1. Introduction
Many companies would state that their aim is to design products that meet their requirements in a reliable and cost-effective manner. Therein lays one of the fundamental tensions of product development. A reliable product is often one that has large safety margins so that it can handle unexpected patterns of use over long periods of time, while a cost effective one might just meet the requirements, that is, one that is not overdesigned. Many products share components with other products through product platforms, which are designed to the requirements of the most demanding application, and thereby overdesigned with regards to many of their applications. As designs are frequently changed during the design process, designers keep margins to absorb the effect of these changes. At the heart of this is the question what are suitable margins on components and systems? A margin on a design is intuitively a straightforward concept, indicating a sort of surplus to what is needed. However, margins are added for a multitude of reasons, under many different names and depend heavily on the use context. Further, margins are not just assigned to the design itself but also to the requirements and even the processes of design and manufacture. At present margins are not captured systematically and the tacit way of dealing with margins is a real source of ‘late discovery’, ‘built in constraints’ and unbalanced products. This paper reports on an empirical study in a truck company which analysed how different groups in the organization add and reduce margins throughout the product development process. The paper argues that a clear understanding and articulation of margins would enable organizations to make active use of these margins to improve both products and processes.
As these margins are referred to by different names, such as room for growth, safety margins or design margins, they are often not visible or obvious to others in the organization, so that companies run the risk of unintentional overdesign. In practice because margins are added both to the requirements as safety margins and to the product as design margins, there is a risk that margins are added twice, often for similar reasons. This paper describes the different terminology used in one organization and shows the different roles margins play across the design process and in particular how margins are a critical but often overlooked aspect of product platform design. This paper argues that an improved ability to set, record and manage margins throughout the entire product development process has potential to enhance these processes, especially in larger organizations. This paper presents the results of a case study in a truck design company and shows the variation in their terminology. It builds on a recent paper (Eckert, Isaksson & Earl Reference Eckert, Isaksson and Earl2019), which formularized the concept of margin and discuss its role in managing iteration in jet engine design. The jet engine designers were also part of validating the empirical findings of the paper.
Margins on a component or subsystem used in a product are relative to that specific product and its intended use. In products such as automotive trucks which have a range of options for different customers as well as variability in how they are used, margins can be difficult to determine. Nevertheless, an awareness of the state of margins throughout the design process can help the designers to accommodate changes and make decisions about design choices. Complex products such as automotive trucks are designed using product platforms that share components across different models and – in the case of the trucks – across different brands. Platform components are designed in a way that they can meet the requirements of the applications with the highest intended demand on performance and can potentially incur large margins for applications with low demands (Isaksson, Lindroth & Eckert Reference Isaksson, Lindroth and Eckert2014). This makes margins a key concept in the design of product platforms.
Both hidden overdesign and hidden underdesign carry real risks for products. Underdesign can lead to failure especially over the lifetime of a product, while overdesign can result in higher purchasing and running costs making products less competitive. These costs can be traded off against cost reductions through component commonality. However, as the empirical study indicates, margins are not tracked systematically across variants in a product platform. Unless margins are clearly expressed and used for such trade-offs and more importantly kept for changes and updates, their potential cannot be used.
In most design research, margins have been considered primarily as means to cope with uncertainty, not as inputs that define opportunities to improve the product or to manage design processes efficiently. Appropriate design margins can absorb changes arising during the design process (Eckert, Clarkson & Zanker Reference Eckert, Clarkson and Zanker2004) and reduce the number of design iterations (Eckert et al. Reference Eckert, Isaksson and Earl2019). Further, they can enable existing products and components to meet new requirements without requiring costly redesign. This is especially relevant as new requirements drive the design of a new product generation. Highly optimized products, that is, those where margins have been taken out, might reduce the production cost for one product generation, but can seriously add to the development cost of the next product generation.
This paper starts with a discussion of related concepts in Section 2 and includes an outline of a formal model of margins (Eckert et al. Reference Eckert, Isaksson and Earl2019). The methodology of the empirical study is introduced in Section 3. The industrial context of automotive trucks is described in Section 4 which discusses some of the major concerns of truck design in terms of product platforms and brands as well as the organizational structure of the company. Section 5 analyses how different teams in the organization use a variety of different terminology through the design process, adding margins to both the requirements and the value of parameters. Some implications of margins for platforms and brands are drawn from the empirical study in Section 6 and mapped onto stages of the product development process in Section 7. Issues in determining and managing margins are addressed in Section 8 with overall conclusions drawn in Section 9.
2. Related concepts
The concept of margins has been addressed by two different communities: safety and design (Eckert & Isaksson, Reference Eckert and Isaksson2017). Safety researchers are concerned with protecting the product against known and unknown risks (see e.g., Modarres, Kaminskiy & Krivtsov Reference Modarres, Kaminskiy and Krivtsov2016 for a discussion of risk and reliability engineering or Oehmen et al. Reference Oehmen, Olechowski, Kenley and Ben-Daya2014 on risk management in the product development process), while design researchers see margins as a way of handling uncertainties during the design process (see de Weck, Eckert & Clarkson Reference De Weck, Eckert and Clarkson2007, for an overview of uncertainty in design).
This can be confusing to both designers and design researchers, as safety issues can also be seen as a source of design uncertainty. These two types of margin, the safety and the design margin, reflect the how margins are considered in industrial practice on both product parameters (design margins) and requirements (safety margins). One perspective on this distinction is provided by the formal framework to define margins in industrial processes by Touboul et al. (Reference Touboul, Reygner, Mangeant and Benjamin2019) who distinguish the effective margin in a design from the demanded margin which represents a requirement on the margin.
2.1. Types of margin and terminology
The literature on margins is extensive and reflects that the concepts of margins are studied for particular stages of the design process, for specific domains of products as well as on margins of different types for areas such as performance (Gale Reference Gale1975; Tan, Otto & Wood Reference Tan, Otto and Wood2016), assurance (Hockberger Reference Hockberger1976), safety (Möller & Hansson Reference Möller and Hansson2008; Iorga, Desrochers & Smeesters Reference Iorga, Desrochers and Smeesters2012), mitigating effects of changes (Tilstra et al. Reference Tilstra, Backlund, Seepersad and Wood2015; Cansler et al. Reference Cansler, White, Ferguson and Mattson2016) uncertainty (Thunnissen Reference Thunnissen2005), excess from standard or platform components (Martin & Ishii Reference Martin and Ishii2002, Eckert et al. Reference Eckert, Isaksson and Earl2019). Example domains include ships (Gale Reference Gale1975; Hockberger Reference Hockberger1976), space systems (Thunnissen Reference Thunnissen2004), buildings (Jones, Eckert & Gericke Reference Jones, Eckert and Gericke2018), aerospace (Guenov et al. Reference Guenov, Chen, Molina-Cristóbal, Riaz, van Heerden and Padulo2018, Eckert et al. Reference Eckert, Isaksson and Earl2019), nuclear facilities (Youngblood Reference Youngblood2010) and automotive (Lebjioui Reference Lebjioui2018). Margin research has tended to concentrate on the conceptual stages, especially for large and complex products such as ships, space systems, aerospace and buildings (Thunnissen Reference Thunnissen2004, Reference Thunnissen2005), although margin concepts such as factors of safety are discussed for the detail design of machine components by Juvinal & Marshek (Reference Juvinall and Marshek1991) in their classic textbook and manufacturing tolerances, which responds to uncertainties throughout product development (Morse et al. Reference Morse, Dantan, Anwer, Söderberg, Moroni, Qureshi and Mathieu2018).
These different scopes of interest in margin research, namely; stages, domains and types, provide different terminology tailored by designers in their industrial practice. However, this multiplicity of meanings and purposes of margins means that there might be a tendency for gaps and duplications to arise in practice. Therefore, a generic view of margins can aid integration across company teams and stages of the process (dealing with different functional parts of a product), supply chain for components and subsystems and the stages of the process. In this way, it is possible to avoid ‘surprises’ in integration. Most importantly this generic view offers the benefit of facilitating the interfaces between product systems, which is a critical aspect in design of complex engineering systems with their wide variety of stakeholders in product development.
The information bias in negotiations is modelled by Austin-Breneman, Yu & Yang (Reference Austin-Breneman, Yu and Yang2016) in terms of envelopes of parameter values in which they negotiate. Simulations of complex design processes reveal the effect of information bias on finding an optimal design. A similar theme is picked up in the work of Dawson, Fixson & Whitney (Reference Dawson, Fixson and Whitney2012), who examine design safety factors as a means to mitigate against misalignment between the product architecture and the organizational structure. They conclude that projects in which the all participants are incentivized to manage safety factors, converge much more successfully. Fernandes et al. (Reference Fernandes, Henriques, Silva and Moss2014) analyse data about change requests for jet engine design and identify imprecision in key parameters as a significant cause of design iteration. They propose communication of this imprecision more clearly to different design teams.
Margins change in scale and type through product development. Set-based design (Sobek II, Ward & Liker Reference Sobek, Ward and Liker1999; McKenney, Kemink & Singer Reference McKenney, Kemink and Singer2011) represents design options by ranges of parameters that narrow during a product development process. Canbaz, Yannou & Yvars (Reference Canbaz, Yannou and Yvars2014) express margins as min max values of ranges of acceptable values. A particular focus of the present paper is to trace, in an extensive study of industrial practice, how margins, and the terminology of margins, evolve throughout product development as designers attempt to meet challenges of new or revised customer requirements, regulatory regimes and new technologies.
Margins built into a design at the beginning of product development can contribute to its adaptability to new requirements during the product life cycle, in redesign (Tackett, Mattson & Ferguson Reference Tackett, Mattson and Ferguson2014) or in the design of a follow-on product (Ross & Hastings Reference Ross and Hastings2005). Margins introduce a degree of redundancy. Ross & Hastings (Reference Ross and Hastings2005) map out a ‘tradespace’ among parameters with margins indicated by where the design sits within this tradespace and De Neufville, Scholtes & Wang (Reference De Neufville, Scholtes and Wang2006) design options can be interpreted as moves in this tradespace. The notion of design option highlights that there is a cost associated with initial overdesign, which enables future product flexibility. Changing requirements during lifetime (Martin & Ishii Reference Martin and Ishii2002) and future evolution (Tilstra et al. Reference Tilstra, Backlund, Seepersad and Wood2015) are extended by Tan, Otto & Wood (Reference Tan, Otto and Wood2016) to assess the impact of multiple margins on systems performance.
Safety margins take account of risks (known and unknown) affecting the product and (Di Maio et al. 2016) in order to create reliable and optimal products, through modelling the distributions of risk. The safety margins can be calculated based on a systematic assessment of uncertainties (Youngblood Reference Youngblood2010). Some industry sectors, such as in construction, add safety factors to the requirements, to deal with uncertainties arising during the building process. Safety margins and safety factors are critical in the certification and licensing of products (Benjamin, Dezfuli & Everett Reference Benjamin, Dezfuli and Everett2016). Tolerances can become critical as design margins in optimized and detailed designs, where so called stack-up effects can cause multiplication. Once in production, the tolerances can be revisited and real margins identified, something where economic gains drive the introduction of digital twin concepts (Wärmefjord et al. Reference Wärmefjord, Söderberg, Lindkvist, Lindau and Carlson2017). Understanding real world geometrical variation and predicting these already during design has been demonstrated by Forslund et al. (Reference Forslund, Madrid, Söderberg, Isaksson, Lööf and Frey2018).
The terminology of margins is summarized in Table 1. A working formal definition of margins (Figure 1) developed by the authors (Eckert et al. Reference Eckert, Isaksson and Earl2019) attempts to connect and cover the relevant concepts reviewed above.
Table 1. Definitions of margin concepts in the literature
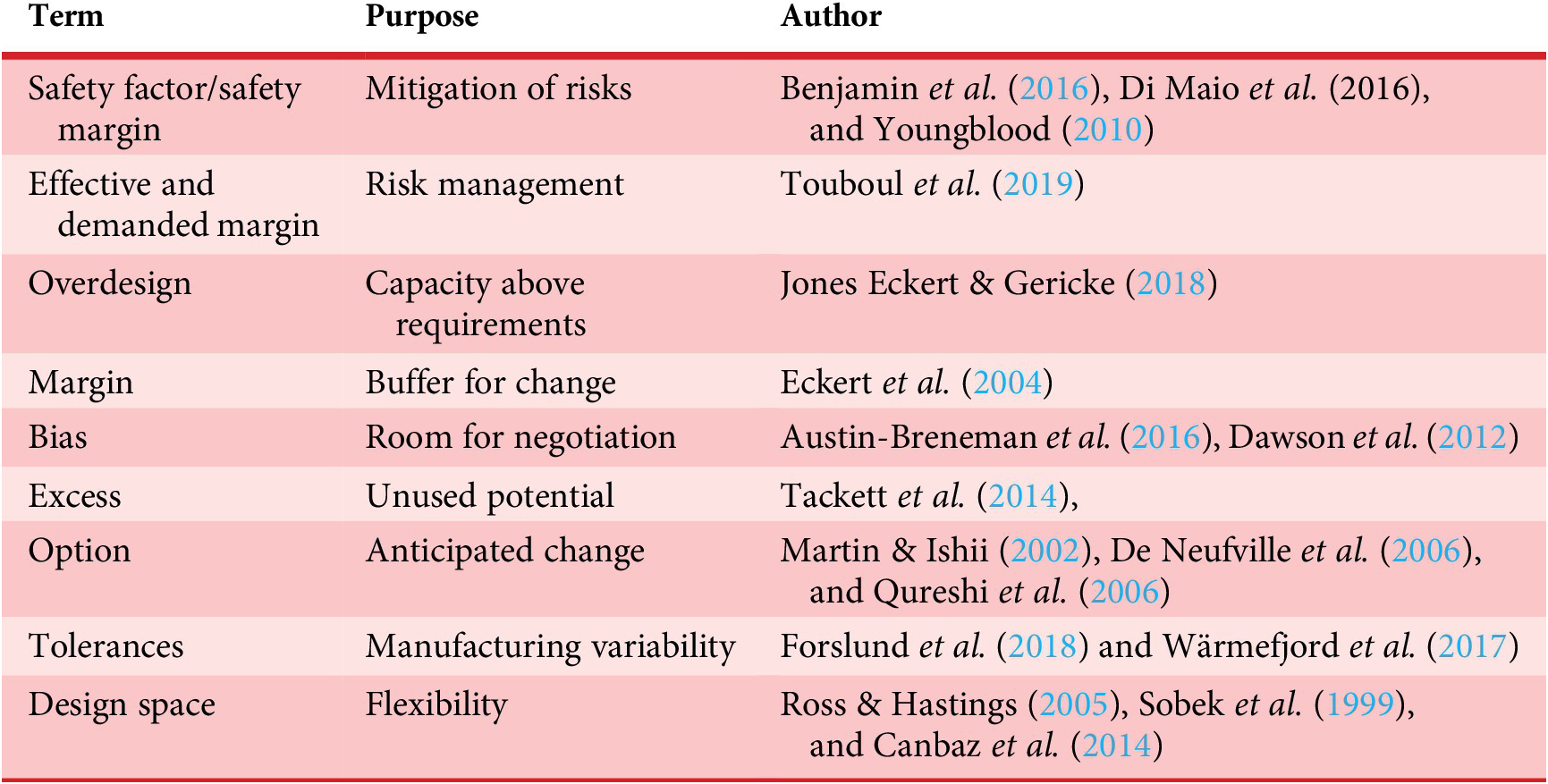
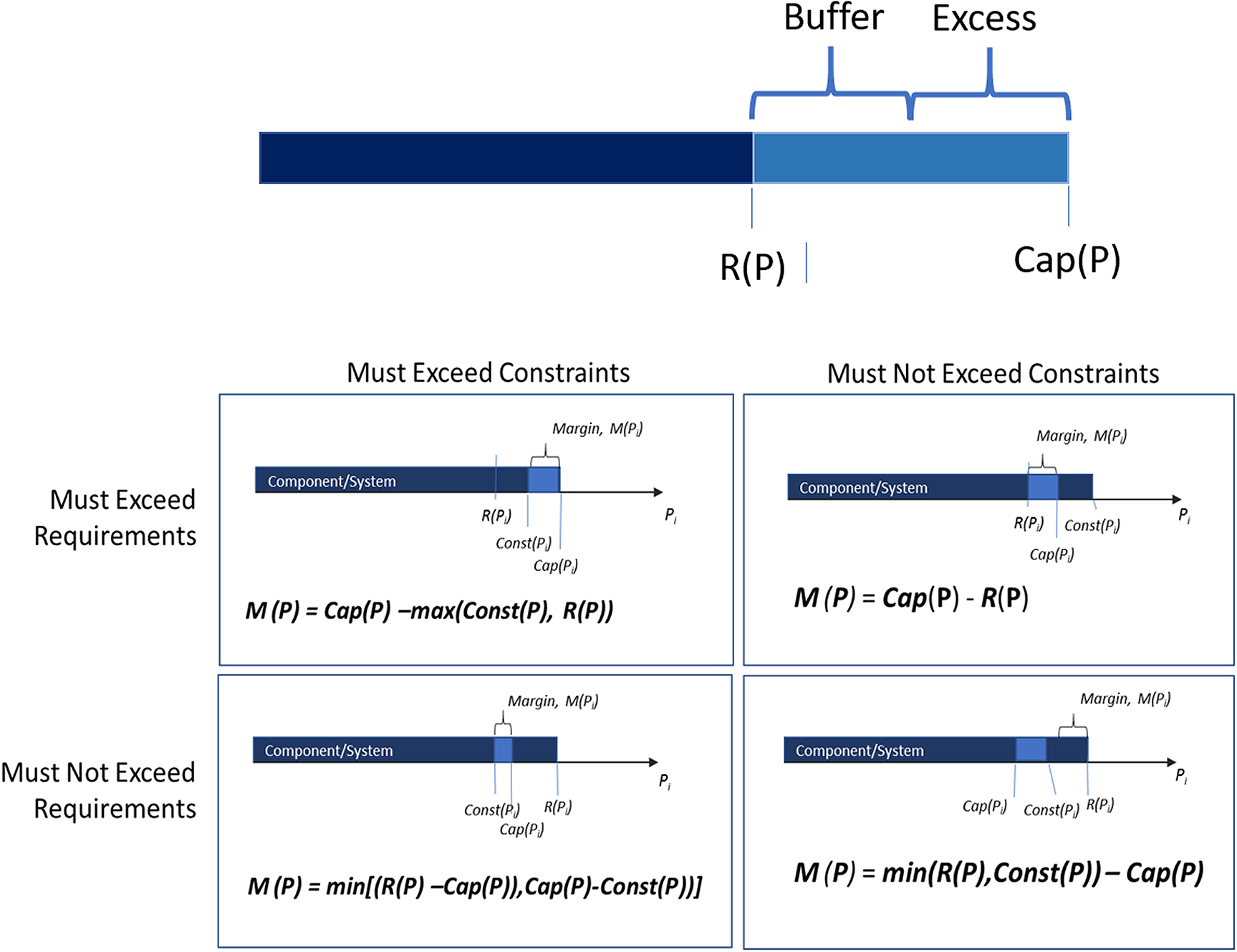
Figure 1. Margin (light blue bar) between requirements and capabilities for a component or system (Eckert et al. Reference Eckert, Isaksson and Earl2019).
2.2. Formal definition of margins
At any stage of product development, the evaluation of performance is to an extent uncertain, depending on the maturity of a design proposal as well as the resources and tools employed in evaluating the proposal. These uncertainties push designers to add buffer margins, as allowances made in parameters, in order to provide high probabilities of meeting functional requirements. The concept of excess is analysed by Tackett et al. (Reference Tackett, Mattson and Ferguson2014), from the perspective of how a design can be upgraded. They identified excess, as the ‘the quantity of surplus in a system once the necessities of the system are met’, while acknowledging that product design is subject to uncertainties.
Product parameters may have buffers, which are not immediately usable in design but offer the potential that they can be reduced and hence release tangible and usable margins. These can be used to accommodate changes in requirements during the design process which may be difficult to manage for companies developing large technical systems, containing multiple interfacing subsystems such as cars, trucks or jet engines.
Our example case illustrates that there may be limited quantitative knowledge about margins. Design margins are often derived from product codes and guidelines or may be empirically selected, based on experience rather than through theory or systematic methods.
In Eckert et al. (Reference Eckert, Isaksson and Earl2019), margins are defined formally in terms of the requirements for the product Req, the constraints Const on the design and its capability Cap, see Figure 1.
Margins have two aspects: buffers B against uncertainties and genuine excess E that can be used in a new design. The uncertainties can arise from any number of different factors, for example there can be uncertainty on the requirement or whether the design would in practice have the assumed capability over the life cycle of the product. As a company may not have a quantified view of their uncertainties, the exact point of division between buffer and excess might be subject to interpretation, but the conceptual distinction is useful.
A fully optimized product would have no excess margin in any of its parts. However, excess provides the ability to respond to new external requirements without redesign as well as changes to requirements which arise from the product development process itself, owing to knock-on effects of changes from one component or subsystem to another. The distinction between buffer and excess is particularly important since parts of the buffer can move to excess, if the source of uncertainty that the buffer caters for is removed, that is, by carrying out a test or by freezing a parameter.
Design margins help the component and system designers understand the key performance parameters, their requirements and thresholds, how robust they are to the required inputs and constraints, and how they interact with other components in a system or a product. However, a key challenge is that the word ‘margin’ has different meanings to different people; moreover, there are several types of ‘margin’ to be evaluated during the design process. This range of meanings and the variety of purposes of margins over a product development process is the focus of this paper.
3. Methodology
This research was carried out as part of a long-standing collaboration with Volvo Truck and GKN aerospace in a research project to use design margins in managing design processes and predicting the impact of engineering change. Volvo Truck develop, customize and manufacture trucks for a large variety of applications. GKN Aerospace is a tier one manufacturer of advanced jet engine components, and a partner and supplier to most jet engine system OEMs. A steering group comprising of senior representatives (managers and/or senior specialists) from Product Planning, Product Engineering, Technology and Methods Development and Platform Configuration and Development reviewed the progress and the results of the project at 2-month intervals. Figure 2 gives an overview of the study.
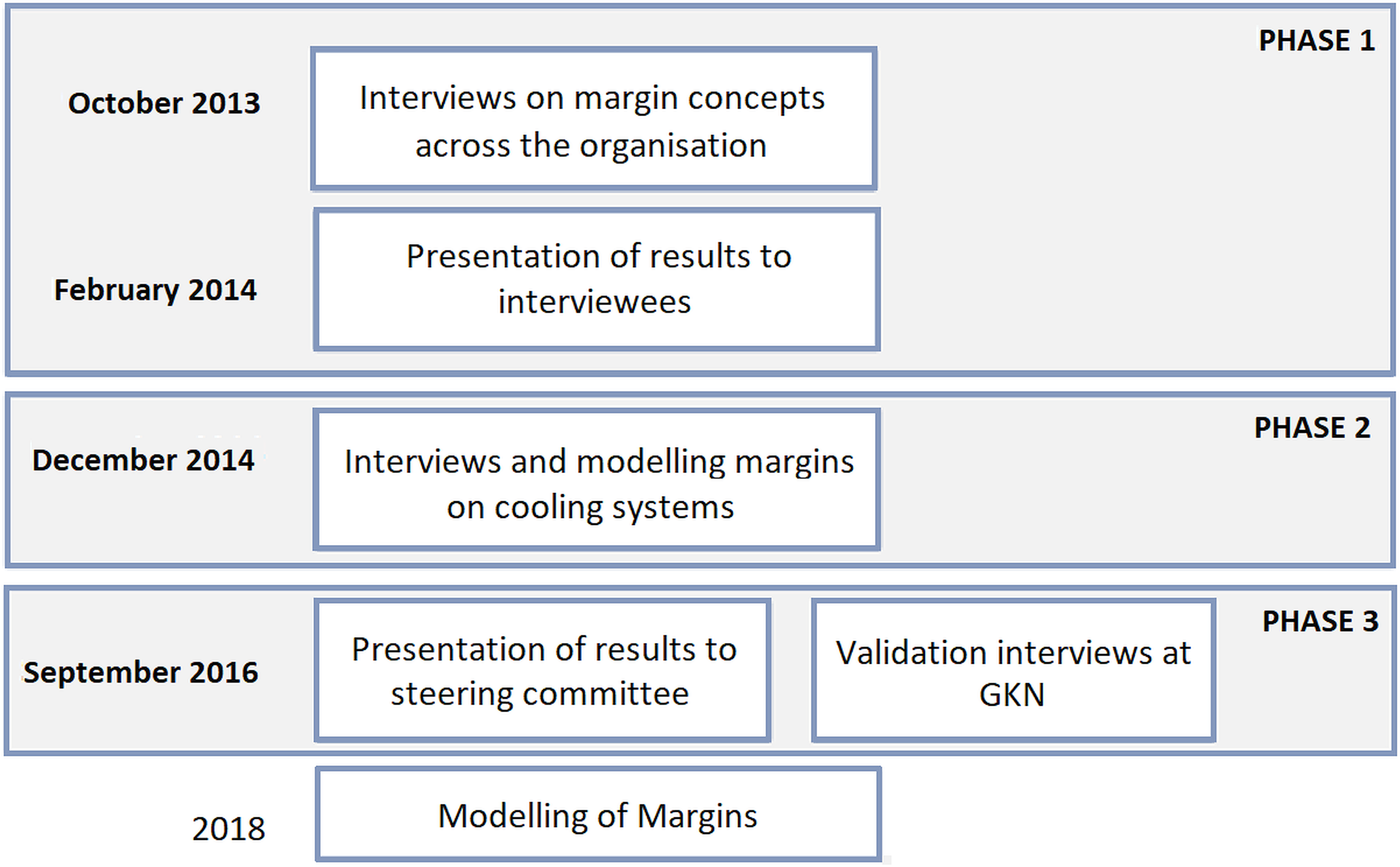
Figure 2. Overview of the three phases of the study.
The project started with a study of how margins are created and managed in the organization with the aim of identifying terminology used in the company around the concept of a margin, including concepts that are not recognized as margins internally. The starting point for the study was chassis development as many of the margin issues around chassis are geometrical and therefore fairly intuitive. The chassis is designed to provide a configurable platform component, with defined (discrete) integration interfaces to meet the multiple product families and brands supported.
A series of interviews was conducted in October 2013 with experienced engineers representing different aspects of chassis design across the product life cycle. The interviews were conducted in English by the first author and third author. All but one of the experts are native speakers of Swedish. The interviews were semiformal. Starting with a discussion of the role of the interviewee they explored how they handled change, variation and the risk of product failure to get them to talk about margins in the context of their own roles. The interviews were complementary and did not cover the same ground, however the interviewees were invited to comment on statements by their colleagues, if these fitted the context of the conversation.
Table 2 gives the roles of the interviewees. In addition, multiple discussions occurred with one of the chief engineers in vehicle engineering (E12). The experts were selected by the E12 and E5 as a representative sample of different roles that take part in the design of the chassis. E8 and E9 worked together on fuel systems and were interviewed together. The rest had complementary expertise and roles, however as some of them had over 35 years’ experience in the organization they all had insights into multiple roles that they held in the past or worked with closely.
Table 2. List of Interviewees by role
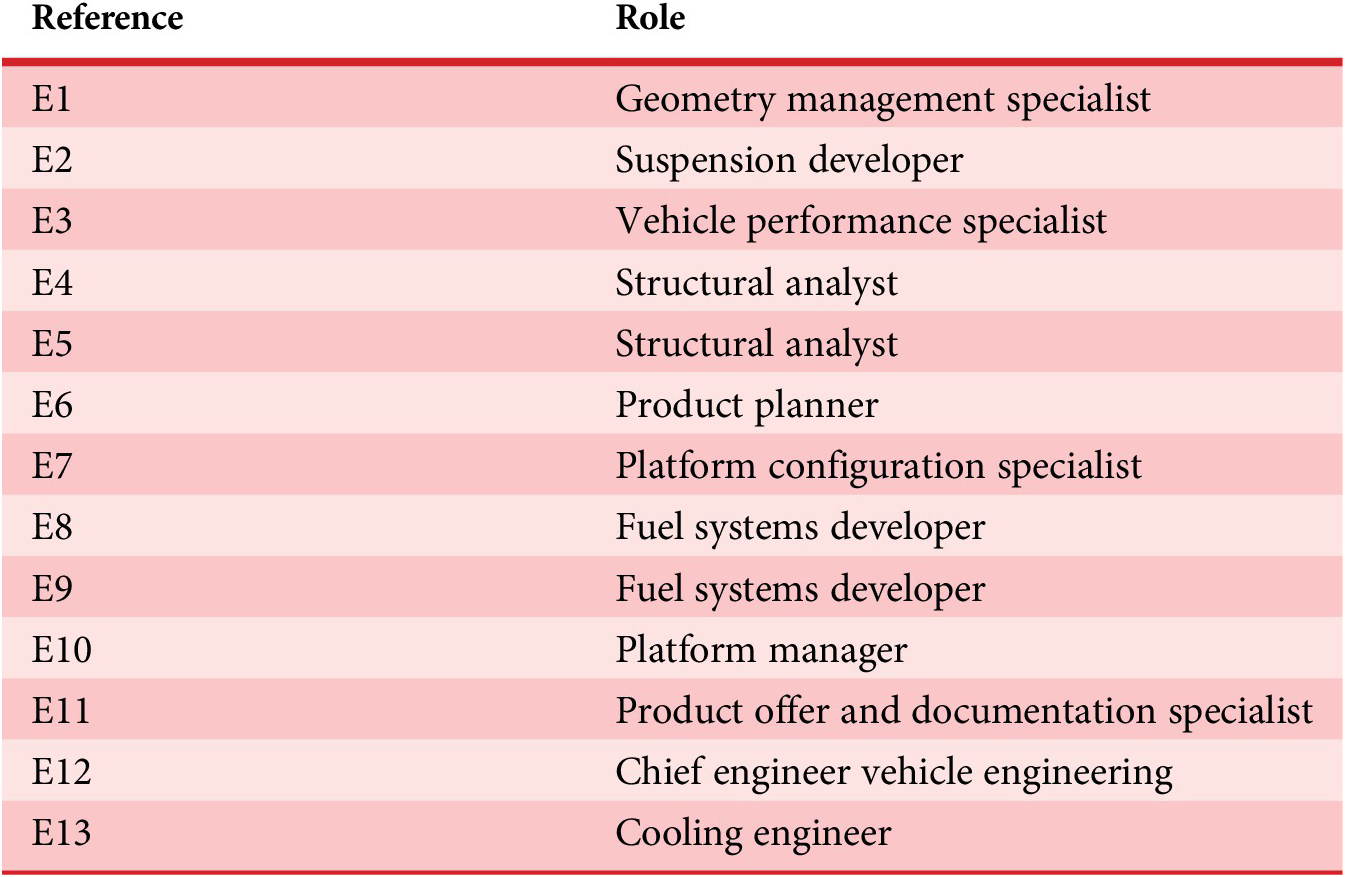
The findings were presented to a group of Volvo engineers, with a wider set of roles, including the steering committee members to which all interviewees were also invited. The participants commented on the findings and added issues that were missed in the presentation. These comments were captured and incorporated into the presentation and checked again with members of the steering committee.
A second round of interviews was conducted in December 2014, where a detailed case example was targeted to better understand a design team’s view on the margins. The case studied focussed on the cooling system, which is heavily constraint by the adjacent systems. The objective was to unfold and resolve the use of margins, and how changes are accounted for during design.
In 2016, the first definitions and representation models for margins were formulated and shown to the steering committee. In addition, three interviews were held with specialists and managers at GKN Aerospace. The objective was to validate the model. During the interviews the experts were asked about the how they handled margin issues, similar to those found in Volvo. Only at the end of the interview, they were shown the analysis presented in this paper.
The interviews were all recorded and transcribed. The analysis followed a loose thematic analysis approach (Boyatzis Reference Boyatzis1998). In the first round of analysis, the first author went in detail through the transcripts highlighting the sections talking about margins and summarized the remaining discussions. The discussion in the relevant sections were grouped into themes and key quotes were identified. Some of these quotes are used in the paper to illustrate key points.
In the second round, the interviewees (including E13) were revisited to look for further explanations on the identified themes as well as reflective comments. The third author also analysed the transcripts and identified themes relevant to margins. This analysis was used to validate and supplement the presentation. In addition, two planning engineers were interviewed to get a perspective on the early phases of product development.
In the third phase, the findings were presented and discussed with the steering committee and shown to the GKN engineers in a more general interview.
This study was a descriptive study and no particular view was considered normative. The engineers talked about the types of margins that were relevant to their area of work. When the engineers voiced differing or contradictory opinions, the causes were analysed. For example, E8 and E9 viewed margins as a positive, because they enabled them to respond to changes in their requirements, while E11 saw them as cost factors. This led to the analysis of margins across the design process presented in Section 7.1, which argues that a multitude of different notions of margins are used through the product development process. As the study focussed on using margins in design, the only safety engineers were part of the GKN team, so that the comments on safety margins came from their design engineers. During the presentation of the results, the engineers collectively recognized all the different notions of margins and often argued for the importance of their own aspect of margin. This strengthened the generalisability of the findings from the Volvo study.
4. The case study context
The study was carried out at Volvo Group Trucks Technology in Gothenburg. Volvo GTT is the research and development organization of the Volvo Group that provides research, engineering, product planning and project execution to final delivery of complete products and aftermarket support. The Volvo Group with their different brands has been developing and producing for a century. It offers a high degree of customization of the trucks with the aim of meeting different customer demands on a global market.
4.1. Trucks
Trucks are used in a wide range of applications and operating conditions. As an international brand Volvo Group trucks are used in all climate conditions from hot sandy deserts to cold northern winters. Some trucks are used in applications, such as long-haul haulage, where they are used for at least 8 or 10 hours every day in relatively steady conditions, others like fire engines are used in extreme situations at peak capacity. Trucks are used on different road surfaces from smooth motorways to rough roads and untreated surfaces, which put a large strain on the suspension.
Trucks are working vehicles, which are built for a specific application and must work reliably. Trucks are designed for robustness and durability. Running cost is an important cost factor of truck ownership and the truck companies are competing on fuel efficiency. To reduce fuel consumption, the companies need to develop more fuel-efficient engines and reduce the weight of the truck. Weight reduction is a driver for product proliferation. For example, long haulage trucks have large fuel tanks to avoid losing time for refuel or risk running out of fuel, while local delivery trucks might have a much smaller tank, since they can be refuelled at base while they are stocked.
Volvo Group sells different trucks for the European and U.S. market under the Volvo brand. Over the last 20 years, the Volvo Group has acquired several other brands to reach new markets. Mack trucks offers highly specialized trucks for the U.S. market including many for off-highway applications, while Renault trucks designs and produces trucks for mainly the European market. Recently the Volvo Group has also formed joint venture with a Chinese and an Indian brand.
The trucks of Volvo, Mack and Renault brands are aimed at different markets and market segments. European trucks have overall length restrictions whereas U.S. trucks have only restrictions on the lengths of the trailer (see Figure 3), which has allowed long cabs with a different configuration. In the European trucks the driver cabin is above the engine and the cooling system, whereas in the U.S. trucks the cabin is behind the engine with generous accommodation for driver on long distance journeys. The variety of trucks for Volvo Group brands is shown in Figure 4.
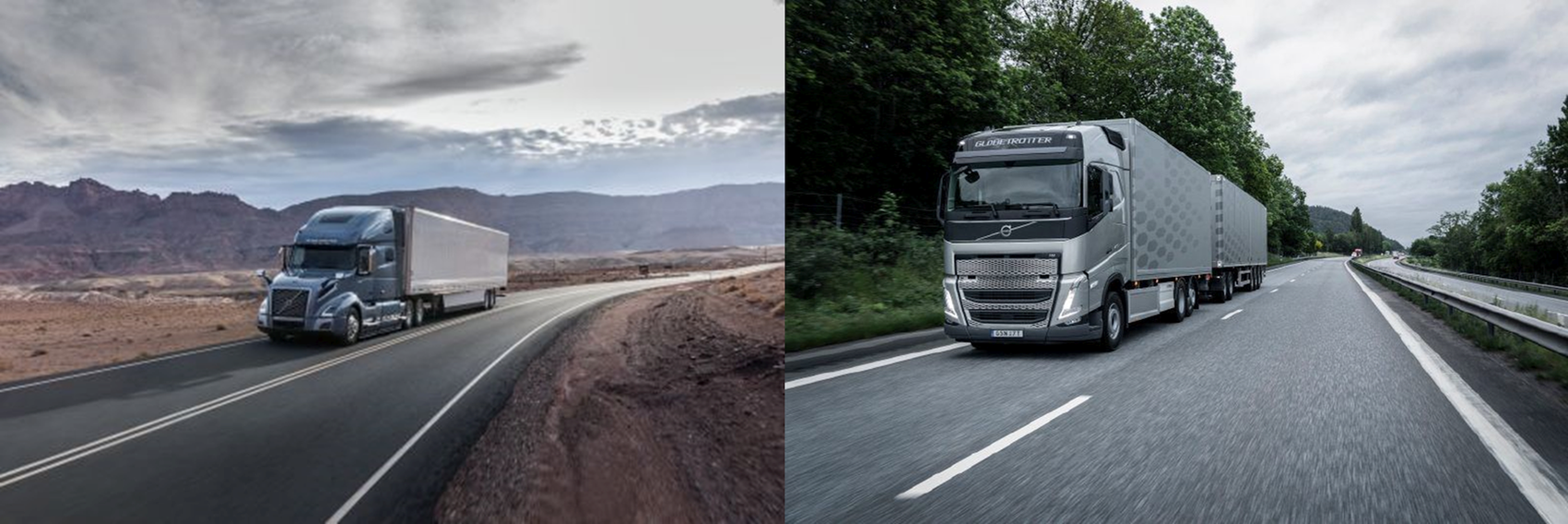
Figure 3. A U.S. (to the left) and a European (to the right) Volvo truck.
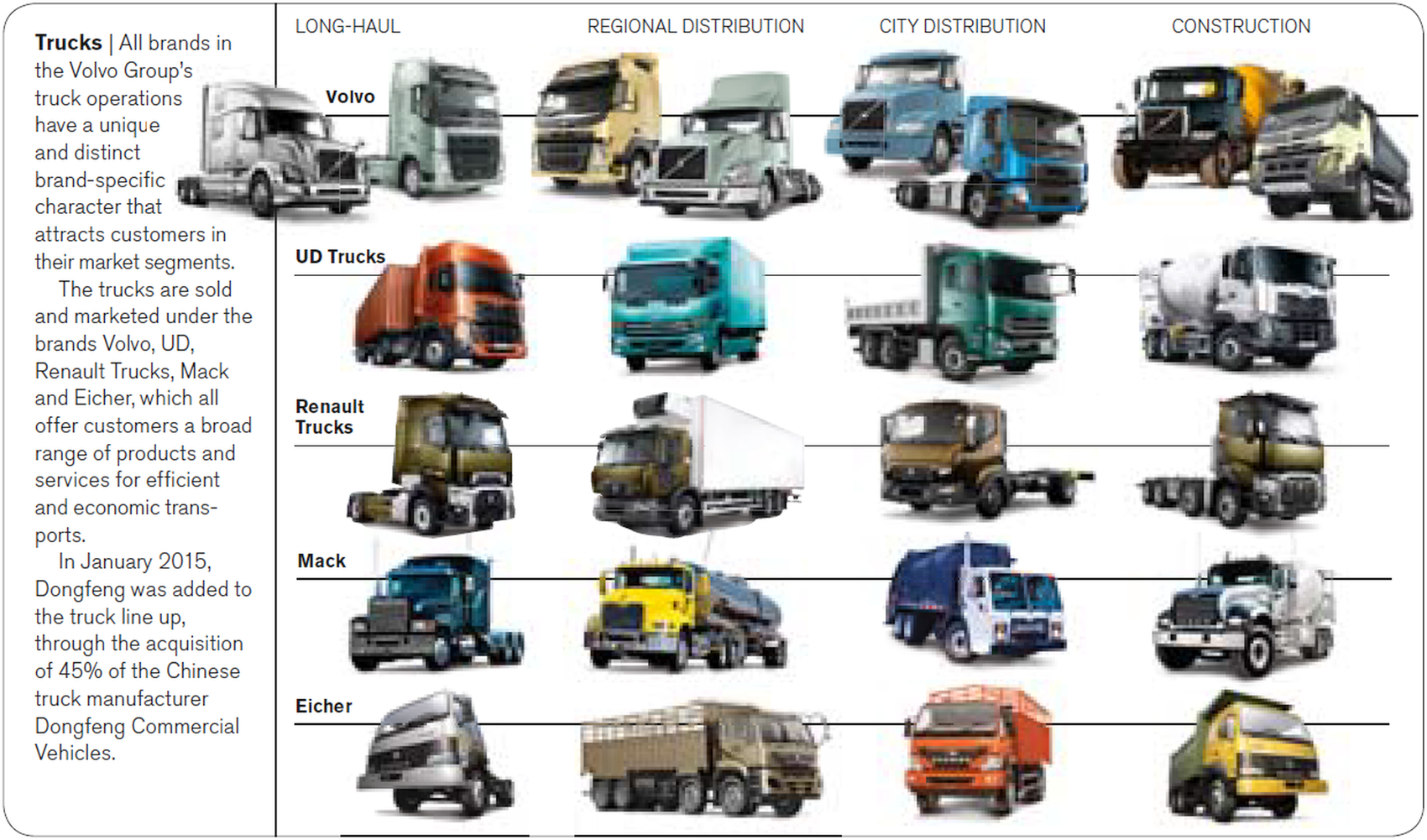
Figure 4. Different trucks of the Volvo Group at the time of the initial study from the annual report of the company (https://www.volvogroup.com/en-en/investors/reports-and-presentations/annual-reports.html.).
A complete truck with all its variation has around 500 different configurable elements (Variant Families), each with at least two versions (Variants). While many options are mutually exclusive, the number of different options is enormous. For each new element added to the product platform option, conflicts need to be checked. This incentivises the company to reduce the number of options offered by using the same components across large parts of its platform. However single components for multiple applications also implies that the components might be overdesigned for many applications.
4.2. The organizational structure in Volvo
The development of trucks is an iterative process across product planning, engineering and physical validation performed on different timespans (Figure 5). The product planning team initiate studies with the longest time horizon. They engage the organization in the development of the next generation of engines, investigate emerging technologies, such as hybrids or alternative fuels, but also analyse future trends in transport Brand oriented teams look at the long-term visions for the brand on a slightly shorter time scale. They analyse market developments and define and monitor the brand identity. The platform planning team governs the current platform and its anticipated evolution and has an eye on the reuse of components in future product generations. The development of the product is organized into system groups developing the major subsystems of the truck, such as engine, cab, chassis and electrical. Volvo also has feature teams that concentrate on a characteristic or feature that the customer can assess and consider in their purchasing decisions like fuel consumption or driver comfort. Features have a similar planning horizon to the system groups, but cut across aspects of multiple systems. Manufacturing gets involved after the conceptual design phase of a new generation of truck and follows the product until it goes out of production.
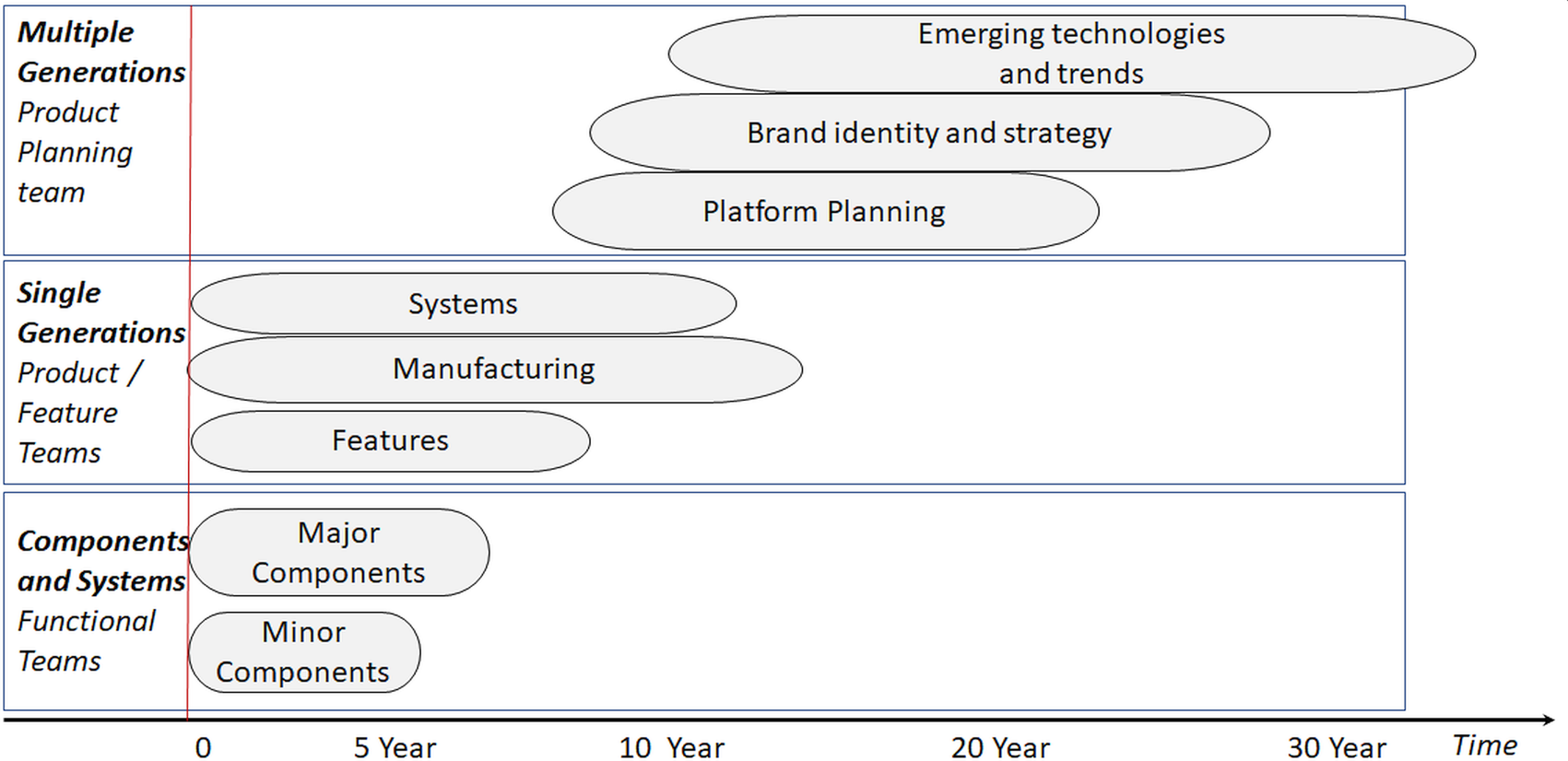
Figure 5. Focus, time scales and planning horizons for teams.
The individual components are designed as part the operation of the system teams. Components are refreshed at different rates. Some components are carried over between generations. Others keep their core functionality and adapted to meet the new product requirements often in response to changes in other components. For example, the cabin had had a major redesign in the previous generation and was only slightly updated in the current generation. New components or systems are designed from scratch if a new market demand is identified and become part of the standard offering. For example, E2 has been involved with designing a new suspension system which was used in trucks with high ground clearance. Some systems and components undergo major overhauls every few generations which are designed to incorporate expected future demands. For example, in this generation a new wiring harness was developed with currently redundant ports to cover use in the next generation.
4.3. Worst-case scenarios
Trucks are used in a wide range of conditions, for example most trucks for the European market run on smooth roads, but many trucks are also used to collect trees from forests, driving the majority of time over very rough surfaces. The worst-case scenarios bundle multiple extreme points into a concrete scenario, so that the designers can think about the interplay between the different factors. For example, a logging truck has to carry very heavy loads on the way to the saw mill over often very rough surfaces, which might be icy and snowy in the winter and muddy in summer, so that they need suspensions and brakes to meet these extreme conditions of use. They might also operate in areas, where they can only be refuelled in very few places and therefore might need large fuel tanks.
To minimize variety in the product platform, many components have traditionally been designed to withstand the greatest demands coming from worst-case scenarios, so that systems like the suspension are overdesigned for the majority of use cases, that is, as the truck operates under smooth road conditions.
Right now, we are checking with regard to adapting to a smooth condition to optimizing the product towards smooth conditions. (E8)
The truck is also operated under very different operating conditions ranging from sandy deserts to salty harbours and temperature ranges from –40 °C to +50 °C, so that many components need to be cooled, heated or insulated, even though they would not need this under most circumstances.
In many cases, the company uses distinct but differentiated worst scenarios for each of the types of truck applications which enable them to analyse the risks and requirements for these trucks. Besides being concrete and specific, worst-case scenarios also enable the designers to work with crisp values for the requirements rather than ranges that arise from the range of different uses (Paté-Cornell Reference Paté-Cornell1996). This is useful for calculating margins, because they can establish a clear split between the buffer and the excess with regards to the requirements of the worst-case scenario.
4.4. Features
Volvo manages product performance and product properties by what they call ‘features’, which cover all the elements of behaviour that distinguish products as seen from a user/customers perspective. The scope of the term has been extended to cover elements, not traditionally thought of as behaviour, which matter to the customers, such as safety or fuel efficiency. All together Volvo has 34 distinct features that they manage separately. Figure 6 shows an extract from the feature list.
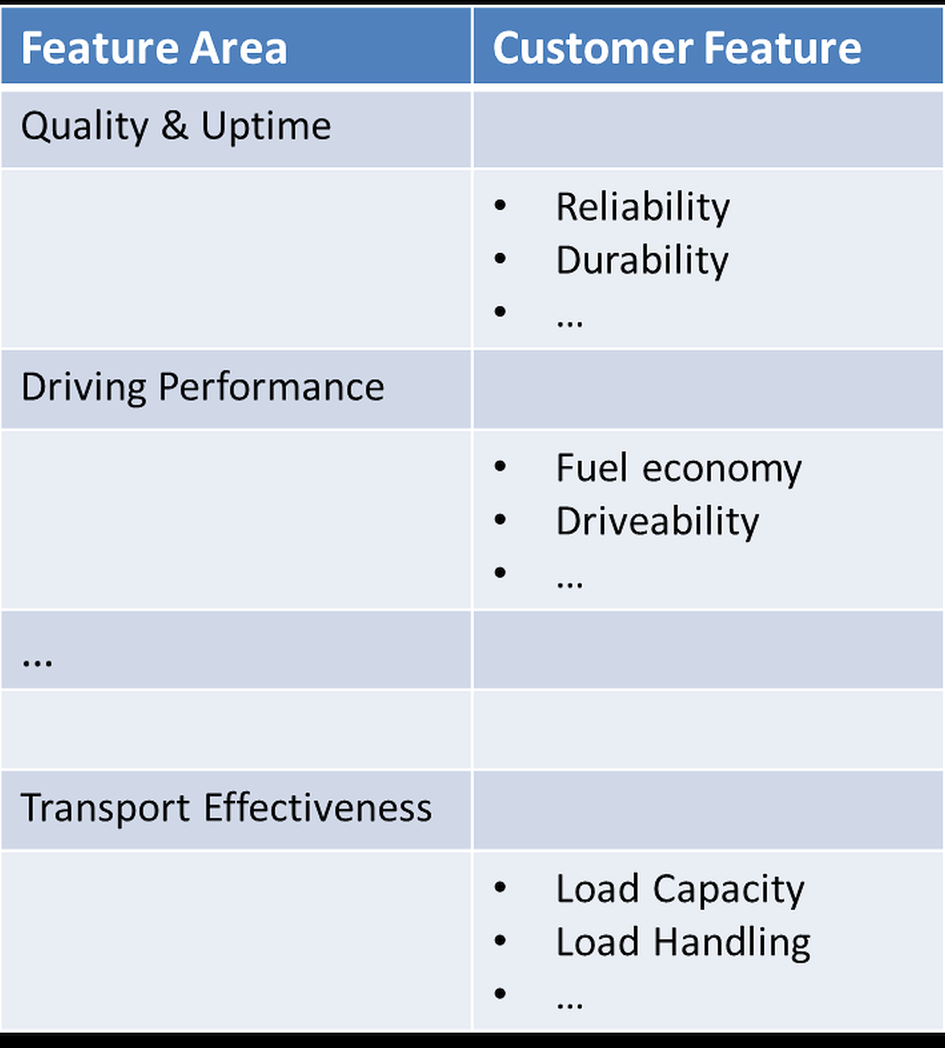
Figure 6. An extract of the feature structure used at Volvo.
Each feature is represented by a feature expert or a small feature team, which can engage in negotiation with each other. The features form a kind of orthogonal structure to a component view of the product as many features cut across different components thereby assuring effective component integration. Features are customer-focused and are set up to represent customer desires or wishes rather than reflecting technical trajectories. For example, the fuel efficiency feature expresses the customers’ wish to reduce their fuel consumption and has the role to assure that fuel consumption is minimized across the entire product such as the selection or detailed development of the engine, the aerodynamics and the weight of the truck. Meanwhile the engine development team works on reducing the fuel consumption of the engine through technical means. Features do not necessarily represent goals that the truck has to meet in absolute terms. Rather they are an articulation of customer driven design intent. Many of the features represent subjective properties of the truck, such as styling and human machine interface issues. These are difficult to quantify and need to be assessed subjectively by the experts as well as measured through instrumenting the truck during testing. The tests are carried out for several reasons (see Tahera et al. Reference Tahera, Wynn, Earl and Eckert2018) at different stages of the design process. The feature experts make sure that their features are tested as part of the testing programme, but physical testing is rarely instigated for specific features. The trucks are tested against both the worst-case scenarios and a number of common types of use scenario.
5. The range of margins concepts used in the case study company
Margins are considered by different groups in the organization, who use different terminology and are not necessarily aware of the margins other groups have added. Margins are added both to the requirements that are given to the designers and the design itself by the designers. This section discusses the terms used for margin concepts in the organization.
Please note that we stick with the terminology used in the company of ‘overdesign’ in the sense of overachieving on requirements. This includes parameters bigger than required, if bigger is better and also smaller than required if smaller is better.
Some properties of the product are difficult to quantify, in particular those associated with subjective product features, such as some aspects of driver comfort, which contributes to the requirements on the suspension system. These issues are dealt with specifically in the research on perceived quality (e.g., Stylidis et al. Reference Stylidis, Wickman and Söderberg2019), however in the case study. In these cases, the feature engineers, like E3, may set generous requirements to be sure a feature will be at an appropriate level, once the conflicting requirements on the components that contribute to the feature are met. These properties are a matter of scale, for which it can be difficult to set a precise threshold and therefore some of these properties are also difficult to test for objectively (see Eckert et al. Reference Isaksson, Lindroth and Eckert2014).
… it’s better to do a little bit of overdesign because who can give a guarantee to me what … people do in internal testing that this is sufficient. (E8)
In this section, we distinguish between margins on the requirements and margins on design, as illustrated in Figure 7, the argument follows roughly when the margins are added in the sequence of the development process, as explained in more detailed in Section 7.1.
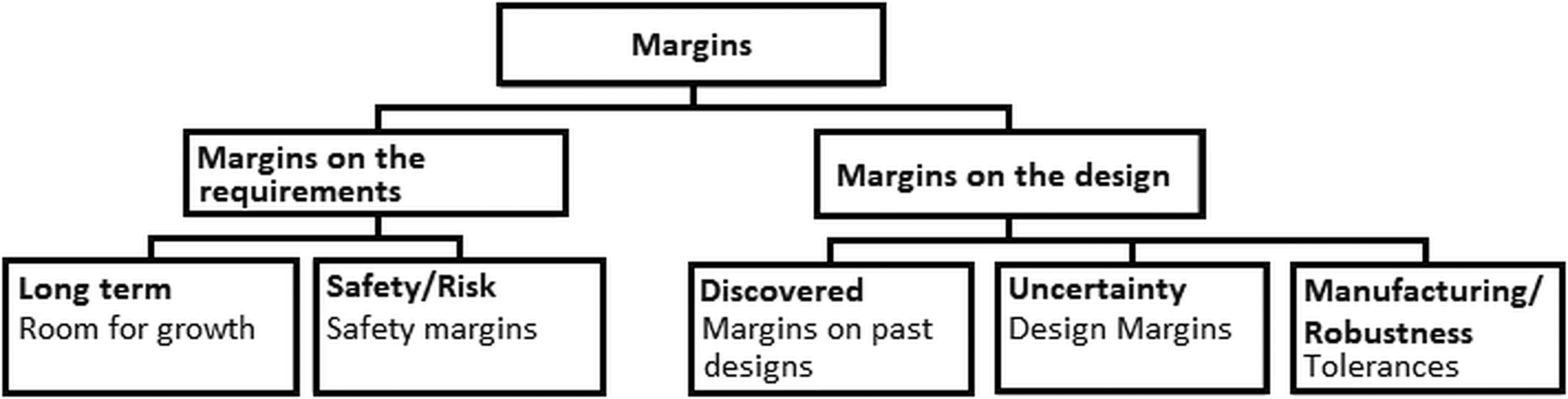
Figure 7. Margins on requirements and design margins.
5.1. Margins on requirements for the product
The company deals with two type of requirements, the long-term business requirements from the product planning team and the requirements for a particular product generation. The long-term planning team looks 20 or 30 years into the future with the aim to have a product ready when the evolving market requires them while not overloading any product generation with innovation and the resulting risk. The short-term requirements for a particular product generation addresses product requirements, such as specific safety issues associated with the intended use.
5.1.1. Room for future growth
The product planning team plans the major steps changes that take place between different generations of trucks, which can involve the introduction of significant innovations such the introduction of hybrid powertrain option. They focus on major systems, such as the cooling system or parts of the power train, which are common across the different brands. To manage the design effort, cost and risk, associated with innovation they plan a small number of major overhauls to systems in each generation. Some of these innovation steps are enforced by emission legislation, for example, the introduction of an after-treatment system was required by emission legislation. Each of these innovation steps requires changes to other systems to accommodate them. For example, the after-treatment is both large and heavy, so that other systems had to be moved or made smaller and lighter. As new technologies, such as new types of fuel or hybrid systems become available the company explores when and whether they can be introduced into their trucks. They estimate the demand on other system arising from these technologies and schedule the changes to these systems accordingly so that supporting systems can either already support the new technology or are upgraded in a way that will only require small changed in a future generation. For example, in the current generation a new wiring harness was introduced which at present only uses about 2/3 second of the available connection slots, knowing that these will be required for a future generation with new demands, such as the control of a hybrid system. This technology introduction road map enables the company to have technology at sufficient technology readiness levels (Mankins Reference Mankins1995) to introduce it in the required product generation. It also enables them to plan margins into systems that are designed to avoid unexpected major reworks on systems. This team speaks of ‘room for growth’ for future generation.
The team is also interested in the margins on solution principles, rather than margins on specific components and systems. They assess how long a particular technology can still be deployed to meet the needs that they are expecting. For example, they had specified the last major overall of the cooling system for the penultimate product generation with the assumption that it would last for several generations by minor adaptations to the some of the components.
5.1.2. Safety margins
Each product generation is designed to different requirements. The core requirements are set out at the beginning, but others evolve through the product development process. The requirements engineers add safety factors to the requirements to account for known or likely failure modes.
Trucks are very mature products and the company tends to know its customers and their intended product uses very well. However, they cannot control how the trucks are actually used or potentially misused.
I would still say that most likely there is 5% or 10% of the customers are maybe doing rare things with the truck that we cannot imagine internally. (E8)
Even if the product has been used highly inappropriately any damage or fault could still be a safety hazard and consequently affect brand reputation. For example, a truck is sold with a specific maximum load, but the company cannot stop customers from overloading the truck significantly. Therefore, the company plans in safety margins:
In one way it means that since you don’t know exactly how the truck will be used you need to consider a certain safety margin…, but what we mean is that in certain systems you need to be very sure that they don’t fail. (E11)
These safety margins are not apparent to the designers who are given prerequisites, as a target requirement against which they truck later is tested without a detailed explanation of the logic behind the values. At GKN, safety is typically associated with flight safety, and hence a central part for certification.
5.2. Types of overdesign in the product
Once the requirements for the product are collected and the product specification is written, the designers work on the detailed design. They add further margins to the components to enable them to respond to the requests for changes during the design process and the demands from new options. Further margins are added to the component to assure robust manufacturing.
In the interviews the engineers used the term safe with two meanings. First, the safety of the truck in use and second the design team being safe against changes to the component or system arising from other components. They therefore also added margins to the component requirements to protect them from future changes, which they also conceptualized as safety margins.
5.2.1. Discovered margins in past designs
The first step of designing a new component or system is understanding whether the existing system can in fact be used in the new design. Designers are under considerable pressure to make use of existing systems, to reduce development costs. They look for excess in the existing design that they can use to meet their new requirements.
In many design situations, the designers know they have to upgrade some systems but are discouraged from touching others. For example, the cooling pump, mounted in the engine block, is a long lead time cast component, which they want to keep constant. To increase its capacity, they might not need to change the geometry design of the pump, but can change the pumping speed (within working limits for the pump), provided there is enough margin in the cooling pump wall strength and associated joints and seals, to withstand the increased pressure. The designer will first try to change the pumping speed by changing the interface to the shaft (the drive pulley) to avoid touching the actual pump mechanism.
5.2.2. Design margins
Designers again add margins to their components, systems or features to avoid needing to change the component later in response to the emerging design of other components.
… The margin that they want to have a bit more extra than what they need…. Because this is question in the future which is something we need to trade. (E12)
They know from experience that due to the interdependency of a system the requirements on their components are often underestimated. For example, the load a casing needs to be able to carry might go up as the final weight of adjacent systems becomes clear.
you are more or less stupid if you don’t perform overdesign initially. (E1)
Margins cannot be seen in isolation. They are interlinked and can be traded off against each other throughout the design process. The designers can identify which components or systems they can change easily, or which still have large margins and use those to generate margin on a system or subsystem. Sometime designers will change or replace a component to provide more margins for the entire system, as in this suspension example:
[If] the vibrations get too much and then you can create some margin by introducing a softer rubber and you can do[this] for all or for a few [parts]. (E11)
Many component parameters are not defined directly by the product requirements but emerge throughout the process. Therefore, it is not sufficient to look at the margins on requirements stated in formal requirements documents. New parameters are defined throughout the product development process, which is constrained by many factors that themselves emerge, often these are also thought of as requirements. For this reason, a clear view of existing margins is needed at each stage of product development. Margins have to be addressed in a systematic way,
Designing margins into the product gives designers flexibility later in the design to meet different requirements in particular those deriving from new options that are added at a later point in the design process. However, designers can also generate this flexibility for themselves through the design decisions that they make. In the following example designers created slits instead of holes to cater for the different positions of a bracket arising in different options.
So if I give you another example … That bracket is positioned attached with only one hole … in that position you will see it sitting like this, and then sitting like that in another position. That height I think… have a valuation of … well I calculate lowers that… 32 different positions. … In height and in length wise as well. One bracket. (E2)
In this example, the designers generate a margin on the position of the screw, by designing the product in a way that gives them flexibility.
Design margins are sometimes also referred to as overdesign.
Yes, we overdesign but after the project start, we try to optimize the tubes for example …we can see that we have the possibility to down the size of the tubes to save cost (E13)
5.2.3. Clearances
Another case where margins are considered during the design phase of a product are clearances around components. Components are often designed with a space envelop associated with them. For example, the engine is allocated a space envelop that it can use if necessary. The space that is not used up then becomes a clearance. Clearances are very important in managing engineering change, because if clearances exist a component can be changed using up the clearance without the change propagating to other components. In this sense, clearances become a natural buffer for engineering change propagation.
As clearances are not entities, they are not explicitly described in a bill of materials but deduced from the CAD models of the system. Clearances often exist in-between different systems and therefore lie across design teams. This makes it difficult to negotiate over clearances as it is not clear who is planning to make use of which clearance. For example, when urea tanks in trucks were introduced as part of the new after treatment systems a space had to be found for them. For most versions, the urea tank fits easily on the chassis, but in some applications of very short trucks, another space was required. The designers therefore looked at space underneath the cab and above the muffler. Usually, there are no links between tanks and the cab design, and the tank designers were not aware that the cab team had also been looking at the same empty space for one of their applications.
To avoid being caught out late in the design process by changes required from other teams, teams often add margins to the space envelops of their systems thereby maybe unnecessarily increasing requested clearances.
5.2.4. Tolerances
One area where the company has been modelling surpluses for a long time, centre around manufacturing tolerances. Tolerance can be interpreted as the maximal allowable variation of a dimension and typically set as a manufacturing requirement on a product (component) to be produced. In a wider sense, design for robustness (Arvidsson & Gremyr, Reference Arvidsson and Gremyr2008) has developed multiple design approaches to deal with variation and make products insensible to noise factors. Most manufactured components have tolerances associated with them to allow for the variability in manufacturing. Today, advanced tools are used to model and simulate impact of tolerances in a geometry assurance process during design (Wärmefjord et al. Reference Wärmefjord, Söderberg, Lindkvist, Lindau and Carlson2017). Margins and tolerances are related, because if a component could be produced with tighter tolerances, some of the value that was used as a tolerance becomes a design margin that can be used for other purposes. On the other hand, if a component has no margin, the variation allowed by set tolerances become functionally critical. When discovering a lack of design margins, the set tolerances can be revisited to potentially release buffer and re-gain excess for the product.
For most components, the variability is a normal distribution and potential extreme points can cause problems. This has given rise to the widespread adoption of methods like 6 sigma, which assure controllable variability of the components and processes to within 6 sigma variation.
It’s a precision definition. That’s … why …we tend to wind up with products that has too large margins… And normally what then takes place is that then you have rationalization projects. (E1)
5.3. Discussion
The designers at the company were not themselves consistent in their use of terms. In particular, the design engineers referred to the design margins also as safety factors. This reflects that they add design margins to protect themselves from the risks of changes (both to design and requirements) occurring which could cause problems. As the designers allocate time against designing a specific component, changes that cannot be buffered, can push them into an unexpected rework cycle, which creates additional work for them and at worst could put the product schedule at risk. In addition, the requirements themselves are firming up during the design process and as safety issues depend on the design decisions made along the design process, the designers want to cover their responsibility for safety issue by adding margins.
6. Margins linking brands and platforms
Volvo GTT utilize product platform(s) with common architecture and shared technologies (CAST) across their different brands. Margins can therefore not only be considered as part of a one product but a network of interlinked products. As Isaksson et al. (Reference Isaksson, Lindroth and Eckert2014) point out using platform components can lead to very significant overdesign and therefore reduced product efficiency from the perspective of an individual product. Volvo like many OEM owns multiple brands which share a common product platform, so that some components are used in all Volvo products. Platforms based on a modular architecture, and development of such platforms is central to many manufactures (OEM’s) of complex products (Otto et al. Reference Otto, Hölttä-Otto, Simpson, Krause, Ripperda and Moon2016).
6.1. Margins and product platforms
The attitude to margins of the product platform team changes over the design process. At the beginning, margins are seen as a mean to reducing the numbers of elements in the platform thus reducing cost through volume, but later margins are a cost issue if it turns out that across the platform there are excesses in component capabilities.
The platform team also deals with the effect of change propagation on the platform. One way to do this is to model the dependencies between functionally organized design solutions (Claesson Reference Claesson2006) in a modular architecture and conduct change propagation analysis of the resulting design structure matrices (Raudberget et al. Reference Raudberget, Levandowski, Isaksson, Kipouros, Johannesson and Clarkson2015), which enable early design phase assessment of risk and robustness of product architectures. This leads to three types of components:
-
• optimized core components, that are shared widely across the product platform and are ideally protected from the impact of change propagation;
-
• overdesigned components, which can absorb the impact of change;
-
• proliferation components, where additional versions are added to the product platform.
For example, the engines are kept constant, but the company allows a platform proliferation on the engine mountings. In some cases, the platform team also needs to make a decision whether a new component is introduced into the platform and treated as a regular component. Components may be designed as special case solutions and then introduced into the whole platform of the next generation. In many cases the platform structures its components in several big increments to manage the modularity in the configuration.
simple rules, having a fuel tank which is always 100 mm longer than the one before and 100 mm shorter than the one after. (E4)
This can lead to overall suboptimal products. As illustrated in Isaksson et al. (Reference Isaksson, Lindroth and Eckert2014) it might well be possible to significantly increase the volume of the fuel tank, if all the margins and clearances were put together.
To develop components that support a modular architecture with increments, the company needs to be disciplined in designing compatible interfaces to are designed to stringent requirements. It is the often the margins at those interfaces, which enable configurable design.
Some components are used in a significant fraction of the products, because the economy of scale outweighs other concerns. For example, the company uses two sizes of cooling fans. The fans are bought in components with a complex geometry. The fan is part of the cooling system and is used to increase the airflow for cooling. The cooling system has tight geometrical constraints. It has the cab flooring on the top, on the sides of the chassis frame, the grille in the front, at the bottom the front underrun protection (FUP) and the engine in the back, as illustrated in Figure 8.
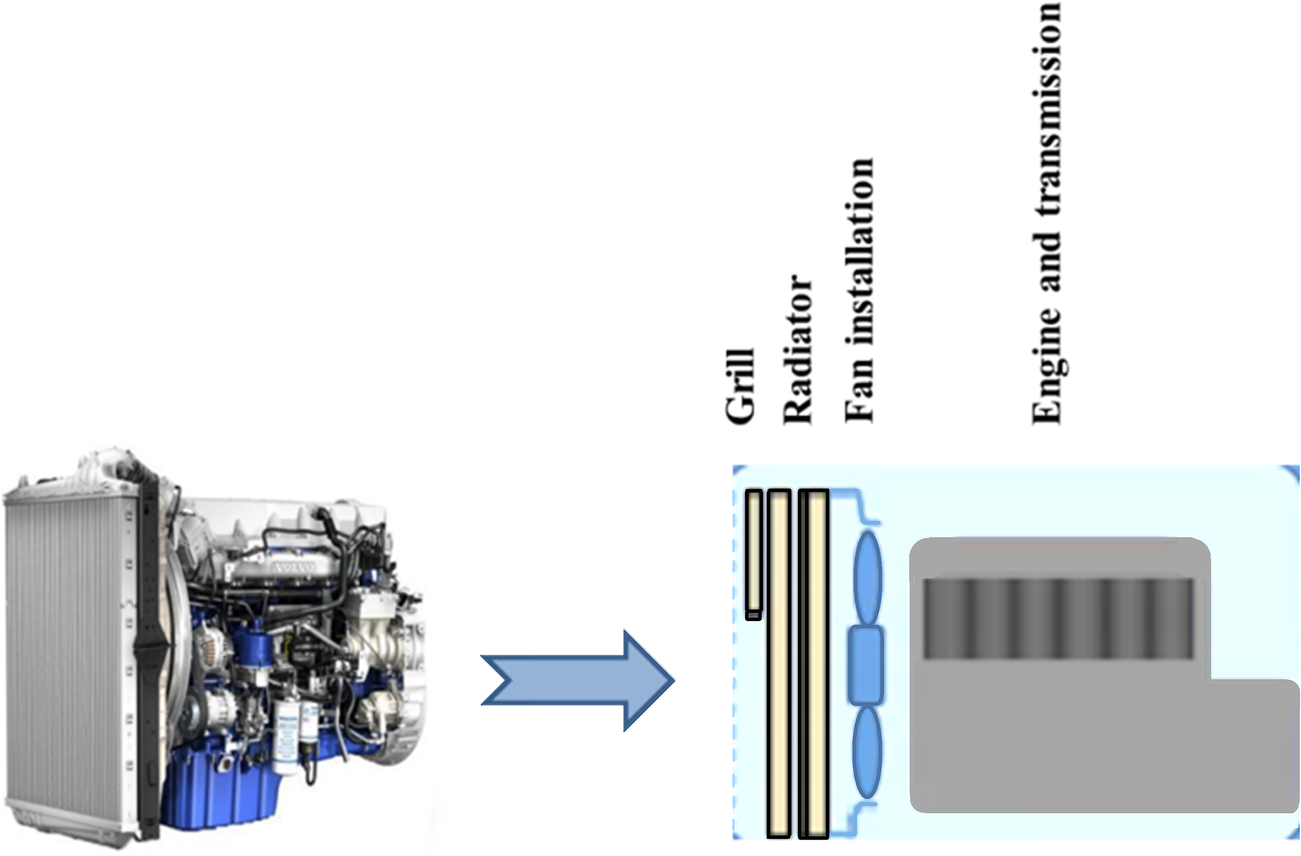
Figure 8. Cooling system layout.
Which fan is used in a particular product is based on calculating the airflow and pressure requirements of a system? In this selection, designers consider the worst-case scenario for fans, which can be far from the typical uses of a truck. For example, the same truck that is used in a temperate climate is also being sold to Africa and driven all day with a heavy load for hills in the blazing heat. Lebjioui, Eckert & Earl (Reference Lebjioui, Eckert and Earl2016) discuss an example where the required air flow would require a fan size of 63 cm, but the next suitable size of fan is 68 cm. A larger than necessary fan is heavier but increases efficiency, as does increased rotational speed. As a long lead time item, that requires considerable redesign, increasing the number of fans would not be economically viable. The increase in part cost would outweigh the increased running cost of. This example illustrates the close link between development cost and component cost.
The designers are aware where they have margins in their components that they can use to buffer against potential changes. For example, if a new engine would be offered for the same truck which requires lower operating temperature, the designers would know that their fan could accommodate this decrease in temperature, which might influence the selection of this engine. In this case the change can be absorbed by the margin in the airflow capacity.
6.2. Margins and brands
Many of the Volvo components are used across the multiple use applications and brands. Ideally, a component would be designed, so that it has a certain degree of margin with regards to both the intended use and the brand requirements. As components are designed to the worst-case scenarios of their most demanding applications, see Section 8, they might be overdesigned for all uses in a particular brand. For example, the fan discussed in the previous section is also deployed in other brands with generally lighter loads, which increased the level of overdesign. Therefore, all applications will have a margin on the fan. Unless margins can be represented and quantified, there remains a difficulty to assess implications for capital and operational costs following the margins allocated when used in the different brands.
At the beginning of the product development phase the engineers might not know which product in which brand the component needs to be designed for. Similarly, they might not know in which way the platform and the brands will be developed and how new brands are added to the product platform over the life cycle of the product. A product platform will be in existence for at least 10 years in which both markets and technical abilities will significantly develop. Currently technology is evolving rapidly and components are replaced ever more frequently, so that the product platforms evolve at an unprecedented speed and knowledge of margins will aid this process of renewal. This healthy tension between ensuring brand uniqueness and commonality of components is normal, see Otto et al. (Reference Otto, Hölttä-Otto, Simpson, Krause, Ripperda and Moon2016)
6.3. Discussion
The design of a platform part that is used in multiple applications needs to be meet the requirements of the most demanding application. This puts margins at the heart of some of the critical trade-off that companies have to make, as shown in Figure 9. The trade-off between product optimization and platform efficiency is fundamentally a margin trade-off, where the company needs to manage acceptable margins. Margins also enable different features to trade-off against each other. It controls the effort put into features, as some features that have been overdesigned in the previous generation do not need to be touched, except perhaps for optimization. Marketing of a new generation typically highlights the features which have considerable improvement.

Figure 9. Example of margins as facilitator of trade-offs.
Margins are also key to the trade-off between the product cost, that is, the cost to the company of producing a truck in terms of the cost of the components and their assembly and the cost of developing and operating the trucks. Margins enable the reuse of components or their adjustment with limited effort, whereas an optimized product is likely to require a significantly greater redesign effort and therefore development cost. However, overdesigned products, that is, those with margins are likely to be heavier needing more material and more fuel to run them and therefore have higher running costs. For overdesigned products there are also a trade-off between the material cost for additional materials and the cost saving from higher production volumes. Considering the high cost of tooling, production cost can be a significant driver for overdesign.
For each component the split between buffer and excess is different for each of the applications they are deployed in. From the perspective of a component, the useable excess is the amount that exceeds the buffer of all the possible applications. The excess for an entire brand or a significant part of a platform can be considerable.
7. Margins across the design process
Margins play an important role in all stages of the product development cycle, but the attitudes to margins are changing throughout the process. While margins at the beginning of the design process are largely seen as an opportunity to respond to new demands and changes, later in the design process margins are increasingly seen negatively as an overdesign which could incur cost in production or operation. However, the same margins are also an opportunity for the following product generation to meet its requirements.
This section follows the terminology used in Volvo and shows the notions of margin in the context in which they have been discussed in the interviews. Figure 10 shows the concepts in the context of the phase of the product development process in which they were discussed in the interviews and when they become most significant in the process. For example, tolerance is shown under production, but of course it is considered in a structured and systematic way during product development. The diagrams presented in this section have been validated with engineers at GKN, who design jet engine components, where a similar logic applies. The major difference would be in creating capability for future product generations. In jet engines this would be explored through design alternatives developed in parallel (see Eckert et al. Reference Eckert, Isaksson and Earl2019) rather than as room for growth designed into the present situation as for trucks.
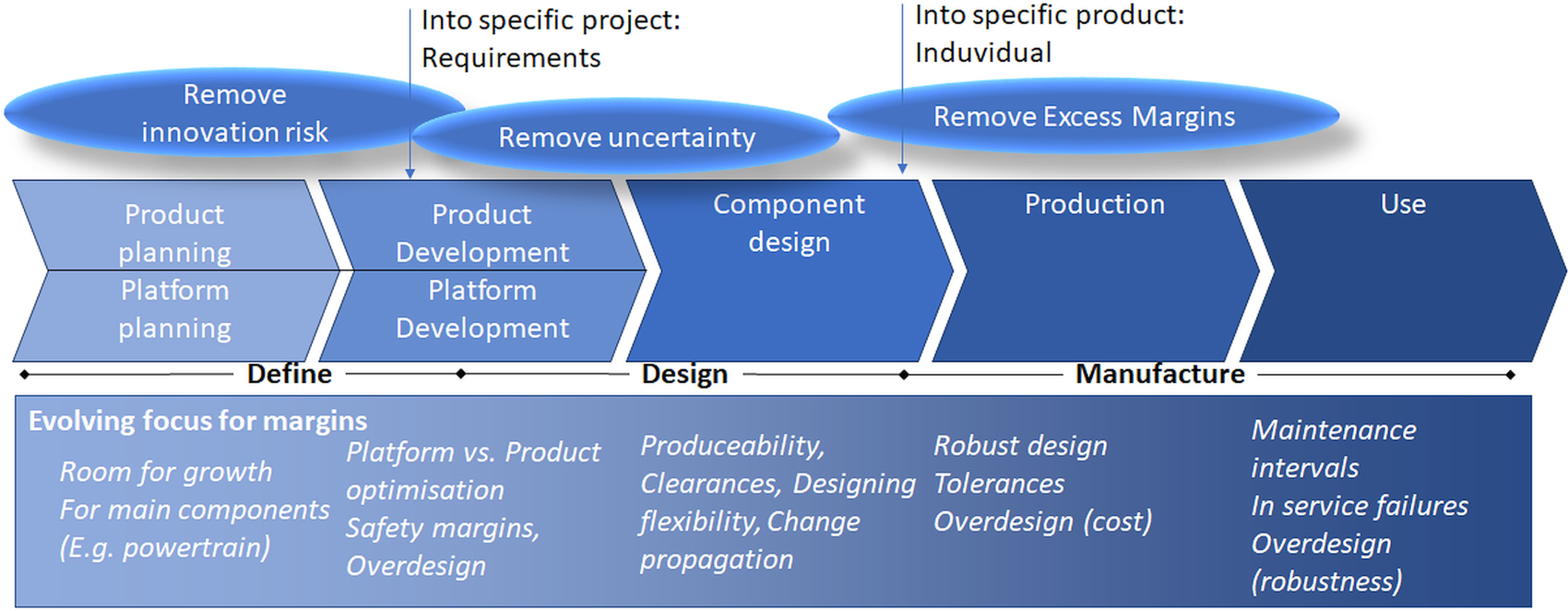
Figure 10. References to margins throughout the life cycle.
7.1. Changing terminology across the design process
Figure 10 follows a simplified model of the company’s development process. Product planning looks 20–30 years ahead and precedes any specific new product development. Similarly, platforms are planned decades ahead. Product development starts with the definitions of the requirements and the concept and moves to component design, but goes through cycles of convergent iteration (see Wynn & Eckert Reference Wynn and Eckert2017). It ends with component and system testing before the product enters production and finally use.
At the beginning of the product development processes, product planning and platform planning occur somewhat in parallel. In both cases, the companies are concerned with managing the long-term risk associated with the product. As innovation can potentially lead to risk, they want to manage the big innovation steps that the company takes and manage the introduction of new technology. For example, the company does not want to have a major redesign of the gearbox or the cooling system in every product generation. Therefore, they introduce room for growth. In the major redesign steps, components are designed with high margins to assure a long-life span and to cover a range of different use applications. For example, the company has two different sized cooling fans for all its application.
As the requirements for a new truck are firming up and the organization is moving into a component design phase, designers become very concerned with managing their own uncertainties. They need to respond to knock-on effects of other changes which are becoming apparent as their colleagues are developing their own solutions. Once the designers have produced a viable design, it then becomes a manufacturing specification. At this point, the emerging design is scrutinized from a cost perspective and the company aims to reduce margins for cost reasons.
During the component design phase, the designers must assure that not only all the components meet their requirements, but that the features they are part of also reach the required level. As explained in Section 11 features represent the properties of the truck that the customers can perceive and are willing to pay for. The goal of designers is for features is to meet these expectations, but not to exceed them.
I mean it’s to over deliver on features, but that is something that we don’t want. …
Margins can be seen as overdesign, that generates cost in the current product generation. Manufacturing engineers are not directly concerned with the features in the next generation, although they may be indirectly in developing manufacturing technologies and processes which will span product generations.
The feature team specify vehicle requirements and later receive results from vehicle tests. They do not explicitly know about margins of components and have no explicit concept of margins on features. However, as they are highly skilled and experienced experts, they often have a tacit understanding of the margins on their features. For example, the feature leader on truck handling specifies the handling characteristics and drives the test trucks to assess their handling. He knows what is required to improve truck handling and what trade-offs need to be made to achieve them.
This tacit knowledge of margins helps the features experts to negotiate these trade-offs informally in small groups, for example around the softness of the suspension. The feature margins are often the result of many different component margins and the same parameter can have large margins with regard to one feature and a small margin with regard to another. In the definition that Volvo uses for features, see Section 4.4, there is also no explicit ranking of the importance of the features. For many features there is a base quality level they need to reach, but beyond that, meeting feature requirements is a matter of degree and the right compromise needs to be found between different features of the overall successful product.
The feature experts and vehicle analysts work with groups of component engineers to understand where a particular feature could be improved. These discussions involve margins indirectly. The feature engineers where mainly interested in their own features and did not consider change propagation on other components arising from improving their own feature.
Once a satisfactory design has been generated, the design is scrutinized for product and production cost. The production engineers look for obvious points of overdesign, which could be taken out to reduce the component cost and make sure that the tolerances are appropriate. While previously margins are largely seen as a possible factor which enable the company to handle risk and uncertainty, margins are now seen as a cost factor. Margins are taken out at this point, which would significantly reduce the development cost of the next product generation.
In the use phase, margins are linked to failure. A component that has failed has not had enough design margin, one that never fails might be overdesigned. This information flags up to the designers in next product generation whether they want to use the component again and make use of the margins or maybe optimize the component. It also points to the link between margins and design for reliability, where safety margins or safety factors are often added at the beginning of the development process by those who set the requirements. Reliability engineering try to make sure that the product that has been designed and manufactured works in the given use contexts.
Overdesigning components or systems against some sets of requirements is also seen as a measure of assuring maximal product commonality across the product platform and therefore a way of reducing production cost; especially when the company acquires new brands and introduced them to the common platform. However, as the development process unfolds, the overdesign is seen progressively as a source of cost. The manufacturing engineers therefore look for components or systems that they consider overdesigned and target them to cut down the production cost of the current generation of products. Hence, the way overdesign is considered is different at each phase of the development process. At the beginning, the engineers think that overdesigning some components or systems can help them cope with the uncertainty and/or risk associated with the product development, whereas towards the end of the process, overdesign is seen as a source of cost that it is necessary to minimize.
7.2. Cumulative margins
Margins are added and used up throughout the entire design processes. While Figure 11 is not to scale it show how margins can potentially be accumulated throughout the design without other parties necessarily being aware of this occurring. This can result in a component or system being severely overdesigned, which adds cost and potentially affect other properties of the product, such as weight. Explicit overdesign occurs at two points (marked as a solid colour) as room for growth for future generations during the product definition phase and as overdesign that is, a buffer arising from changes in requirements or in other components during product development. Margins to requirements are marked in blue and margins on the design in orange/red.

Figure 11. Cumulative design margins.
Different margins are tracked in different ways. In Figure 11, the design margins are split into the buffer against expected uncertainties and the genuine excess on the components. The figure indicates that in spite of increasing requirements the overall margins can be reduced, as the uncertainty is also reduced. Once the produce goes into the service most of the remaining buffer (apart from that accounting for the extremes of use) also becomes excess.
The concepts discovered in Volvo do map to a certain extent to the concepts discussed in the literature in Section 2, even though the terminology is different.
A design process begins with looking for margins in the past design. While the concept of excess in Tackett et al. (Reference Tackett, Mattson and Ferguson2014) talked about the refurbishment of ships, where the excess appears to be a genuine discovery, the truck designers are largely aware about where to look for excess, even if they need to carry out specific analyses. Handling engineering change can also involve a certain amount of searching for excess that they might not have been aware of. For example, when they needed to fit a urea tank on a particular model where it was not possible to fit it next to the fuel tank, the engineers identified space under the cabin, which they would usually have thought of as under the responsibility of the truck team and fairly inaccessible. The production engineers also look for excess as they try to minimize the cost of the components for production. In some cases, the designers might not see this as excess, because they had kept it for a future generation or version. For them, the margins might be more like an option than excess.
The idea of room for growth applied by the product planners who take a view across production generations, is very similar to options. The product planners are concerned both about margin on components and system and also solution principles. A potentially dangerous point in any product development process is the sudden discovery that a totally new type of design is required. The product planners want to manage the innovation steps in the truck by assuring that many systems can either accommodate the new requirements or can be adapted in a fairly straight forward way, so that the teams can focus on innovations that add value to the organization. This makes room for growth essentially a strategic tool. There was little evidence that margins would be kept specifically for this strategic flexibility, rather than being included in the design margins engineers set.
Unlike the aerospace industry, the automotive industry does not prescribe statutory safety margins. The designers were aware that safety factors were included in the pre-requisites but did not have a clear picture how these had arisen. Therefore, some added more margins for extreme use cases. This also had the effect that the conceptual boundary between safety margins and design margins was blurred. Design margins were largely put in place to accommodate changes that arose during the design process, as requirements often go up. The company culture tries to accommodate changes rather than negotiate them. While bias in the sense of Austin-Breneman et al. (Reference Austin-Breneman, Yu and Yang2016) might well have been kept by some engineers, this did not come up in the interviews. However, this type of negotiation might well occur between the brands.
The company is becoming very interested in the idea of set based design, because of the obvious overlap between design sets and the affordances of product platforms. They are planning to use margins to look at product platform issues. However, at the time of the study they did not use design space or set based concepts.
The case study shows the relevance of the concepts in the literature to industrial practice (Table 3) but it also highlights how the literature is missing the cumulative effect of margins throughout the design process. As the rationale for margins is not captured in a central way, margins might be added multiple times, in particular with regards to safety or use concerns. The fact that potentially very large margins can accumulate in platform products over the development process is not raised in the literature. One reason for this accumulation is that margins and the rationale for them are not captured and communicated.
Table 3. Mapping of the margins concepts in Volvo to those identified in the literature
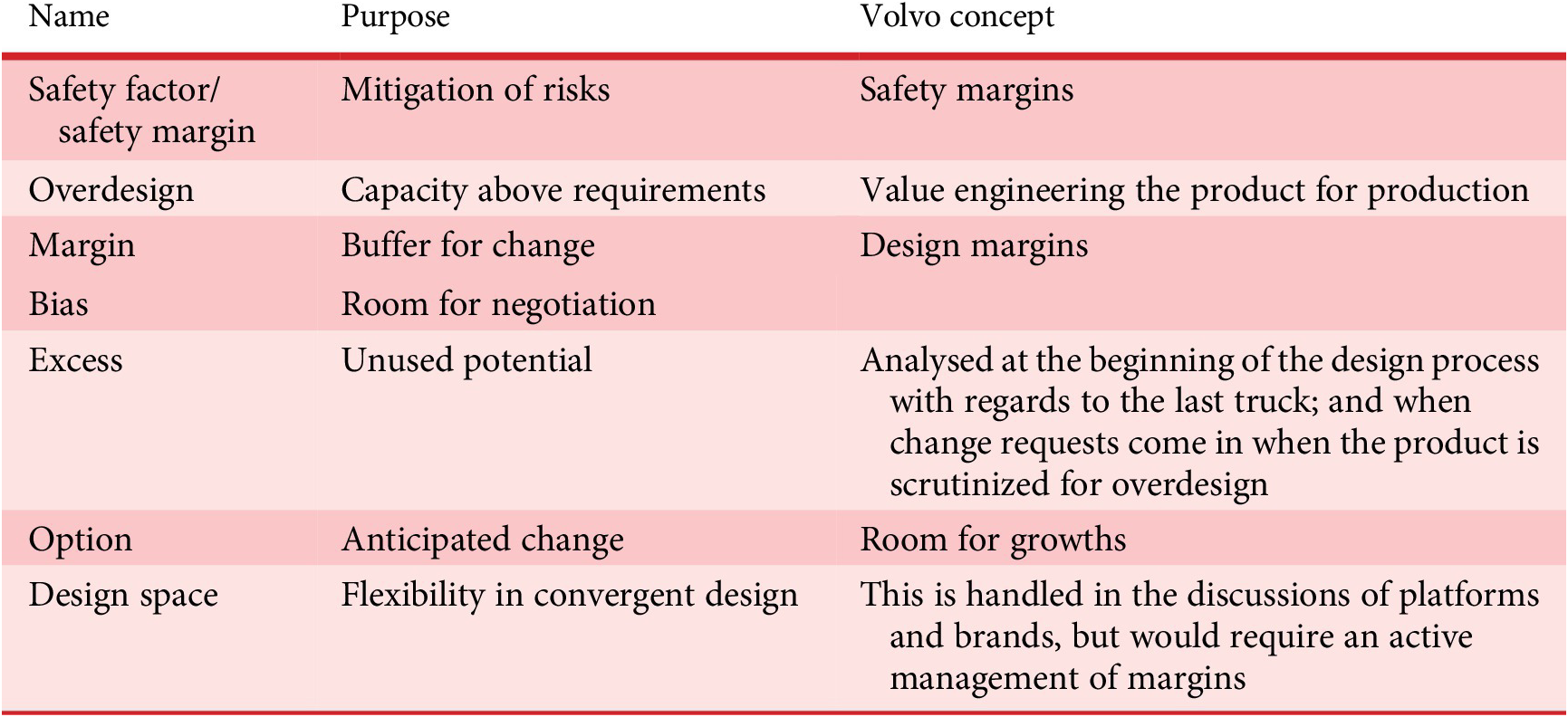
7.3. Distribution of the boundary around buffer and excess
In Eckert et al. (Reference Eckert, Isaksson and Earl2019), we argued that the division between the requirements and the buffer and the excess can be seen as a distribution depending on the uncertainties that the product is facing, that is, as a distribution of the requirements as shown by the red line. This is in line with other notions of margins as a means of managing uncertainty, as argued by Thunnissen (Reference Thunnissen2004).
The engineers in the company also place margins against uncertainties, however they have strategies to handle some of these uncertainties and make them explicit. The load on any component or system is uncertain through the variability of use cases. However, the company handled these through worst-case scenarios, as explained in Section 8. This enabled them to use a small number of crisp values rather than handling distributions and may more importantly gave them a logic of handling the interaction between different margins.
In designing a platform component, they needed to consider the worst-case scenario for the most demanding application and assure that this can be met. This gave them a single precise value to work to as a requirement to cover the distribution of potential use cases. For example, for cooling one of the worst-case scenarios is driving up the steady slop of the Sierra Nevada and they would need to specify a fan so that it would be sufficient cooling for the heaviest truck fully loaded. In some cases, they would add a safety factor to that as well and others they could trade this value off against other parameters such as component life before a recommended replacement or time before a recommended stop.
Figure 12 shows that the division between buffer and excess also can be seen as a distribution of the requirements placed by different applications and their relevant worst-case scenarios. Only a small number of applications will be at the extreme points, for example in cooling few trucks continuously drive up a mountain with a heavy load and few only ever drive light loads in a flat cold land. While the general excess of a component is against this extreme case, engineers are aware that the buffer might be much larger for other applications and make decisions accordingly, for example, taking very heavy load cases out of the product platform.

Figure 12. Distribution of buffer and excess.
When the designers need to identify excess, for example to handle an unexpected change, they look at the application to identify those that might be relevant and make a judgement whether they are affected. They can increase the excess by reducing the distribution of application.
8. Knowing margins
The different terminology around margins summarized for the case study in Figure 11 hides a common phenomenon and poses a challenge to managing margins efficiently. The knowledge about margins is localized and not captured systematically across the company.
8.1. Knowing and communicating margins
Generally, designers have a sense of the margins on the components they are responsible for. Rather than knowing an explicit value of margins they have a sense of whether their component would be able to absorb higher requirements or be changed easily without requiring major rework. However, this knowledge is usually not recorded explicitly. Margins are not communicated explicitly across the organization but become parts of the discourse in informal negotiations within the company. In the absence of a shared vocabulary for margin like concepts and commonly accepted formalizations of margins, expressing margins in a design process can be difficult.
Designers might also choose not to disclose margins, as they enable them to respond to new demands. When margins are eroded over time, the blame and with it potentially the cost might be passed on to the person or organization who requested the last change (Eckert et al. Reference Eckert, Clarkson and Zanker2004). Some critical margins are flagged up as part of concerns for the longevity of the product, in terms of stating that the current design narrowly managed to accommodate a requirement. This is not formal recording. In stable component teams, designers are likely to remember, but this information is lost in team changes. In Eckert et al. (Reference Isaksson, Lindroth and Eckert2014), we have argued that iteration across supply chain relationship is partially caused by different parties not disclosing the margins they keep for uncertain requirements and capabilities.
Large margins are less likely to be flagged up by the design engineers, who are protecting components with critical margins and are concerned about change propagation, as they do not pose a problem unless the product is investigated for value engineering. In the case study a dedicated team of engineers looked at the maturing design to identify value saving opportunity. They tried to identify large margins that they can take out, but they are interested in making the production of components cheaper and focussed on heavy parts.
As designers are often aware of the state of the margins of their own components, they often try to protect components with critical margin in the design process from changes. One way of doing this is by embedding the parameter values deeply in the sequence in which dependent decisions are being made, so that they parameters and their components cannot be changed without undoing a large part of the design process. For example, much of a product is designed around the harmonic frequencies, if these frequencies are changed most components would need to be altered, therefore values from which the harmonic frequencies are derived are usually not changed again.
8.2. Testing and margins
The testing process is designed to assure that a product meets the requirements. The company typically tests for an average case and several extreme points. Physical tests of complex products, such as trucks, are expensive and the company only puts a product to a physical test when they are fairly sure the product will pass the requirements. In some cases, the small margins are flagged up before test and confirmed by test or even emerge from the test process. Margins may be identified during test but rarely. Larger margins are not identified through the normal testing process. The company does not test a product to failure as they do not want to destroy their prototype equipment, apart from legally required tests such as crash tests.
This can be frustrating to the engineers as tests might not give much of a sense for some margins.
sometimes they know that and sometimes it’s sort of an unknown because we pass the test but we don’t know by how much we passed it. That’s a problem I think that it’s not always testing to failure. I always say that a successful component test always ends in complete failure. (E4)
Engineers can therefore be surprised, even if they had a broad sense of where the margins lie. This is in particular an issue for third party components. Suppliers test their components and guarantee that the components meet the requirements, but probably do not disclose margins even if they are aware of them as they might to be able to sell the same or a slightly altered product for the next generation. The supplied product might perform better than the supplier specifies because (i) additional performance is kept in reserve or (ii) they are unsure of the extra capability and do not want to overclaim.
we fulfil the requirement, we don’t have a problem and then…but then you don’t know where the borderline is …But test to fail then … know you really don’t if you have one percent margin or if you have 150% margin. (E8)
Vehicle analysis and simulation is increasingly used to evaluate and drive the design before any physical tests. Virtual models of systems and components are assembled into complete vehicle models for simulations in various operating environments. This makes it possible to identify margins, especially if they are explicitly requested. Vehicle analysis together with system and component analysis can be used to calculate, for example, fatigue life and thus get an indication where margins might be hidden.
It’s a bit different here. When we analyse we calculate what will the life be, so we analyse really until the end, until it breaks. Of course, it doesn’t matter for us, it takes just as long time. (E4)
Vehicle analysis has the potential to be an effective way to identify margins provided it becomes part of the official processes. In summary, a product needs to be physically tested to compliance and virtually tested to failure.
As the product is tested against the requirements that are specified any overdesign (against inflated requirements) included in the product definition phase, is not revealed later on. Later overdesign is also rarely quantified as products are typically tested to see whether they comply with the requirements rather than testing them see by how much they exceed the requirements. It is, however, increasingly becoming possible to use vehicle analysis to identify the likely life span of a component and therefore the amount that it is overdesigned compared to the design requirements.
8.3. Explicit management of margins
Some major systems are designed explicitly so that a system does not have to be redesigned in the next product generation. For example, the truck company recently redesigned their wiring harness and created a new harness with several unused ports in the expectation of needing them in a future product generation. In this example, the margins are clearly visible to everybody including the customers, as the additional cost is minimal for the current generation but with a clear advantage in the future.
Designers can take active design act steps to generate margins within a product. The obvious one is to overdesign a system or component and thereby generating an excess that can be used up in future changes. This does not mean that all parts of a system are overdesigned, rather than an engineer designs or redesigns specific components so that the overall system has a greater flexibility. For example, if a system is getting too heavy, it might be enough to redesign one component to make it substantially lighter to give the whole system a weight margin that they can use for future changes. Usually this can only be justified if there is an immediate benefit for the current system.
Since the study began ‘design margin’ is becoming common terminology in the organization used along the development project and actually throughout the life cycle process. As reported, the notion of design margin is not concise and evolves through along the process, but represents a rationale in that specific context at that time. As design decisions are made, products are defined and the rationale regarding the design margins use is often lost. What remains is the product definition (sizes, technology selections, etc.). As one feedback from Volvo participants, the short-term effect is that the insights in margins helped trigger the introduction of margins concepts in relation to the experience management system. It can be argued that a clearer conception of design margins gives product developers a useful tool to communicate through the process.
9. Discussion and conclusions
The existing literature on margins, see Section 2, concentrates on particular aspects of margins, whereas this paper provides a systematic view of margins across the entire product lifecycle. The empirical study has shown that margins are added to the product at various times throughout the process and designers may not be aware of the margins that other have added. However, it is possible that margins could be actively designed into a product and managed. As Section 7 shows margins are present for multiple purposes, but margins can also add significantly to the component costs as well as running cost of a product. Therefore, companies should optimize the margins themselves. This raised the question, how they can get the benefits of margins in terms of flexibility and ability to handle change without a large cost associated with specifying, tracking and managing margins.
9.1. Managing margins
Some major systems are designed explicitly so that a system does not have to be redesigned in the next product generation. For example, the trucks recently redesigned their wiring harness and created a new harness with several unused ports in the expectation of needing them in a future product generation. In this example, partly because they are expressed discretely as unused ports, the margins are clearly visible to everybody including the customers. The additional cost is minimal for the current generation but demonstrates a clear advantage subsequently. Although these margins do not significantly increase the component costs, they do increase the piece number in the product platform, and probably the running cost of the product in terms of weight, for example.
Designers can take active design steps to generate margins within a product. The obvious path is to overdesign a system or component and thereby generate an excess that can be used up in future changes. This does not mean that all parts of a system are overdesigned, rather that designer focusses on the design or redesign of specific components so that the overall system has a greater flexibility. For example, if a system is getting too heavy, if might be enough to redesign one component to make it lighter to a give the whole system a weight margin that can be used for future changes. Usually, this can only be justified if there is an immediate benefit for the current design.
Sometimes the design itself can be flexible so that it can be used in different contexts without requiring a change. A simple example is that the designers designed some fixing where screws where screwed into slides rather can holes, so that they could be moved around without needing to add additional holes. Similar decisions can be taken about far more complex components. In fact, some of the motivation between a move from hardware to software comes from a need for increased flexibility.
9.2. Conclusions and further work
This paper argues that margins play an important role throughout the entire design process; however, it is not recognized as a unified concept which is clearly communicated and tracked throughout the design process. Rather different stakeholders have different notions of margins and do not disclose the rationale behind adding margins or the amount that they have added. This can lead to products which are more costly to produce than is necessary. However, margins also enable designers to avoid design changes as existing components and systems can accommodate new requirements and thereby saving significant design time. Margins are at the heart of a trade-off between product and process cost. With traditional testing it has been difficult to establish the values of margins as few tests are carried out to destruction, but the increased vehicle analysis simulation capability now available makes it possible to establish the values of margins at different stages of the design process.
The empirical findings clearly demonstrate that a notion of margins is used in practice, but also that the loose and highly context-dependent use of margins as a label is a source of suboptimal design and often overdesign. We have shown how the assigning of margins is built into the evolving design throughout the development process, which can be difficult to untangle at a later stage.
Margins are a combination of buffers built into a design to cater for uncertainty and excess which is a genuine surplus in a component, system or design. While different notions of margins favour one or other aspects, it becomes clear that both aspects have to be examined together. As the excess part of a margin provides design flexibility, designers can try to reduce uncertainty, for example by reducing the variability in use, to move parts of the buffer element of the margin into a useable excess.
In future work, we are looking more closely at the design process of specific components to understand exactly how margins, and the designers understanding of these margins, has shaped the design process. Understanding margins is the key to carrying out engineering change processes efficiently. The concept of margin can therefore inform more accurate change prediction.
The systematic capture of margins has huge potential benefits, but also bring significant effort and costs. To quantify margins, it is necessary to track requirements systematically, which is often not done in a systematic and joined up way. In an ideal world, tracking margins becomes an integral part of the testing and validation process, so that rather than checking requirements compliance the actual margins are established through simulations and recorded. A simpler process would allow designers to flag up critical margins in a CAD or PLM system to remind themselves and alert colleagues of potential problems with margins. Doing this, the designer should see an instant reward in better decision making and trust in dealing with margins rather than overloading them with a burden of extra work.