Introduction
Weeds pose the highest potential for yield loss of all crop pests, constituting a significant threat to food security and agricultural productivity among key food (wheat [Triticum aestivum L.], soybean [Glycine max (L.) Merr.], and rice [Oryza sativa L.]) and fiber (cotton [Gossypium hirsutum L.]) crops (Oerke Reference Oerke2006). Effective weed control is essential for viable crop production, with herbicides the primary weed control technology used. The many advantages of herbicides over other weed control technologies (high efficacy, selectivity, low cost, etc.) has led to reliance on this form of weed control in cropping systems. A consequence of this is the widespread evolution of herbicide-resistant weed populations throughout the world’s cropping regions (Heap Reference Heap2019). The loss of herbicide use due to resistance is compounded by the lack of new herbicide development and regulatory removal of existing chemistries. With fewer herbicide options available now and into the foreseeable future, effective weed control in cropping systems will be reliant on the introduction of highly effective alternative weed control technologies.
Adoption of new weed control technologies requires evidence of high efficacy, reliability, and demonstrated economic suitability for routine use within cropping systems. Conservation crop production systems based on reduced tillage and residue retention have many demonstrated advantages (Dumanski Reference Dumanski2015; Kassam et al. Reference Kassam, Friedrich, Derpsch, Lahmar, Mrabet, Basch, GonzÆlez-SÆnchez and Serraj2012; Mitchell et al. Reference Mitchell, Shrestha, Mathesius, Scow, Southard, Haney, Schmidt, Munk and Horwath2017). Herbicides have played a key role in the success of these cropping systems, providing effective weed control without interfering with the fundamental principles of conservation (D’Emden et al. Reference D’Emden, Llewellyn and Burton2008; Llewellyn et al. Reference Llewellyn, D’Emden and Kuehne2012). The reliance on herbicidal weed control in these systems has been driven not only by herbicidal efficacy, but also by the lack of suitable alternatives. At present, herbicides are the only option that provide highly effective, flexible, and economical weed control for conservation cropping system. Routinely used options complementing the use of herbicides in integrated management programs include harvest weed seed control (Walsh and Powles Reference Walsh and Powles2014) and crop competition (Chauhan et al. Reference Chauhan, Singh and Mahajan2012). These options can impact weed populations, yet individually do not provide the same level of immediate weed control as herbicides. Thus, the need remains for suitable alternative weed control treatments for routine use in cropping systems.
Rapid developments in sensing, vision, and computational efficiencies associated with the automobile, security, and defense industries, are generating new weed control possibilities. These technologies create the opportunity for site-specific weed management (SSWM) in large-scale crop production, through the detection of individual weeds followed by the rapid, accurate delivery of the control option (Bakker et al. Reference Bakker, Asselt, Bontsema, Müller and Straten2010). Accurate detection and subsequent point-specific targeting of weeds enables the use of nonselective alternative weed control technologies for selective in-crop weed control (Fernández-Quintanilla et al. Reference Fernández-Quintanilla, Peæa, Andœjar, Dorado, Ribeiro and López-Granados2018; Wiles Reference Wiles2009; Yang et al. Reference Yang, Prasher, Landry and Ramaswamy2003).
Given the diverse array of alternative mechanical and thermal weed control options available, the challenge is to identify appropriate weed control systems for use in large-scale cropping systems. While inputs and methods differ significantly between control options, all share an associated energy requirement for activation and use. Furthermore, accounting for energy consumption enables an improved understanding of weed control efficiency with respect to emissions and climate change. This shared energy requirement provides an opportunity to measure weed control efficacy per unit of energy consumed, enabling comparison across the comprehensive and diverse range of alternative weed control techniques. Energy consumption, therefore, provides an indication of weed control cost when the comparison is made using similar energy sources.
An energy use−based approach requires a holistic comparison, inclusive of key areas of energy consumption. The comparison presented here includes energy involved in the production of the required consumable (e.g., herbicide, grit, or steel) and in the application of the consumable. The aim of this review, then, was to compare current and alternative mechanical and thermal weed control methods based on the energy used in controlling weeds when used as broadcast or site- and point-specific treatments.
Framework for the Calculation of Energy Estimates
Energy requirements have been calculated within key parameters and assumptions for weed growth stage and density for both broadcast and SSWM control methods, allowing the fair comparison of weed control treatments.
Estimated energy consumption was calculated on a per hectare basis with an assumed weed density of 5 plants m−2. This value was chosen to represent a typical weed density in Australian grain fields from a survey of Australian grain growers (Llewellyn et al. Reference Llewellyn, Ronning, Clarke, Mayfield, Walker and Ouzman2016). Average weed density was reported to be 1 to 10 plants m−2 by 40% of growers. Given the indiscriminate nature of broadcast weed control, the energy requirements are assumed to be insensitive to changes in weed density. The energy cost associated with site-specific treatment is directly proportional to the number of weeds present. Hence, a doubling of weed density will result in an approximate doubling of energy required per hectare, accounting for fixed, time-reliant energy consumption in power generation, weed detection, and computation. All energy estimates are based on either published or calculated values required for the control of 2-leaf-stage broadleaf weeds.
Accounting for the considerable variability in working widths of weed control technologies, energy requirements have been scaled up or down (depending on the implement or system) to allow comparison at a designated working width of 1 m. While implement width influences tractor size, the draft force per meter of implement, and thus energy consumption, remains the same. Working width also has a linear relationship with draft force for calculation of tillage energy use and is mathematically independent of the distance implements are dragged per hectare. Thermal and mulching control methods involve quantity of consumables used per hectare, while site-specific calculations use energy consumed per weed multiplied by weed density, both of which are independent of working width. Field efficiency factors, which include situation-dependent parameters such as field shape, operator skill, losses when maneuvering equipment, and soil conditions (American Society for Agricultural Engineers 2000), were not included in energy estimates.
While the additional energy consumption associated with wear of tillage components has been included, it is assumed that weed control efficacy and power draw remain constant and are not adversely impacted by increasing implement wear over time. Other shared requirements such as monetary cost and labor are additional factors influencing research and adoption of weed control options; however, these costs are highly inconsistent between regions and have not been included in estimates. An energy-focused approach enables the translation and scaling of results for consistent application globally, and if similar energy sources are used, will help inform labor and monetary cost estimates based on local expertise.
Assumptions relating to the calculation of specific energy components are described in the relevant sections below.
Energy Estimation Methods
The total energy (E total) associated with each weeding technique was calculated as the sum of energy directly (E direct) applied for weeding purposes and energy indirectly (E indirect) applied to carry equipment and consumables across the field (Equation 1):

The direct energy requirement was defined as the energy applied to perform the actual weeding treatment. For mechanical methods, the source of energy is a combination of energy expended due to draft force (E draft) and via the power takeoff (PTO) (E PTO). For thermal methods, the energy source is either electrical (E elec) or chemical (E chem). The total direct energy is a sum of the energy applied from all sources (Equation 2):

Draft force was estimated using Equation 3 (American Society for Agricultural Engineers 2000):

where D is the draft force in newtons; F is a dimensionless soil parameter based on whether the soil is of fine, medium, or coarse texture (assumed to be medium texture); A, B, and C are machine-specific parameters; S is the working speed (km h−1); W is the width of the equipment (m); and T is the tillage depth (cm). Values for soil and machine-specific parameters were based on those reported in American Society for Agricultural Engineers (2000), while speed and tillage depth were estimated from the literature or commercial specifications. The calculation of energy expenditure per hectare from draft force involved multiplying draft force by the distance the implement was dragged per hectare.
PTO energy (E PTO) applies to mechanical equipment requiring PTO power (Equation 4):

where P PTO is the PTO power required (watts), T is the torque required to rotate the implement (Nm), and ω is the rotation rate of the implement (rad s−1). A torque range of 22 to 50 Nm was applied for all rotated equipment, based on a rotary tiller tested on silt loam soil and sandy soil (Hirasawa et al. Reference Hirasawa, Kataoka and Kubo2013). The rotation rate was taken from the relevant literature or commercial equipment specifications. The time required to cover 1 ha was estimated based on working speed and equipment width in Australian conditions. This was multiplied by the power requirement to estimate the energy consumption per hectare.
Several studies have identified the electrical energy (E elec) requirements for weed control, and where energy conversion was required, the energy requirement was divided by the system efficiency to calculate the input energy required. Chemical energy contained within the fuel consumed (E chem) was estimated by multiplying the appropriate heat of combustion values by the mass of fuel used. The values applied for heat of combustion were: 50 MJ kg−1, 45 MJ kg−1, and 46 MJ kg−1 for propane, diesel, and kerosene, respectively. Respective density values used when necessary were 580 kg m−3, 832 kg m−3, and 810 kg m−3.
The indirect energy (E indirect) is the sum of energy required to move consumables and equipment around the field (Equation 5):

Calculation of indirect energy was based on the rolling resistance, where the rolling resistance force is the product of weight and the rolling resistance coefficient μ (Equation 6):

where g is acceleration due to gravity, and m cons and m equip are the total mass of consumables and equipment, respectively. The coefficient μ was taken to be 0.12 based on a study by McAllister (Reference McAllister1983), which reported that in average conditions, the coefficient of rolling resistance for rubber tires on soil ranged from 0.077 to 0.153. The mass of the consumable required per hectare was either estimated or taken from the relevant literature. Four trips were assumed per hectare to refill the consumable, acknowledging variability in practice. Refilling frequency was selected to limit the maximum load to a reasonable level of several tonnes for broadcast methods and several hundred kilograms for site-specific methods. Thus, the maximum mass of each consumable carried was a quarter of the per-hectare requirement. It was assumed that the mass of the consumable declined steadily, so that the average amount carried was half the maximum amount. Therefore, mass was taken to be one-eighth of the per-hectare requirement. Energy expended to refill the consumable was not considered, nor was the distance to refilling stations.
Energy intrinsic in the non-reusable consumable, such as herbicide, plastic, and steel on wearing cultivator surfaces was incorporated as an indirect energy requirement. Energy required for production of the implement was not considered. In targeted-control methods the energy associated with moving sensor and actuator mass and positioning the end effector was not included. This approach was taken because the weight of the sensors needed to perform weed detection and targeting is small compared with the entire system. The exceptions are cases in which a system would require a component (such as a pump, compressor, or transformer) deemed sufficiently heavy to significantly alter energy consumption. Energy involved in data acquisition and processing for weed recognition and weed control delivery is assumed to be equivalent across all SSWM treatments and was calculated on total power consumed over 1 h of operation and included as a constant value in all targeted approaches.
This paper presents standardized energy consumption levels to capture the diversity of control options available for various crop and weed development environments. While limited by these assumptions, it presents an opportunity to compare efficiency on an energy basis where other comparisons would not provide similar fairness of comparison. The comparison provides a basis for cost comparison of alternative methods, given similar sources of energy.
Energy Consumption Estimates
Broadcast Weed Control Treatments
Thermal Weed Control
Thermal weed control options are those that heat or freeze weeds, resulting in cell rupture and plant death. Treatments include ultraviolet light, infrared heating, flaming, hot water, hot foam, hot air, steam, freezing, and microwaves, presented in order of increasing energy consumption (Table 1).
Table 1. Summary of energy estimates for thermal weed control methods.

a Ninety five percent reduction in biomass.
b Estimate.
c Based on two-row flame weeder (Agricultural Flaming Innovations 2012).
d Weeds were controlled at the 2-leaf stage of fodder beet (Beta vulgaris L.). No weed growth stage was provided.
e Assumed similar to SW900 steam weeder (Weedtechnics 2006).
f DAS, days after sowing; no information provided on growth stage.
g Assuming similar water consumption to hot-water weeding.
h Estimated from Cutulle et al. (Reference Cutulle, Armel, Brosnan, Kopsell, Hart, Vargas, Gibson, Messer, McLemore and Duncan2013).
Within the spectrum of UV light, plants are most sensitive to UV-B (280 to 315 nm) wavelengths, whereby damage occurs due to heating of plant tissue (Andreasen et al. Reference Andreasen, Hansen and Streibig1999). Using a 2.35-kW UV lamp, Andreasen et al. (Reference Andreasen, Hansen and Streibig1999) found 2-leaf burning nettle (Urtica urens L.) required 0.6 to 1.0 GJ ha−1 for a 95% reduction in biomass, while 4-leaf-stage annual bluegrass (Poa annua L.) required 6 to 10 GJ ha−1, and common groundsel (Senecio vulgaris L.) required 13 to 100 GJ ha−1. Highlighting variability and the potential influence of species on this approach, the control of 12-leaf-stage shepherd’s-purse [Capsella bursa-pastoris (L.) Medik] required 1.7 GJ ha−1. Based on the assumption of broadleaf weed control at the 2-leaf stage, the energy requirement for UV weed control was estimated between 0.6 to 1.0 GJ ha−1.
IR weeders use hot ceramic or metal plates heated with propane burners to radiate heat energy (Rifai et al. Reference Rifai, Miller, Gaduš, Otepka and Košik2003); several studies investigating the energy requirements of IR weeding have found reduced energy efficiency compared with flame weeding (Ascard Reference Ascard1998; Parish Reference Parish1990; Rask and Kristoffersen Reference Rask and Kristoffersen2007) (Table 1). At the 6-leaf stage or lower, Astatkie et al. (Reference Astatkie, Rifai, Havard, Adsett, Lacko-Bartosova and Otepka2007) found that an energy dosage of 3,887 MJ ha−1 provided 100% control of redroot pigweed (Amaranthus retroflexus L.), ladysthumb (Persicaria maculosa Gray), and white mustard (Sinapis alba L.); however, only 64% of common lambsquarters (Chenopodium album L.) plants were controlled, highlighting varying species response. In contrast, a study by Ascard (Reference Ascard1998) found that energy consumption of IR weeders was similar to flame weeding, with a propane consumption of 61 kg ha−1 (3,074 MJ ha−1) to control white mustard at the 2-leaf stage. Parish (Reference Parish1989) reported that an energy of 2,000 to 4,000 MJ ha−1 was required to severely inhibit the growth of white mustard and ryegrass species (Lolium spp.), respectively (Table 1). These values suggest a control range of 2,000 to 3,887 MJ ha−1.
Flame weeding involves the use of propane burners to create intense heat (both radiative and convective) to control weeds in the interrow region of row crops or across the whole field in fallow situations (Ascard Reference Ascard1994). Covers, or reflectors, to contain the heat energy close to targeted weeds improve energy efficiency by reducing heat loss (Figure 1); however, flame weeding still has relatively high fuel consumption (Rask and Kristoffersen Reference Rask and Kristoffersen2007). The efficacy of flame weeding is highly dependent on weed species and regrowth capacity following flaming (Knezevic et al. Reference Knezevic, Stepanovic and Datta2014; Sivesind et al. Reference Sivesind, Leblanc, Cloutier, Seguin and Stewart2009; Vester Reference Vester1985). There is a 2- to 3-fold increase in energy consumed for the control of grass species (Table 1). However, for 2- to 6-leaf-stage broadleaf weeds, including common lambsquarters (Ascard Reference Ascard1995a; Astatkie et al. Reference Astatkie, Rifai, Havard, Adsett, Lacko-Bartosova and Otepka2007; Rasmussen Reference Rasmussen2003), redroot pigweed (Astatkie et al. Reference Astatkie, Rifai, Havard, Adsett, Lacko-Bartosova and Otepka2007; Knezevic and Ulloa Reference Knezevic and Ulloa2007), white mustard (Ascard Reference Ascard1994; Astatkie et al. Reference Astatkie, Rifai, Havard, Adsett, Lacko-Bartosova and Otepka2007), velvetleaf (Abutilon theophrasti Medik.) (Knezevic and Ulloa Reference Knezevic and Ulloa2007; Ulloa et al. Reference Ulloa, Datta and Knezevic2010), and pineapple-weed (Matricaria discoidea DC.) (Ascard Reference Ascard1994; Ascard Reference Ascard1995a; Ulloa et al. Reference Ulloa, Datta and Knezevic2010), propane consumption varied between 20 and 86 kg ha−1. Based on these propane usage patterns, estimates of 1,008 to 4,334 MJ ha−1 were calculated for effective weed control of 2-leaf-stage broadleaf species (Table 1).

Figure 1. Interrow (left; source Stepanovic [Reference Stepanovic2013]) and broadcast (right; source KULT[2018]) flame weeders in use on early POST maize and PRE vegetable beds, respectively.
Hot-water weeding relies on the storage of heat energy in water (de Cauwer et al. Reference de Cauwer, Bogaert, Claerhout, Bulcke and Reheul2015; Hansson and Mattsson Reference Hansson and Mattsson2003), demonstrating plant damage responses similar to those produced by flame and IR weeding. Efficacy studies have shown that single treatments can control annual and young perennial weeds, while more mature perennial weeds require multiple treatments (Daar Reference Daar1994; Hansson and Mattsson Reference Hansson and Mattsson2003; Rask and Kristoffersen Reference Rask and Kristoffersen2007). Hansson and Ascard (Reference Hansson and Ascard2002) calculated that approximately 10,000 L of water was needed for 90% control of 2-leaf-stage white mustard. There were significant differences between weed species in response to hot-water treatments. While the ED50 (the dose required to result in a 50% reduction in weed biomass) for 39-d-old horseweed (Erigeron canadensis L.) and dandelion (Taraxacum officinale F. H. Wigg.) was 1,500 MJ ha−1 (water temperature of 98 C), the ED50 for similarly aged perennial ryegrass (Lolium perenne L.) and annual bluegrass was 2- and 5-fold higher, respectively (de Cauwer et al. Reference de Cauwer, Bogaert, Claerhout, Bulcke and Reheul2015). These studies suggest an energy consumption range of 1,500 to 3,970 MJ ha−1 for variable control in broadleaf species, with an additional requirement of 10,000 L ha−1 of water (Table 1).
Thermodynamic principles suggest the efficiency of hot-water weeding systems may be improved with the inclusion of a foaming agent acting as an insulator, prolonging the contact period of hot-water with weeds (James et al. Reference James, Reid and Tindall2009). Kempenaar and Spijker (Reference Kempenaar and Spijker2004) found that the addition of foam increased the effectiveness of a hot-water treatment by 50% to 60%. Experiments by Kristoffersen et al. (Reference Kristoffersen, Rask and Larsen2008) used a dosage of 163 kg ha−1 of propane (8,220 MJ ha−1) to treat or control mixed species of young broadleaf weeds on traffic islands using a hot water with foam system (Table 1).
Steam weeding is more efficient at transferring heat energy than hot-water treatments, with steam containing more energy per unit mass than water, a higher rate of heat transfer than air, higher heating temperatures than water, and an ability to condense onto plants (Kerpauskas et al. Reference Kerpauskas, Sirvydas, Lazauskas, Vasinauskiene and Tamosiunas2006). Kolberg and Wiles (Reference Kolberg and Wiles2002) found that the energy for heating 3,200 L ha−1 was 8,900 MJ ha−1, and this treatment provided 100% control of 2-leaf-stage common lambsquarters and redroot pigweed (Table 1). Rifai et al. (Reference Rifai, Astatkie, Lacko-Bartosova and Gadus2002) applied steam (requiring 6,920 MJ ha−1 for heating) to fringed willowherb (Epilobium ciliatum Raf.), yellow toadflax (Linaria vulgaris Mill.), and common lambsquarters, which provided 79%, 24%, and 50% control, respectively (Table 1). These values suggest a range of 6,920 to 8,900 MJ ha−1 for steam weeding.
Freezing weeds with either liquid CO2 or N2 has been investigated as an alternative to other thermal methods. Fergedal (Reference Fergedal1993) reported that while freezing had a similar effect on weeds as flame weeding, the energy required was 6,000 MJ ha−1 (14,200 L N2 ha−1) with liquid N2 and 12,000 MJ ha−1 for liquid CO2 (Table 1). Cutulle et al. (Reference Cutulle, Armel, Brosnan, Kopsell, Hart, Vargas, Gibson, Messer, McLemore and Duncan2013) combined freezing with a ballasted roller, aiming to reduce the cryogen requirement, and reported that 9,360 L ha−1 of liquid N2 was required for 83% control of pitted morningglory (Ipomoea lacunosa L.) at the 6- to 8-leaf stage.
The application of hot air for the control of weeds is suggested as comparable in efficacy to that of steam, hot water, and flame weeding; however, the energy consumption is significantly higher (Rask and Kristoffersen Reference Rask and Kristoffersen2007). The control of weeds on a traffic island with hot air required 335 kg ha−1 of propane equating to 16,884 MJ ha−1 (Kristoffersen et al. Reference Kristoffersen, Rask and Larsen2008) (Table 1). However, this study did not attempt to find the minimal acceptable dosage, so lower dosages may be possible.
Microwave treatment of weeds involves use of a waveguide and horn antenna to focus microwaves onto the treated area, resulting in thermal damage to the plant (Figure 2). Microwave exposure time required for effective weed control is dependent on the antenna size (influencing wavelength), microwave power, dielectric loss factor, plant morphology, and species (Brodie et al. Reference Brodie, Ryan and Lancaster2012b, Reference Brodie, Jacob and Farrell2015; Sartorato et al. Reference Sartorato, Zanin, Baldoin and De Zanche2005). With an upright growth habit, grasses are less susceptible than species with a prostrate growth habit (Brodie Reference Brodie2016a; Brodie and Hollins Reference Brodie and Hollins2015; Brodie et al. Reference Brodie, Ryan and Lancaster2012b; Sartorato et al. Reference Sartorato, Zanin, Baldoin and De Zanche2005). Significantly higher energy densities are required for the control of grasses than broadleaf species, where 9,600 to 38,000 MJ ha−1 reduced the biomass of 2-leaf-stage broadleaf weeds (Table 2) by 90%, while 35,000 to 75,000 MJ ha−1 was required to similarly reduce the biomass of grasses (Brodie Reference Brodie2016b; Sartorato et al. Reference Sartorato, Zanin, Baldoin and De Zanche2005; Wayland et al. Reference Wayland, Merkle, Davis, Menges and Robinson1975). Consequently, the reported energy consumption for microwaves is 9,600 to 38,000 MJ ha−1 for young broadleaf species, incorporating an efficiency factor of 75% for the microwave-producing magnetron.
Table 2. Microwave energy requirements for the control (90% reduction in biomass) of broadleaf and grass species at various growth stages where specified.

a Abbreviation: DAS, days after sowing
b Johnsongrass was 180-cm tall. New growth from rhizomes and seed was measured at 24 d posttreatment.
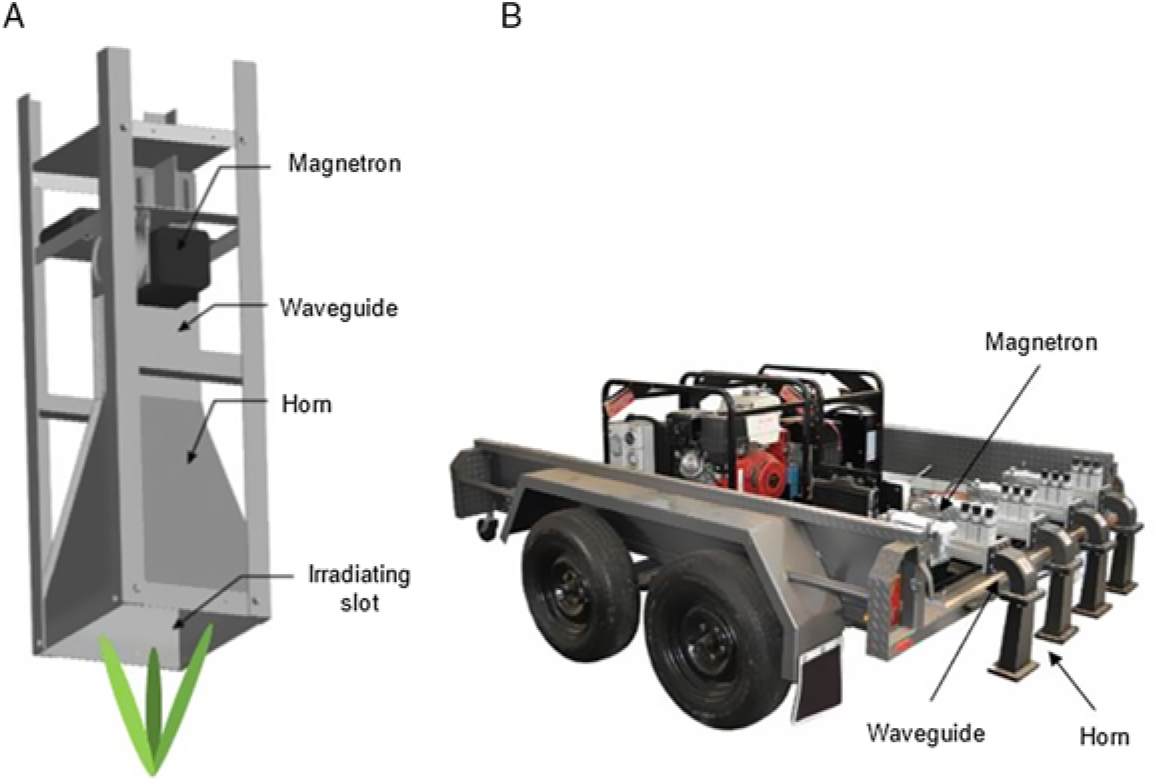
Figure 2. (A) Diagram of a microwave antenna used in microwave weed control (Sartorato et al. Reference Sartorato, Zanin, Baldoin and De Zanche2005) and (B) a series of magnetrons and antennae mounted on a trailer (Brodie Reference Brodie2016a).
Primary Tillage Treatments
Tillage controls weeds by uprooting, burying, or severing roots from shoots (Zimdahl Reference Zimdahl2013) or burying weed seeds to prevent emergence via deep seed placement, induced dormancy, or seed decay (Davis et al. Reference Davis, Cardina, Forcella, Johnson, Kegode, Lindquist, Luschei, Renner, Sprague and Williams2005; Gramshaw and Stern Reference Gramshaw and Stern1977). Effectiveness of tillage on seedlings is closely related to soil drying conditions following treatment (Buhler et al. Reference Buhler, Stoltenberg, Becker and Gunsolus1994; Cavers and Marguerite Reference Cavers and Marguerite1990; Kurstjens et al. Reference Kurstjens, Kropff and Perdok2004). The role of tillage in cropping systems has declined significantly with the adoption of conservation cropping systems. While primary tillage operations, such as moldboard plowing, disking, and rototilling (rotary hoeing) are not routinely used, these techniques may be implemented for strategic weed control and soil amelioration purposes in conservation cropping systems (Davies et al. Reference Davies, Bakker, Scanlan, Gazey, Hall, Riethmuller, Abrecht, Newman, Harding and Hayes2013; Hobbs et al. Reference Hobbs, Sayre and Gupta2008; Norsworthy et al. Reference Norsworthy, Ward, Shaw, Llewellyn, Nichols, Webster, Bradley, Frisvold, Powles and Burgos2012; Roper et al. Reference Roper, Davies, Blackwell, Hall, Bakker, Jongepier and Ward2015). Considering the diversity of operations, implement setups, operator techniques, soil characteristics, and tractor conditions, values for energy consumption are inherently variable and should be viewed as comparative energy consumption–based ranking of tillage operations. Research on the impact of implement geometry (Godwin Reference Godwin2007) soil characteristics (Chen et al. Reference Chen, Munkholm and Nyord2013; Perdok and Kouwenhoven Reference Perdok and Kouwenhoven1994), and draft force highlights this variability.
Reflecting the consumable-inclusive approach taken in this review, the loss of steel from the working surfaces of tillage implements has been included as intrinsic energy consumption. The production of steel in the United States requires approximately 14.9 MJ kg−1 and up to 20.0 MJ kg−1 once transmission and distribution losses are incorporated (Hasanbeigi et al. Reference Hasanbeigi, Price, Aden, Zhang, Li and Shangguan2011). Based on field and controlled-environment testing, wear rates were found to be 90 to 210 g ha−1 of steel for plowshares, 60 to 135 g ha−1 for cultivators, and 30 to 96 g ha−1 for harrows in sandy loam soils (Bayhan Reference Bayhan2006; Horvat et al. Reference Horvat, Filipovic, Kosutic and Emert2008). In rotary hoes, wear rates of 15 to 158 g ha−1 were observed, depending on hardness of tiller blade surfaces, soil characteristics, and speed (Caslli et al. Reference Caslli, Hasanaj and Dimo2017; Kaminski et al. Reference Kaminski, Sypula, Chlebowski, Nowakowski, Malinovska and Osadcuks2018). Using these wear values and the energy consumed in steel production, an indirect consumption value of 0.6 to 1.9 MJ ha−1 was calculated for flex-tine, spring-tooth, and roller harrows and rod and basket weeders. An indirect energy value of 1.2 to 2.7 MJ ha−1 was included for the sweep cultivator and chisel plow, and 1.8 to 4.2 MJ ha−1 for the tandem-disk harrows and moldboard and disk plows.
Primary tillage operations involved in the analysis include offset-disk, moldboard, and chisel plowing. Given the potential requirement for additional tillage operations following primary tillage treatments for soil smoothing in preparation for planting (e.g., harrowing), the estimated energy consumption provided should be viewed as a minimum. With a tillage depth of 10 to 25 cm for offset disks, energy use per hectare was calculated at 43 to 90 MJ ha−1 for offset disks incorporating indirect energy costs (American Society for Agricultural Engineers 2000). Confirming these calculations, a field study by Al-Suhaibani and Al-Janobi (Reference Al-Suhaibani and Al-Janobi1997) observed energy requirements between 12 MJ ha−1 and 63 MJ ha−1 based on specific draft force measurements (excluding indirect energy consumption) at the drawbar for an offset-disk plow. Table 3 presents the breakdown of total energy as the sum of indirect and direct energy consumption values.
Table 3. Summary of energy consumption for broadcast tillage and mulching weed control options.

a PTO, power takeoff.
b References provided cover efficacy of control option and/or estimations for energy consumed including variables used in provided calculations.
c Based on Rostselmash disk harrows (Rostselmash 2017).
d Direct energy consumption estimated from published draft force (Moitzi et al. Reference Moitzi, Haas, Wagentristl, Boxberger and Gronauer2013).
e Massey Ferguson RM4-16HD 4 Furrow Plow (Massey Ferguson 2016).
f Direct energy consumption estimated from published draft force (Arvidsson et al. Reference Arvidsson, Keller and Gustafson2004; McLaughlin et al. Reference McLaughlin, Drury, Reynolds, Yang, Li, Welacky and Stewart2008).
g Case IH PTX600 3 section chisel plow (Case Corporation 2002).
h Aerostar 150 (Einböck GmbH CoKG 2017).
i Based on the Duck Foot Cultivator (MP Iron Industries 2018).
j Falc CR1500 (Inlon 2018).
k Estimated from Bigham Rod Weeder (Bigham 2017).
l DCU0590 Heavy Duty Cultivator (Delmade 2017).
m Based on Rolling Harrow Model 225 (Unverferth Manufacturing 2017).
n Talex Z302 (Talex 2012).
o Flail Mower Standard 105 (Agpro Australia 2017).
p Model 85 Mulch Layer (Hummert International 2013).
Moldboard plowing has a dual impact on weed populations by burying weed seeds to a depth from which they cannot emerge as well as targeting established weeds (Chauhan et al. Reference Chauhan, Gill and Preston2006; Yenish et al. Reference Yenish, Doll and Buhler1992). Moitzi et al. (Reference Moitzi, Haas, Wagentristl, Boxberger and Gronauer2013) conducted a draft force study on moldboard plowing 25-cm deep and found energy values on sandy loam ranging from 160 to 169 MJ ha−1. The energy consumed increased to 230 to 237 MJ ha−1 on loamy clay (Table 3).
On clay and silt loam soils, chisel plowing was found to consume between 600 and 800 MJ ha−1, respectively, based on specific draft force measurements (Arvidsson Reference Arvidsson2010). In lighter clay loam soils, measured draft force suggested a lower energy consumption of 100 MJ ha−1 (McLaughlin et al. Reference McLaughlin, Drury, Reynolds, Yang, Li, Welacky and Stewart2008). These results suggest energy consumption between 100 to 800 MJ ha−1 for chisel plowing in a range of climatic and soil conditions.
Secondary Tillage Treatments
While secondary tillage treatments are used for seedbed preparation, breakdown of clods, and soil-surface smoothing, any weed seedlings present will also be controlled by uprooting or burial. These treatments are also used as a false seedbed approach in which soil disturbance stimulates the germination of weeds and a subsequent operation controls emerged seedlings. Implements used for this purpose include the flex-tine (4.2 to 7.5 MJ ha−1), spring-tooth (23 to 24 MJ ha−1), roller (29 to 31 MJ ha−1), and tandem-disk (28 to 50 MJ ha−1) harrows. Energy requirements and specifications are summarized in Table 3.
Sweep cultivators use triangular or duck foot–shaped blades that are pulled through the soil at a shallow depth (Ahmad et al. Reference Ahmad, Tang, Steward, Young and Pierce2014). Sweep cultivators are used to control weeds before planting with less vigorous soil disturbance than chisel plowing. Terpstra and Kouwenhoven (Reference Terpstra and Kouwenhoven1981) reported a weed mortality of 91% to 100% in the path of the implement when soil was dry, and the working depth was 2.5 cm. However, weeds 2.5- to 3-cm tall and not directly in the path of the blades were killed 36% to 60% of the time by soil coverage. Based on an equipment mass of 100 kg m−1 width, the total energy requirement for sweep cultivation is calculated to be 13 to 14 MJ ha−1 (Table 3).
Basket weeders are ground-driven, cylindrical, spring-wire baskets operating in the first few centimeters of soil (Cloutier et al. Reference Cloutier, van der Weide, Peruzzi, Leblanc, Upadhyaya and Blackshaw2007), with baskets most effective against weed seedlings in moist soil with low clay content (Bowman Reference Bowman1997; Evans et al. Reference Evans, Bellinder and Hahn2012). Basket weeders have an estimated total energy usage of 29 to 31 MJ ha−1 (Table 3).
Rotary hoes are typically powered by a PTO and operate with rotating hoe blades in the vertical plane cutting through the soil, at an operating depth of up to 15 cm, pulling out and burying weeds (Hendrick and Gill Reference Hendrick and Gill1978). Draft force per meter width is 600 N (American Society for Agricultural Engineers 2000) when operating at a rotational speed of 320 rpm and a working speed of 14 to 16 km h−1 (Bowman Reference Bowman1997). The total energy consumption is 12 to 17 MJ ha−1 (Table 3).
Rod weeders involve a rotating metal rod with an operating depth of 3 to 10 cm and displace weeds by dragging or pulling them from the soil. The operating speed is between 8 and 11 km h−1 (Bowman Reference Bowman1997), with the rotating rod driven by PTO or hydraulic motors. At a speed of 8 km h−1, the draft force required per meter width is approximately 1.0 to 1.6 kN (American Society for Agricultural Engineers 2000). The calculated energy consumption is 15 to 24 MJ ha−1 (Table 3).
Mowing Weed Control Treatments
Mowing involves the cutting of plant material at a set height above the ground for delayed growth or control. Effective weed control typically requires multiple cuttings to control regrowth and exhaust carbohydrate reserves (Busey Reference Busey2003; Butler et al. Reference Butler, Brouder, Johnson and Gibson2013; Radosevich et al. Reference Radosevich, Holt and Ghersa2007). The blades of disk and flail mowers were identified as a consumable item involving an intrinsic energy involved in production. Tuck et al. (Reference Tuck, O’Dogherty, Baker and Gale1991) observed wear rates of disk mowing teeth between 1.2% and 5.6% of tooth volume, depending on the hardness of the steel; however, based on these values, the energy involved was deemed insignificant. Mowers are generally PTO driven, with rotary disk and flail mowers requiring on average 5 and 10 kW, respectively (American Society for Agricultural Engineers 2000; Rotz Reference Rotz1992). The energy requirements estimated at 31 and 57 MJ ha−1 for disk and flail, respectively are based on a speed of 7 km h−1 (Table 3) for one pass and up to 154 to 285 MJ ha−1 for five passes.
Mulching
Mulching involves covering the soil surface with a layer of plant residue or plastic to prevent the germination and emergence of weed seedlings through a lack of sunlight, nitrogen immobilization, and the presence of allelochemicals (Petersen et al. Reference Petersen, Belz, Walker and Hurle2001; Teasdale and Mohler Reference Teasdale and Mohler2000). Mulch may either be applied using external resources (plastic and organic mulch) or through in situ cover crops mulched in place.
Plant residue
Weed control can be achieved with an organic mulch thickness of 7 to 15 cm (Ozores-Hampton et al. Reference Ozores-Hampton, Obreza and Stoffella2001) at rates of between 9,000 and 210,000 kg ha−1 (Kosterna Reference Kosterna2014; Smith et al. Reference Smith, Reberg-Horton, Place, Meijer, Arellano and Paul2011; Teasdale and Mohler Reference Teasdale and Mohler2000). Teasdale and Mohler (Reference Teasdale and Mohler2000) used a mulch model to suggest that 9,000 kg ha−1 would be effective in delivering approximately 90% weed control. Yordanova and Gerasimova (Reference Yordanova and Gerasimova2016) found a 4- to 10-cm mulch thickness reduced weeds by 95% to 100% after 60 d. Based on these mulch masses, the energy associated with carrying and distributing 9,000 kg of mulch was estimated to be 13.2 MJ ha−1. In addition to the transport and distribution costs of mulch, the energy cost associated with the production of organic mulch was estimated at 0.10 to 0.60 MJ kg−1 based on the energy cost for the industrial production of compost (Boldrin et al. Reference Boldrin, Andersen, Młller, Christensen and Favoino2009; Komilis and Ham Reference Komilis and Ham2004). A rate of 9,000 kg ha−1 results in an intrinsic energy cost of 900 to 5,400 MJ ha−1.
Plastic
Plastic mulching (polyethylene) involves laying impermeable, transparent, or opaque plastic sheeting over a field or row to control weeds, increase soil temperature, and conserve soil moisture. Egley (Reference Egley1983) found the use of transparent polyethylene sheets for 1 to 4 wk reduced populations of pigweeds (Amaranthus spp.), spurred anoda [Anoda cristata (L.) Schltdl.], morningglory (Ipomoea spp.), horse purslane (Trianthema portulacastrum L.), and unspecified grass species by 64% to 98%. Estimation of indirect energy consumption in laying and removing the plastic sheeting is based on a 191-kg Model 85 Mulch Layer (Hummert International 2013), with similar mass to the mulch lifters used for removal. Assuming a plastic thickness of 0.031 mm (Lament Reference Lament1993) results in 300 kg ha−1 of polyethylene. Production energy for polyethylene sheeting ranges from 25 MJ kg−1 for high-density polyethylene to 28 MJ kg−1 for low-density polyethylene (Vlachopoulos Reference Vlachopoulos2009). Plastic mulch in most cases is discarded after a single use; however, trials have demonstrated the potential for the product to be reused at least once (Nyoike and Liburd Reference Nyoike and Liburd2014). Consequently, the energy associated with the production of the plastic mulch results in an indirect energy value of 187 to 235 GJ ha−1 (Table 3).
Herbicides
Herbicides are integral to weed control in cropping systems and have been included in this review as a reference point for comparison with alternative control methods. Green (Reference Green, Stout and Mudahar1987) estimated energy consumed in the production of herbicide varied from 80 MJ kg−1 for nitrophenols (e.g., dinoseb) to 454 and 460 MJ kg−1 for glyphosate and paraquat, respectively. Helsel (Reference Helsel2016) suggested newer production techniques may result in energy efficiency gains of up to 10%. However, patent restrictions and other proprietary rights prevent access to information required for accurate determination of energy consumption in the production of modern herbicides (Helsel Reference Helsel and Pimentel2006, Reference Helsel2016). The rates provided in Table 4 are label rates of common herbicides, used to overcome variability in use patterns, energy consumed in production, and variable application techniques.
Table 4. Energy consumed in the production of various key herbicides (Helsel Reference Helsel and Fluck1992).

a Application rates were taken from label rates for registered use.
Energy consumed in application manifests in diesel consumption through either the tractor or self-propelled sprayer (Safa et al. Reference Safa, Samarasinghe and Mohssen2010). Diesel consumption for boom-type trailed and self-propelled sprayers at various crop stages was observed to vary from 1.0 to 3.9 L ha−1 (Dalgaard et al. Reference Dalgaard, Halberg and Porter2001; Helsel Reference Helsel and Fluck1992; Lincoln University 2008; Ortiz-Canavate and Hernanz Reference Ortiz-Canavate, Hernanz, Kitani, Peart and Ramdani1999; Safa et al. Reference Safa, Samarasinghe and Mohssen2010; Wells Reference Wells2001), suggesting an energy consumption for application of between 37 and 145 MJ ha−1. Using glyphosate as an example herbicide, applied at 1.25 g ae ha−1, the application energy combined with energy consumed in glyphosate production results in an energy requirement of 604 to 712 MJ ha−1, depending on treatment number, combination, herbicide rate, and application technique. It should also be noted that some residual herbicides may require incorporation through cultivation. In these cases, the actual energy consumed for the application of an herbicide will be the sum of both herbicide application and incorporation. Depending on cultivator type, values in Table 3 can be used to complement Table 4 as required.
Discussion of Broadcast Treatment Estimates
Tillage-based weed control tactics were the most energy efficient of the currently available broadcast weed control options, suggesting these techniques will remain a consideration for use in weed control programs. The average energy requirements of all available tillage weed control treatments, except moldboard and chisel plowing, were substantially lower than herbicidal and thermal approaches (Figure 3). Despite the generally reduced energy requirements of tillage-based techniques, the resulting soil disturbance can have negative impacts on soil health, a significant barrier to the routine use of tillage-based weed control (Angers et al. Reference Angers, Bolinder, Carter, Gregorich, Drury, Liang, Voroney, Simard, Donald, Beyaert and Martel1997; Paul et al. Reference Paul, Vanlauwe, Ayuke, Gassner, Hoogmoed, Hurisso, Koala, Lelei, Ndabamenye, Six and Pulleman2013). Nevertheless, tillage-based weed control treatments remain an option for weed control in conservation cropping systems as an infrequent strategic weed control and soil amelioration approach. Within the three primary tillage operations, the specific draft force for chisel plowing was found to be higher than for both the moldboard and disk plowing. The more aggressive lift and forward movement of soil by the chisel plow requires more force compared with the cutting and folding movement of moldboard plows and cutting and rolling action of disks (Arvidsson et al. Reference Arvidsson, Keller and Gustafson2004).

Figure 3. Total energy requirement estimates for mechanical (blue), herbicidal (green), mulch (yellow), and thermal (red) broadcast weed control methods when used to target 2-leaf-stage seedlings at a density of 5 plants m−2. Bar length represents the range of energy consumption values estimated.
The energy requirements for thermal techniques are an order of magnitude higher than mechanical and herbicidal options and strongly influenced by species and thermodynamic principles. Thermal weed control relies on the heating of plant tissue, which is predominantly water, and resultant disruption of cell structure and processes. Liquid water has a large heat capacity of 4.18 J C−1 g−1; thus, a large quantity of energy is required to heat cellular water to the point of cell damage compared with the movement of soil.
Broadleaf weeds with unprotected growing points required substantially lower levels of heat exposure than species with more protected growing points such as grasses (Ascard Reference Ascard1995a; Knezevic and Ulloa Reference Knezevic and Ulloa2007; Ulloa et al. Reference Ulloa, Datta and Knezevic2010). Similarly, mowing is most effective against annual broadleaf weeds with aboveground apical meristems (Cloutier et al. Reference Cloutier, van der Weide, Peruzzi, Leblanc, Upadhyaya and Blackshaw2007; Gibson et al. Reference Gibson, McMillan, Hallett, Jordan and Weller2011). The rate of heat transfer influences efficacy of weed control and can be explained by Fourier’s law of heat conduction, whereby the transfer of heat energy, and hence cell death, is faster between objects with a larger temperature difference (de Cauwer et al. Reference de Cauwer, Bogaert, Claerhout, Bulcke and Reheul2015). Higher temperatures have been shown to reduce the required energy dose for weed control (Ascard Reference Ascard1995b). Other thermal methods such as microwaving are dependent on water content, which varies significantly between species. The energy results provided demonstrate this variability.
Site-Specific Weed Management
An SSWM system integrates detection, computation, and actuation operations to enable weed control on a site- or point-specific basis. For further details on the specifics of SSWM, please see the reviews by Fernández-Quintanilla et al. (Reference Fernández-Quintanilla, Peæa, Andœjar, Dorado, Ribeiro and López-Granados2018) and Berge et al. (Reference Berge, Goldberg, Kaspersen and Netland2012), which provide excellent summaries. Real-time image collection and computation energy requirements are significant and have been included in SSWM estimates. Using road-based autonomous vehicles as a basis for calculations, Liu et al. (Reference Liu, Tang, Zhang and Gaudiot2017) found systems for fully autonomous vehicles consumed between 11 to 18 MJ (3,000 to 5,000 W) over 1 h of operation.
Site-Specific Herbicide Treatments
Herbicides are already used for SSWM in fallow situations using “green-on-brown,” reflectance-based technology, with research focusing on a site-specific approach for in-crop application (Christensen et al. Reference Christensen, Słgaard, Kudsk, Nłrremark, Lund, Nadimi and Jłrgensen2009; Fernández-Quintanilla et al. Reference Fernández-Quintanilla, Peæa, Andœjar, Dorado, Ribeiro and López-Granados2018). At a point-specific level, Franco et al. (Reference Franco, Pedersen, Papaharalampos and Ørum2017) describes the goal for targeted herbicide application as single doses of herbicide applied to individual weeds within crops in the form of a micro-dosing type system. Using this system, Lund et al. (Reference Lund, Słgaard and Graglia2006) achieved 84% control of rapeseed (Brassica napus L.) as a test broadleaf weed using an equivalent 26 g ae ha−1 of glyphosate with a field density of 100 plants m−2. Similarly, Mathiassen et al. (Reference Mathiassen, Lund and Kudsk2016) found 90% control with 2.5 to 32 g ae ha−1 of glyphosate when applied on rapeseed and black nightshade (Solanum nigrum L.) at a density of 300 plants m−2. Using these micro-dosing figures, energy requirements were estimated at 0.24 MJ ha−1 and approximately 15 MJ ha−1 with the inclusion of computational energy.
Thermal Methods
Concentrated solar radiation
Concentrated solar radiation involves focusing incident sunlight onto weeds. The use of a Fresnel lens to focus sunlight for weed control was investigated with a 1.4-m2 lens (Johnson et al. Reference Johnson, Krall, Delaney and Pochop1989) (Figure 4). An exposure time of 1 s was sufficient to kill 96% of redroot pigweed seedlings at the 2-leaf stage. However, the mortality of green foxtail [Setaria viridis (L.) P. Beauv.] at the 4-leaf stage was only 60% with a 10-s exposure time. According to Johnson et al. (Reference Johnson, Krall, Delaney and Pochop1989), Fresnel lenses can produce temperatures of up to 370 C in strong sunlight. It is difficult to estimate the energy requirements that would be associated with such a system, given that the thermal energy is transferred directly from the sun. However, the energy requirement for computation and actuation would remain.

Figure 4. A Fresnel lens focuses sunlight to create a high temperature (>300 C) band for controlling weed seedlings (Johnson et al. Reference Johnson, Krall, Delaney and Thiel1990).
Electrical weeding: continuous contact
Continuous-contact electrical weeding involves the use of voltages between 6 and 25 kV (Diprose and Benson Reference Diprose and Benson1984) applied to the weed with an electrode, with the circuit completed by a nearby grounding wheel. Electrodes can be simple, such as flat bars, either targeted at the plant or swept across a field. Blasco et al. (Reference Blasco, Aleixos, Roger, Rabatel and Moltó2002) reported that a dose of 90 J was sufficient to kill all weeds with fewer than 5 leaves. Dykes (Reference Dykes1984) observed that as weeds matured from 3 to 5 wk, the required lethal dosage increased from 250 to 2,000 J. However, Vigneault et al. (Reference Vigneault, Benoit and McLaughlin1990) found that an average energy dose of 1,760 J was necessary to kill weeds after flowering. Assuming 2-leaf-stage broadleaf weeds for comparison, the energy requirement was estimated at 19 MJ ha−1.
Electrical weeding: spark discharge
Spark-discharge electrical weeding involves locating electrodes within 1 to 2 cm of the plant, resulting in an electrical arc passing into the plant. If the electrodes touch the plant, the spark may be inhibited (Diprose and Benson Reference Diprose and Benson1984); therefore, the electrode must be precisely positioned. Using very high voltages (25 to 60kV), spark discharge required only 0.135 J to control 4- to 6-cm-tall seedlings of mouseear chickweed [Cerastium fontanum Baumg. ssp. vulgare (Hartm.) Greuter & Burdet] (Mizuno et al. Reference Mizuno, Tenma and Yamano1990). Based on 0.135 J per weed and indirect energy requirements, estimated energy consumption is 14.5 MJ ha−1.
Laser weeding
Laser weeding involves the use of a laser beam for pyrolysis (burning) or cutting. Effectiveness is dependent on laser type, laser spot size, plant morphology, treatment duration, and weed size (Kaierle et al. Reference Kaierle, Marx, Rath, Hustedt, Leyson, Lancaster and Woodworth2013; Marx et al. Reference Marx, Barcikowski, Hustedt, Haferkamp and Rath2012; Mathiassen et al. Reference Mathiassen, Bak, Christensen and Kudsk2006). The calculated energy estimates presented for each laser system were based on reported electro-optical (e/o) efficiency, with estimates calculated by dividing reported laser energy consumption by the reported efficiency, where it had not been already incorporated (Table 5) (Gates et al. Reference Gates, Keegan, Schleter and Weidner1965; Kim and Ki Reference Kim and Ki2012; Marx et al. Reference Marx, Barcikowski, Hustedt, Haferkamp and Rath2012; Wöltjen et al. Reference Wöltjen, Haferkamp, Rath and Herzog2008).
Table 5. Wavelength, electro-optical efficiency (e/o), and spectral absorption for laser systems used to control weeds using pyrolytic and cutting approaches.a

a These efficiency figures are incorporated in the final energy estimates for laser weed control based on available reported figures (Gates et al. Reference Gates, Keegan, Schleter and Weidner1965; Kim and Ki Reference Kim and Ki2012; Marx et al. Reference Marx, Barcikowski, Hustedt, Haferkamp and Rath2012; Wöltjen et al. Reference Wöltjen, Haferkamp, Rath and Herzog2008).
b Abbreviations: IR, infrared; Nd:YAG, neodymium-doped yttrium aluminum garnet; UV, ultraviolet.
Laser pyrolysis
The pyrolysis approach to laser weed control involves a laser beam irradiating a plant part, typically the growing point. Rapid heating results in cell rupture and plant tissue damage, similar to the effect of other thermal methods. Laser spot size has a significant influence on efficacy, whereby smaller spot sizes decrease the energy requirements but increase the difficulty in effectively targeting the meristem (Wöltjen et al. Reference Wöltjen, Haferkamp, Rath and Herzog2008). Conversely, large spot sizes do not require the same level of precision, but can result in large off-target energy losses (Langner et al. Reference Langner, Ehlert, Heisig, Bornim and Kirste2006). For every 1% loss of spot diameter covering a weed, the energy requirement per weed increased by 1.3 J (Kaierle et al. Reference Kaierle, Marx, Rath, Hustedt, Leyson, Lancaster and Woodworth2013; Mathiassen et al. Reference Mathiassen, Bak, Christensen and Kudsk2006). To accommodate losses in the targeting of weeds, a 6-mm spot diameter has been used in determining energy estimates for the pyrolysis approach (Heisel et al. Reference Heisel, Schou, Christensen and Andreasen2001, Reference Heisel, Schou, Andreasen and Christensen2002). For a CO2 laser, 21 to 101 J per weed was required for 90% biomass reduction in 2-leaf-stage dandelion, redroot pigweed, and cultivated tobacco (Nicotiana tabacum L.) (Kaierle et al. Reference Kaierle, Marx, Rath, Hustedt, Leyson, Lancaster and Woodworth2013; Langner et al. Reference Langner, Ehlert, Heisig, Bornim and Kirste2006; Wöltjen et al. Reference Wöltjen, Haferkamp, Rath and Herzog2008). Similar biomass reductions for barnyardgrass [Echinochloa crus-galli (L.) P. Beauv.] required between 21 and 264 J per weed (Marx et al. Reference Marx, Barcikowski, Hustedt, Haferkamp and Rath2012). A 940-nm diode laser had an energy range of 34 to 283 J per weed when irradiating the same broadleaf species as the CO2 laser (Wöltjen et al. Reference Wöltjen, Haferkamp, Rath and Herzog2008). The 810-nm, 90-W laser had a range of 58 to >225 J per weed when testing common chickweed [Stellaria media (L.) Vill.], scentless chamomile [Tripleurospermum inodorum (L.) Sch. Bip.], and rapeseed (Mathiassen et al. Reference Mathiassen, Bak, Christensen and Kudsk2006). A 532-nm diode laser consumed 14 to 110 J per weed for control of the same species (Mathiassen et al. Reference Mathiassen, Bak, Christensen and Kudsk2006). Langner et al. (Reference Langner, Ehlert, Heisig, Bornim and Kirste2006) achieved 75% control of a common cornsalad [Valerianella locusta (L.) Lat.] population with a dose of 1.4 J per weed using a tripled neodymium-doped yttrium aluminum garnet (Nd:YAG) laser with a 6-mm spot diameter. The doubled Nd:YAG laser and thulium fiber laser required 14 and 23 J per weed respectively to control redroot pigweed (Kaierle et al. Reference Kaierle, Marx, Rath, Hustedt, Leyson, Lancaster and Woodworth2013). Most research in this area has reported on weed biomass reductions and not control; therefore, the calculated energy estimates are based on 90% biomass reductions and control (where cited). Incorporating efficiencies in Table 5 with the energy requirements for control of a 2-leaf-stage broadleaf weed provides total energy estimates for laser pyrolysis of between 15 and 249 MJ ha−1.
Laser cutting
Laser cutting involves knife-like use of the beam to cut through plant stems. Effectiveness of this approach depends on stem thickness, plant type, cut location, and proportion of laser wavelength absorbed. A 10-mm laser swath is assumed for estimates of energy consumption for laser cutting. CO2 lasers with a high spectral absorption and e/o efficiency would be optimum for cutting (Table 5) (Heisel et al. Reference Heisel, Schou, Christensen and Andreasen2001; Schou et al. Reference Schou, Heisel, Nordskov, Christensen, Jensen, Thestrup and Toftmann2002). The broadleaf species wild mustard (Sinapis arvensis L.), common lambsquarters, and black nightshade required 10 to 75 J for complete stem cutting at the 2-leaf growth stage. The grass species perennial ryegrass and winter wheat (Triticum aestivum L.) required 5 to 125 J per weed for stem cutting at 1 to 2 cm above the soil surface (Heisel et al. Reference Heisel, Schou, Christensen and Andreasen2001, Reference Heisel, Schou, Andreasen and Christensen2002; Schou et al. Reference Schou, Heisel, Nordskov, Christensen, Jensen, Thestrup and Toftmann2002). Including indirect energy consumption, the control of broadleaf weeds at the 2-leaf stage required between 18 and 314 MJ ha−1.
Microwaves
Focusing microwaves onto weeds using a small horn antenna has been suggested as a novel weed management tool (Brodie et al. Reference Brodie, Ryan and Lancaster2012a). The difficulty associated with this method is how to precisely direct the microwaves within a narrow spatial band suitable for targeting individual weeds.
Assuming that microwaves could be targeted onto the seedling stem alone, an aperture size of 5-mm width by 5-mm height is applied (Tajima et al. Reference Tajima, Song, Yaita, Ajito and Kukutsu2013). The energy requirement would be 67 J per weed, including an efficiency factor of 75% for the microwave-producing magnetron. This is based on a test conducted on the five stems of a paddymelon (Cucumis myriocarpus Naudin) (Brodie et al. Reference Brodie, Ryan and Lancaster2012a). Each stem was treated with 200 J cm−2 using an aperture size of 86 mm by 20 mm, resulting in a total energy consumption of 18 MJ ha−1.
Mechanical
Water-jet cutting
High-pressure water jets are widely used in industrial machining and fabrication and have recently been evaluated as a weed control method (Fogelberg and Blom Reference Fogelberg and Blom2002). Ishida et al. (Reference Ishida, Okamoto and Kaizu2005) found 90% and 100% weed control was obtained at a pressure of 30 MPa (the highest pressure tested) with a nozzle diameter of 0.4 mm and flow rate of 1.4 L min−1. The required power would be approximately 800 W, if the water jet is active for a 10-mm cut, at a speed of 7.78 m s−1. The nozzle would be open for 0.02 s, thus 16 J (direct energy) and 0.47 ml of water would be associated with cutting each weed (Table 6). This is equivalent to 15 MJ ha−1 and 24 L ha−1 at a density of 5 weeds m−2 with the inclusion of indirect energy requirements.
Table 6. Summary of energy consumption for physical weed control methods when used for the site-specific targeting of individual weeds at a density of 5 plants m−2.a
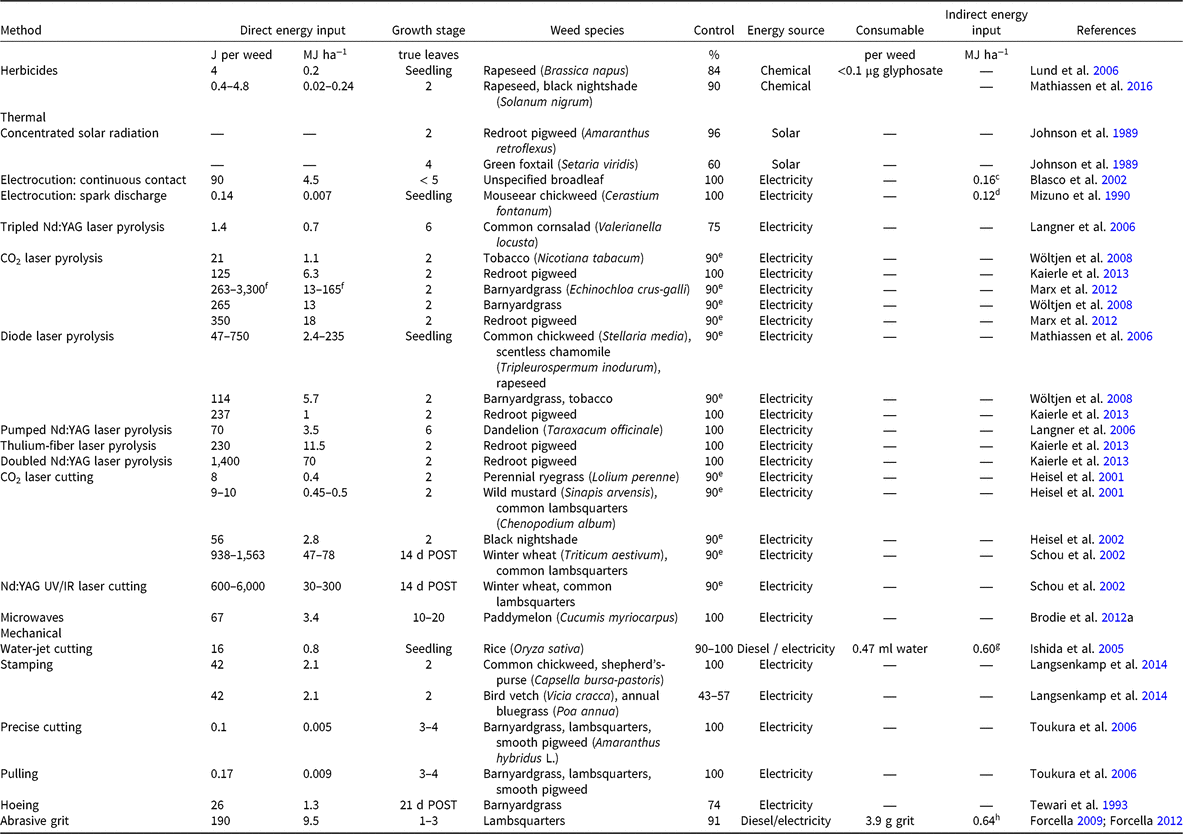
a The underlying indirect energy consumption of 14.4 MJ ha−1 in computation has been calculated from autonomous car systems (Gawron et al. Reference Gawron, Keoleian, De Kleine, Wallington and Kim2018; Liu et al. Reference Liu, Tang, Zhang and Gaudiot2017). References have been provided to source papers for energy estimates.
b Abbreviations: IR, infrared; Nd:YAG, neodymium-doped yttrium aluminum garnet; UV, ultraviolet.
c Based on a 15-kV, 750-W transformer (14 kg) (Tortech Transformers, 2018).
d Based on a 15-kV, 375-W transformer (10kg) (Tortech Transformers, 2018).
e Ninety percent reduction in biomass.
f Variation in energy due to increase in laser spot area from 14 to 28 mm−2
g Based on a 30-MPa, 750-W pump (37 kg) (Jiangsu Hoofar Industrial Company, n.d.).
h Based on a 690-kPa, 1.8-kW compressor (30 kg) (Jedair Compressors, n.d.).
Stamping
The concept involves the pushing weeds into the ground, or “stamping” weeds, using a low refractory period actuator (Sellmann et al. Reference Sellmann, Bangert, Grzonka, Hänsel, Haug, Kielhorn, Michaels, Möller, Rahe, Strothmann, Trautz and Ruckelshausen2014). Langsenkamp et al. (Reference Langsenkamp, Sellmann, Kohlbrecher, Kielhorn, Strothmann, Michaels and Trautz2014) tested a tube-stamp apparatus in which a spring was compressed and then released suddenly to push a round solid metal bar, and consequently the weed on the soil surface, into the ground. The direct energy required to stamp a weed using this apparatus is approximately 42 J (2.1 MJ ha−1). From one stamp treatment, common chickweed and shepherd’s-purse had a fatality rate of 100%. In contrast, bird vetch (Vicia cracca L.), annual bluegrass, and green foxtail efficacy was between 43% and 57%.
Precise cutting
The precise cutting of individual weed stems on a targeted basis has become possible with improved weed-detection technology and precise actuation. Toukura et al. (Reference Toukura, Devee and Hongo2006) investigated the force and energy required to shear weed stems with scissors. It was found that less than 0.1 J was required per weed across several broadleaf and grass species at the 3- to 4-leaf stage. Assuming a density of 5 weeds m−2, this process would entail a direct energy requirement of 0.005 MJ ha−1 (Cloutier et al. Reference Cloutier, van der Weide, Peruzzi, Leblanc, Upadhyaya and Blackshaw2007).
Pulling
Mechanically pulling weeds for control was investigated by Toukura et al. (Reference Toukura, Devee and Hongo2006), who found that approximately 0.17 J was required to remove both broadleaf and grass weeds at the 3- to 4-leaf stage. In a study by Kurstjens and Kropff (Reference Kurstjens and Kropff2001), average weed mortality was 47% to 61%, with similar mortality for grass and broadleaf species. Like tillage, mortality was found to be highly dependent on soil moisture, with higher mortality in dry soil compared with moist soil. A system that uses a pair of rollers to uproot weeds (Saber et al. Reference Saber, Lee, Burks, MacDonald and Salvador2013) could potentially reduce the difficulty of actuation compared with a clamping, robotic-arm mechanism.
Chipping
Targeted chipping with a tine, blade, or chip hoe is a novel area of research with potential to reduce both energy consumption and soil disturbance. A chip hoe and similar methods involve digging out weeds at a shallow depth with an actuated tine with a low refractory period. In response to the detection of a weed, the tine swings down and chips out a weed before returning to its resting state. Research on shallow cultivation tools such as push–pull weeders was used to estimate the energy requirement for this method. A push–pull weeder is a handheld implement with a flat blade, used to uproot weeds. Tewari et al. (Reference Tewari, Datta and Murthy1993) reported that each cycle of motion of a push–pull weeder used 26 J of direct energy to remove 1 weed. Energy consumption in chipping is dependent on several factors, including blade frontal area, blade shape, blade mass, and soil dynamics such as structure, moisture content, and composition. As targeted chipping is a novel area of research, there is limited research on the energy consumption and efficacy of this control option.
Abrasive grit
Blasting individual plants with abrasive grit derived from corn cobs has been investigated as an approach to weed control (Forcella Reference Forcella2009). It was found that one “split-second” blast was sufficient to kill common lambsquarters seedlings. Assuming a blast duration of 0.1 s, the energy consumed was estimated at approximately 190 J per weed, based on the compressor used in these studies. Average grit emission rate was assumed to be 39 g s−1 (Forcella Reference Forcella2012), providing an estimate of 3.9 g of grit consumed per weed (Table 6).
Discussion of Site-Specific Energy Consumption
Like broadcast methods, mechanical techniques in general used less energy than thermal approaches in controlling targeted weeds (Figure 5). Direct energy requirements for the six mechanical weed control treatments ranged from 0.005 MJ ha−1 for precise cutting to 9.5 MJ ha−1 for abrasive grit; however, five treatments required less than 2 MJ ha−1 of direct energy for effective weed control. There were similarly low direct energy requirements for herbicidal weed control, ranging from 0.02 to 0.24 MJ ha−1. Thermal weed control treatments were generally more energy intensive; however, treatments varied markedly from 0 for solar radiation to 6,000 MJ ha−1 for Nd:YAG IR laser cutting. However, when the Nd:YAG laser was used for pyrolysis, the weed control energy requirement was comparable to that of herbicides and mechanical weed control techniques. Spark-discharge electrocution and microwaves also had low energy requirements, but research on these techniques is limited, and their weed control potential has not been established.
In line with findings for broadcast weed control methods, broadleaf weeds required less energy for control with thermal methods than grass species. In most broadleaf weed species, the apical meristem is situated above the soil, while in grass species the growing point is often protected at or below the soil, making grasses more difficult to control with highly targeted treatments, such as lasers and water jets (Wöltjen et al. Reference Wöltjen, Haferkamp, Rath and Herzog2008). Similarly, cutting below the meristem with lasers at the seedling stage was effective in controlling broadleaf weeds but less effective in grasses, in which the meristem is situated at or below the soil surface (Heisel et al. Reference Heisel, Schou, Christensen and Andreasen2001). With electrocution, microscopic observations revealed that plant damage from spark discharge was due to the rupturing of cells in the roots and stems, as the entrance and exit points for the flow of electricity, respectively (Mizuno et al. Reference Mizuno, Tenma and Yamano1990, Reference Mizuno, Nagura, Miyamoto, Chakrabarti, Sato, Kimura, Kobayashi, McGill and Rowarth1993). This overcomes issues with the precise targeting of the apical meristem.
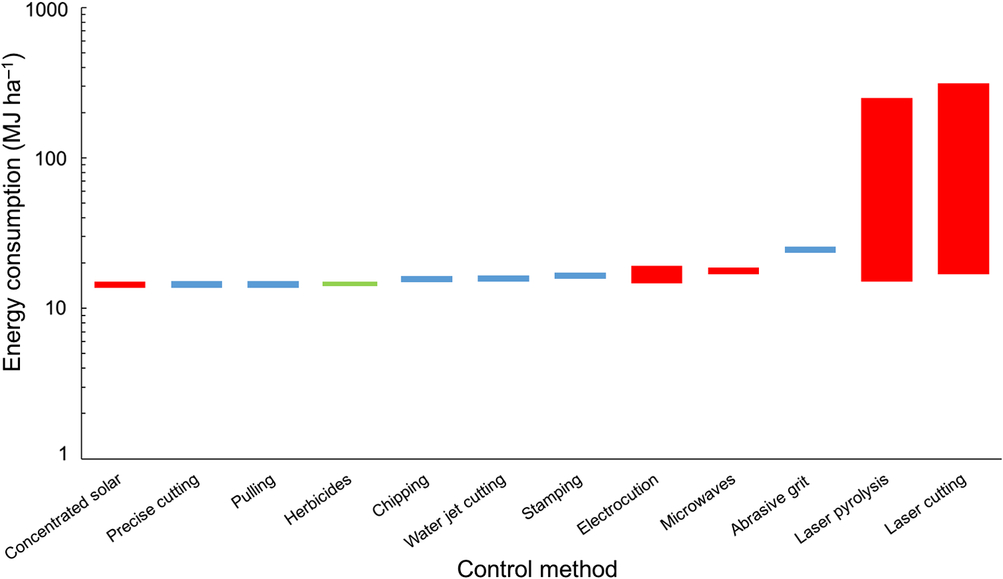
Figure 5. Total energy requirement estimates for physical weed control techniques, mechanical (blue), herbicidal (green), and thermal (red), used in a site-specific approach to target a weed population with a density of 5 plants m−2.
The value of 14.4 MJ ha−1 was used as a constant in all SSWM approaches to represent computational energy requirements, however, it is likely these values will decline as central processing unit and graphics processing unit efficiencies improve (Gawron et al. Reference Gawron, Keoleian, De Kleine, Wallington and Kim2018). Consequently, the fixed indirect energy requirements of SSWM methods will continue to decline.
Broadcast vs. Site-Specific
The comparison of energy requirements for alternative weed control technologies indicates that a site-specific approach provides economically realistic weed control opportunities for large-scale operations. The targeting of individual weeds results in substantial reductions in energy requirements, up to 97% for herbicides, 97% for tillage, and 99% microwaves. Beyond energy itself, the estimation of energy requirements provides an opportunity for comparison of potential economic costs of alternative control methods, based on similar energy sources. Additionally, the ability to target specific weeds improves choice of weed control technique, whereby nonselective alternate weed control technologies may be used for in-crop selective weed control. Machine vision and weed detection provide the selectivity required to achieve discrimination, previously reliant on chemical and biological processes.
Future Research
While SSWM may provide these opportunities, the implementation of alternative methodologies relies on effective, consistent, and timely detection and/or identification of weeds for real-time management. Consequently, future research, investment, and collaboration should focus not only on weed control methods, but also on the ability to accurately detect and identify weeds with machine vision. The field is advanced in many external industries (such as industrial automation, automotive, and defense), suggesting interdisciplinary research may be crucial to success in the weeds domain.
Concurrent with the development of identification algorithms, there is a clear need for in-field evaluations of promising alternative methods, such as lasers, electrocution, and targeted hoeing. Further analysis is required of site-specific energy thresholds as determined by density, processing speed, and computational energy consumption. The current limitations of site-specific approaches stem from information processing and accurate weed recognition, which become significantly slower under high weed density. Nevertheless, significant advancements in sensor technology, processing speed, and precision of control modules is encouraging.
Author ORCID
Guy Coleman https://orcid.org/0000-0002-8808-2965
Acknowledgments
This research was funded by the Grains Research and Development Corporation. The authors declare no conflict of interest.