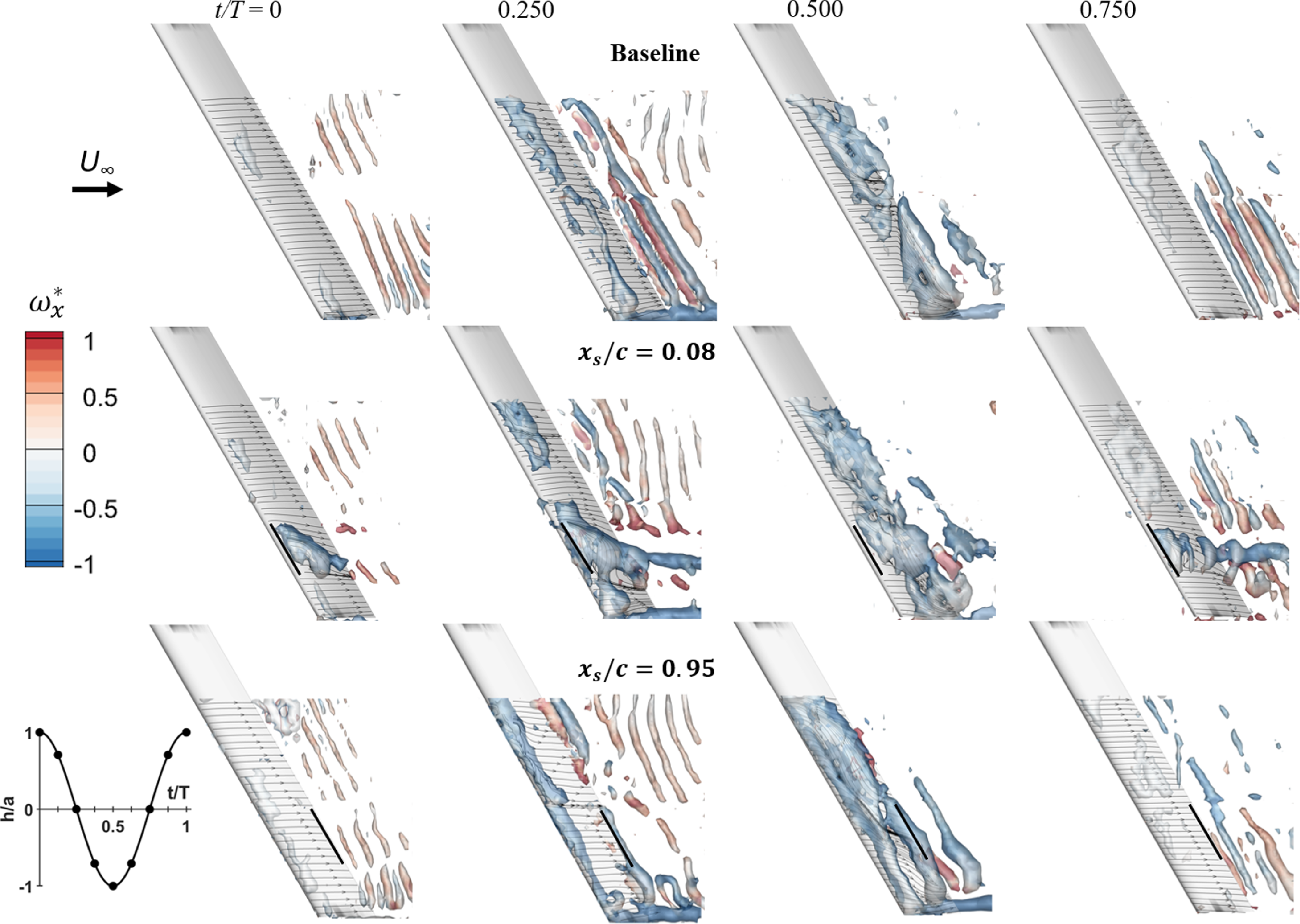
Figure 15. Top views of vortical structures with isosurfaces of Q
*=0.25, coloured with streamwise vorticity, on the clean wing and wings with trailing-edge and leading-edge spoilers for the case of α = 5°, k = 0.24,
$\varLambda$
= 30°, H/c = 4%.
At the higher reduced frequency of k = 0.94, both spoilers become ineffective for
$\varLambda$
= 30° (see force/moment data in Fig. 12). The leading-edge vortices for all cases are much stronger and dominate the flow as shown in Fig. 16. The trailing-edge spoiler has little effect on the leading-edge vortices. Even for the leading-edge spoiler case, there is only a small local effect on the LEV and the leg of the vortex on the wing surface. Overall, because of the strong LEVs, mini-spoilers become ineffective, regardless of the location of the spoilers and the wing sweep angle.
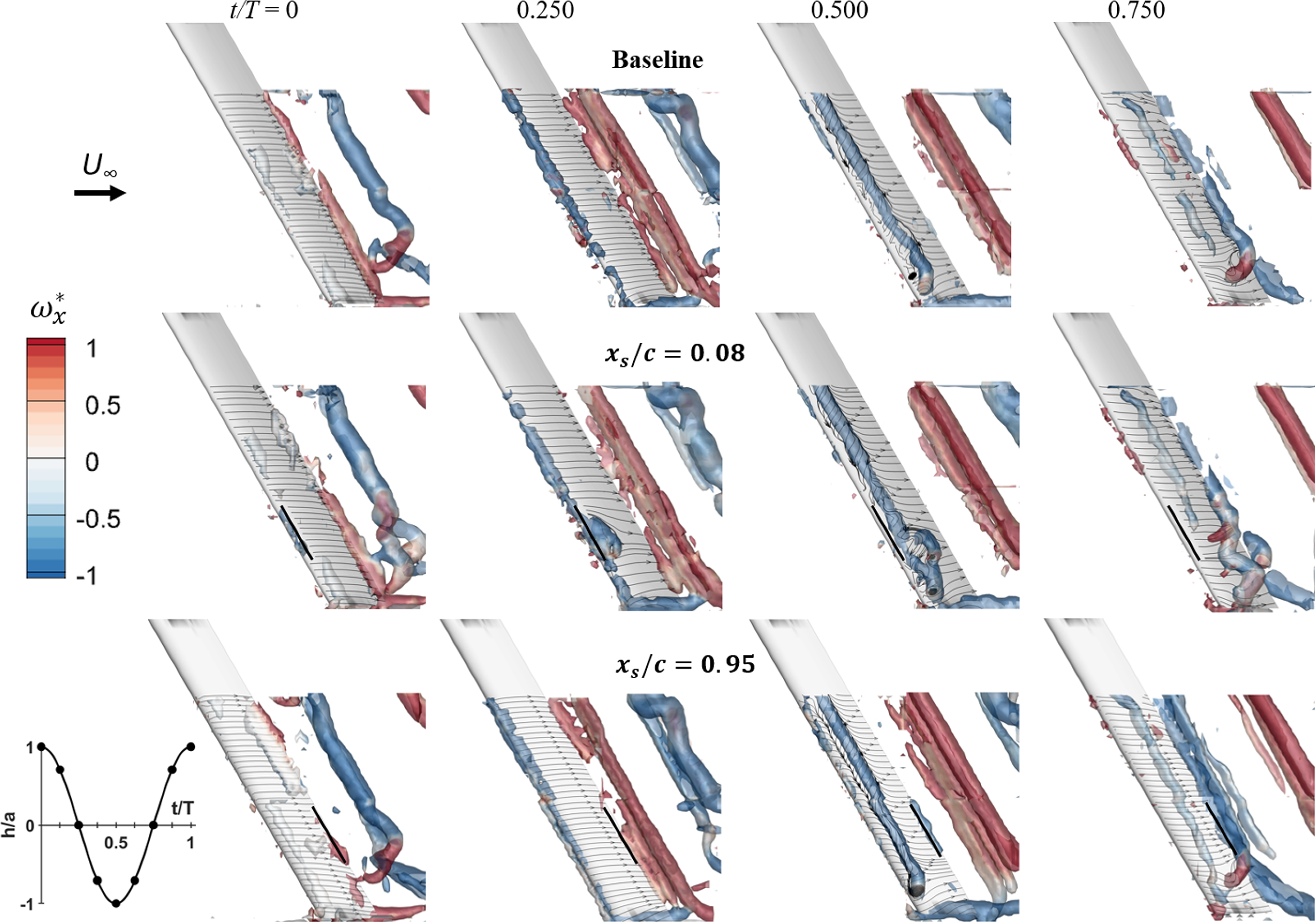
Figure 16. Top views of vortical structures with isosurfaces of Q
*=0.25, coloured with streamwise vorticity, on the clean wing and wings with trailing-edge and leading-edge spoilers for the case of α = 5°, k = 0.94,
$\varLambda$
= 30°, H/c = 4%.
As shown previously in Fig. 12, the highly swept wing (
$\varLambda$
= 40°) is incapable of producing load alleviation with the spoiler parallel to the leading edge. At this high sweep angle, spanwise flow is expected to be stronger. For the stationary wings (k = 0) and at α = 5°, Fig. 17 compares the time-averaged velocity magnitude contours superimposed with the near-surface streamlines from the PIV measurements for
$\varLambda$
= 0° in part (a) and for
$\varLambda$
= 40° in part (b). For the
$\varLambda$
= 0° wing, the spoiler parallel to the leading edge induces significant flow separation behind it, thus resulting in the significant load reductions as shown in Fig. 12 (
$\Delta {C_{L,max}}$
/
${C_{L,max}}$
=
$ - 19{\rm{\% }}$
). In contrast, for the
$\varLambda$
= 40° wing, the spoiler parallel to the leading edge does not generate similar recirculation regions; instead, the spanwise flow increases the magnitude of the velocity behind the spoiler. This results in less effectiveness of lift reduction (
$\Delta {C_{L,max}}$
/
${C_{L,max}}$
=
$ - 3{\rm{\% }}$
). In order to prevent or decrease the spanwise flow, we experimented with the idea of a ‘spoiler normal to the freestream’ as shown in Fig. 17(c). There is still some spanwise flow, but with slight improvement in the performance (
$\Delta {C_{L,max}}$
/
${C_{L,max}}$
=
$ - 7{\rm{\% }}$
).
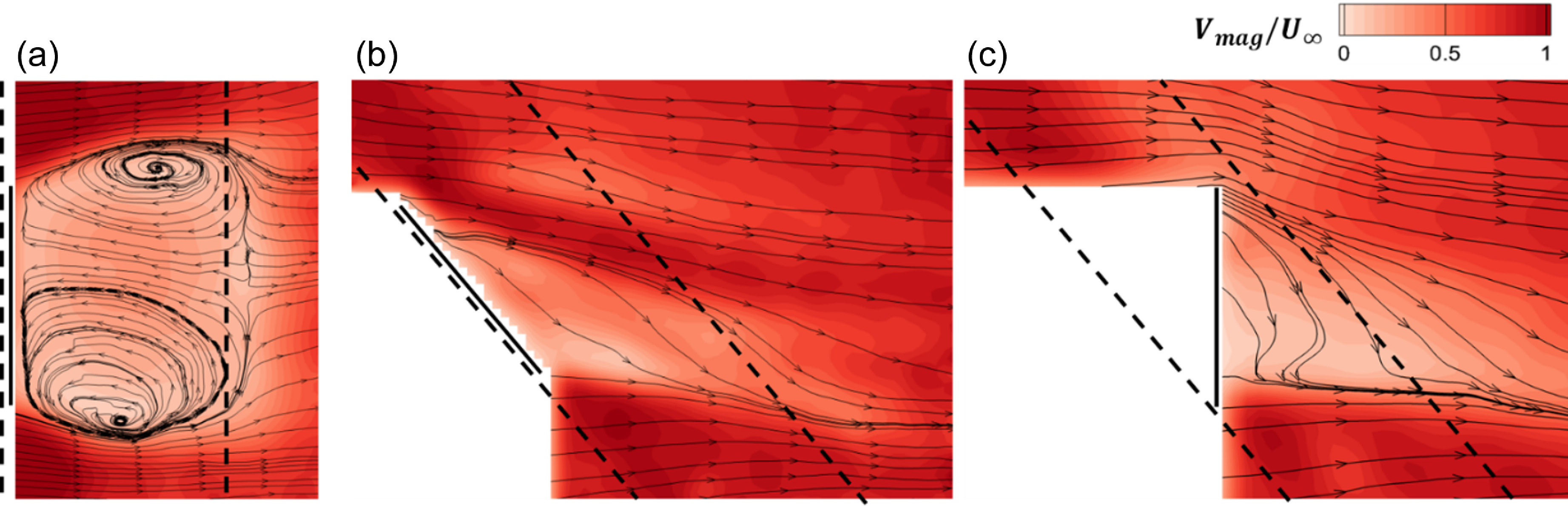
Figure 17. Time-averaged near-surface velocity magnitude contours from PIV measurements for: (a)
$\varLambda$
= 0° wing with leading-edge spoiler; (b)
$\varLambda$
= 40° wing with spoiler parallel to leading edge of wing; (c)
$\varLambda$
= 40° wing with spoiler perpendicular to the freestream; α = 5°, k =0, H/c = 4%.
Figure 18 shows the same wing and spoiler configurations in Fig. 17, but at a higher angle-of-attack of α = 10°. For the unswept wing, there is some asymmetry in the separation region (this might be due to the increased angle-of-attack and the strength of the wing-tip vortex) and slightly larger separation area. This results in a slight increase in the magnitude of the percent lift reduction (
$\Delta {C_{L,max}}$
/
${C_{L,max}}$
=
$ - 23{\rm{\% }}$
). However, for the
$\varLambda$
= 40° wing, an even stronger spanwise flow is observed for the spoiler parallel to the leading edge (Fig. 18(b)), resulting in
$\Delta {C_{L,max}}$
/
${C_{L,max}}$
=
$ - 2{\rm{\% }}$
. Similarly, Fig. 18(c) suggests that the spoiler is ineffective in mitigating the influence of the spanwise flow. The spoiler in this case might be contributing to the increased flow separation on the wing surface inboard of the spoiler. The resulting lift reduction is
$\Delta {C_{L,max}}$
/
${C_{L,max}}$
=
$ - 1{\rm{\% }}$
only.
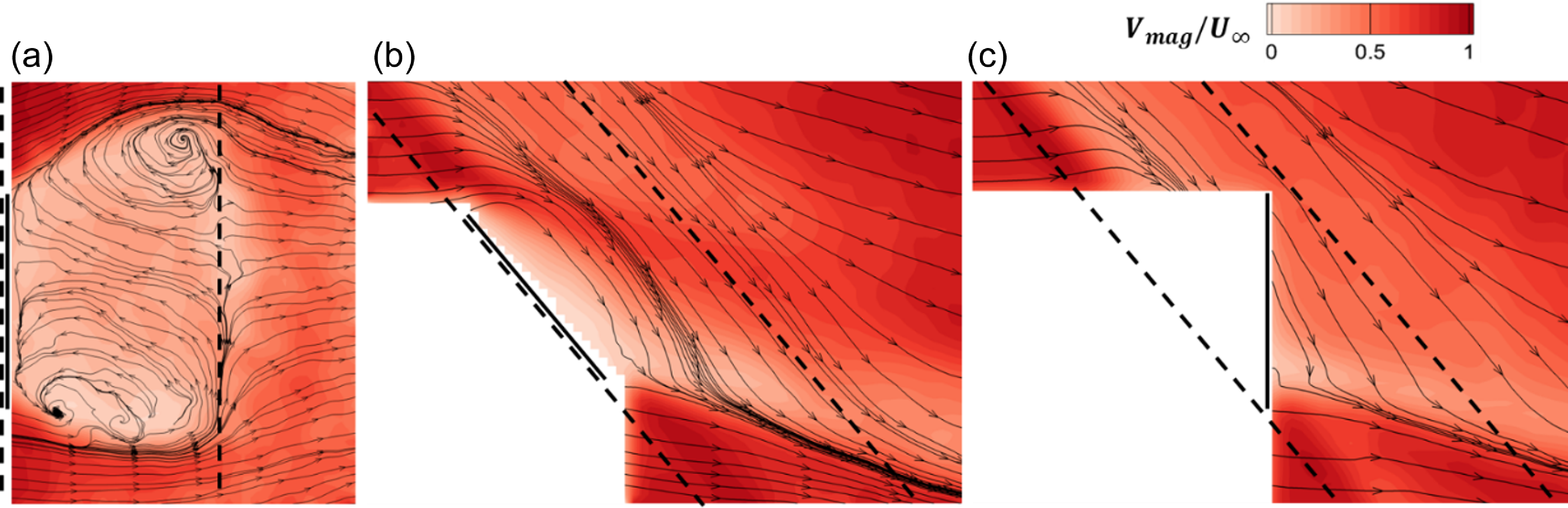
Figure 18. Time-averaged near-surface velocity magnitude contours from PIV measurements for: (a)
$\varLambda$
= 0° wing with leading-edge spoiler; (b)
$\varLambda$
= 40° wing with spoiler parallel to leading edge; (c)
$\varLambda$
= 40° wing with spoiler perpendicular to the freestream; α = 10°, k =0, H/c = 4%.
4.0 Conclusions
The frequency responses of the separation control and circulation control on plunging wings were investigated. In addition, they were compared on the unswept (
$\varLambda$
= 0°), and swept wings (
$\varLambda$
= 30° and
$\varLambda$
= 40°). The effectiveness of mini-spoilers for load alleviation was studied by means of lift and bending moment measurements, volumetric velocimetry measurements and particle image velocimetry measurements in a water tunnel. This work focused on part-span spoilers on finite plunging wings. The majority of the study concentrated on the pre-stall angle-of-attack of α = 5°, because it represents a more typical flight regime.
For the unswept wing (
$\varLambda$
= 0°), both the percent lift and moment reductions show that the best reductions are for the stationary wing (k = 0) for the pre-stall angle-of-attack of α = 5°. Both the leading-edge spoiler and trailing-edge spoiler exhibit similar performance, with the leading-edge spoiler being slightly better. The effectiveness of the spoilers significantly diminishes by increasing reduced frequency of the wing plunging motion, with not much loads attenuations beyond the cut-off frequency. The leading-edge spoiler outperforms the trailing-edge spoiler at the stall and post-stall angles of attack.
At k = 0 and α = 5°, the separated shear layer from the spoiler near the leading edge does not exhibit any roll-up of the vorticity, and the effectiveness becomes maximum. With increasing reduced frequency, the leading-edge spoiler excites the shear-layer roll-up, promoting flow reattachment and reducing the effectiveness of the loads attenuation. For the trailing-edge spoiler, at k = 0, the circulation control is achieved by the deflection of the flow behind the spoiler. The effectiveness of the lift attenuation also decreases with increasing reduced frequency, but for a different reason. A strong LEV forms primarily due to the increase of the effective angle-of-attack, and the trailing-edge spoiler becomes engulfed in the separated flow and cannot deflect the flow behind the spoiler. The cut-off reduced frequency is similar for both the leading-edge and trailing-edge spoilers, implying that the physical mechanism is related to the flow separation near the leading-edge of the wing. The effect of spoiler height has also been examined, revealing that the taller spoiler (H/c = 0.08) provides better load alleviation than the shorter one (H/c = 0.04) for the leading-edge spoiler. However, the effect of the spoiler height is smaller for the trailing-edge spoiler.
At the sweep angle of
$\varLambda$
= 30° and the pre-stall angle-of-attack of α = 5°, the spoilers’ effectiveness in load alleviation decreases significantly in comparison to the unswept wing, with both LE and TE placements showing comparable performance. At k = 0, the leading-edge spoiler sheds a vortex from its inboard tip that moves outboard, due to the spanwise flow. This causes partial reattachment of the flow and reduction of the separation area behind the spoiler. Meanwhile, the trailing-edge spoiler is not able to deflect the flow to the same degree as for the unswept wing. This might be due to the inclined wake flow behind the spoiler. With increasing reduced frequency, the stronger streamwise vortex shed from the spoiler becomes the limiting factor for loads attenuation. Around the same reduced frequency, the trailing-edge spoiler becomes immersed in the separated flow produced by the flow separation at the leading edge, resulting in much lower effectiveness. At even higher frequencies, strong leading-edge vortices make both spoilers ineffective. For the even higher sweep angle (
$\varLambda$
= 40°), load alleviation is not achievable for the current span of the spoiler, regardless of whether the spoiler was placed perpendicularly to the freestream or parallel to the leading-edge.
Acknowledgments
The authors express their gratitude for the support from the Engineering and Physical Sciences Research Council (EPSRC) of the United Kingdom under Grant No. EP/S028994/1, titled “Three-dimensionality and Instabilities of Leading-Edge Vortices” and the Airbus PhD Studentship. Special thanks go to Dr. Andrea Castrichini of Airbus for his insightful discussions.