The production of pottery in the broad sense is one of the oldest activities in human history. With the discovery, 30,000 years ago, of the special properties that clay acquires upon firing, the first synthetic material was created: ceramic (Vandiver et al., Reference Vandiver, Soffer, Klima and Svoboda1989). To date, in Serbia, only the Zlakusa area continues to produce pottery in the old, archaic manner (Djordjević-Bogdanović, Reference Djordjević-Bogdanović1996, Reference Djordjević-Bogdanović2016; Djordjević, Reference Djordjević2005, Reference Djordjević, Lugli, Stoppiello and Biagetti2013; Milošević et al., Reference Milošević, Djordjević and Logar2019b). The village of Zlakusa lacks the proper raw materials to produce high-quality ceramics and pottery. The raw material instead is delivered from a distance – from the villages of Vranjani and Rupeljevo (Milošević et al., Reference Milošević, Dabić, Kovač, Kaluđerović and Logar2019a). It is this careful selection of raw materials that results in the high quality of the pots, which contributed to the survival of this form of pottery despite periods in which demand for it had almost completely ceased. It is this ability to find the best raw clay and the best type of temper (calcite) and mix them in the optimum ratio that has kept Zlakusa pottery manufacturers active to this day, and it remains the only such pottery trade in the area once known for its thriving potters. Characterization of the pottery, temper, filler, clay body and its provenance with relation to a specific production centre can be performed more accurately through investigation of clay materials used in the production of ceramics (Montana et al., Reference Montana, Ontiveros, Polito and Azzaro2011). Raw materials such as clays have various industrial and technological applications (Christidis, Reference Christidis and Christidis2011), but their final application is influenced by their properties. The main goal of this study is to present a mineralogical characterization of the clay body and the temper used in the manufacture of traditional pottery, which will consequently provide a useful means for identifying the provenance of archaeological ceramics.
Locality and material
The village of Zlakusa (43°47′N, 19°57′E, elevation 400–931 m) is located on the slopes of Drežnik Hill, along the right-hand bank of Djetinja River, western Serbia. It belongs to the district of Zlatibor in the territory of the municipality Užice, and it is ~14 km away from the city of Užice (Serbia).
The raw clay deposit is located in the village of Vranjani (Dobrodo deposit). It consists mostly of Miocene sediments, mainly sand, clay, marl and dolomite, which were deposited in freshwater basins (Fig. 1, top right) (Mojsilović et al., Reference Mojsilović, Baklajić, Đoković and Avramović1971). The clay in the Dobrodo deposit does not have a uniform appearance and chemical composition. It is layered with clays of various colours and shades, from yellow to dark grey, due to differences in mineralogy (Milošević et al., Reference Milošević, Dabić, Kovač, Kaluđerović and Logar2019a).

Fig. 1. Geographical (left) and geological (right) locations of the investigated samples. Adapted from Milošević et al. (Reference Milošević, Dabić, Kovač, Kaluđerović and Logar2019a).
To obtain high-quality clay for pottery making, it is necessary to dig at a depth of >1.5–3.0 m and up to a depth of 8 m. Digging deeper than 8 m has been noted by the contractor to lead to a high probability of landslides. Every year, a new pit is dug out, while the previous one is buried and is not used again. Calcite is supplied to Zlakusa from the village of Rupeljevo (Fig. 1, bottom right) on Vrstine Hill. The extraction of calcite is achieved when the overburden of soil is removed. Calcite, once it is destroyed by blasting, is then easily removed from the bed due to its physical properties.
Preparation of the clay body
According to Djordjević (Reference Djordjević, Lugli, Stoppiello and Biagetti2013), after mixing of all of the types of raw clays present in the quarry (Milošević et al., Reference Milošević, Dabić, Kovač, Kaluđerović and Logar2019a) and removal of aplastic material (pebbles or plants), the clay mix is first immersed in a barrel of water and left to stand in it for the next 24 h. As the excess water is drained, the clay body is extracted onto a table, which will allow for its further preparation and for the addition of calcite. The calcite pieces are first hammered to obtain smaller pieces and then ground in a fine grinding hammer mill, and for the most part, the same particle size is used for all types of vessels. The fine grinding hammer mills are not standardized and are products of the potters themselves. After that, the calcite is sieved and added to the clay body in a clay:calcite ratio of 1:1 or 0.4:0.6, depending on the type or the size of the vessel to be made. For example, for larger pots, such as celebration or wedding pots, the recipe involves 60% calcite and 40% clay (Djordjević, Reference Djordjević, Lugli, Stoppiello and Biagetti2013). The next step is to mix the clay and calcite powder into a homogeneous mass that is ready for processing. From there, a piece of clay body is taken, kneaded by hand and then used to construct a vessel on a hand-driven winch.
An investigation was carried out on three samples: raw clay after proper mixing (ClMx); crushed calcite (CC) prepared for the application; and the final clay body (ClBd) after mixing the ClMx with the CC in the desired ratio.
Methods
The X-ray powder diffraction (XRPD) data were collected on a Rigaku SmartLab X-ray powder diffractometer using Bragg–Brentano geometry and Cu-Kα radiation in the scan range of 3–70°2θ with a step size of 0.01° and a scanning speed of 2° min–1. The diffractometer was operated at 40 kV and 30 mA. The XRPD experiments were carried out on powdered bulk samples and on oriented mounts in three preparations, namely: natural air dried (AD), treated with ethylene glycol (EG) and heated at 550°C for 1 h (H). The mineral phases were identified using the Rigaku PDXL software and the PDF-2 database (International Centre for Diffraction Data). The chemical composition was determined by X-ray fluorescence (XRF) spectroscopy using a PANalytical MiniPal 4 XRF spectrometer equipped with a high-resolution silicon drift detector (SDD). Differential thermal analysis (DTA) was performed on a modernized ADAMEL furnace equipped with a Pt-PtRh thermocouple and BK PRECISION XLN15010 DC power supply as the heating rate controller in an air atmosphere. The heating rate was 10°C min–1 in a temperature range of 20–1100°C. The scanning electron microscopy (SEM) study was performed with a JEOL JSM-6610LV SEM coupled with an Oxford Energy Dispersive X-Max 20 mm2 SDD energy dispersive X-ray spectrometer (EDXS) to study the particle morphology and to assess the grain size. The grain-size distribution was determined using the pipette method according to the DIN ISO 11277 (2002). The Atterberg limits (plasticity index (PI), plastic limit (PL) and liquid limit (LL)) were determined according to the Casagrande method (LCPC, 1987) and calculated according to Atterberg (Reference Atterberg1911).
Results and discussion
Chemical composition
The chemical composition of the ClMx indicates that the raw clay material used for the ceramic production consists mainly of Al2O3 (~16 wt.%) and SiO2 (~57 wt.%) and minor CaO, K2O and TiO2 (Table 1). The high SiO2 and low Al2O3 contents might be associated with increased amounts of the clay minerals, quartz and feldspars (Kramar et al., Reference Kramar, Lux, Mladenović, Pristacz, Mirtič, Sagadin and Rogan-Šmuc2012; Boussen et al., Reference Boussen, Sghaier, Chaabani, Jamoussi and Bennour2016; Milošević et al., Reference Milošević, Logar, Dojčinović, Rosić and Erić2016; Daghmehchi et al., Reference Daghmehchi, Rathossi, Omrani, Emami and Rahbar2018). The molar ratio of SiO2:Al2O3 (3.41%) reflects the large contribution of quartz in the sample (Abdelmalek et al., Reference Abdelmalek, Rekia, Youcef, Lakhdar and Nathalie2017; Milošević et al., Reference Milošević, Logar, Kaluđerović and Jelić2017, Reference Milošević, Dabić, Kovač, Kaluđerović and Logar2019a). The K2O (1.01 wt.%) is associated with the presence of minor K-feldspar or mica (illite or muscovite) (Monterio & Vieira, Reference Monterio and Vieira2004; Celik, Reference Celik2010), while the MgO (0.76 wt.%) is attributed to minor smectite or chlorite (Montana et al., Reference Montana, Ontiveros, Polito and Azzaro2011). The slightly larger amount of Fe2O3 (~5 wt.%) may be derived from the hydroxides/oxides in the raw material and may produce red-coloured ceramics (Abajo, Reference Abajo and Beralmar2000; Murray, Reference Murray2007; Daghmehchi et al., Reference Daghmehchi, Rathossi, Omrani, Emami and Rahbar2018; Milošević et al., Reference Milošević, Dabić, Kovač, Kaluđerović and Logar2019a), which is still acceptable in ceramics (Baccour et al., Reference Baccour, Medhioub, Jamoussi, Mhiri and Daoud2008) as a ‘dark-firing’ ceramic body (Dondi et al., Reference Dondi, Guarini, Ligas, Palomba and Raimondo2001; Milošević & Logar, Reference Milošević and Logar2017). The relatively large loss on ignition (LOI; 15.86%) may be related to dehydroxylation of hydrated minerals or hydroxides, oxidation of organic materials and decomposition of carbonates (Milheiro et al., Reference Milheiro, Freire, Silva and Holanda2005; Baccour et al., Reference Baccour, Medhioub, Jamoussi, Mhiri and Daoud2008; Abdelmalek et al., Reference Abdelmalek, Rekia, Youcef, Lakhdar and Nathalie2017).
Table 1. Chemical analysis of the ClMx and CC temper.

The chemical composition of the CC temper indicates that the raw material has high CaO and SiO2 contents (28.8 and 27.5 wt.%, respectively) and low Al2O3, Fe2O3 and Na2O contents (Table 1). The slightly larger amounts of Al2O3 and Na2O are due to contamination by clay minerals during milling. The large CaO content is related to the abundant carbonates, which are also responsible for the high LOI (31.88%) (Milheiro et al., Reference Milheiro, Freire, Silva and Holanda2005; Baccour et al., Reference Baccour, Medhioub, Jamoussi, Mhiri and Daoud2008; Abdelmalek et al., Reference Abdelmalek, Rekia, Youcef, Lakhdar and Nathalie2017).
Mineralogy
The mineral phases identified in the ClMx sample are kaolinite/halloysite, mica/illite, smectite, quartz, paragonite, feldspar, calcite and hematite (Fig. 2), in accordance with the mineral phases reported by Milošević et al. (Reference Milošević, Dabić, Kovač, Kaluđerović and Logar2019a). Quartz is the most abundant non-clay mineral, while calcite and feldspars are accessory minerals. Based on the abundance of the minerals present and their association, there is a wide variety of properties that promote the application of the ClMx in the manufacture of ceramic products (Christidis, Reference Christidis and Christidis2011; Abdelmalek et al., Reference Abdelmalek, Rekia, Youcef, Lakhdar and Nathalie2017). The XRPD traces of the oriented clay fractions of the investigated samples are presented in Fig. 2. The transformation of kaolinite into metakaolin is observed with the disappearance of the reflection at 12.3°2θ (7.1 Å) after heating at 500°C (Bergaya & Lagaly, Reference Bergaya, Lagaly, Bergaya, Theng and Lagaly2006; Abdelmalek et al., Reference Abdelmalek, Rekia, Youcef, Lakhdar and Nathalie2017).

Fig. 2. XRPD traces of the ClMx and ClBd samples together with oriented patterns of the clay fraction: untreated sample (AD), solvated with ethylene glycol (EG) and heated at 550°C (H).
The ClBd sample is a mixture of the ClMx and CC samples at a ~1:1 ratio, as reported by the pottery manufacturers (Table 2). The ClMx sample has a large calcite content (Fig. 2). When comparing the oriented patterns, calcite addition is evident in the ClBd sample, which has a smaller clay content than the ClMx sample. The semi-quantitative estimation of the mineral phases obtained by the whole-powder pattern fitting of the investigated samples is shown in Table 2.
Table 2. Semi-quantitative estimation of the mineral phases in the investigated samples.

The SEM images and EDX analyses of the investigated ClMx and ClBd samples are shown in Fig. 3. Kaolinite occurs as lamellar hexagonal flakes with broken edges, while montmorillonite particles mainly form larger crumbly aggregates and dense plates with undefined edges. Titanium minerals in the form of rutile needles (~20 μm) are evident in the samples, in agreement with Milošević et al. (Reference Milošević, Dabić, Kovač, Kaluđerović and Logar2019a). A smaller amount of illite occurs in the form of fibres and laths. Halloysite or disordered kaolinite is observed as rolled, platy to elongated tubular particles and is present in minor amounts compared to the kaolinite content (Frost et al., Reference Frost, Van Der Gaast, Zbik, Kloprogge and Paroz2002; Joussein et al., Reference Joussein, Petit, Churchman, Theng, Righi and Delvaux2005; Milošević & Logar, Reference Milošević and Logar2017). The ClBd sample contains abundant large calcite particles, and the greater calcium content when compared to the ClMx sample is also confirmed by EDX analysis (Fig. 3).

Fig. 3. The SEM and EDX analysis of the investigated ClMx and ClBd samples.
A rhombic shape of the calcite crystals is most common in the observed samples, validated by SEM/EDX analysis of the CC sample (Fig. 4). Calcite is mostly pure CaCO3 with a minor Fe content and slight contamination by clay particles and quartz (Fig. 4).

Fig. 4. XRPD, SEM and EDX analysis of the CC sample.
The DTA curves of the investigated samples show a couple of endothermic peaks (Fig. 5). The first significant endothermic peak at between 120°C and 220°C is associated with the loss of adsorbed and interlayer water and indicates the presence of layered silicates such as illite, kaolinite, halloysite and/or montmorillonite (Greene-Kelly, Reference Greene-Kelly and Mackenzie1957; Földvári, Reference Földvári2011; Milošević et al., Reference Milošević, Dabić, Kovač, Kaluđerović and Logar2019a). For the ClBd sample, two smaller thermal events are observed in the same region in comparison to the ClMx sample, which is characterized by a broad band. The thermal events at ~350°C and ~450°C are indicative of iron minerals (goethite and limonite) and halloysite, which are present in smaller amounts (Norton, Reference Norton1939; Grim & Rowland, Reference Grim and Rowland1944).
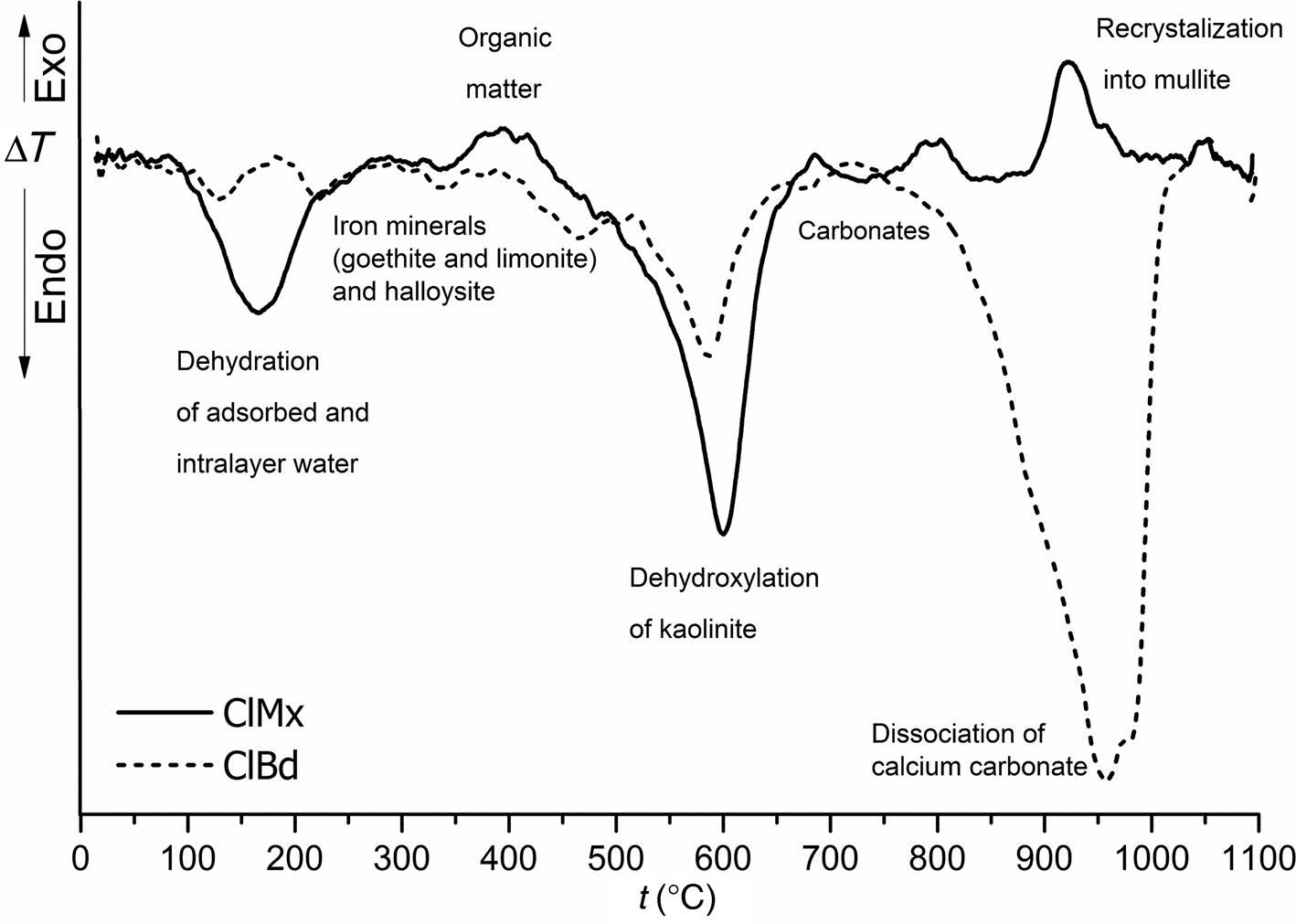
Fig. 5. DTA of the investigated ClMx and ClBd samples.
The broad endothermic event at between 550°C and 650°C represents dehydroxylation of kaolinite and halloysite and transformation to amorphous metakaolinite and metahalloysite, but it could also be indicative of illite minerals (Norton, Reference Norton1939; Speil et al., Reference Speil, Berkelhamer, Pask and Davies1945; Földvári, Reference Földvári2011; Milošević et al., Reference Milošević, Dabić, Kovač, Kaluđerović and Logar2019a). The presence of these phases was confirmed by XRPD and SEM analysis. The low-intensity endothermic peaks that are notable at between 750°C and 800°C in the ClMx sample are attributed to carbonates, and the smaller broad band at ~850°C confirms the presence of illite (Grim & Rowland, Reference Grim and Rowland1944). The formation of a new crystalline phase, primarily mullite or pseudomullite, was observed in the ClMx sample at ~950°C (Speil et al., Reference Speil, Berkelhamer, Pask and Davies1945; Földvári, Reference Földvári2011) in the form of a strong exothermic peak.
The decomposition of calcium carbonate is evident from a large band at ~950°C and a small endothermic band at ~750°C (Fig. 5). Typical and strong decomposition effects for calcite begin at ~820°C, reach a peak at 950°C, slowly drop at 990°C and afterwards end rapidly at ~1010°C, in accordance with previous work (Beck, Reference Beck1946; Smykatz-Kloss, Reference Smykatz-Kloss1982). As previously mentioned, the ClBd sample represents a mixture of the ClMx and CC samples, which is evident from the presence of thermal events that correspond to phyllosilicates (kaolinite, illite and halloysite) and iron minerals.
Particle-size analysis
The particle-size distribution of the ClBd sample is essential to defining the properties of green pastes during drying and firing (Rivi & Ries, Reference Rivi and Ries1997; Milošević et al., Reference Milošević, Dabić, Kovač, Kaluđerović and Logar2019a). The tested ClMx and ClBd samples contain 86.3 and 32.9 wt.% of clay, 10.8 and 6.4 wt.% of silt and 2.8 and 60.6 wt.% of sand fractions, respectively. The particle analysis results from our samples were plotted on a ternary diagram (McManus, Reference McManus and Tucker1988; Strazzera et al., Reference Strazzera, Dondi and Marsigli1997; Milošević et al., Reference Milošević, Dabić, Kovač, Kaluđerović and Logar2019a) (Fig. 6). The ClMx sample with the greatest percentage of clay fraction has high porosity and very low permeability, while the sample with the greatest sand fraction (ClBd) can be classified as clayey sand (Fig. 6).

Fig. 6. Ternary diagram of the investigated samples showing the particle-size distribution (after McManus, Reference McManus and Tucker1988; Strazzera et al., Reference Strazzera, Dondi and Marsigli1997).
Evaluation of plasticity and toughness
Plasticity is a property that allows ceramic masses to form a plastic body (Fenili et al., Reference Fenili, Biz, Boa Hora, Madeira, Modesto and Bernardin2004, De Oliveira Modesto & Bernardin, Reference De Oliveira Modesto and Bernardin2008). The plasticity properties of the studied samples are shown in Table 3. Samples with PI <10% are not appropriate for the manufacture of building-related items, and those with a PI >34% would be difficult to extrude (Barnes, Reference Barnes and Wesley2014). The LL values for ClMx (55.2%) and ClBd (32.4%) are within the range defined for application in the manufacture of ceramics (30–60%) (LCPC, 1987; Baccour et al., Reference Baccour, Medhioub, Jamoussi and Mhiri2009). The samples can be described as very plastic (ClMx) and moderately plastic clays (ClBd). Calcium minerals (mainly calcite), representing the main impurity, are not plastic and decrease the ceramic body plasticity (De Oliveira Modesto & Bernardin, Reference De Oliveira Modesto and Bernardin2008), which is an advantage in the ceramic industry. According to their maximum toughness (T max) values (17.5 and 30.0 kJ m–3 for ClMx and ClBd, respectively), the samples can be described as moderately tough (ClMx) and very tough (ClBd) clays (Table 2) (Moreno-Maroto & Alonso-Azcárate, Reference Moreno-Maroto and Alonso-Azcárate2018). Toughness represents the ability of a clay to be deformed, and it is highly correlated with PI and LL (Barnes, Reference Barnes and Wesley2014; Moreno-Maroto & Alonso-Azcárate, Reference Moreno-Maroto and Alonso-Azcárate2018; Milošević et al., Reference Milošević, Dabić, Kovač, Kaluđerović and Logar2019a).
Table 3. Plasticity and toughness values of the investigated samples.

aAccording to Moreno-Maroto & Alonso-Azcárate (Reference Moreno-Maroto and Alonso-Azcárate2018).
Industrial application
Extrusion involves the forced pushing of the raw material through a fixed profile to gain a desired shape. As previously stated, extrusion of clay material requires an optimal PI that is between 10% and 34% (Abajo, Reference Abajo and Beralmar2000; Vieira et al., Reference Vieira, Sánchez and Monteiro2008; Milošević & Logar, Reference Milošević and Logar2017). When plotted on a plasticity diagram, the ClMx sample is acceptable for extrusion, while the ClBd sample might be used in the manufacture of bricks and pottery, but it is not acceptable for extrusion (Fig. 7a).

Fig. 7. (a) Extrusion behaviour based on Abajo (Reference Abajo and Beralmar2000) and (b) Winkler's diagram (Winkler, Reference Winkler1954) of the samples examined.
The projection of the grain-size results onto a Winkler's diagram (Winkler, Reference Winkler1954) indicates that the two samples are not suitable raw materials for the production of bricks (Fig. 7b). The industrial properties of the ClBd sample, in terms of brick production, might be enhanced by adjusting the grain size and content of CC added according to the clay content. This remains to be investigated.
Conclusion
The main focus of this investigation was the mineralogical analysis of the clay body used in the manufacture of traditional pottery prepared with local clays and tempers in western Serbia. Three samples were studied: ClMx (raw clay produced by proper mixing of clays from Dobrodo deposit, Vranjani, Serbia), CC (crushed, ground and sieved calcite from Rupeljevo, Serbia, prepared for application) and ClBd (the final clay body after mixing the raw clay with the CC in the appropriate ratio). The ClMx sample consists mainly of Al2O3 (~16 wt.%) and SiO2 (~57 wt.%) together with minor amounts of CaO, K2O and TiO2, which indicate a large amount of clay minerals with quartz and feldspars impurities, while the CC sample has a high content of CaO (28.8 wt.%) and SiO2 (27.5 wt.%), indicating the presence of carbonates and quartz. Kaolinite/halloysite, mica/illite and smectite as the main mineral phases, together with quartz, paragonite, feldspar, calcite and hematite, have been identified in the ClMx sample. A greater calcite concentration compared with the ClMx sample is evident in the ClBd sample, together with the clay minerals, quartz and feldspar. The ClBd sample is a mixture of the ClMx and CC sample in a ratio of ~50:50, as reported by the pottery manufacturers, which was confirmed by the analytical methods used. Based on the plasticity and grain size, we have confirmed that the ClBd may be used in the manufacture of pottery, but its industrial applications are limited, although these could be enhanced by adjusting the techniques of manufacture or the paste recipes.