
Introduction
The introduction of iron technology to the Circumpolar North has been a neglected topic of archaeological research and considered peripheral to Old World ferrous metallurgical developments (Wertime Reference Wertime1973; Pleiner Reference Pleiner2000). The region has typically not been included in broad narratives of prehistoric iron technology, and it is generally accepted that the latter was established much later in this region than elsewhere in Eurasia. According to the prevailing diffusion model, iron technology began as a single invention in the Near East in the second millennium BC. From there it is believed to have spread westwards around 1200–500 BC, only reaching the peripheral areas of the Circumpolar North during the Viking Age or pre-modern times (AD 700–1600) (Pleiner Reference Pleiner2000; Peets Reference Peets2003; Buchwald Reference Buchwald2005; Koryakova & Epimachov Reference Koryakova and Epimachov2007; Zavyalov & Terekhova Reference Zavyalov and Terekhova2018). This diffusionist model is often associated with evolutionary perspectives that link technological progress with societal complexity (Childe Reference Childe1944). Hence, iron technology is strongly connected to the emergence of stratified societies and a sedentary way of life based on agriculture. Consequently, the role of iron technology in societies defined as less stratified or highly mobile (e.g. hunter-gatherers, nomads and pastoralists) is generally underestimated in metallurgical research, these being considered insufficiently complex to be associated with iron.
In recent decades, several studies have questioned this interpretation (for a review, see Erb-Satullo Reference Erb-Satullo2019), but they have not had a significant impact on iron research in Europe. For example, although there have been numerous finds of iron objects and evidence of metalworking at prehistoric hunter-gatherer sites in Northern Fennoscandia (i.e. the Scandinavian and Kola peninsulas, Finland and Karelia), and in the Russian Arctic and the Bering Strait region (Figure 1) (Huurre Reference Huurre1981; Hood & Olsen Reference Hood and Olsen1988; Kosmenko & Manjuhin Reference Kosmenko and Manjuhin1999; Lavento Reference Lavento1999; Sundquist Reference Sundquist1999; Jørgensen Reference Jørgensen2010; Cooper et al. Reference Cooper2016; Vodyasov Reference Vodyasov2018) (Figure 1), these finds are predominantly understood along traditional interpretative lines, and are thus disregarded as anomalies. Consequently, none of these sites has been subjected to archaeometallurgical analyses, except for a few chemical analyses of slag (Buchwald Reference Buchwald2005; Vodyasov Reference Vodyasov2018). This paucity of research has limited our understanding of early iron technology in the Circumpolar North and sustained the assumption that metallurgical knowledge was underdeveloped and archaic, or reduced to a simple acquaintance with metals that reached the region as imports via trade or exchange (Koryakova & Epimachov Reference Koryakova and Epimachov2007; Jørgensen Reference Jørgensen2010; Cooper et al. Reference Cooper2016). The use of iron is further typically interpreted as small-scale, for domestic use only and based on a small-tool tradition associated with a hunter-gatherer mode of subsistence (Hood & Olsen Reference Hood and Olsen1988; Kosmenko & Manjuhin Reference Kosmenko and Manjuhin1999; Sundquist Reference Sundquist1999; Jørgensen Reference Jørgensen2010).
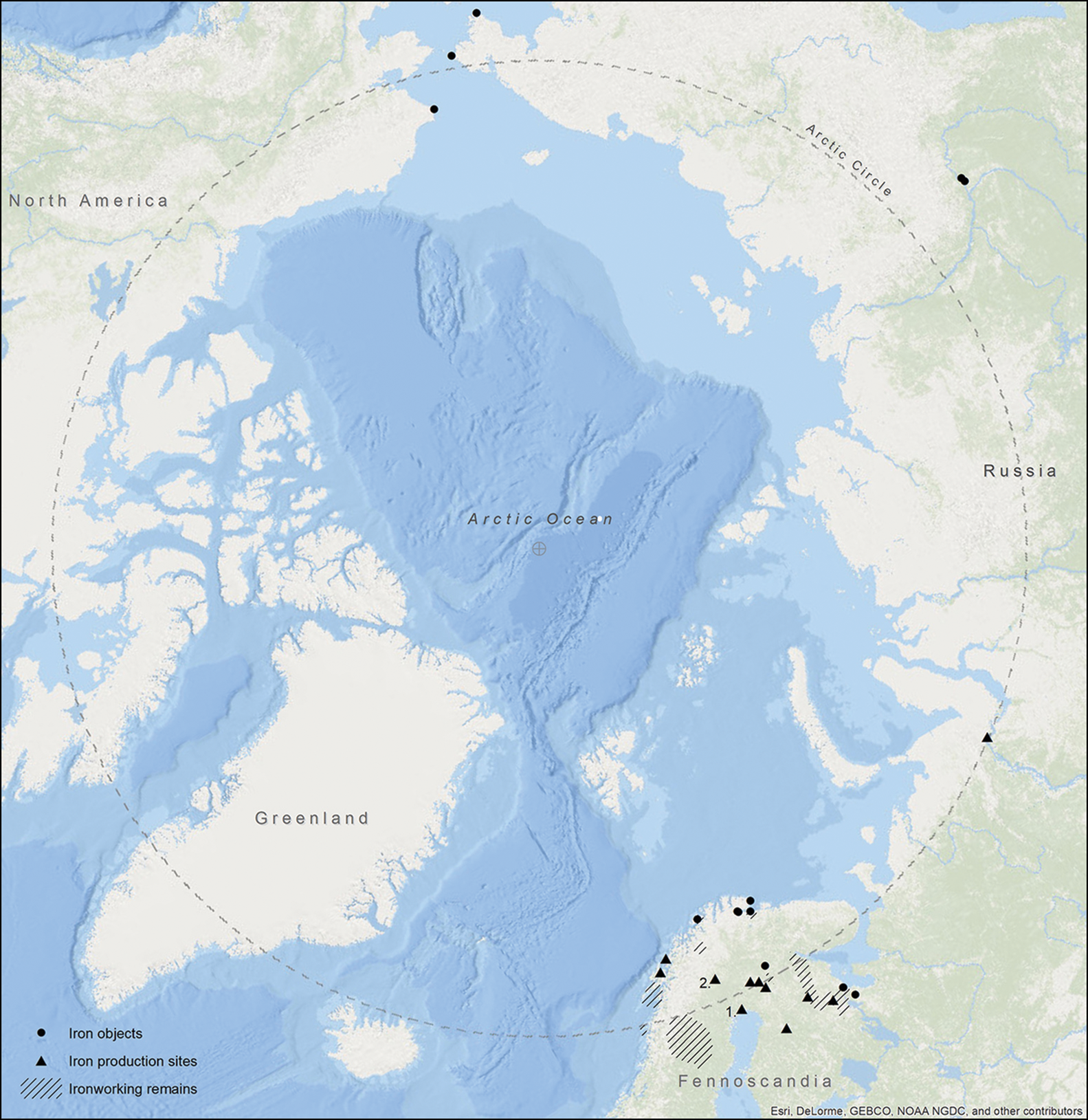
Figure 1. Published iron objects and metalworking remains in the Circumpolar North from the Late Bronze Age to the beginning of the first millennium AD: 1) the Sangis site (Sangis 730 and 842); 2) the Vivungi site (Vivungi 723) (figure by C. Bennerhag © Norrbottens Museum).
To increase our knowledge of early iron metallurgy in the Circumpolar North, we adopt an alternative perspective that goes beyond these assumptions and works towards an understanding of the mechanisms of transmission and technological change. This is based on evidence from two recently excavated sites near Sangis and Vivungi in northernmost Sweden, and builds on recent research on the development of metallurgy (Roberts et al. Reference Roberts, Thornton and Pigott2009) and other technological innovations (Jordan Reference Jordan2015; Grøn & Sørensen Reference Grøn and Sørensen2018). While several Eurasian and Scandinavian researchers have highlighted the role of social networks of skilled practitioners in the initial transmission of metallurgy, their findings have yet to have an impact on European iron research (e.g. Chernykh Reference Chernykh1992; Hjärthner-Holdar & Risberg Reference Hjärthner-Holdar and Risberg2009; Forsberg Reference Forsberg, Anfinset and Wrigglesworth2012; White & Hamilton Reference White and Hamilton2018). Likewise, here, we too emphasise the importance of actor networks, including experienced metalworkers and active apprenticeship—rather than mere exposure to metals—for the transmission of the knowledge of iron metallurgy to Northern Fennoscandia.
This article introduces the sites of Sangis and Vivungi, which provide extensive evidence that iron technology was already integrated in hunter-gatherer subsistence strategies in Northern Fennoscandia during the pre-Roman Iron Age (c. 200–50 BC). By combining archaeometallurgical analyses and archaeological research, we reconstruct the chaîne opératoire. The craftsmanship at these sites was elaborate, including the mastery of bloomery-steel production and advanced smithing techniques traditionally associated with craft specialisation in Transcaucasia c. 1200 BC and the Roman Empire in the first century BC (Pleiner Reference Pleiner2000, Reference Pleiner2006; Zavyalov & Terekhova Reference Zavyalov and Terekhova2018) (for further information on methodology, see the online supplementary material (OSM)).
Archaeological setting
The sites of Sangis and Vivungi, named after the villages closest to them, are located in the Arctic and Boreal zone of north-eastern Sweden: Sangis lies close to Lake Storträsket in the coastal area of the Bothnian Bay and Vivungi in the interior, approximately 140km north of the Arctic Circle (Figure 1). At both sites the landscape is characterised by coniferous forests, lake systems and vast mires—optimal conditions for the procurement of aquatic foods and the resources required for iron production (e.g. fuel and limonite ore).
In 2006–2007 and 2010, rescue excavations in advance of a railway expansion were carried out at Sangis by archaeologists from the County Museum of Norrbotten (directed by Carina Bennerhag). The investigations opened an area of around 7000m2, constituting one of the largest archaeological excavations in northernmost Sweden to have taken place in the last 50 years. Analyses have included the first comprehensive archaeometallurgical study of prehistoric remains in Northern Fennoscandia. The excavations revealed an iron-smelting site (Sangis 842) and a hunter-gatherer habitation site (Sangis 730), less than 500m apart, the latter including both primary smithing (consolidation of blooms) and secondary smithing of iron objects. The smelting site (Sangis 842) consisted of one bloomery furnace (Figure 2) and debris from iron smelting, comprising slags, technical ceramics (i.e. furnace wall lining) and iron waste. Radiocarbon analyses of furnace remains, charcoal embedded in slag and carbon extracted from iron (steel) waste indicate that iron production took place between c. 200 and 50 BC (Figure S146 & Table S5.1). The furnace area at Sangis 842 was associated with contemporaneous hunter-gatherer habitation remains (Table S5.2), including domestic hearths, lithic debitage, asbestos-tempered pottery, as well as faunal remains—mainly fish but also reindeer antler, some of the latter showing cut marks made with a metal blade.

Figure 2. Left) the bloomery furnace at the Sangis site (Sangis 842); right) the lower part of the furnace shaft left in situ. Note the two blasting holes for the air inlet in the furnace wall and the groove on the flat stones for mounting the bellow (photographs by C. Bennerhag © Norrbottens Museum).
The hunter-gatherer habitation site (Sangis 730) yielded archaeological finds dating from the pre-Roman Iron Age to the Viking Age (c. 500 BC–AD 900). Radiocarbon-dating reveals four consecutive occupational phases (Table S5.2). More than 50 features were identified, consisting of household and smithing hearths and cooking pits, along with large quantities of lithic debitage, ceramic fragments, metallurgical finds and debris (iron and copper alloys), and faunal remains. Zooarchaeological analyses show that the inhabitants’ diet was dominated by freshwater fish in all phases, emphasising the importance of aquatic resources. The faunal remains also include small game mammals (hare, marten and squirrel) and fragments of worked antler (probably from reindeer), indicating crafts such as the handling of furs and horn working. Evidence for smithing activities was concentrated in the central part of the habitation site, and consisted of five features, including at least three smithing hearths; the associated assemblage comprised plano-convex slags, hammerscale, iron waste and several finished and semi-finished items of iron and steel. A bronze buckle (F1784) (Figure 3) was also found, as was slag with copper droplets on the surface, which indicates that different types of metals were worked on site. Radiocarbon-dating of metallurgical remains, including charcoal and burnt bones from structural remains, charcoal embedded within slag and carbon extracted from iron (steel) objects and iron waste, show that metallurgical activities began shortly after 200 BC and continued until around AD 200 (Figure S147 & Table S5.1).
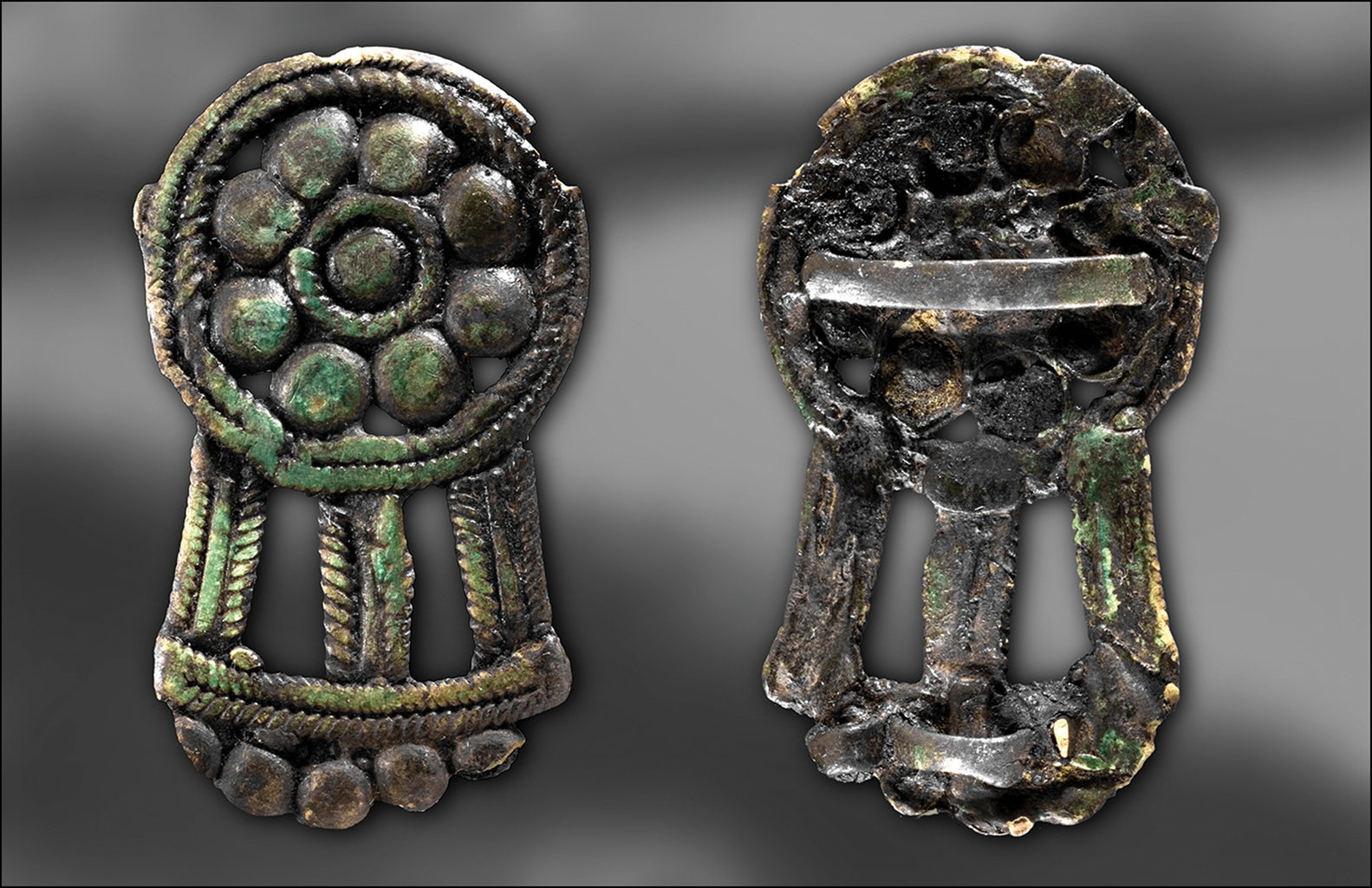
Figure 3. Bronze buckle (F1784) from the Sangis smithing site (Sangis 730). Charred organic material (resin?) was found next to the bronze buckle, radiocarbon-dated to c. 50 BC–AD 115 (Poz 23733) (photograph by S. Nygren © Norrbottens Museum).
The excavations at the Vivungi site were carried out in 2017 by researchers from Luleå University of Technology in northern Sweden, in collaboration with archaeologists from the Sangis excavations and archaeometallurgists at the Swedish National Historical Museums. Initial metal detecting and a magnetometry survey identified three potential production areas close to the shore of Lake Vaihkojärvi, two of which were excavated. Excavations uncovered the remains of two bloomery furnaces (furnaces two and three; Figure 4) approximately 30m apart. These yielded smelting slag, technical ceramics, and iron ore and waste. Unlike the Sangis site, no evidence of smithing activities was found. Radiocarbon analyses of furnace remains, charcoal embedded within slag, and carbon extracted from iron (steel) waste indicate that iron production started at Vivungi around 100 BC, with overlapping dates around 50 BC–AD 50 (Figure S148 & Table S5.1). Scattered occupation remains were also found in each furnace area, comprising debris from lithic procurement and ceramic fragments, along with faunal remains mainly of fish, beaver and reindeer. Due to their thin vegetation cover and slow soil-formation processes, prehistoric sites in northern Sweden are generally not stratified, making it difficult to date the occupation remains at sites with mixed functions. Radiocarbon-dating of a representative sample of faunal remains from both furnace areas reveals at least four periods of habitation, indicating repeated hunter-gatherer occupation from the Mesolithic period to the Middle Ages (c. 5300 BC–AD 1600) (Table S5.2). None of the dated faunal remains, however, was contemporaneous with iron smelting at the Vivungi site.

Figure 4. The bloomery furnaces at the Vivungi site (Vivungi 723) (left: furnace two; right: furnace three). A charcoal feature was found inside furnace two (bottom), showing that the inner part of the furnace shaft was oval (photographs by C. Bennerhag © Norrbottens Museum).
Archaeometallurgical results
Iron production at the Sangis and Vivungi sites
The furnace structures at the Sangis and Vivungi sites were shaft furnaces with underlying slag pits, intended for multiple firings. They all share similar features and consisted of a rectangular frame of vertically set stone slabs leaving one side open, and a shaft of clay built within and partly on this frame. Metallurgical debris in front of every furnace comprised slag, technical ceramics (wall fragments) and iron waste, as well as iron ore at the Vivungi site (see S1–4 in the OSM).
The curvature of the furnaces’ wall fragments and field observations of the structural remains suggest that the furnace shafts were round (Figure 4), with an inner diameter of 0.25–0.35m and estimated heights of about 0.5–0.7m above the blowing zone, taking into account the technical aspects of the process (see S2.3 & S3.4). Air inlets, measuring 20–40mm in diameter, indicate that the furnaces were bellow-blown (Figure 2). Ceramic analyses show that the furnace shafts were made of local clay with good refractory qualities, but with differences in raw material selection and curation both within and between the sites (see S2.3 & S3.4). At the Sangis site and in one of the Vivungi furnaces (furnace two), coarse-grained clays with very poor to poor plastic qualities were used. These furnace shafts were repaired more frequently than is usual in Scandinavian Iron Age contexts. The other furnace at the Vivungi site (furnace three) used a more workable and finer-grained clay; the shaft was probably demolished and rebuilt after every two to three smelts, suggesting differences in the availability and hence procurement of suitable clays in the local surroundings.
The slag assemblages consist exclusively of smelting slag (see S2.1 & S3.1), characteristic of slags known from contemporaneous bloomery iron production sites—not least a relatively high bulk iron content (Table S3) and a clear, but somewhat variable, presence of manganese. A general feature of lake and bog iron ores is their highly variable manganese content. The use of manganese-rich ore (defined by Pleiner (Reference Pleiner2000) as exceeding 3.5 wt% MnO) is reflected in the slags at the Vivungi site (approximately 3.4–5.1 wt% MnO), and further confirmed by the lake and bog iron ores found next to the furnaces (>5 wt% MnO). No iron ore was found at the Sangis site, although the adjacent wetland and nearby lake's geological conditions are favourable to ore formation. The slag analysed from this site, however, indicates that ores containing manganese were used here (approximately 1.5–2.2 w% MnO). The composition of the slag from the Vivungi site deviates from that of Sangis, reflecting natural geological variations. The Vivungi slag can further be distinguished by variations in other minor and trace elements (Table S3), thus suggesting that the smelters there exploited several different ore sources.
Several pieces of irregular, magnetic lumps, characteristic of iron lost during iron production, were found adjacent to all the Sangis and Vivungi furnaces (Figure 5; see S2.2 & S3.2). Remarkably, most of the samples consist of homogeneous steel with a quite high carbon content (0.7–0.8 per cent); some are even cast iron (>2 per cent carbon). This suggests that high-carbon steel was produced intentionally during the smelting process. At the Sangis site carbon-free (ferritic) and low-carbon iron have also been identified, indicating knowledge of the techniques for producing different types of iron.

Figure 5. Iron waste from the Vivungi site (Vivungi 723). The etched sample shows a pearlite texture, which demonstrates a high carbon content (photograph and micrograph by E. Ogenhall © The Archaeologists, Swedish National Historical Museums).
Evidence for smithing at the Sangis habitation site
The workshop area at the Sangis habitation site contained metallurgical debris comprising predominantly smithing slags. Analyses have identified homogeneous and heterogeneous slag (see S1), indicating that both primary smithing of blooms and secondary smithing of objects took place there. This is further confirmed by the presence of unconsolidated pieces of iron waste, suggesting that iron blooms were brought to the smithing site without prior forging, and by highly magnetic hammerscale associated with the smithing hearths, formed during hot forging on an anvil.
Chemical analyses of slag inclusions within iron waste and objects at Sangis show somewhat high but varying manganese contents (see S4, Tables S1 & S3), suggesting that the smithing site was supplied with various types of iron, probably from different iron-smelting systems. Several furnaces were operating simultaneously in the area, as attested by the chemical analyses of slag from the nearby smelting site (Sangis 842). Although the analyses so far show no direct linkage between the smelting and smithing sites, they do demonstrate that the raw materials at both sites originated from the same geological area. This strongly suggests that contemporaneous furnaces supplying the smithing site were probably operating nearby.
The artefact assemblage from the Sangis habitation site comprised tools (mainly knives), along with an axe and several semi-finished objects. Metallographic analyses show that steel is present in both the iron waste and the finished and semi-finished objects (see S1.2), indicating that the smiths used bloomery steel as a starting point in the forge. Ferritic iron was also observed among the finds (mainly in the iron waste, and more rarely in the objects), as was phosphoric iron (see S1.2). The objects’ composite construction (welding and possibly lamination) and the combination of different qualities of iron and steel demonstrate extensive knowledge of different smithing techniques. Various heat treatments, such as quenching and annealing, were also applied to enhance material properties.
Two unidentifiable objects (F1559, F2771) were made of multi-layered steel, with variable carbon contents. One (F1559; Figure S24) was quenched, while the other (F2771; Figures S30–31) was annealed. The latter is radiocarbon-dated to c. 40 BC–AD 150 (Ua-59597; Table S5.1). Multi-layered structures were also identified in two knives (F878 and F2021). One (F878; Figures S21–23) has several alternating bands running from the edge to the ridge, resembling lamination techniques; the central band has a higher carbon content than the outer parts, indicating that the hardest steel is at the edge. Such smithing techniques are usually associated with the Late Iron Age (c. AD 500) (Pleiner Reference Pleiner2006), yet the knife is radiocarbon-dated to c. AD 120–330 (Ua-59594; Table S5.1). The other knife (F2021; Figures S25–26) is made of several bands of phosphoric iron and low-carbon steel, resembling pattern welding—another common technique in the Late Iron Age. Given its low carbon content, this knife could not be radiocarbon-dated, but its context suggests a date contemporaneous with the other finds. Another object showing advanced forging techniques is a socketed axe (F2684; Figure 6: FS27–29) with a multi-layered structure of steel of different strengths. It was heat-treated in several steps using quenching and annealing. Its radiocarbon date range of c. 340–50 BC (Ua-36295; Table S5.1) makes it one of the earliest heat-treated steel objects in Northern Europe.

Figure 6. Socketed axe from the Sangis smithing site (Sangis 730) with a multi-layered structure indicating steel. The micrograph cross-section shows light lines indicating welding seams (photograph by S. Nygren © Norrbottens Museum; micrograph by L. Grandin © The Archaeologists, Swedish National Historical Museums).
Discussion
Cutting-edge technology
The archaeometallurgical analyses of the Sangis and Vivungi sites reveal the inhabitants’ advanced knowledge of metallurgy. At an early stage, different types of iron, including soft ferritic iron and high-carbon steel, were produced. The numerous finds of high-quality steel waste at both sites indicate that smelting processes at high temperatures had been mastered, including the use of extreme temperatures in the furnaces (Crew et al. Reference Crew, Hosek, Cleere and Mihok2011), as attested by the presence of cast iron. Combined, this evidence suggests that the smelters were aware of the refractory properties of clays, as it is critical to maintain the structural stability of the furnace shaft during the high-temperature smelting process. Furthermore, differences in maintenance strategies between the furnaces at the Sangis and Vivungi sites indicate that the smelters were well acquainted with a variety of raw materials and aware of their properties.
In European iron research, the intentional production of bloomery steel is generally linked to the mastery of Roman iron technology starting around 100 BC. This is particularly well attested in the Roman province of Noricum (present-day Austria), where steel is believed to have been produced directly in the smelting furnace (Pleiner Reference Pleiner2006). Finds of droplets and small pieces of high-carbon steel of an earlier date have, however, been found at several production sites in Europe (see Crew et al. Reference Crew, Hosek, Cleere and Mihok2011), and in Scandinavia there is evidence of steel production as early as 800–700 BC (Hjärthner-Holdar Reference Hjärthner-Holdar1993). This suggests that crucial steps towards deliberate steel production were also taken outside the Roman Empire. While manganese-rich ores were understood to be an important prerequisite for the production of bloomery steel in Noricum, enabling carbon to be alloyed with the metallic iron (e.g. Buchwald Reference Buchwald2005; Crew et al. Reference Crew, Hosek, Cleere and Mihok2011; Hjärthner-Holdar et al. Reference Hjärthner-Holdar, Grandin, Sköld and Svensson2018), such ores are common throughout Europe (Rostocker & Bronson Reference Rostocker and Bronson1990). Indeed, the correlation between manganiferous ores and the intentional production of steel is evident at the Sangis and Vivungi sites, where analyses of smelting slags show the use of these ores to produce steel. This is further evident in the limonite ores at the Vivungi site (with >5 wt% MnO) and in several steel artefacts at the Sangis smithing site, which show extremely high quantities of manganese (up to 32 wt% MnO) (Table S1). Overall, this evidence suggests that the northern bloomery smelters graded the ores; they possessed extensive knowledge of the properties of the raw materials and used them to produce iron and steel of different quality.
The intentional production and demand for various qualities of steel are confirmed by the numerous steel objects found at the Sangis smithing site, which are made of several different steel alloys (and combinations thereof) that produced very hard and tough edges. Other types of iron were also used, including relatively soft, ferritic iron and phosphoric iron with a higher ductility than carbon steel. Overall, the smiths had a thorough knowledge of the properties of each alloy and which materials were suitable for different tools. Furthermore, the forged artefacts show advanced craftsmanship, including forge-welding and heat treatments in several steps. Pattern welding—observed on one of the Sangis knives—is an example of a highly advanced, composite structure exploited for its decorative potential. This technique was widely used during the Late Iron Age, requiring years of training (Gilmour Reference Gilmour2017).
Steel artefacts and advanced smithing techniques are strongly associated in European iron research with the Roman Empire, and thus considered unusual beyond the Roman frontiers (Sim & Ridge Reference Sim and Ridge2000; Buchwald Reference Buchwald2005; Pleiner Reference Pleiner2006). Similarly, in Eurasian iron research, the mastery of advanced smithing techniques is associated with Transcaucasian metallurgy, which was already operating around 1200 BC and is believed not to have spread beyond this region (Zavyalov & Terekhova Reference Zavyalov and Terekhova2018). In South India, there is evidence of lamination techniques at around 1000 BC (Gullapalli Reference Gullapalli2009), while in the Ananino Culture in the Ural region of North-western Eurasia, eighth- to sixth-century BC burial finds include examples of heat-treated steel objects manufactured by welding (Koryakova & Epimachov Reference Koryakova and Epimachov2007), similar to the techniques observed at the Sangis smithing site. In central Sweden, Estonia and Slovakia, there is further evidence of welded steel objects ((Hjärthner-Holdar Reference Hjärthner-Holdar1993; Mikhok & Pribulová Reference Mikhok, Pribulová and Ch. Nørbach2003; Peets Reference Peets2003), showing that advanced forging techniques were known outside the Roman Empire from as early as the fifth century BC to the second century AD. The tendency within iron research has, however, been to treat these examples as exceptional, or to consider them as imports. There are few published metallographic analyses of iron artefacts from beyond the Roman frontiers (Goodfrey & Nie Reference Goodfrey and Nie2004), and iron research has generally focused on the later Iron Age, with higher or more extensive iron-production levels attributed to the Roman world.
Technological networks
Our archaeometallurgical analyses illustrate the homogeneity of the metallurgical remains from the Sangis and Vivungi sites, indicating a shared or common technological tradition over a large area. Mastery of a craft, such as metallurgy, generally presupposes both theoretical knowledge and physical training, including apprenticeship and practical guidance from a skilled person (White & Hamilton Reference White and Hamilton2018). The analyses illustrate a general lack of experimentation, as would be expected when practitioners attempt to copy products from another context (White & Hamilton Reference White and Hamilton2018). This in turn indicates that the technology was introduced as a full package including objects, smithing and smelting techniques—all arriving at the same time, presumably through direct contact with experienced metalworkers. The transmission and maintenance of iron technology probably involved the agreement and commitment of many actors, given the labour-intensive extraction and preparation of the raw materials and the collective nature of the iron-production process. Hence, the technology could only have been introduced and accepted within a consenting social environment and a community that appreciated the advantages of its adoption (see Hjärthner-Holdar & Risberg Reference Hjärthner-Holdar and Risberg2009). This, in turn, implies that the hunter-gatherers of the Circumpolar North were active partners in a reciprocal process, rather than passive recipients.
In addition, we also observe design similarities over a large geographic area. The Sangis and Vivungi furnaces are morphologically similar to contemporaneous production sites in Finland and Russian Karelia (Kosmenko & Manjuhin Reference Kosmenko and Manjuhin1999; Lavento Reference Lavento1999) and some Late Bronze Age iron-production sites in central Sweden (Hjärthner-Holdar Reference Hjärthner-Holdar1993), whose rectangular stone-frame construction is a notable feature. The identical furnace design across this vast area is striking, as the rectangular shape is not required for the process. We interpret these similarities as a manifestation of a shared or common technological tradition, in which production practices and design ideas result from relatively far-reaching social interactions (Jordan Reference Jordan2015).
A number of Bronze Age finds of eastern origin, related to the Seima-Turbino phenomenon and the Ananino Culture in north-western Russia, show clear evidence that the hunter-gatherers of Northern Fennoscandia formed part of technological networks as early as the beginning of the second millennium BC (Forsberg Reference Forsberg, Anfinset and Wrigglesworth2012). Although the nature of these networks has yet to be fully explored, the geographic distribution of the stone-frame furnaces and the Bronze Age finds (Forsberg Reference Forsberg, Anfinset and Wrigglesworth2012) suggests extensive continuity and contacts. It appears that previously established local and regional technological networks made the rapid spread of iron metallurgy in the Circumpolar North possible.
The discovery of a bronze buckle at the Sangis smithing site (Figure 3), whose moulding technique and style are most closely paralleled in the Pyanobor Culture (300 BC–AD 200), a direct successor of the Ananino Culture, indicates that the eastern contacts were still active when iron was being processed at our Fennoscandian sites. That the Pyanobor Culture is characterised by specialised knowledge in iron technology, including steel production and advanced forging techniques (Koryakova & Epimachov Reference Koryakova and Epimachov2007), is intriguing, as is the link between the Ural area and Northern Scandinavia during the second half of the first millennium BC revealed by genetic studies (Ingman & Gyllensten Reference Ingman and Gyllensten2007). These aspects require further detailed investigation.
Organisational structure
The archaeometallurgical and archaeological data from the Sangis and Vivungi sites provide, for the first time, comprehensive evidence for an iron-smelting system in the Circumpolar North. Knowledge of iron smelting in prehistoric societies, which are assumed to be less complex and highly mobile, is unusual (for an exception, see Agatova et al. Reference Agatova, Nepop and Korsakov2018), although a growing body of research on African nomadic and pastoralist societies that combines archaeometallurgical and ethnographic/ethnohistoric approaches suggests that our evidence may not be entirely atypical (e.g. Iles Reference Iles2018). The Sangis site represents a notable archaeological context, however, in that the full chaîne opératoire is present, including the smelting of iron, primary smithing of blooms and secondary smithing of objects. Such sites are unusual in the Early Iron Age, and very rare in hunter-gatherer contexts. The Sangis site therefore offers an excellent opportunity to examine the spatial and organisational structure of an iron-smelting system, and the integration of new technology into hunter-gatherer communities.
At Sangis, the chemical analyses suggest a local exchange network consisting of several decentralised production units operating simultaneously in the area, supplying the smithing site with iron. This implies an organisational structure within which multiple households were stakeholders in the production process, with the smithing site centrally positioned in the distribution chain. This pattern can also be discerned at the Vivungi site, where several local furnaces were in use at the same time, although so far smithing has not been documented. Overall, this suggests a more extensive production and more complex organisation of iron technology than previously assumed for the Circumpolar North.
The scale of production is further demonstrated by the furnaces themselves, which were used several times. The productivity of iron production has not previously been assessed in terms of hunter-gatherer economies. Based on Hjärthner-Holdar et al.'s (Reference Hjärthner-Holdar, Grandin, Sköld and Svensson2018) estimated iron consumption of a Late Iron Age farm (2–5kg/year) and the calculated yield of Swedish limonite ore (10kg of ore producing 5kg of slag and 5kg of metal), the scale of production at each of our furnaces (ranging from 9–80kg of iron) would have exceeded the consumption of a single household, even if spread over several years. Thus, iron was of no less importance to the hunter-gatherer community than to more sedentary farming societies.
The production of iron and the manufacture of artefacts was a labour-intensive process, involving multiple materials, several production steps and specialised knowledge. Ores had to be prospected and roasted, wood was required to produce charcoal, and clay and stone were needed to build and repair the furnaces and smithing hearths. The collective nature of this endeavour required organisation and planning throughout the year, and the investment of numerous participants at a collective level. This further implies that a sedentary mode of life was required over extended periods in various optimal locations close to important resources.
The availability of raw materials (i.e. ore, fuel and building material) was key to the location of the production and manufacturing sites. The abundant freshwater fish remains found at the Sangis and Vivungi sites imply that access to nearby aquatic food resources was of equal importance for the establishment of the sites. The conjunction of different resources suggests that iron technology had become an integral part of the exploitative strategies (Binford Reference Binford1979) of the Northern Fennoscandian hunter-gatherers during the pre-Roman Iron Age. Remains of craft activities such as horn- and bone-working, and evidence of metallurgy involving copper/bronze and lithic procurement alongside the smithing remains at the Sangis site, further suggest that iron metallurgy had become organisationally incorporated with other residential activities. This is reinforced by the fact that smelting and smithing were sustained over a considerable period. Such an endeavour seems unlikely without a well-established socio-economic structure.
Conclusion
Our research has uncovered new evidence that iron technology formed a substantial part of the hunter-gatherer subsistence in the Circumpolar North more than 2000 years ago. The greater mobility of hunter-gatherer societies should no longer be considered an obstacle to appreciation of their complex social organisation. Moreover, the spatial and organisational nature of the processes involved in iron production suggests a higher degree of sedentism than previously recognised in this context. Overall, the traditional interpretative paradigm—labelling iron technology in the Circumpolar North as small scale, dependent on imports and underdeveloped or ‘archaic’—is a simplification of a more complex situation. In a global perspective, our results have important implications regarding the emergence of ferrous metallurgy in societies seen as less complex or highly mobile.
Acknowledgements
We thank the County Museum of Norrbotten and ‘The Archaeologists’ of the Swedish National Historical Museums in Uppsala, especially Erik Ogenhall, for their valuable input and productive collaboration. Special thanks are due to the local community of Vivungi for their close collaboration and contribution to fieldwork and research. All the data underlying the study are deposited at the County Museum of Norrbotten in Luleå, Sweden, and are freely available.
Funding statement
This work was supported by the Swedish Research Council (2016-02076).
Supplementary material
To view supplementary material for this article, please visit https://doi.org/10.15184/aqy.2020.248