1 Introduction
Metallic tooling is widely used as a shape-giving support in most manufacturing techniques for high-performance composite structures, including autoclave curing (Fernlund et al. Reference Fernlund, Rahman, Courdji, Bresslauer, Poursartip, Willden and Nelson2002), filament winding (Lossie & Van Brussel Reference Lossie and Van Brussel1994), or bladder molding (Bernet et al. Reference Bernet, Michaud, Bourban and Månson2001). Despite achieving good surface quality, low micro-structural defects, and excellent structural performance, composite parts fabricated using these processes are generally limited in geometrical complexity as their manufacturability is bound to the capability of the tooling. As a consequence, composite parts often do not achieve the full lightweight potential. Traditional tooling is typically machined and assembled and, therefore, characterized by long lead times, representing a major up-front non-recurring cost, especially for low volume series. Moreover, tooling may require continual maintenance and modifications dependent on the design and the variety of produced parts (Campbell Reference Campbell2003).
The trend toward integrated, high-performance composites with complex shapes demands for manufacturing techniques with increased design freedom and flexibility. Recently, additive manufacturing (AM) has been increasingly used for the production of metallic and polymeric tools and molds for various manufacturing process chains (e.g. injection molding). AM encompasses a set of production technologies allowing complex geometries to be created from digital models. The process works, in general, by solidifying or depositing material layer by layer only where required to build a three-dimensional (3D) part (ASTM Std. F2792-12a 2012). Previous studies demonstrated the added value of unprecedented AM design solutions which improve the performance of the part in terms of weight savings (Orme et al. Reference Orme, Gschweitl, Ferrari, Madera and Mouriaux2017), heat transfer (Dede, Joshi & Zhou Reference Dede, Joshi and Zhou2015), or fluid flow (Schmelzle et al. Reference Schmelzle, Kline, Dickman, Reutzel, Jones and Simpson2015), to name a few. On the processing side, AM has a clear potential in the cost-effective production of functional and complex-shaped tools. Among others, binder jetting has been identified as a promising technique for rapid sand-casting applications. Critical parameters such as gas permeability, strength, and heat absorption are defined during the design process and directly manufactured, resulting in a functional, light, and low-cost mold (Upadhyay, Sivarupan & El Mansori Reference Upadhyay, Sivarupan and El Mansori2017). AM functional tools can also complement established manufacturing process chains to achieve parts with very specific requirements. For example, the replication quality of features on the micro-scale is limited using traditional injection molding processes. Zhang et al. have proposed a soft tool with micro-features made by vat photo-polymerization, a high-resolution 3D-printing technique. The soft tool is inserted during the injection molding process to replicate the micro-features onto the molded part (Zhang et al. Reference Zhang, Pedersen, Gøtje, Mischkot and Tosello2017).
AM has also been adopted in the production of tools for the prototyping and fabrication of composite parts (Black Reference Black2015; Türk et al. Reference Türk, Brenni, Zogg and Meboldt2017). A major consideration in the layup processing of thermoset composites is the curing step, where elevated temperatures and pressures are applied over time. Therefore, major research activities focus on the development of thermally stable thermoplastic materials and their characterization for the processing with composites (Li et al. Reference Li, Taylor, Bheemreddy, Iyibilgin, Leu and Chandrashekhara2015; Lušić, Schneider & Hornfeck Reference Lušić, Schneider and Hornfeck2016; Duty et al. Reference Duty, Kunc, Compton, Post, Erdman, Smith, Lind, Lloyd and Love2017). Researchers at Oak Ridge National Laboratory have proposed to reinforce thermoplastic beads with carbon-fiber loadings to improve the thermo-mechanical properties for 3D printing of in-autoclave tooling (Hassen et al. Reference Hassen, Lindahl, Chen, Post, Love and Kunc2016; Stratasys Ltd. 2017a ). Stratasys Ltd. has presented an updated design guideline for composite tooling using fused deposition modeling and is commercializing a thermoplastic blend (St-130) material for soluble tooling which is chemically dissolved in an alkaline solution (Stratasys Ltd. 2017b ). Ma et al. (Reference Ma, Gibson, Balaji and Hu2007) reported that filling thermoset epoxy composites with alumina powder increases the thermo-mechanical properties and may be suitable for rapid tooling applications.
In previous research, we have proposed two manufacturing techniques for the autoclave processing of hybrid lightweight structures. Here, we define hybrid structures as multi-material structures on the macroscopic level which are combined from different materials using a specific process. In the first approach, ST-130 material was used to produce soluble in-autoclave tooling for a novel lower limb prosthesis (Türk et al. Reference Türk, Einarsson, Lecomte and Meboldt2018). Although this approach yielded a mechanically viable and lightweight product, the approach presented shortcomings in terms of ST-130 material cost, availability, thermo-mechanical stability, and excessive material usage. In the second approach, a water-soluble sand core was produced with binder jetting, over-laminated with carbon-fiber reinforced polymers (CFRP), and cured in the autoclave. The approach was applied to the lower leg structure of the hydraulic quadruped (HyQ) robot developed at the Italian Institute of Technology (Semini et al. Reference Semini, Tsagarakis, Guglielmino, Focchi, Cannella and Caldwell2011). The resulting structure consisted of load introduction elements made with selective laser melting (SLM) which were co-cured to pre-impregnated (prepreg) CFRP. Weight savings greater than 50% highlight the potential of this approach for hollow and complex-shaped hybrid lightweight structures (Türk, Triebe & Meboldt Reference Türk, Triebe and Meboldt2016). However, the sand core approach presented limitations with regard to material brittleness, insufficient sealing quality, and most importantly the coarse printing resolution which limits the possibility for the integration of design features. As a result, the approach is not suitable for highly intricate structures with high geometrical complexity.
This paper presents a novel manufacturing technique for complex-shaped, hybrid composite structures eliminating the shortcomings of previous approaches. It allows the manufacturing of hollow composite and hybrid composite structures using an autoclave prepreg curing process, while keeping the tooling effort (lead time and costs) low and allowing for design variants through AM design adoptions. In this technique, a polymer shape-giving shell is produced with AM and filled with a temperature-resistant filler material prior to the lamination of the reinforcements. In addition, metal AM is used to produce structural lightweight components which are integrated during the layup of the reinforcements. After curing, the filler material is removed and the polymeric shell is peeled out, resulting in a highly integrated and complex-shaped composite part. The approach is applied to the lower leg structure of the HyQ robot, which is fabricated, mechanically verified, and successfully operated on the robot.
This paper is organized as follows. Section 2 outlines the generalized manufacturing technique. Section 3 describes the design and manufacturing of the robot leg structure using the novel manufacturing technique. Section 4 presents the results. Section 5 discusses the approach in a wider context and Section 6 concludes the paper.
2 Manufacturing technique
This section presents a manufacturing technique for complex-shaped, hybrid composites. Any composite tooling requires to provide the shape of part to be built, the structural support to withstand curing conditions, and the necessary functionality to position and fix load introduction elements. In most traditional and recent AM tooling, these three functions are combined in one singular part yielding high cost, long lead times, and/or high material usage (Morena Reference Morena2011). The key feature of the proposed technique originates from function-based methodologies developed by Kirschman & Fadel (Reference Kirschman and Fadel1998) which, in this context, is expressed as a separation of the three aforementioned functions as follows: An additive manufactured shell provides the layup surface for the part shape and integrated design features supporting the manufacturing or the operation of the part. A filler material acts as a temporary structural curing support during pressure and temperature loading. Both are removed after curing, resulting in a complex part. Hence, a function-driven tooling approach is chosen on multiple levels. The first level is the separation of functions as mentioned previously, which is a key novelty in the context of tooling. Second, leveraging the design freedom of AM allows the integration of additional functional features within the tooling shell. The manufacturing technique is depicted in Figure 1 and the major steps are described in the following subsections.
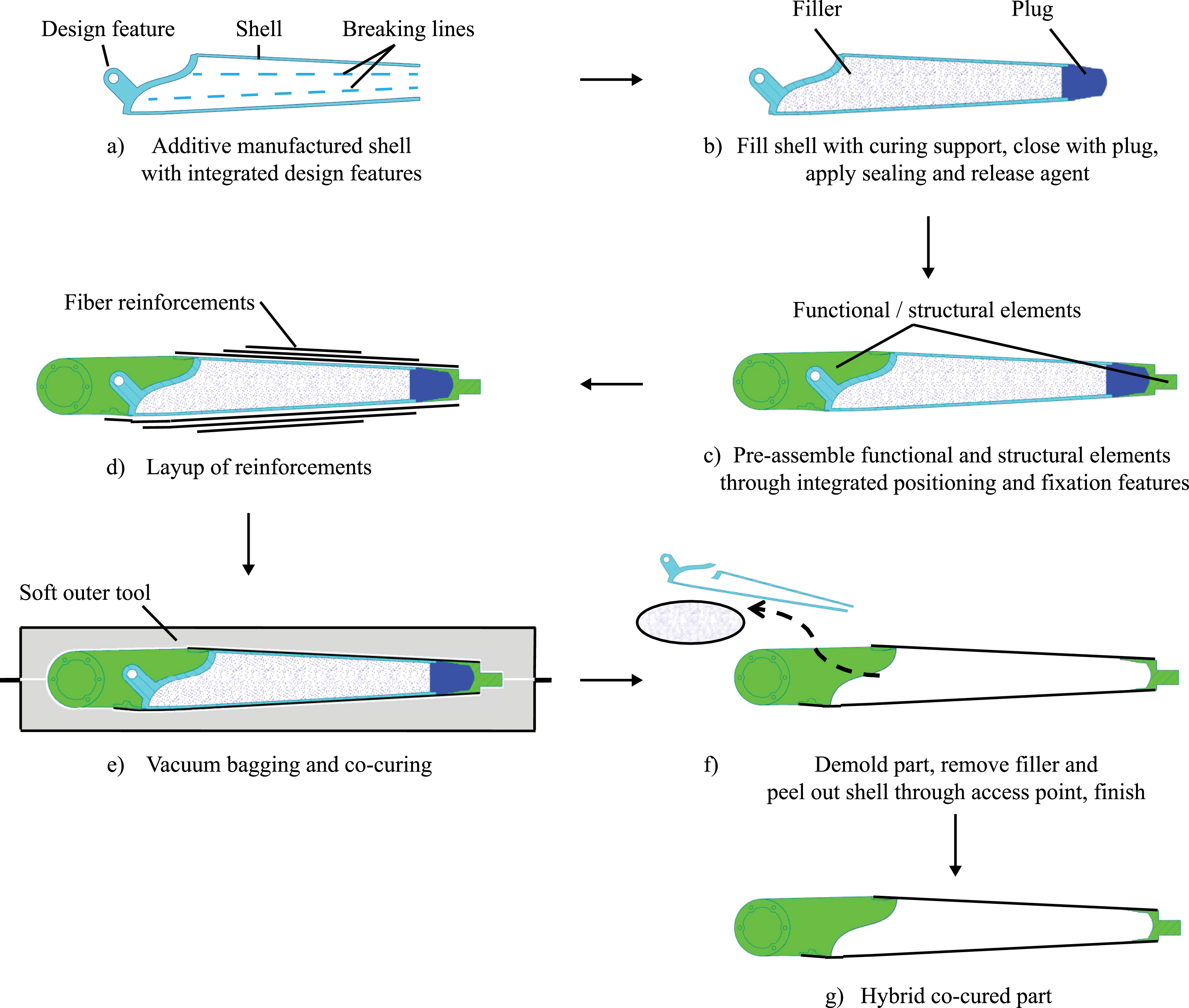
Figure 1. Manufacturing technique for complex-shaped hybrid composites using a functional 3D-printed shell (a) which is filled with a structural curing support (b) and pre-assembled with functional elements (c). Reinforcement fibers are laid on the assembly (d) which bagged and cured (e). After curing, the part is demolded, the filler is removed, and the shell is peeled out (f), resulting in a hybrid composite part (g).
2.1 Shell tooling
A thin 3D-printed polymeric shell provides the complex layup surface and thus the inner contour of the hollow composite part to be built (Figure 1a). In addition, defined design features may be integrated into the shell to add specific functions to it. Here, design features are defined as data which is related to the design object and may refer to shape, material, tolerance, or other functional aspects of the part (Ovtcharova, Pahl & Rix Reference Ovtcharova, Pahl and Rix1992). They may support the manufacturing or the operation of the part, and examples include positioning and fixation interfaces for the assembly of additional elements. The shell thickness should be selected such that the shell can easily be removed in the subsequent process steps while providing sufficient stability during the filling and the curing step. Bulging should be avoided during filling and curing pressure should not lead to shell collapse. After curing, the shell is removed along integrated breaking lines which correspond to local thickness reductions in the shell.
2.2 Fill shell and enclosure
The shell is filled with a filler material and closed with one or multiple 3D-printed plugs (Figure 1b). The main function of the filler material is to provide a temporary structural support during curing of the part in a fiber-reinforced polymer (FRP) manufacturing process, where elevated temperature and pressure are applied over time. The following requirements for the filler material are proposed. First, the filler may be a granular material with good flowability when poured into complex volumes with undercuts. The grain size and the grain size distribution may be considered to successfully fill hollow spaces with detailed geometric features. In addition, the filler material should withstand elevated curing loadings. Therefore, it ideally is temperature-resistant, exhibits a coefficient of thermal expansion close to the one of the part, and has adequate stiffness in compression. Moreover, the material should be widely available and cost-efficient. The plug is a critical interface element to enclose the filler in the hollow body shell. It may be produced with the same manufacturing technique as the shell to ensure compatibility. The interface of the plug to the shell is critical and should be designed as press fit to prevent resin inflow during curing. A temperature-resistant sealant is applied to the outer volume comprising the shell and the plug to prevent resin inflow during curing. Additional surface operations (e.g. sanding) may be conducted to improve the surface quality prior to sealant application. The sealant also acts as a basis for the release agent which allows to remove the tool (surface) from the cured part. In this research, we definte the inner tooling as the assembly of the elements that fulfill the tooling function, which in this research consists of the assembled, enclosed and sealed shell with the filler material inside of it.
2.3 Pre-assembly
One advantage of the technique is the possibility to pre-assemble complex functional and structural elements with the tooling prior to the layup of the FRP and thus prepare the hybridization of the structure (Figure 1c). Pre-assembly occurs through design features which are integrated into the shell or the plug and into the counter-parts. Here, we distinguish structural and functional elements. Structural elements are relevant to the load-bearing capability of the hybrid part and include inserts, load introduction interfaces, and fixation elements. Functional elements provide specific additional functionalities for either the operation of the part or its manufacturing and are not relevant to its primary load-carrying capability. Functional elements relevant to the part operation may consist of housing, fixations, pockets, cable ducts, and venting hoses, to name a few. Manufacturing elements support the processing which may be particularly challenging for complex parts. Among others, they include layup and handling aids, positioning and fixation elements, structural curing aids and post-processing aids (Türk et al. Reference Türk, Kussmaul, Zogg, Klahn, Leutenecker-Twelsiek and Meboldt2017).
2.4 Layup
In the layup step, the reinforcements are cut in the desired orientation to (near) net shape and sequentially draped on the pre-assembled tool according to the ply book (Figure 1d). Pre-impregnated (prepregs) FRP may be used for autoclave or out-of-autoclave processing as well as semi-finished fiber products such as those employed in resin transfer molding, filament winding, and wet layup technique. The layup surfaces should meet draping requirements in order to build a complex shape without defects with a fiber alignment that is suitable for structural loads. Also, high fiber volume content should be guaranteed over the whole part.
2.5 Bagging and curing
A vacuum bagging is conducted prior to curing and may include a bleeder, a breather, and a release film, dependent on the specific application (Figure 1e). A soft outer tool may be used to enhance the pressure distribution on the layup during curing. The outer tool may be realized from master models which may be produced with AM. The composite is cured according to the selected composite processing route. In this research, the emphasis is placed on the autoclave prepreg curing technology as it is a robust state-of-the-art technique for the production of high-performance CFRP parts. In this process, prepregs are cured in the autoclave where elevated pressure and temperature is applied to consolidate the layup. This process allows to achieve CFRP parts with high fiber volume content and low porosity (Gutowski Reference Gutowski1997). Moreover, the process allows to produce low to medium volume parts with varying geometries. It should be noted that the proposed manufacturing technique is not limited to autoclave curing and may be extended to other composites manufacturing processes. The composite may be co-cured or co-bonded to solid interface elements to form an intrinsic hybrid structure as proposed by Kießling et al. (Reference Kießling, Ihlemann, Riemer, Drossel, Dittes, Scharf, Lampke, Sharafiev, Pouya and Wagner2018) and Nieschlag et al. (Reference Nieschlag, Ruhland, Daubner, Koch and Fleischer2018). Co-curing composites are considered to be efficient as both the curing and the joining process for the composite are achieved simultaneously (Shin, Lim & Lee Reference Shin, Lim and Lee2003). Co-curing does not require an adhesive as the excess resin is extracted from the composite material during consolidation. Alternatively, co-bonding may be used to increase the load-carrying capability of the joint by inserting an adhesive layer between the metallic and the composite adherend during layup. Consider the difference in electrode potential of both adherends and take measures to avoid contact corrosion if required.
2.6 Remove tool and post-process
After completion of the curing cycle, the soft outer tool is removed (Figure 1f). The shell is mechanically opened (e.g. drilling) at one or multiple access points to remove the filler material. The shell is peeled out along integrated breaking lines which allow for sequential removal of the shell. The plug is removed mechanically. Key to successful core removal is the consideration of the access points during the design phase. Finally, finishing operations may be applied to finalize the part. The resulting structure is hybrid, co-cured, complex-shaped, and highly integrated (Figure 1g). Ideally, the structure is lightweight and exhibits the complex geometry required to optimally perform in the designated operation.
3 Experimental
3.1 Reference structure
The HyQ robot was developed at the Italian Institute of Technology (Figure 2a). HyQ is able to perform highly dynamic motions such as running, jumping, and trotting. Moreover, HyQ can navigate over rough terrain. HyQ weighs approximately 80 kg and measures 1 m in length (Semini et al. Reference Semini, Tsagarakis, Guglielmino, Focchi, Cannella and Caldwell2011). The four legs are hydraulically actuated and are composed of upper and lower leg assemblies (Figure 2b). In this research, the lower leg is redesigned using the manufacturing technique presented in Section 2, focusing on weight reduction while guaranteeing structural integrity. Reducing the weight and the mass moment of inertia in actuated masses may increase the robot’s performance and reduce the power requirements. Figure 2c shows the design space of the lower leg which consists of six main structural elements, one shaft, two bushings, two disc springs on the shaft, and 18 bolts. Without the foot, the lower leg weighs 660 g. The six structural elements are made from aircraft grade aluminum and the shaft is made from high-performance steel. The reference design has been iterated for weight reduction and robustness.

Figure 2. Hydraulic quadruped (HyQ) robot (a), leg assembly (b), and lower leg design space (c); adapted from Semini et al. (Reference Semini, Tsagarakis, Guglielmino, Focchi, Cannella and Caldwell2011) and IIT (2018).
3.2 Loading conditions
Four main maneuvers are conducted with the HyQ. In the (i) walking trot maneuver, the robot moves forward with a velocity of up to
$2~\text{m}~\text{s}^{-1}$
. In the (ii) flying trot, the robot moves diagonal leg pairs together with an average velocity of
$1.5~\text{m}~\text{s}^{-1}$
. The robot lifts off completely between the steps and lands on two diagonal legs, introducing critical peak loads into the structure. Other maneuvers are (iii) the squat jump which consists of a vertical jump of approximately 0.15 m height and (iv) the shin collision in which the robot overcomes random obstacles leading to collisions (Semini et al.
Reference Semini, Tsagarakis, Guglielmino, Focchi, Cannella and Caldwell2011; IIT 2018). The ground reaction forces are extracted from experimental data sets and transformed into a local coordinate system to estimate the loads for the lower leg structure. Based on the experimentally measured loads, a conservative load case envelope of eight individual load cases is derived (Table 1). For example, load case 1 (LC-1) consists of a superposition of the maximum compression force
$F_{x,\text{loc}}=-1100$
N with the maximum bending load
$F_{B,\max }=1050$
N which acts at an angle of
$5^{\circ }$
from the local
$z$
-axis. Applying the formula
$F_{B,\max }=\sqrt{(F_{y_{\text{loc}}})^{2}+(F_{z_{\text{loc}}})^{2}}$
to LC-1 results in
$F_{B,\max }^{5^{\circ }}=\sqrt{(92)^{2}+(1046)^{2}}=1050$
N. The other load cases were calculated accordingly.
Table 1. Load envelope comprising eight load cases


Figure 3. Design concept for the hollow multi-material part using additive manufacturing for structural and functional interfaces and a load-bearing shell made of composite materials.
3.3 Design concept
A multi-material design concept combining additive manufactured structural elements with high-performance CFRP prepreg is proposed. The design concept combines the strengths of both AM and the prepreg layup technologies in accordance with Ashby’s guideline for hybrid material selection (Ashby & Bréchet Reference Ashby and Bréchet2003). CFRP are materials with outstanding stiffness- and strength-to-weight ratios if the fibers are oriented in the direction of the load. Therefore, they are appropriate for light, load-bearing, shell structures. AM, on the other hand, allows to realize 3D design features with a defined geometry which is promising for complex functional and structural elements such as load introductions and interfaces (Love et al. Reference Love, Kunc, Rios, Duty, Elliott, Post, Smith and Blue2014; Türk, Klahn & Meboldt Reference Türk, Klahn and Meboldt2015). The promise of AM with CFRP is the realization of highly efficient structures by (i) realizing more efficient and more complex lightweight designs, (ii) reducing the part count through integral design, (iii) saving material through optimized load paths, and (iv) integrating additional functionalities through multi-functional design (Türk et al. Reference Türk, Klahn and Meboldt2015). Figure 3 shows the design concept for the lower leg structure. In this concept, structural elements are produced with AM to realize an optimal load-carrying 3D shape while providing assembly interfaces and ensuring the range of motion of the system. CFRP prepregs provide an efficient lightweight structural integrity over the length of the lower leg. The CFRP is co-cured to the AM parts.

Figure 4. Structural knee- and foot-interface elements with integrated features for processing and operation.
3.4 Structural AM elements
Figure 4 shows the detailed design of the structural knee-interface (a) and the foot-interface (d) elements which are designed to be manufactured with SLM. A key feature of AM is the integration of additional functionalities (Gibson, Rosen & Stucker Reference Gibson, Rosen and Stucker2010; Tang, Hascoet & Zhao Reference Tang, Hascoet and Zhao2014). The knee-interface element is a highly complex part featuring an integrated hard stopper to prevent the lower leg from additional damage in the case of software failure. Moreover, interfaces for the bearings and encoders are considered during the design. Particular attention is placed on the adhesion surface which is critical to transfer the loads from and into the CFRP. It is iteratively optimized to minimize stress peaks to allow for co-curing instead of bonding. The inner side is tapered to reduce the stiffness discontinuity in the transition area of the SLM part to the CFRP which also serves as a form fit to position the 3D-printed tooling shell.
Post-processing operations may significantly increase the total cost of the SLM part (Atzeni & Salmi Reference Atzeni and Salmi2012). Therefore, they should be considered during the design. In this research, temporary post-processing supports are integrated into the blank part (b) by including a clamping aid and a solid shaft to reduce the vibrations during machining. Moreover, a position stop is integrated, supporting the positioning of the part during post-processing. This allows to machine the part from two planes only (c). First, the upper stopper surfaces are machined for flatness and parallelism. In the same step, the inner encoder interface is machined from the top. Then, the bearing surfaces and the shaft are machined from the side, allowing for an efficient post-processing procedure without having to re-clamp the part. The foot interface (d) consists of a thin SLM shell with a blank cylinder at its end. The outer surface is co-cured to the CFRP. Form fits are integrated into the inner surface to position the foot interface to the clamping aid and two screw holes allow for its fixation. The clamping aid is circular to allow for lathing of the thread including a relief groove. The fixation is removable and the clamping aid is reusable to account for small series production. During pre-assembly, the inner form fits are also used to position the foot interface to the 3D-printed tooling shell.
3.5 Tooling
The tooling concept shown in Figure 5 consists of a 3D-printed shell providing the layup surface for the CFRP, the necessary interfaces for the pre-assembly, and post-processing features. The general shell thickness amounts to 2 mm to prevent deformations during filing of the support material. Pre-assembly features include holes for the positioning of the shaft and complex form fits for the positioning of the SLM parts. Tolerances of 0.2 mm are considered at the assembly interfaces (shown in red in Figure 5) to take into account the manufacturing inaccuracies of selective laser melting and sintering. Post-processing features consist of multiple longitudinal breaking lines which allow for shell removal after curing. The shell thickness is reduced to 0.6 mm to create stress peaks during mechanical removal loading. The stress peaks result from a geometric effect which can be scaled and adapted to various shell geometries.
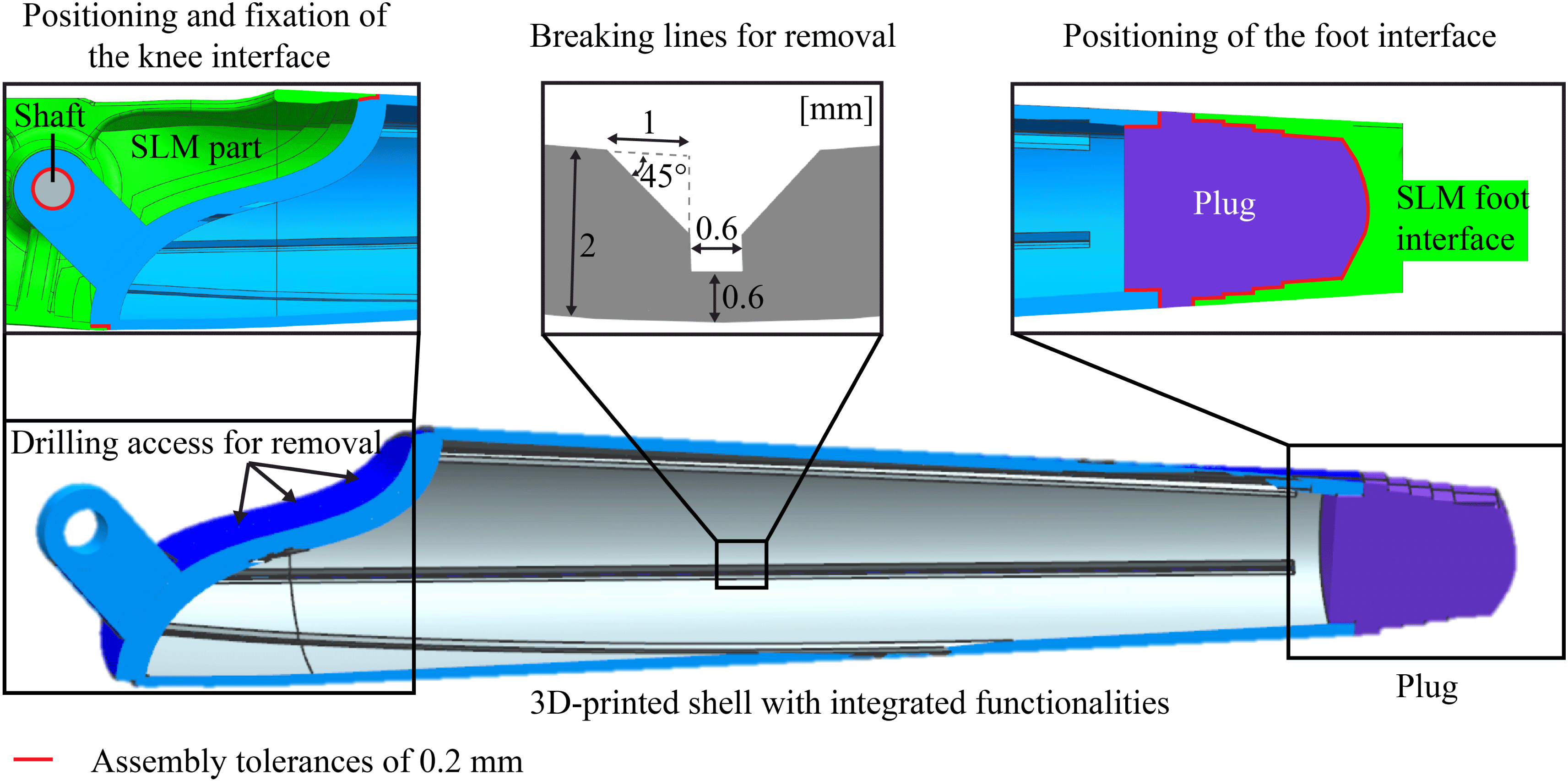
Figure 5. Additive manufactured shell with integrated design features including interfaces and breaking lines for post-cure removal of the shell.
3.6 Materials and layup
Material properties are summarized in Table 2. The composite layup consists of several layers of uni-directional (UD) SIGRAPREG C U150-0/NF-E34038% carbon-fiber prepreg with epoxy resin and twill fabric SIGRAPREG C W200-TW2/2-E323/45% manufactured by SGL Group (2018). The general layup concept consists of UD layers in areas which are mainly loaded in tension and compression, while twill layers oriented at
$\pm 45^{\circ }$
are placed in areas with significant shear loading. Local CFRP reinforcements are patched in critical areas including the transition from the CFRP to the knee-interface part. An offset is considered in circumferential direction to provide a taper. A symmetric layup is defined at the top and bottom: The first fabric ply is oriented in 0-direction
$(0_{f})$
and the second one is placed at
$45^{\circ }$
, denoted as
$(45)_{f}$
, followed by three UD plies at
$0^{\circ }$
$(0_{UD})$
. The layup is symmetric amounting to a total of 10 plies:
$(0_{f}/45_{f}/0_{UD}/0_{UD}/0_{UD})_{s}$
. On the sides, the layup is defined as follows:
$(0_{f}/0_{f}/45_{f}/0_{UD})_{s}$
amounting to a total of eight plies. The knee-interface parts are made from Ti6Al4V alloy processed with SLM due to excellent strength-to-weight properties of around
$260~\text{kNm}~\text{kg}^{-1}$
(Concept Laser 2018). The shaft is made from S355J2C steel.
3.7 Numerical model
A static linear-elastic simulation model was built in Abaqus to verify the structural performance of the hybrid part. The design allowables were defined to ensure the structural integrity of the leg for the entire lifetime (Table 3). The static strength of TiAl6V4 was conservatively derived from the material properties. A conservative value for the fatigue strength was chosen based on the assumption of a total of
$10^{6}$
load cycles for TiAl6V4 processed with SLM (Gong et al.
Reference Gong, Rafi, Starr and Stucker2012; Hosseini Reference Hosseini2012). Safety factors for static and fatigue loading were defined to 1.5 and 1, respectively.
The structural integrity of the CFRP was assessed using a maximum strain criterion amounting to 0.4% strain for static and fatigue loading. This factor is conservative, employed in aircraft industry, and already includes poor hot-wet notched compression performance and post-impact requirements. The co-cured adhesion area may be critical to the structural integrity of the hybrid part. Therefore, the allowable was set to 8 MPa, a conservative value. The single-lap shear strength of co-cured CFRP-Ti6Al4V joints was characterized in internally conducted tests and amounted to approximately 13 MPa. Therefore, a safety factor of 1.68 was achieved.
Table 3. Design allowables, where a refers to conservative values for the fatigue strength and based on single-lap shear test experiments

The finite element method (FEM) model in Figure 6 includes the two titanium parts and the CFRP layup. The titanium parts were modeled using tetrahedral solid elements with quadratic shape functions (C3D10), and for the CFRP S4R, general-purpose shell elements were employed. The CFRP shell and the AM parts were tied, assuming to be non-separable without any relative displacement. This assumption serves as a first approximation for the global behavior of the structure. Reference points and kinematic coupling was used to apply the constraints. The bearing interfaces were fully constrained except for the rotation around the local
$y$
-axis. The influence of the shaft was taken into account by limiting the movement of the corresponding nodes at the contact surfaces and fixing their displacement in the local
$z$
-direction through a reference point and kinematic coupling. The loads were introduced as concentrated forces using a reference point which was coupled to the lower surface of the foot insert. The foot consists of a spherical rubber which allows to introduce forces but no moments, and, therefore, it was idealized as a point contact with forces only.

Figure 6. Numerical simulation model for the structure using Abaqus. The composite is tied to the interface elements.
3.8 Manufacturing
The lower leg was fabricated according to the generalized manufacturing technique presented in Section 2. The tooling (comprising the shell and the plug) was produced from DuraForm HST Composite (3D Systems 2018) using selective laser sintering on a DTM Sinterstation 2500plus with a part bed temperature of
$170\,^{\circ }\text{C}$
, laser power of 48 W, scan speed of
$10~\text{m}~\text{s}^{-1}$
, and a hatch distance set to 0.24 mm. SLS was selected due to its relatively high accuracy (Salmi et al.
Reference Salmi, Paloheimo, Tuomi, Wolff and Mäkitie2013), potential cost-efficiency for high-variety manufacturing (Fontana, Marinelli & Meboldt Reference Fontana, Marinelli and Meboldt2017), and its freedom of design. Also, the HST material is commercially available and exhibits acceptable thermo-mechanical properties (Türk et al.
Reference Türk, Brenni, Zogg and Meboldt2017). The filler material consisted of commercially available table salt which was filled into the shell and compacted by shaking and tapping. Salt is a granular material, exhibits a high compression modulus, has a melting temperature of up to
$800\,^{\circ }\text{C}$
(Sriapai, Walsri & Fuenkajorn Reference Sriapai, Walsri and Fuenkajorn2012), is inexpensive, and is widely available. The plug was produced with SLS and enclosed the inner volume of the shell. The plug and the shell were bonded using J-B Weld, a high temperature two-component epoxy system. In the next step, the tool was sealed to prevent resin inflow during curing. Note that sealing is critical to achieve satisfactory surface quality and mechanical performance at the inner surface of the CFRP, where post-processing may not be feasible and quality inspection may be difficult. The resin MGS L 235 and the corresponding hardener were manually applied using a roller and cured at room temperature to seal the tool. Next, a standard release agent (Axel XTEND 832) was applied to allow tool–part release after curing.
The SLM parts were produced from Ti6Al4V on a Concept LaserCusing machine by 3D Precision SA, Switzerland. The parts were removed from the building platform. The bonding surfaces were covered during the sand-blasting operation to retain the as-built surface roughness. To relieve residual stresses, the parts were heat-treated in a chamber filled with argon gas. The parts were heated at a rate of
$5\,^{\circ }\text{C}~\text{min}^{-1}$
, held for 2 h at
$840\,^{\circ }\text{C}$
, and cooled down at a rate of
$1\,^{\circ }\text{C}~\text{min}^{-1}$
to
$500\,^{\circ }\text{C}$
, resulting in a total cycle time of 12 h. To account for part errors due to thermal deformation (Paul, Anand & Gerner Reference Paul, Anand and Gerner2014), a positive material offset of 1 mm was considered on relevant functional surfaces of the SLM parts. In the next step, the SLM parts were machined for functional surfaces and tolerances. The knee interface was screwed to a counter-part using the integrated clamping aid (Figure 7) which acted as a reference surface and allowed for automated machining. In the last machining step, the vibration support was removed. The foot interface was attached to the 3D-printed machining tool, and the thread and the groove were lathed.

Figure 7. Machining of the 3D-printed titanium knee-interface element.
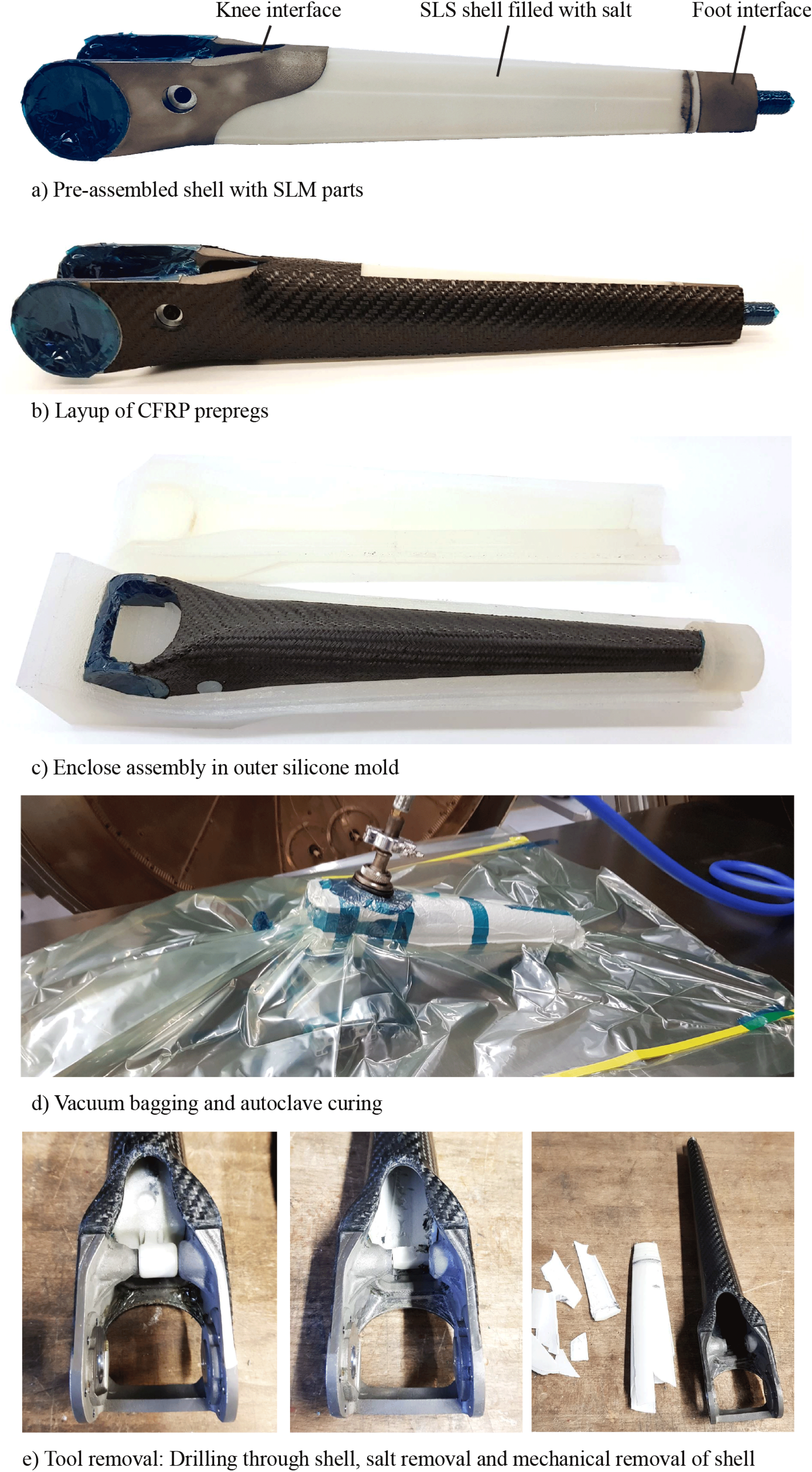
Figure 8. Manufacturing technique combining a 3D-printed shell and structural elements with carbon-fiber prepreg composite for autoclave processing.
The separate parts consisting of two structural SLM elements and the sealed tooling were assembled using the integrated positioning and fixation features of the 3D-printed tooling, as shown in Figure 8a. The knee interface was fixed using the shaft and the foot interface was fixed using bolts. Adhesive tape was applied to functional surfaces to avoid resin contamination. The prepreg material was cut to the desired shape and laid down on the pre-assembled tool according to the layup defined in Section 3.6 (b). The entire assembly was placed in a two-part silicone outer mold. ProtoSil RTV 245 silicone from Altropol (Altropol 2018) was cast into a 3D-printed master mold to form the outer soft tooling. The silicone mold should support the compaction of the CFRP, improve the pressure distribution, and minimize wrinkles (c). The assembly was vacuum bagged (d) and cured in the autoclave: The assembly was heated at a rate of
$1\,^{\circ }\text{C}~\text{min}^{-1}$
up to
$100\,^{\circ }\text{C}$
, held for 300 min, and cooled down at a rate of
$1\,^{\circ }\text{C}~\text{min}^{-1}$
. Vacuum and 2 bar autoclave pressure were applied.
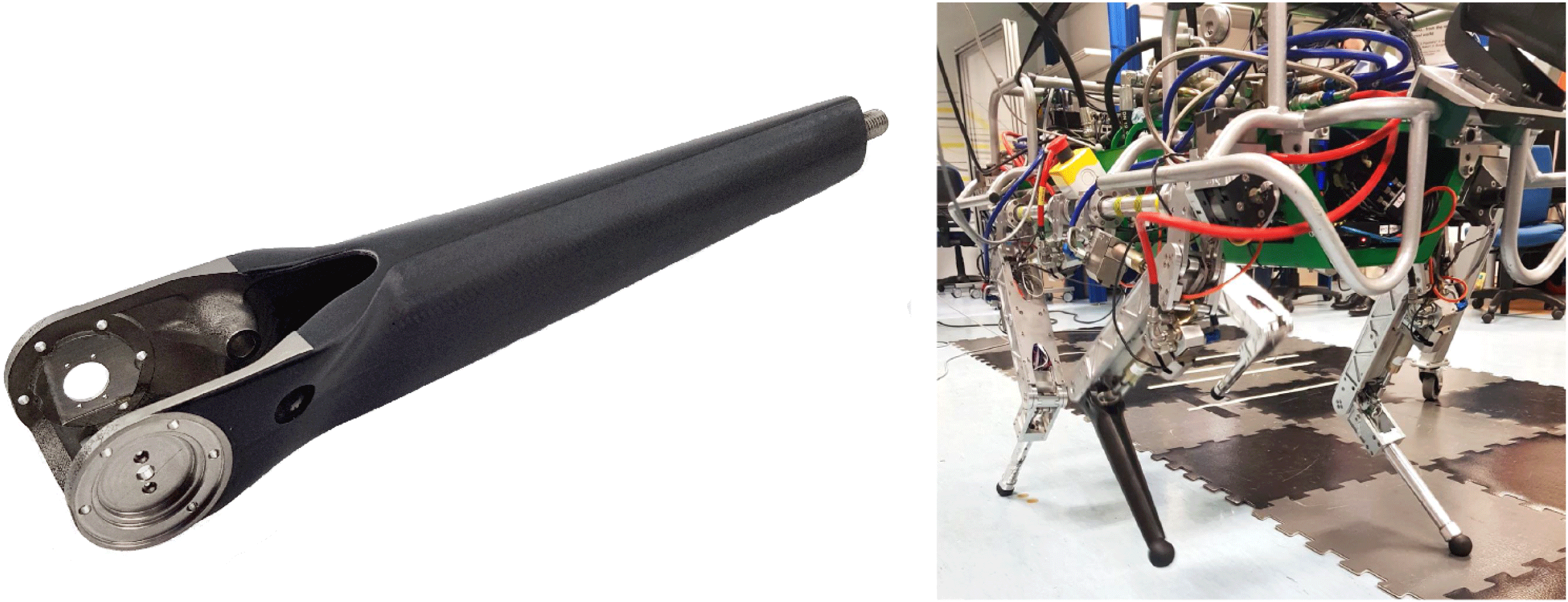
Figure 9. Hybrid co-cured composite structure with integrated structural titanium interfaces (left) and during operation on the HyQ robot at the Italian Institute of Technology in Genova.
After curing, the following steps were taken to finalize the part (e). First, the shafts and the bolts were removed which were required for the fixation of the tooling. Then, a hole was drilled into the shell to access the salt. The shell was completely emptied from the salt. Finally, the shell was removed piece by piece using a plier. The shell successfully broke along the intended breaking lines. The plug was removed from the part by applying a force through the two bore holes of the foot interface. Finally, surface finishing operations were applied. The resulting structure is an intrinsic hybrid lightweight structure, as the hybridization occurred during the curing process. The structure is complex-shaped and hollow. It was mounted on the HyQ robot (Figure 9) and successfully operated through a set of highly dynamic maneuvers.
4 Results
4.1 Simulation results
The load envelope consisting of eight load cases was numerically analyzed for structural substantiation. Table 4 shows the maximum Von Mises stresses in the knee-interface element and the maximum in-plane strain in the composite laminate. The simulation revealed that combined tension and bending loading at
$25^{\circ }$
(load case 5) yields stresses amounting up to 489 MPa located in the bearing seats of the knee interface (Figure 10a).
Table 4. Von Mises stresses in the knee interface and logarithmic laminate strains in the composite for different load envelopes

To determine the structurally critical location of the composite laminate, the maximum absolute value for the in-plane logarithmic strain (LE) was evaluated within each ply and calculated at the nodes of each element (Figure 10b). The maximum strain is observed for a combined tension and bending loading at
$45^{\circ }$
(load case 6) and amounts up to 0.31% in the transition of the composite to the knee interface. All values are below the allowables defined in Table 3 and therefore the design is acceptable.

Figure 10. Simulation results for the critical load cases. Peak stresses are recorded for load case 5 in the bearing seats. Maximum in-plane laminate strain is found for load case 6 in the composite at the interface to the knee interface.
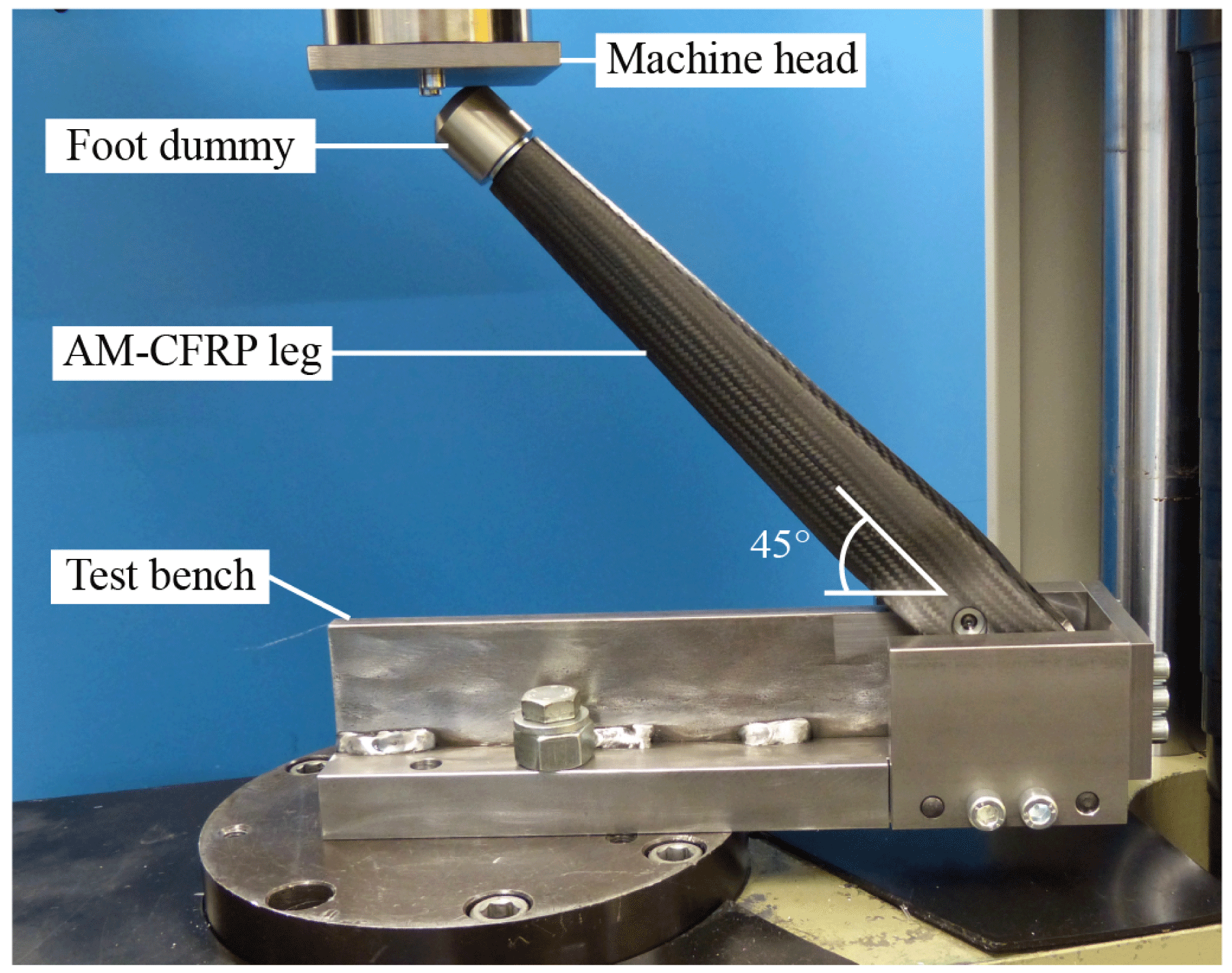
Figure 11. Ultimate strength test setup.
4.2 Ultimate strength test result
A static test setup (Figure 11) replicating the compression–bending load case 3 (LC-3) was designed. LC-3 corresponds to a very common loading type during the operation of the robot which can easily be replicated using a tensile testing machine and a simple test setup. The purpose of the ultimate strength test is to identify the maximum loading capabilities of the structure and to verify the simulation model for operational load ranges. In this setup, the part is oriented at an angle of
$45^{\circ }$
to the horizontal. A static load was applied vertically into the foot dummy. The part was constrained at the bearing surfaces and at the shaft imitating the boundary conditions when mounted on the HyQ. The test load was applied using a Zwick Retroline DO131569 tensile testing machine with a displacement rate of
$0.5~\text{mm}~\text{min}^{-1}$
until failure occurred.
Figure 12 compares the test with simulation results. The force-displacement diagram shows a quasi-linear behavior until reaching a load of 2900 N where a loss in stiffness was observed. The structural integrity was maintained up to the ultimate load of 5994 N where abrupt failure occurred. The ultimate load significantly exceeded the operational load of 1600 N. In the simulation, the displacement of the load introduction point (foot interface) was taken as a reference. The simulation and the experiment are in good agreement for loads amounting to approximately 2900 N. In this area, the experimental stiffness of the structure amounts to
$543~\text{N}~\text{mm}^{-1}$
compared to
$577~\text{N}~\text{mm}^{-1}$
in the simulation, corresponding to a deviation of 6%. Non-linear effects may have occurred for loads above 2900 N which are not captured by the linear-elastic simulation. The steel shaft showed plastic deformation, which may have caused the discrepancy between the simulation and the experiment. Also, first failure in the CFRP may have occurred. However, both the simulation and the experiment highlight the structural integrity of the novel lower leg structure for loads within the operation envelope.

Figure 12. Comparison of experimental and simulation results for static loading.
The failure locations depicted in Figure 13 show that the co-cured interface of the CFRP to the knee interface is critical. Mixed failure including laminate and adhesive failure is observed (a). We assume that the combined compression and bending loading induced shear and peel stresses which may have caused this type of failure. In addition, cracks in the laminate were observed next to the cutout of shaft (b). First, the co-cured area may have failed, leading to significant stress peaks and causing laminate fracture.

Figure 13. Laminate and mixed failure mode at the interface of the CFRP shell to the knee interface.
4.3 Weight
The final prototype weighs 298 g which corresponds to a reduction of 55% compared to 660 g of the reference design. The values are averaged over two prototypes and rounded to the gram. One hundred and fifty-one grams are attributed to the knee interface, 24 g to the foot interface, 13 g to the shaft, 2 g to the sleeve, 104 g to the CFRP, and 4 g to the bolts and the washer. The weight savings arise from several factors. First, lightweight CFRP materials were used instead of aluminum. Second, the part count was significantly reduced through an integral design approach. The stopper and the bearing seats were integrated into the knee interface which allowed to eliminate joining elements. Moreover, one integral CFRP shell was employed compared to multiple machined elements requiring additional joints. Third, the freedom of design provided by the combination of AM with CFRP allowed to realize better load-oriented shapes which reduces the amount of un-utilized material.
5 Discussion
A manufacturing technique combining a 3D-printed shell with a granular structural support material for autoclave curing of CFRP was proposed and applied to a robotic structure. The main implications arise from separating shape, functionality, and structural curing support of the tooling. A major advantage of the proposed technique is the possibility for individualization and variety manufacturing of complex composite and hybrid structures without significantly increasing the manufacturing effort. The technique is design-driven and allows for rapid modifications and the realization of scalable product variants and families (Lei, Yao, Moon & Bi Reference Lei, Yao, Moon and Bi2016). Design changes are mainly conducted in the digital environment and translated to digital production files for automated fabrication of shells and molds and near-net shape cutting of the reinforcements. Thus, the technique leverages the customization potential of 3D printing which is extended to composite manufacturing.
The technique is suitable for lot size one and small volume manufacturing of highly custom parts. However, scaling the technique to mid to high volumes is limited by the manual layup process, which is time-consuming for complex layups and geometries. While AM is automated and multiple layups can be cured in a single autoclave, the estimated time for performing the layup process typically scales proportionally with the production volume, and paralleling layup requires additional workforce.
In future, by leveraging a streamlined digital workflow for AM (Bonnard, Mognol & Hascoët Reference Bonnard, Mognol and Hascoët2010; Kim et al. Reference Kim, Witherell, Lipman and Feng2015) in combination with a product and manufacturing systems platform (Landahl et al. Reference Landahl, Levandowski, Johannesson, Söderberg, Wärmefjord, Carlson, Kressin, Isaksson and Vallhagen2016), we expect to significantly improve design and manufacturing efficiency for complex variants. The proposed technique may be cost-competitive as the printing time is shorter and material consumption is lower compared to solid 3D-printed tooling. The separation of functions allows to process commercially available SLS materials in autoclave conditions instead of employing proprietary materials. Moreover, the technique allows to integrate accurate design features and thus to include additional functions into the shell considering only few manufacturing restrictions. By using SLS for the shell production, minimum wall thicknesses have to be considered for stable processing, but no support structures are required and the dimensional error is relatively small (Ibrahim et al. Reference Ibrahim, Broilo, Heitz, de Oliveira, de Oliveira, Nobre, dos Santos Filho and Silva2009; Salmi et al. Reference Salmi, Paloheimo, Tuomi, Wolff and Mäkitie2013). Also, bigger shell structures may be possible by assembling separate shell segments.
The study revealed a few limitations. The tooling was tested in an autoclave curing cycle at
$100\,^{\circ }\text{C}$
and a total of 3 bar pressure only. Many aerospace structures are cured at
$180\,^{\circ }\text{C}$
and pressures ranging up to 10 bar. The limits of the processing window of the proposed technique are not yet known and the thermal behavior of the polymeric shell at extreme processing conditions was not investigated. The technique has worked well for the given geometry which was closed, elliptic, and approximately 30 cm in length. The filler material has well supported the shell during curing as no dents were observed. However, for a larger filling volume, the shell design may require modifications. The shell may be modeled as a plate with a distributed pressure loading. To avoid dents, the free length of the shell may have to be reduced for larger areas subjected to combined thermal and pressure loading. A simulation model for the prediction of the mechanical behavior of the shell and the filler subjected to thermo-mechanical loading is desired. The shell removal is critical to achieve a lightweight structure and requires part specific modifications. Studies on design guidelines for shell removal should be conducted by characterizing design parameters including the pre-determined breaking line geometry, breaking line length, and pitch, to name a few. The autoclave process was selected for curing, but the technique has the potential for extension to other composite manufacturing processes. 3D-printed shell elements filled with granular filler material may withstand high pressures and therefore have significant potential for applications in resin transfer molding and forming techniques, potentially allowing for a new scale of flexible high-volume manufacturing.
The simulation and the ultimate strength tests have shown that the co-cured interface of the CFRP to the titanium SLM part is critical to the load-bearing capability of the hybrid structure. Multi-material designs often exhibit stiffness discontinuities at interfaces which may yield stress peaks. Both AM and the prepreg technology offer potentials for the design of a bonding area with quasi-equal stiffness. The prepreg technology allows to tune the stiffness by varying materials, layup design, ply thickness, and orientation. The surface roughness of SLM may affect the bonding strength. Parameters influencing the surface roughness of SLM parts mainly include the building orientation and post-processing operations such as sand-blasting or roto-finishing. The process inherent (as-built) surface roughness could be beneficial to the bonding strength. Future joining concepts may use the peculiarities of AM or include novel 3D pin reinforcements that mechanically interlock with the reinforcements or resin modifications. These results also reveal potential for further weight savings in the composite outside the interface. The application of fiber patches on a base laminate allows for optimization and tailoring of the structure and thus for improved utilization of the material. Optimal patch reinforcements may be found from numerical optimization (Kussmaul, Zogg & Ermanni Reference Kussmaul, Zogg and Ermanni2018).
Weight savings of 55% were achieved compared to the reference structure. In addition, the mass moment of inertia could be reduced by roughly 70% as the center of gravity was moved close to the knee joint. Both characteristics should significantly impact the dynamic behavior of the actuation of the lower leg. Future studies should investigate how weight and mass moment of inertia reductions affect the robot’s performance in terms of acceleration or power requirements.
6 Conclusions
A novel manufacturing technique for complex-shaped, hybrid composites was proposed. The key novelty is the removable tooling using a 3D-printed functional shell and a structural filler material for autoclave curing. The technique was applied to the lower leg structure of the HyQ robot: Carbon-fiber prepregs were co-cured to structural elements made by SLM, resulting in an intrinsic hybrid lightweight structure. The lower leg structure was tested in ultimate strength loading and successfully operated on the HyQ robot. Weight savings of 55% and significant lead time reduction indicate that the approach could be appropriate for complex-shaped, lightweight structures with potential for individualization.
Acknowledgments
We thank Dr. C. Semini and V. Barasuol of the Dynamic Legged Systems Lab of the Italian Institute of Technology for proposing the HyQ as a case study and for providing the experimental loads in Section 3.2. We thank Prof. P. Ermanni of ETH Zurich and Dr. M. Zogg of Inspire AG for providing access to the laboratory infrastructure. We also thank D. Fenner of ETH Zurich for his excellent craftsmanship on the milling machine. This research was supported by the Product Development Group Zurich, ETH Zurich.